At the Additive Manufacturing Campus in Oberschleißheim, the BMW Group is trialling wire arc additive manufacturing (WAAM), in which a wire made of aluminium or similar is melted using an arc. Then a software-controlled robot places a large number of welding seams on top of each other with precision, until a complete component is finished.
Because the pressure means that layer by layer there is no need to pay attention to demouldability, hollow structures with an optimum ratio between rigidity and weight are possible.
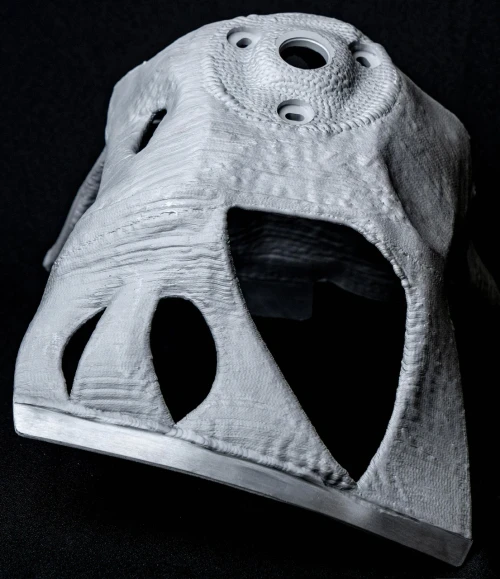
This means that the components can be lighter and more rigid than comparable die-cast parts currently manufactured in series production. They can also be produced more sustainably thanks to lower energy requirements and less material waste. In the future, the plan is to use components manufactured using the WAAM process in BMW Group production vehicles.
The large width and height of a single welding seam means that components can be produced extremely quickly using WAAM. In contrast to laser beam melting, which is already used in prototype and small series production at the BMW Group, WAAM is particularly suitable for larger components. The typical wall thicknesses are well suited to components in the body, drive, and chassis areas. However, tools and devices can also be manufactured using this high-tech process, which is also used in the aviation industry.
BMW Group employees have been focusing on the WAAM process, also known as build-up welding, since 2015. A WAAM cell for the production of test components has been in use at the Additive Manufacturing Campus since 2021. One of these example applications is a suspension strut support, which, in extensive testing on the test bench, is being compared with the series production component made from aluminum pressure die-casting.
In this early stage it is already clear that the WAAM process can result in lower emissions in the production process. The lower weight of the components, their advantageous material usage ratio, and the option to use renewable energy means that the components can be produced more efficiently.
—Jens Ertel, Head of BMW Additive Manufacturing
The next stage of development on the road to series production is testing components in the vehicle, which will start in the foreseeable future.
The wider welding seams in the WAAM process mean that the surfaces of the components are not smooth, but slightly rippled and must be finished in critical areas. However, BMW Group engineers were able to demonstrate that WAAM components can be used for high loads, including cyclical loads, even without post-treatment of the surface.
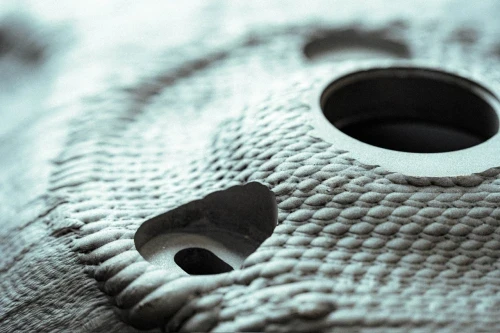
Optimized process parameters are crucial for ensuring durability directly from production, so the combination of welding process and robotic path planning must be coordinated optimally.
To make optimum use of the components produced in the WAAM process, the combination of the manufacturing process and a general new component design is paramount. To this end, the BMW Group continues to accelerate the use of generative design. Here, the computer uses algorithms to design optimized components based on the specific requirements.
These algorithms are developed in close collaboration with interdisciplinary teams and are in part inspired by evolutionary processes in nature. As with bionic structures, the first step is to use only the material that is actually required for the topology of the component, and during fine-tuning in the second step, the component is reinforced only where necessary. This ultimately results in lighter and more rigid components as well as greater efficiency and improved vehicle dynamics.
Different additive production processes are not necessarily in competition with each other, rather they should be viewed as complementary. For example, laser beam melting will continue to be more advantageous than the WAAM process when it comes to the highest level of detail resolution. In terms of the possible size of the component and the deposition rate, however, wire arc additive manufacturing is superior.
The BMW Group is initially planning centralized WAAM production of components in Oberschleißheim, in the future, production at other locations and the use of the technology by suppliers is also possible. Further, it would even be conceivable to produce individual components directly on the assembly line using this process and to manufacture different parts without new tools, simply by changing the software. Sustainability can also be further improved by increasing the use of recycled metals.
Source from Green Car Congress
Disclaimer: The information set forth above is provided by greencarcongress.com independently of Alibaba.com. Alibaba.com makes no representation and warranties as to the quality and reliability of the seller and products.