Audi’s Premium Platform Electric (PPE), developed jointly with Porsche, is a key component for the expansion of the global portfolio of all-electric Audi models. For the next generation of electric vehicles from Audi, the company has redeveloped the electric motors, the power electronics, the transmission, as well as the high-voltage battery and all related components, and tailored them exactly to the requirements of battery electric vehicles.
The Audi Q6 e‑tron is the first production model on the PPE. (Earlier post.)
Motors. All powertrain components for the PPE are designed to be even more compact than the drive systems developed and installed previously, and they stand out due to higher efficiency. In total, the efficiency measures around the new electric motors for the PPE enable 40 kilometers of extra range compared to the first-generation Audi e-tron.
In the area of production, the degree of automation and the vertical range of manufacture have increased significantly. The new electric motors for the PPE require about 30% less installation space than those of previous electric models. Their weight has been reduced by about 20%.
The PSM (permanent magnet synchronous motor) on the rear axle of the Audi Q6 e-tron series has a length of 200 millimeters. The ASM (asynchronous motor) on the front axle has a length of 100 millimeters. When not in use, it is able to rotate freely without significant drag losses.
The new hairpin winding and a direct oil-spray cooling system in the electric motor’s stator contribute substantially to the drive system’s higher efficiency. For example, the fill factor has increased to 60 percent compared to 45 percent for the conventional windings that were used previously.
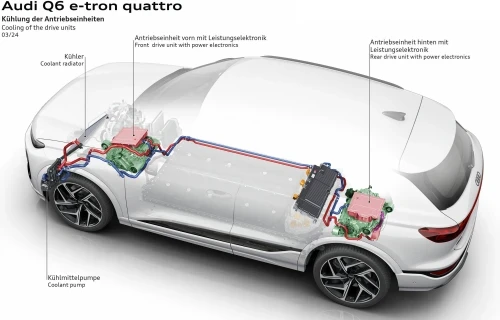
An electric oil pump in the transmission also contributes to the increased efficiency. Due to the rotor oil cooling, Audi was also able to largely dispense with the use of heavy rare earth elements while simultaneously increasing the power density by 20%.
Power electronics and transmission for the PPE. The power electronics (inverter) controls the electric motor and also converts direct current from the battery into alternating current. The data for the exact control of the inverter is provided by the domain computer HCP1 (high-performance computing platform 1), which is responsible for the drive system and the suspension.
Silicon carbide semiconductors are installed in the more powerful version of the water-cooled inverter. Due to their efficiency—60% higher—they particularly excel under partial load and are more reliable. As a result, they contribute significantly to the efficiency and higher performance of the PPE electric motors. The range advantage compared to silicon semiconductors is about 20 kilometers.
Due to the 800-volt architecture, thinner wire can also be used for the wiring of the battery and the electric motor. This reduces installation space, weight and consumption of raw materials. Because the system heats up less due to lower heat loss, the cooling system is also smaller and more efficient. The transmission works with dry sump lubrication and an electric oil pump. Nozzles spray the gears directly. This design minimizes friction losses and also reduces installation space.
Charging performance. The 800-volt architecture, which is required for charging outputs of up to 270 kW, is one of the key factors for high charging performance. The cell chemistry has been optimized to accommodate such a high value. Audi says it has achieved an optimum balance between energy density and charging performance. The cells developed in collaboration with the supplier offer a high energy density, a significantly reduced cobalt content, and lower resistances for the best possible charging performance.
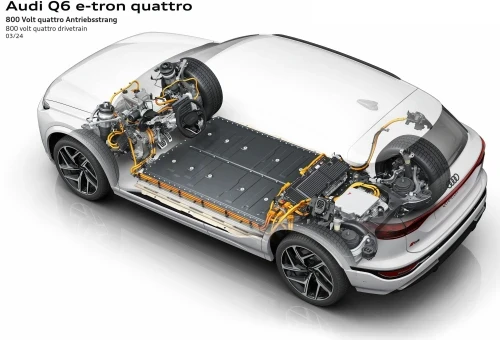
In addition to the 800-volt architecture, intelligent thermal management makes a significant contribution to high charging performance and the long service life of the HV battery in the PPE. The most important component is predictive thermal management, which uses data from the navigation system, the route, the departure timer and the customer’s usage behavior to calculate the need for cooling or heating in advance and to provide them both efficiently and at the right time.
If a customer is driving to charge at an HPC charging station included in the route planning, the predictive thermal management system will prepare the DC charging process and cool or heat the battery so that it can charge faster, thus reducing the charging time. If there is a steeper rise ahead, the thermal management system will adjust the HV battery by appropriate cooling to prevent a higher thermal load. If the driver has selected efficiency mode in the drive select menu, the conditioning of the battery is activated later and the real range can be increased depending on the driving behavior. In dynamic mode, the goal is optimal performance.
However, if the current traffic situation does not allow for dynamic driving, the thermal management system will react to this and minimize the energy usage for the battery conditioning.
Post and continuous conditioning is another new feature in the PPE’s thermal management system. This function monitors the battery temperature for the entire service life to keep the battery at the optimum temperature range even when the vehicle is stationary—for example, at very high outside temperatures. The coolant flow was optimized by implementing the U-flow principle underneath the battery modules. This leads to high-temperature homogeneity within the battery—monitored by 48 temperature sensors—and ultimately to high energy delivery and absorption performance.
With a state of charge (SoC) of about 10%, vehicles in the Audi Q6 e-tron series need just ten minutes at a fast-charging station at a maximum charging power of 270 kW with DC charging to generate a range of up to 255 kilometers (158 miles) under ideal conditions. It takes 21 minutes for the HV battery to be charged from an SoC of ten percent to 80 percent. A communications control unit, referred to as the Smart Actuator Charging Interface Device (SACID), acts as an interface to establish a link between the charging socket and the charging station and transmits the incoming standardized information to the HCP5 domain computer.
Vehicle thermal management. The vehicle’s thermal management system has been redesigned. To compensate for the increased efficiency in the drivetrain and the resulting reduction in heat loss, the water-glycol heat pump is supplemented by an air heat pump. This means that in addition to the waste heat in the coolant of the electric motor, power electronics, and battery, the ambient air can also be used as a heating source for the interior.

The temperature exchange now works directly via a heating coil. Moreover, an 800-volt air PTC heater was developed as an effective addition, which also directly supports the interior temperature control in the air conditioning unit in the event of increased heating requirements. This avoids the heat losses associated with water-based heating circuits.
Recuperation and friction brakes.As a rule, with the PPE, about 95% of all everyday braking process can be covered via recuperation, i.e., regenerative braking via the electric motors. The use of fiction brakes in brake blending occurs correspondingly later or more rarely. In the PPE, the recuperation function is also no longer handled by the brake control system, but rather by the HCP1, one of the five high-performance computers in the vehicle, which is responsible for the drive system and suspension in the PPE. As a result, the influence of the drive system on the braking system increases.
The transition from regenerative braking via the electric drive systems to mechanical braking via the hydraulically actuated friction brakes is no longer perceptible to the driver. The brake blending ensures a well-controlled pedal feel with a clearly defined, constant pressure point.
The Intelligent Brake System (IBS) known from previous e-tron models has undergone significant further development in the Premium Platform Electric. For example, axle-specific brake blending is possible for the first time.
Recuperation remains on the rear axle as needed, while hydraulic pressure is generated on the front axle. As is typical for Audi, there is an option for two-stage coasting recuperation, selectable via the paddles on the steering wheel. Coasting is also possible. Here the electric SUV rolls freely when the foot is removed from the accelerator, without additional drag. Another option in the Audi Q6 e-tron series is driving mode “B,” which comes very close to what is colloquially called the “one-pedal feeling.”
E³ 1.2 electronic architecture. With the new E3 1.2 electronic architecture, Audi customers experience the advantages of vehicle digitalization more immediately than ever before. E³ makes it possible to increase the number, size and resolution of the screens in the vehicles. It is also designed for wireless updates (over the air) and for the addition of new features, for example, by offering Functions on Demand.
In the Q6 e-tron series, Audi is introducing a completely new, standardized infotainment platform based on Android Automotive. Numerous vehicle functions can be controlled using Audi’s digital assistant, a self-learning voice assistant. The digital assistant is deeply integrated in the vehicle and is visualized by means of an avatar in the dashboard (Audi Assistant Dashboard) and in the augmented-reality head-up display for the first time. With a store for third-party apps, users can also use their favorite apps from their digital ecosystem directly on the vehicle display.
The store gives customers access to a wide variety of apps, which can be installed in the MMI directly without requiring the use of their smartphones. Initially, applications from the following categories will be available: Music, Video, Gaming, Navigation, Parking and Charging, Productivity, Weather and News. The Music category, for example, includes apps such as Amazon Music and Spotify. The store will be continuously expanded in the future. It can be selected via a separate tile in the MMI. The additional apps will then be seamlessly integrated into the MMI and will be available for secure and reliable use during the journey. The app portfolio on offer is specific to each market. The familiar Audi smartphone interface for integrating Apple CarPlay and Android Auto is also available in the Q6 e-tron series.
The scalable and future-proof electronic architecture allows Audi to offer various vehicle models and derivatives on a standardized electronic basis. This approach reduces complexity in both development and production and creates additional economies of scale. In addition, the new electronic architecture forms the basis for future innovations. Security (security by design) and update capabilities are anchored in the architecture right from the start.
The transfer of functions from the sensor-actuator level to the computer level, i.e., the increasing decoupling of hardware and software, will also make it possible to cope with the increasing complexity in the coming years safely.
The focus of development was on high-performance and secure networking of domain computers, control units, sensors and actuators. Five high-performance computers, known as the Audi high-performance computing platform (HCP) form the E3 1.2’s central nervous system. All vehicle functions are allocated to the various HCPs according to domain. Audi networks the individual vehicle systems with familiar automotive protocols and with Gigabit Ethernet.
Source from Green Car Congress
Disclaimer: The information set forth above is provided by greencarcongress.com independently of Alibaba.com. Alibaba.com makes no representation and warranties as to the quality and reliability of the seller and products.