Table of Contents
1. Introduction
2. Key types of brake lubricants and their uses
3. Market trends and developments
4. Critical factors to consider when choosing brake lubricants
5. Top-performing products and their features
6. Conclusion
Introduction
Using brake lubricants is essential for maintaining the effectiveness and durability of brake systems. They decrease friction levels, prevent corrosion, and minimize noise levels effectively. These specialized products are formulated to withstand extreme temperatures and maintain compatibility with sensitive brake components like rubber and plastic parts. Choosing the right lubricant enhances performance and safety, particularly in high-stress applications. The correct lubricant prevents wear and tear on essential components, ensuring smooth operation and reducing maintenance needs. Selecting the best product for each system can significantly impact overall performance and durability.
Key types of brake lubricants and their uses
Silicone brake lubricants: Temperature resilience and material compatibility
Silicone-based lubricants are commonly used in brake systems because they can withstand extreme temperatures better than other options. This feature allows them to endure the heat produced during braking without deteriorating over time, making them particularly suitable for vehicles that regularly undergo heavy or repeated braking. Their ability to maintain a consistent structure even under harsh conditions ensures that the lubricant remains effective and offers long-lasting protection to the brake system.
Furthermore, silicone-based brake greases are well suited for rubber and plastic parts frequently used in brake systems. This feature helps prevent the wear and tear of seals and bushings and prolongs the lifespan of brake parts. Nevertheless, a downside is that silicone lubricants might shift away from the intended area of application, which could decrease their efficiency over time.
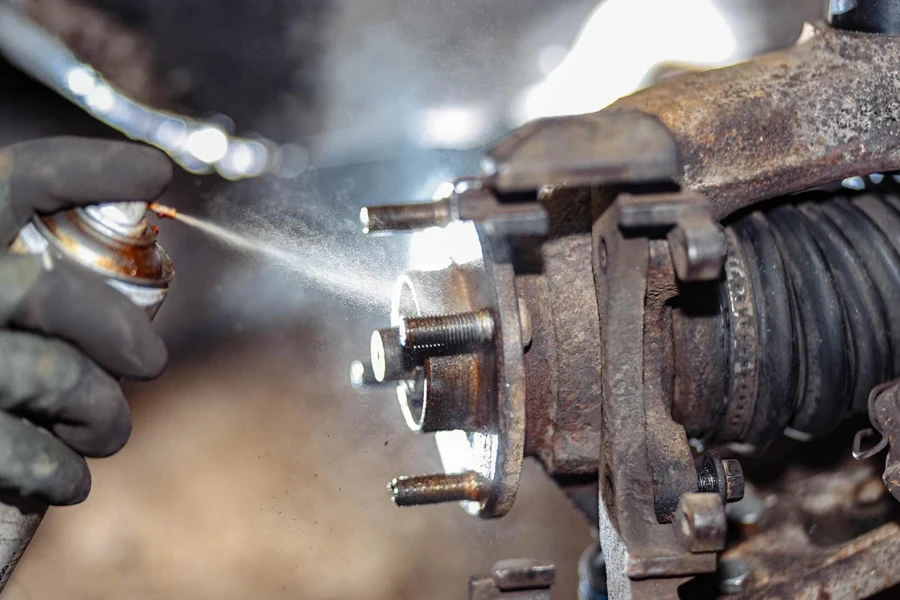
Ceramic brake lubricants: Durability and performance under stress
Lubricants made from ceramics are recognized for their toughness and efficiency in handling pressure situations, making them a preferred choice in demanding and high-performance scenarios. This is where they offer great protection against wear and rust, especially when brake systems are heavily used or experience heavy loads regularly. One key advantage of these lubricants is their ability to significantly reduce brake noise, a common problem encountered in high-performance braking systems.
Ceramic lubricants are also durable as they are engineered to outlast various other available lubricants. This characteristic diminishes the necessity for reapplication and upkeep, making them a practical option for vehicles and machinery that demand enduring and reliable performance in challenging environments. While ceramic lubricants may come at a high cost compared to other alternatives, their prolonged lifespan and top-notch protection typically make the expense worthwhile.
Market trends and developments
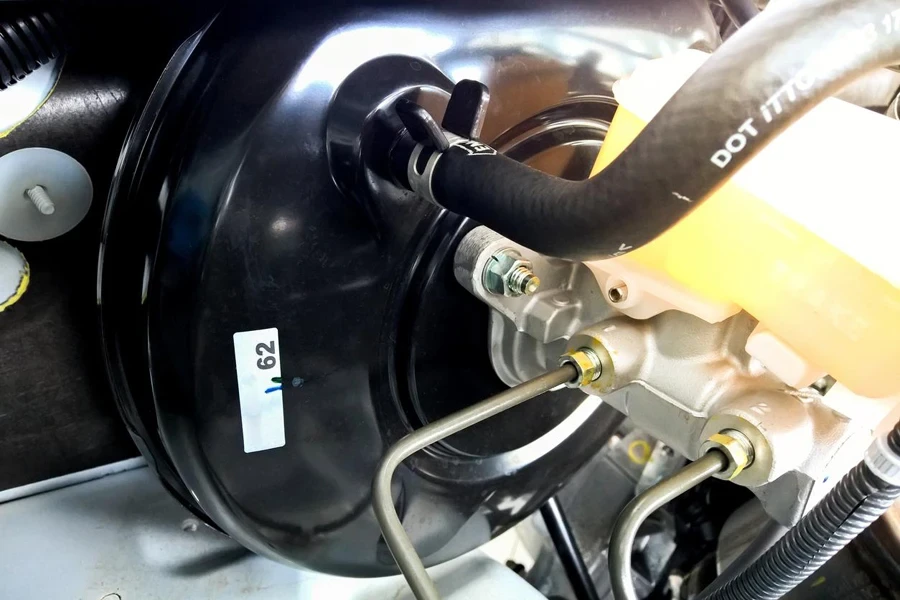
Growth of brake lubricants in the automotive sector
The automotive sector continues to influence the demand for brake lubricants as vehicle manufacturing expands worldwide. This is especially seen in regions such as Asia Pacific and Latin America, where the need for specialized lubricants is rising. By 2023, the global market for lubricants was valued at approximately USD 70.44 billion and is expected to reach USD 80.35 billion by 2032 due to factors like increasing vehicle ownership rates in developing areas and the growth of commercial vehicle fleets dedicated to logistics and transportation services.
Brake fluids are crucial for keeping vehicles safe and running smoothly by minimizing friction and wear. The rise in car production has created a need for top-notch lubricants tailored to the special braking requirements of these vehicles. Additionally, the surge in electric vehicle (EV) production has introduced new demands for high-performance lubricants, as these vehicles often require specific formulations to meet their unique braking system needs.
Shift toward more environmentally friendly and longer-lasting formulations
The brake lubricant market is changing due to considerations prioritizing sustainability and eco-friendly options. Regulations enforced by governments to promote acceptable lubricants (EAL) have motivated manufacturers to create products with minimal environmental impact. These EAL products are intended to lower emissions and prevent pollution in delicate ecosystems, driving the production of nontoxic brake lubricants.
The need for brake lubricants that last long is increasing in industries using heavy-duty vehicles and high-performance machinery. New formulations are developed to offer better wear resistance and longer intervals between applications with improved thermal stability levels. This shift towards durability is prompted by cutting down maintenance expenses and minimizing downtime, especially within commercial vehicle fleets and industrial settings.
In the evolving industry landscape, brake system solutions undergo enhancements to boost performance under various conditions, like temperature and pressure levels, thus extending the longevity of brakes overall. This becomes crucial in demanding scenarios where repeated braking actions intensify the wear and tear of lubricants at a high pace.
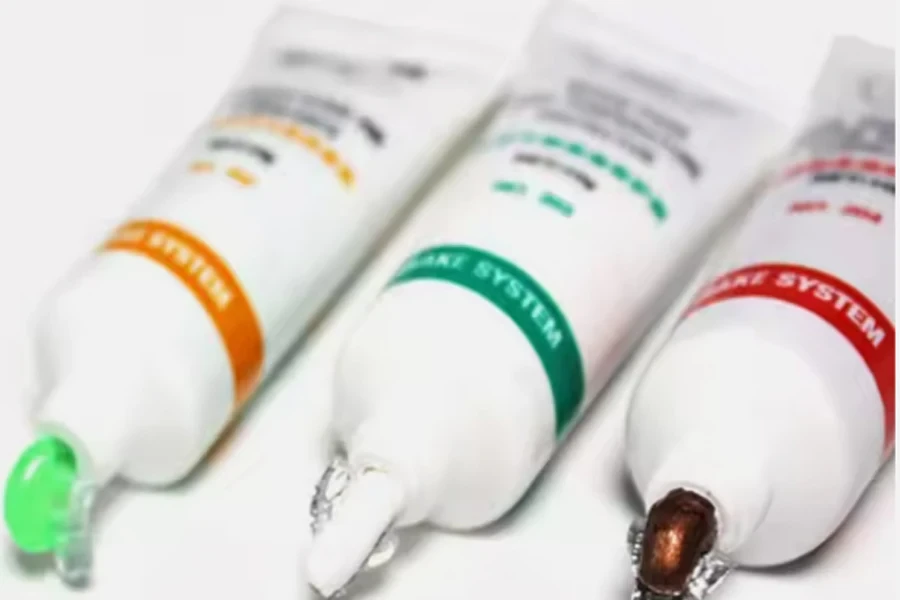
Critical factors to consider when choosing brake lubricants
Temperature tolerance: Ensuring performance in extreme heat
Brake fluids must endure the heat produced by braking systems in demanding conditions like high-performance or heavy-duty settings where temperatures can surpass 500°F. Suppose the lubricants are not up to handling heat levels; they may deteriorate, leading to reduced performance and posing risks to the braking system’s safety. Silicone-based lubricants, with their reputation for heat tolerance, are frequently suggested for use in scenarios with extreme temperature variations. Some artificial and polyglycerol-derived lubricants may also provide heat resistance based on their unique composition formulae. Choosing a lubricant with ideal temperature endurance is crucial for maintaining peak performance in demanding situations.
Compatibility with brake materials: Avoiding damage to plastic and rubber
Brake systems often include parts crafted from plastic and rubber, like seals and bushings, that are quite sensitive to the kind of lubricant employed in them. Particular lubricants derived from petroleum can lead these materials to expand and crack or break down with time. Silicone and polyglycerol-based lubricants typically work better with rubber and plastic elements, ensuring the durability of these materials in the long run. Using the wrong lubricant might cause components to wear out more quickly and the system to become less reliable; hence, choosing one compatible with the system ensures longevity.
Lubricant migration and retention: How to prevent product displacement
One prevalent problem with brake lubricants is migration. When the lubricant shifts away from its intended area of application, this can diminish application area effectiveness, resulting in friction increase, wearing down, or even causing failure to some parts. Specific silicone-based lubricants, suitable for high-heat scenarios, may be susceptible to migration over time. In response to this challenge, the industry has introduced denser formulations to minimize the risk of product displacement. Moreover, using synthetic mixtures and polyglycerol-based alternatives often results in better adherence over extended periods, offering dependable lubrication. Choosing a lubricant with strong retention capabilities guarantees steady effectiveness and lessens the need for frequent maintenance.
Ease of application: Considering dispensing methods
When it comes to applying brake lubricants, how easy it is is important, especially for tasks that require frequent upkeep. Lubricants come in various forms like sprays, pastes, and gels; each type serves a specific purpose. Sprays are great for covering areas fast, and gels offer a precise application for tasks like caliper pins. Opt for a simple lubricant that is simple to apply to save time and effort during maintenance tasks while enhancing productivity and reducing errors in the process.
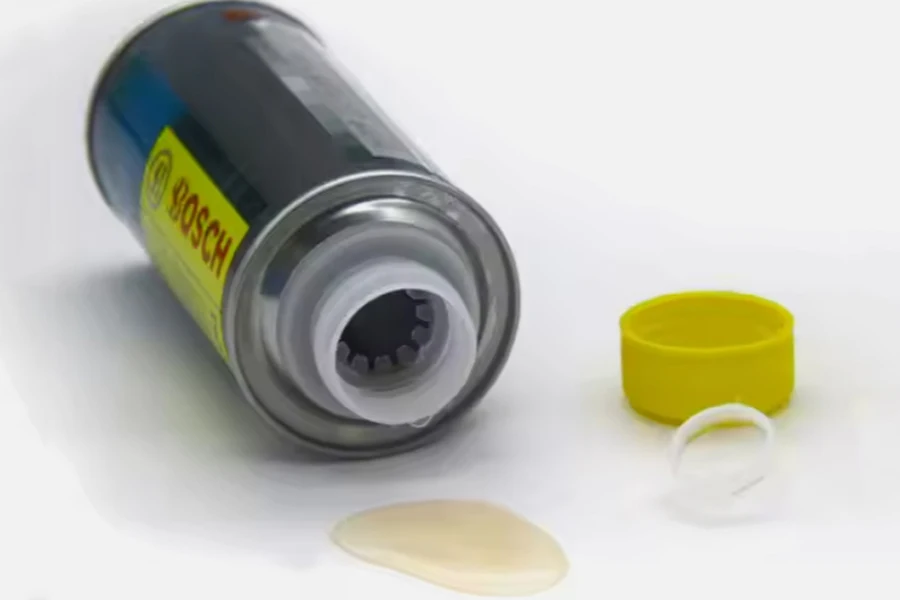
Top-performing products and their features
Leading silicone-based brake lubricants: Performance and compatibility
Silicone-based brake lubricants are well known for their ability to handle high temperatures and work well with various materials in the automotive industry. This type of lubricant is perfect for heavy-duty vehicles and those that demand high performance. One exceptional product in this field is the Permatex Silicone Ceramic Extreme Brake Lubricant. Its formula doesn’t melt at temperatures as high as 3000°F (1649°C) thanks to the ceramic solids added to it. This lubricant guarantees less brake noise and consistent performance over a long period. It also works well with plastic and rubber parts to help prevent them from wearing out over time.
Permatex silicone-based lubricants are also a good choice for vehicles facing various conditions since they stay reliable in hot and cold weather. It is perfect for tough rides, like trucks and electric vehicles that need to perform well in extreme situations.
Ceramic-based lubricants: Long-lasting options for heavy-duty vehicles
Brake lubricants made from ceramics are crafted to last long and perform well in scenarios with intense braking requirements. They are adept at minimizing wear and rust on metal components under extreme heat conditions. The AGS SIL Glyde Brake Lubricant stands out as a durable option in this segment because it blends silicone advantages with ceramic enhancements for enhanced longevity and efficacy.
When it comes to duty and commercial vehicles specifically, ceramic-based lubricants stand out because they provide lasting protection and minimize the need for constant reapplications. Their impressive resistance to temperatures and durability under intense braking conditions make them a top choice for industries that prioritize reliability and long-term cost savings.
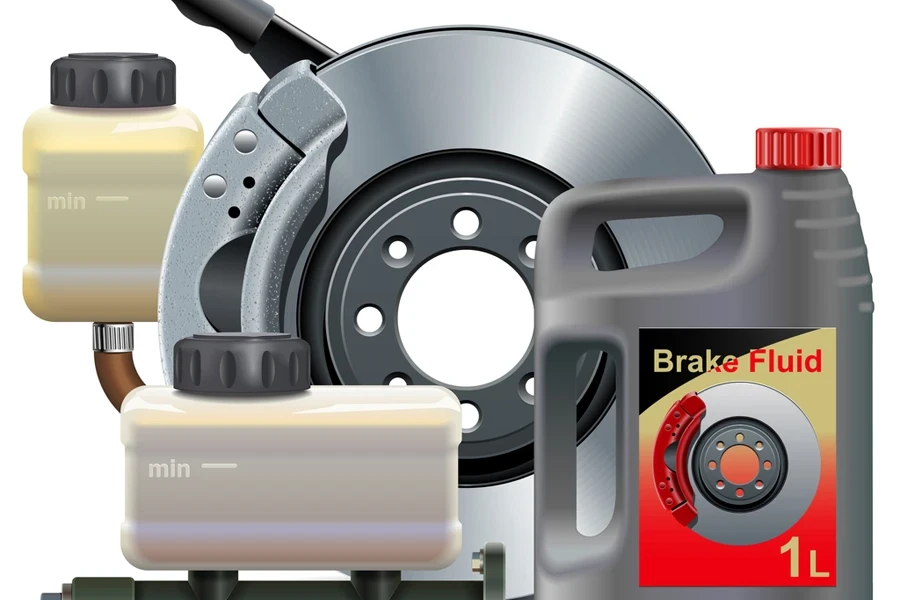
PFPE Lubricants: Balancing performance and environmental considerations
PFPE lubricants are specially designed for challenging environments. They are known for their ability to withstand a wide range of temperatures and resist chemicals effectively. These artificial mixtures have gained popularity due to their top-notch performance and positive environmental impact. Brands like MOLYKOTE offer PFPE lubricants that have heat resistance capabilities and are compatible with various materials such as plastics and elastomers.
PFPE lubricants stand out for their performance in high temperatures and chemically active settings, which makes them perfect for precision braking systems. Moreover, their inert nature prevents chemical reactions and ensures long-lasting resilience even in corrosive surroundings. Synthetic blends are gaining popularity for their eco-friendly benefits, with longer intervals between applications leading to reduced waste production.
Conclusion
Choosing the right brake lubricant is crucial for maintaining the efficiency and lifespan of brake systems in different industries. Factors to consider include how well the lubricant handles temperature changes, its compatibility with materials used in brakes, how long it lasts after application, and how easy it is to apply. Silicone-based lubricants perform best at high temperatures, while ceramic-based ones are known for their durability in tough situations. PFPE synthetic blends are an eco-friendly option that offers great thermal stability and resists chemicals well. Each type of lubricant has benefits that suit the specific needs of various braking systems to enhance maintenance efficiency and cut expenses while guaranteeing brake performance in the long run.