Table of Contents
● Introduction
● Market overview
● Different types and their features
● Things to consider when selecting products
● Conclusion
Introduction
Truck brake pads are essential for maintaining the safety and performance of heavy-duty vehicles, especially in demanding conditions. With the growing commercial vehicle market, choosing the right brake pads has become crucial for fleet managers and business owners. The various materials and designs available today offer options to meet specific performance needs, from durability to cost-efficiency. Understanding these options helps businesses make informed decisions that align with safety regulations and operational demands. Selecting the right brake pads can significantly impact the longevity and reliability of a fleet.
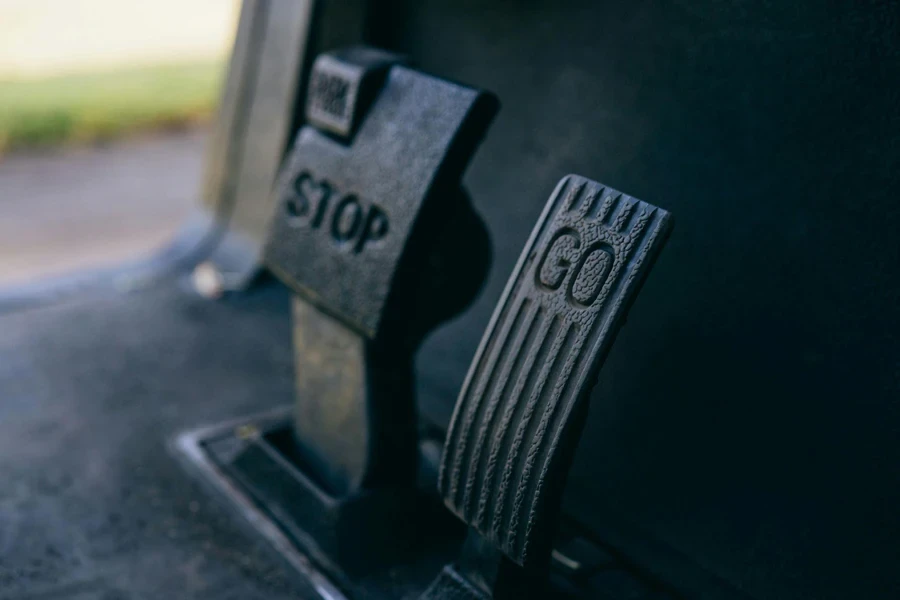
Market overview
The global truck brake pad market is expected to reach USD 3.07 billion in 2024 and grow further to USD 5.93 billion by 2031, with a steady CAGR of 8.6%, according to Data Bridge Market Research. This robust growth is fueled by increasing demand for commercial vehicles across industries like logistics, construction, and mining, as well as the implementation of stringent safety regulations that mandate reliable braking systems. Additionally, adopting advanced materials and technologies, such as ceramic and low-metallic pads, improves durability and braking performance, further boosting the market. Fleet operators and manufacturers focus on high-performance, longer-lasting brake pads to reduce operational costs and improve vehicle efficiency.
Thanks to significant vehicle sales growth in countries like China and India, the Asia-Pacific region leads the market. China’s vehicle sales alone surpassed 30 million units in 2023, which has spurred demand for high-quality brake pads. North America and Europe also hold substantial market shares, driven by strict regulatory standards, technological advancements, and the increasing adoption of electric vehicles requiring specialised brake pads. However, the market faces challenges such as the growing popularity of regenerative braking systems, particularly in electric and hybrid cars, which reduce wear on conventional brake pads, and the rise of ride-sharing services, which could shift vehicle ownership trends, slightly dampening future brake pad demand.
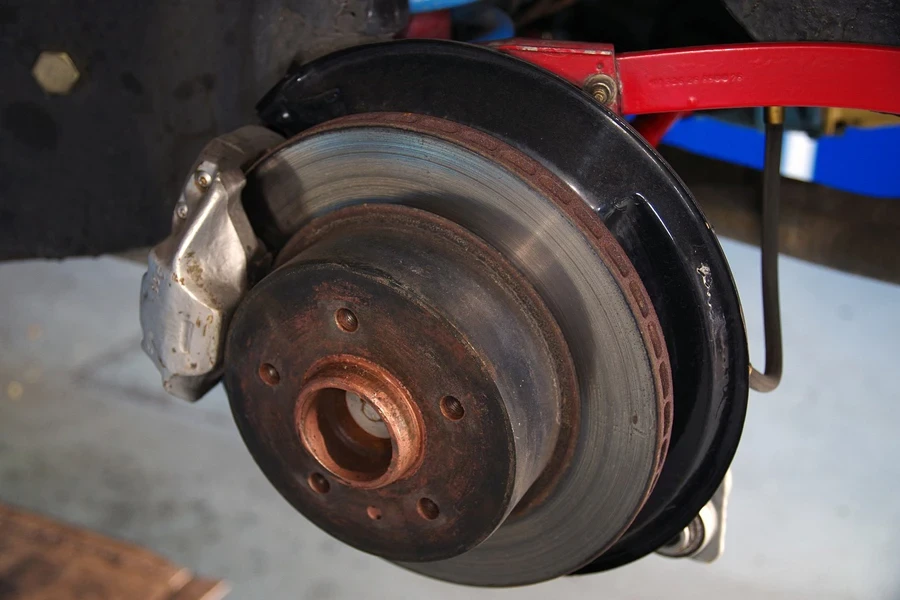
Different types and their features
Truck brake pads come in various types, each designed to meet specific performance requirements based on the truck’s use, load capacity, and driving conditions. Understanding each type’s material composition and characteristics helps fleet managers choose the most suitable brake pad for their vehicles.
Semi-metallic brake pads
Semi-metallic brake pads are made from a combination of metals such as steel, iron, and copper, bonded together with friction materials. These pads are known for their durability and excellent performance in extreme conditions, such as heavy loads or high-speed braking. Semi-metallic pads can withstand higher temperatures than other types, making them ideal for trucks operating in harsh environments. However, they tend to produce more noise and dust and can wear down brake rotors faster than other pads. According to Global Market Insights, semi-metallic pads are common for heavy-duty trucks due to their strength and heat dissipation properties.
Low-metallic brake pads
Low-metallic brake pads are designed with a small percentage of metal, often less than 30%, mixed with organic materials. They are effective in high-heat applications, such as long-distance hauls or frequent braking scenarios. These pads provide good braking power at a lower cost, making them a budget-friendly option for truck operators. However, low-metallic pads produce more noise and brake dust than ceramic or organic pads, which can concern some fleet operators. Their high thermal conductivity helps dissipate heat efficiently but may require more frequent maintenance due to faster wear rates.
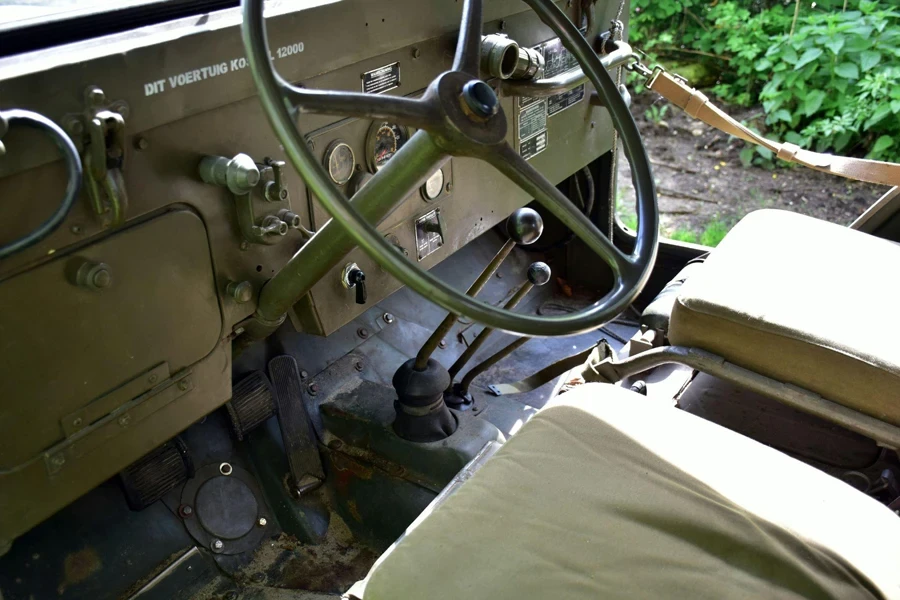
Non-asbestos organic (NAO) brake pads
NAO brake pads are made from organic materials such as fibres, rubber, and resins, making them environmentally friendly and safer to manufacture. These pads are typically softer and quieter than their metallic counterparts, which makes them suitable for lighter trucks that do not experience extreme braking conditions. According to industry reports, NAO brake pads provide consistent performance with less noise and dust, although they may wear out faster and may not be ideal for heavy-duty applications. They are commonly used in lighter trucks or in regions where environmental regulations are stricter on the materials used in brake pads.
Ceramic brake pads
Ceramic brake pads comprise ceramic fibres, bonding agents, and filler materials, offering high durability and low noise. These pads are well-suited for heavy-duty applications because they can withstand high temperatures without losing braking power. They produce less dust and are quieter than metallic options, making them a preferred choice for trucks that require long-lasting performance with minimal maintenance. However, ceramic brake pads are more expensive than other types, making them a costlier investment upfront. According to Global Market Insights, ceramic pads are increasingly popular in high-performance trucks where consistent, reliable braking is essential, especially in commercial fleets focused on minimising maintenance costs.
Things to consider when selecting products
Choosing the right truck brake pads involves a balance of several critical factors. Truck operators and fleet managers must consider the vehicle’s weight, load capacity, performance needs, regulatory requirements, and long-term maintenance when selecting brake pads to ensure optimal safety and cost-efficiency.
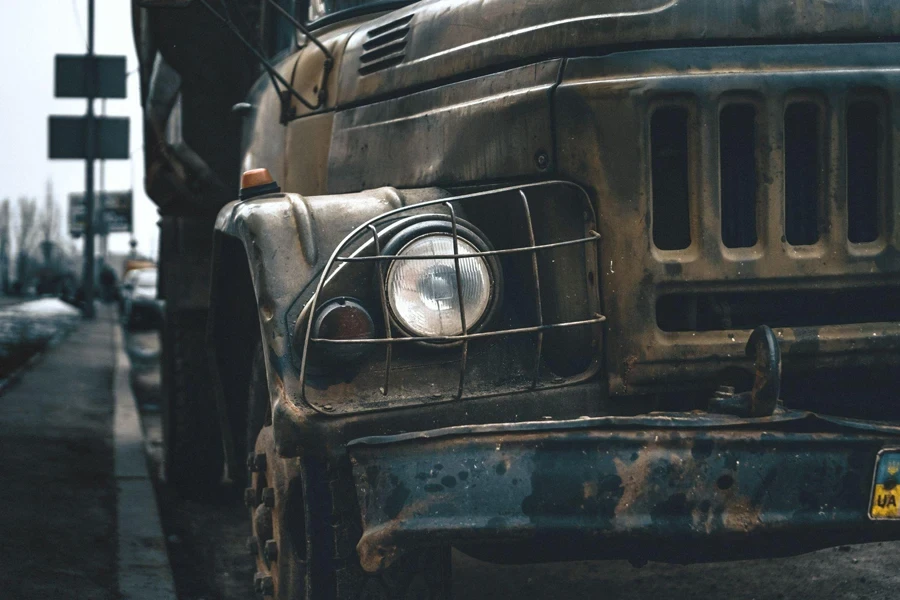
Vehicle type and usage
The weight and load capacity of the truck plays a significant role in determining the type of brake pad required. Heavier trucks, such as those used for long-haul freight or construction, demand brake pads that can handle extreme loads and frequent, hard braking. Semi-metallic or ceramic brake pads are often preferred for these applications due to their heat resistance and durability under heavy loads. Non-asbestos organic (NAO) brake pads may be a better fit for lighter trucks or those operating in less demanding conditions, as they provide sufficient braking performance with less wear and noise. According to Global Market Insights, selecting the right type of brake pad based on vehicle usage helps ensure consistent performance. It prolongs the lifespan of both the brake pad and rotor.
Performance vs. cost
Balancing performance with cost is a key consideration when selecting brake pads. While high-performance pads, such as ceramic or semi-metallic, offer longer lifespans and better resistance to wear, they come at a higher price point. For fleet operators managing multiple vehicles, the initial investment can be significant. Low-metallic and NAO pads, although more affordable, may require more frequent replacement, leading to higher long-term maintenance costs. According to Data Bridge Market Research, the decision should be based on the truck’s operational demands—high-performance pads are essential for trucks facing extreme driving conditions. In contrast, budget-friendly options may be sufficient for lighter loads or less frequent use.
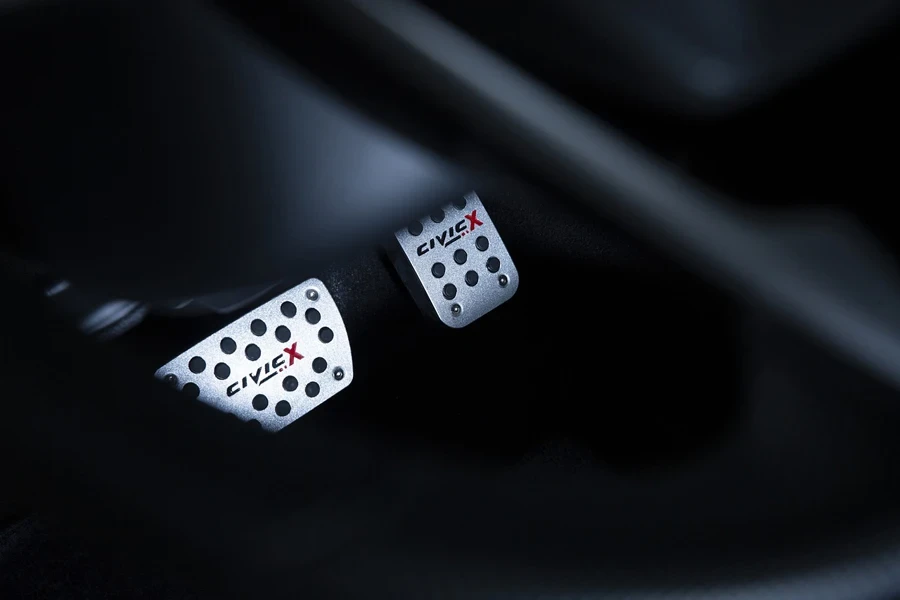
Regulatory compliance
Compliance with local safety and environmental regulations is crucial in brake pad selection. Due to ecological concerns, some regions have strict limits on copper content in brake pads, pushing manufacturers to develop alternatives like ceramic or low-metallic pads. Additionally, regulations on noise pollution may necessitate the use of quieter brake pads, such as NAO or ceramic, especially in urban or residential areas. According to Global Market Insights, adhering to these regulations avoids penalties. It ensures that trucks meet industry standards for safety and environmental impact, particularly as governments globally move toward greener technologies in the automotive industry.
Longevity and maintenance
Brake pads’ lifespan and maintenance intervals directly impact the total cost of ownership for fleet operators. Semi-metallic and ceramic pads typically last longer and require fewer replacements, making them ideal for fleets that minimise downtime and maintenance costs. However, regular inspections and timely replacements are essential to prevent excessive wear that can damage the brake rotors, leading to higher repair costs. According to Data Bridge Market Research, operators should carefully consider the expected lifespan of the brake pads relative to the truck’s operating conditions and schedule maintenance accordingly to maximise efficiency and reduce overall costs.
Conclusion
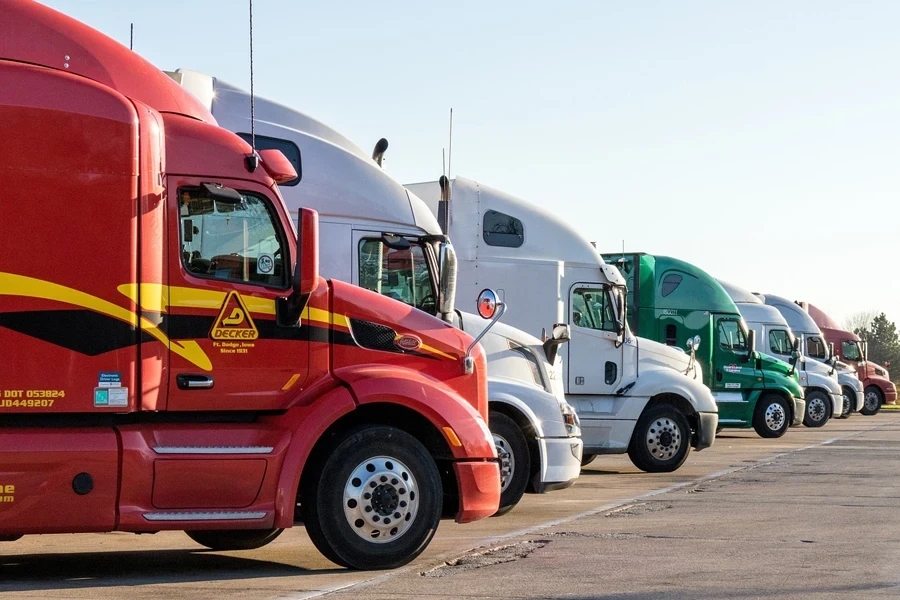
Selecting the right brake pads for your truck fleet requires careful consideration of multiple factors, including performance, cost, and regulatory compliance. Semi-metallic, low-metallic, NAO, and ceramic brake pads offer unique advantages depending on the vehicle’s load, driving conditions, and environmental requirements. Fleet managers can ensure safer and more efficient operations by understanding each type’s features and limitations and balancing long-term maintenance needs with upfront costs. Compliance with local safety and environmental regulations is essential to avoid penalties and maintain industry standards. Making informed decisions based on these factors will help optimise vehicle performance, reduce downtime, and extend the lifespan of your fleet’s braking system.