An entrepreneur operating a metalworking shop or factory should invest in suitable machines to succeed in the metalworking industry. Due to technological advancements, these industrial tools have evolved, making it easy to create desired metal parts in any shape and size.
The evolution of these tools has contributed to the invention of many machines that can produce complex shapes of metal parts with reduced human effort and maximum efficiency. And since one can choose from various metal working machines, it is essential to understand the different types of machines out there and their functions. With this in mind, this article will discuss 11 standard machines used in the metalworking industry, so that buyer’s can confidently source the machines they need.
The global metalworking machinery market
The global market size for metalworking machinery is projected to expand at a compound annual growth rate (CAGR) of 9.4%, from US $230,48 billion in 2021 to US $364.92 billion in 2026.
This growth is propelled by several factors, including:
- Stable economic growth in many developing and developed countries, propelling investments in the end-user markets.
- Recovering commodity prices following adverse effects of Covid-19.
- Advanced computer numerical control (6-axis CNC) milling machines, facilitating the conversion of raw metal bars into final complex components.
Type of metalworking machines
Those working in a metalworking factory know that high-quality products can only come from the right industrial equipment. Below is a list of standard metalworking machines used for specific operations, including metal cutting and shaping.
1. Horizontal lathe machine
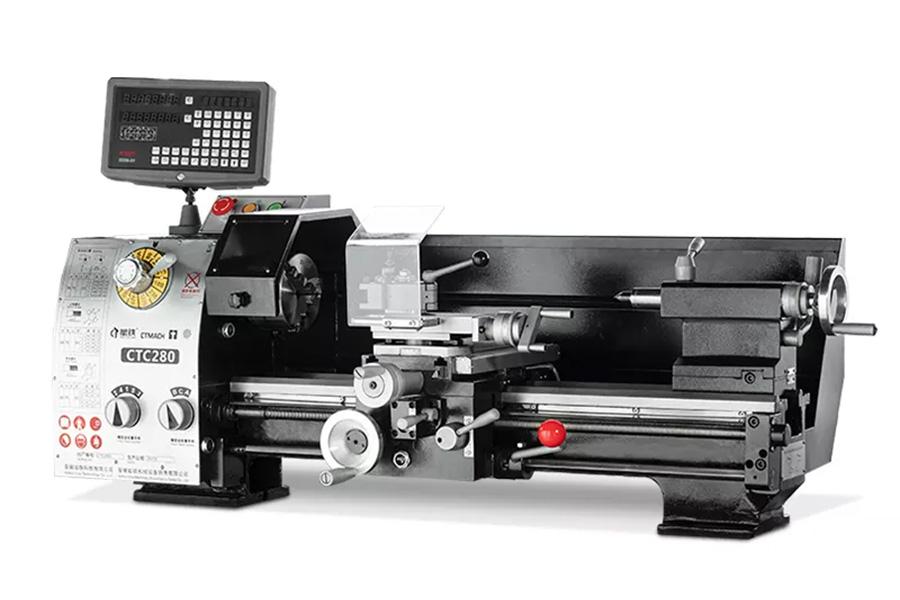
This machine is often used in rotating the piece of material one is working on. Lathes can be utilized to cut, knurl, sand, drill, thread, bore, turn, and face plastics, wood, and metallic parts. They come in a range of sizes and orientations with several accompanying accessories to enhance their functions.
Most metal workers who deal in precision metal work enjoy working with lathe machines. For instance, factories producing light machinery will likely use lathe machines to improve their products.
2. Vertical lathe machines (VTLs)
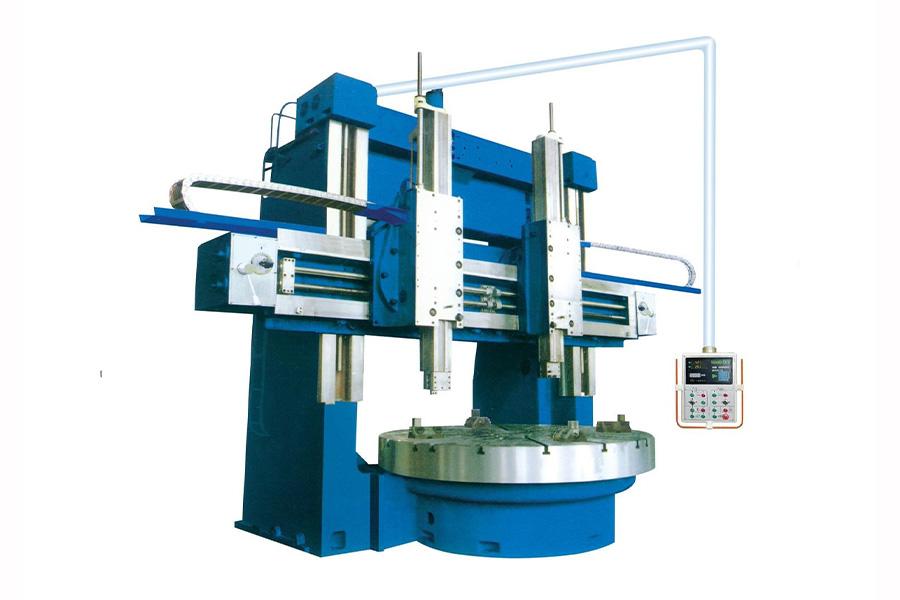
VTLs are one of the most multifunctional tools in the metal-working industry. They are often used for machining hardy alloys, high-speed steel tools, ceramic tools, and ferrous and non-ferrous metals.
Furthermore, they can work large metal parts with a diameter ranging from 1 to 20 meters. They deliver efficient metal cutting functions including cylindrical boring, turning, surfacing, and tapering.
3. Milling machines
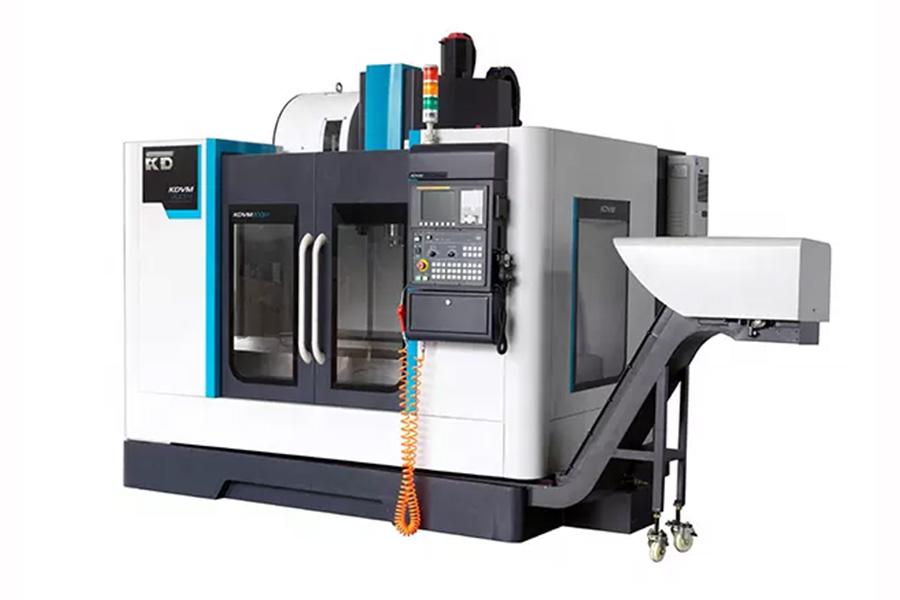
Milling machines have several functions when processing various materials in industrial and manufacturing applications. They employ rotating cutting tools to refine workpieces through drilling, milling, reaming, and broaching.
Milling machines are categorized depending on the direction of their spindle rotation. The vertical machines have their spindles at the right angle to the workpieces. Horizontal milling machines have the rotating cutter horizontally oriented and run parallel to the workpiece. In contrast, the universal milling machine can be horizontal or vertical, depending on the needs of specific applications.
4. Broaching machines
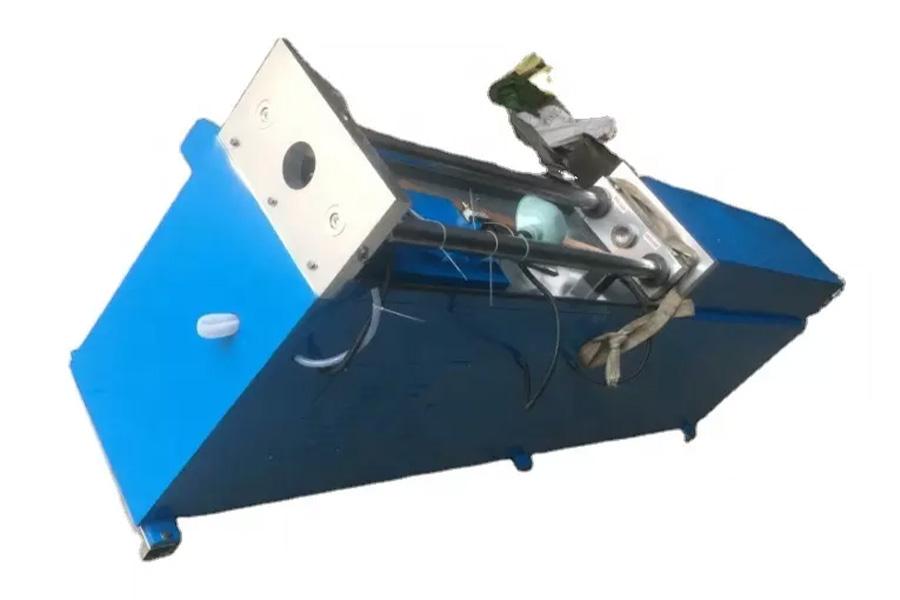
The operator can use a broaching machine to form, cut, and shape various materials. The machine employs a broach or toothed tool to remove materials and refine the workpiece. The process can be linear or rotary, depending on how the machine is placed with the workpiece.
For example, when removing materials on the workpiece, the rotary broaching machine rotates its toothed tool to create products for professionals handling metalworking projects.
5. Grinding machine
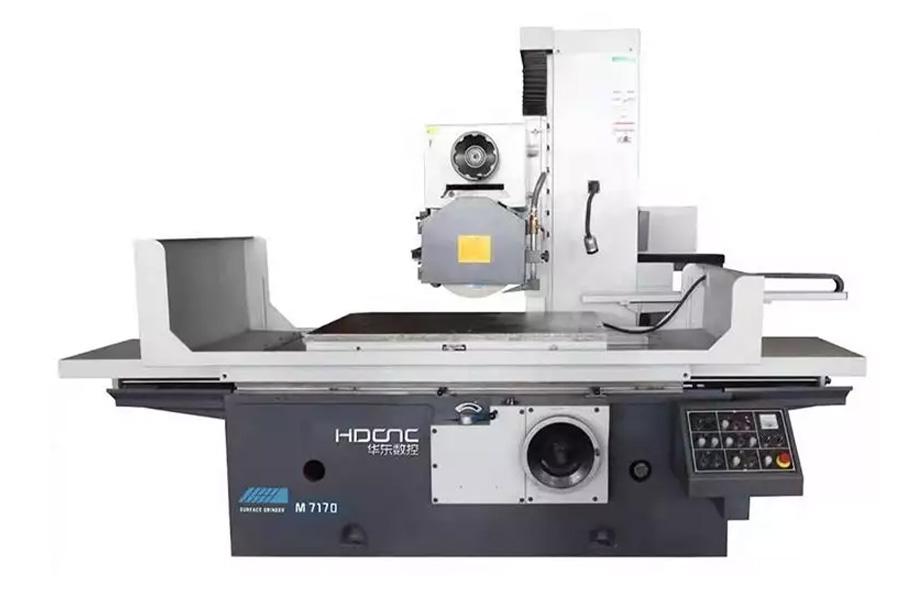
Grinding machines are popular tools in the metalworking industry since they are used to shape or finish metal surfaces. Grinders use abrasion to remove unwanted material from the workpiece. Since the grinding process generates heat, most modern grinding machines are fitted with water-cooled systems, oil-based coolants, or air-cooling systems to keep the workpiece cool.
The type of grinding machine one should select depends on the material being worked on and the intended result. For instance, more rigid materials may need stainless steel grinding plates, while softer materials will do well with aluminum plates.
Grinding machines can also be used as cutting tools where other devices cannot produce the shape required.
The metalworking industry needs different grinders that suit varied purposes, such as holding and making a specific workpiece shape.
6. Drilling machines
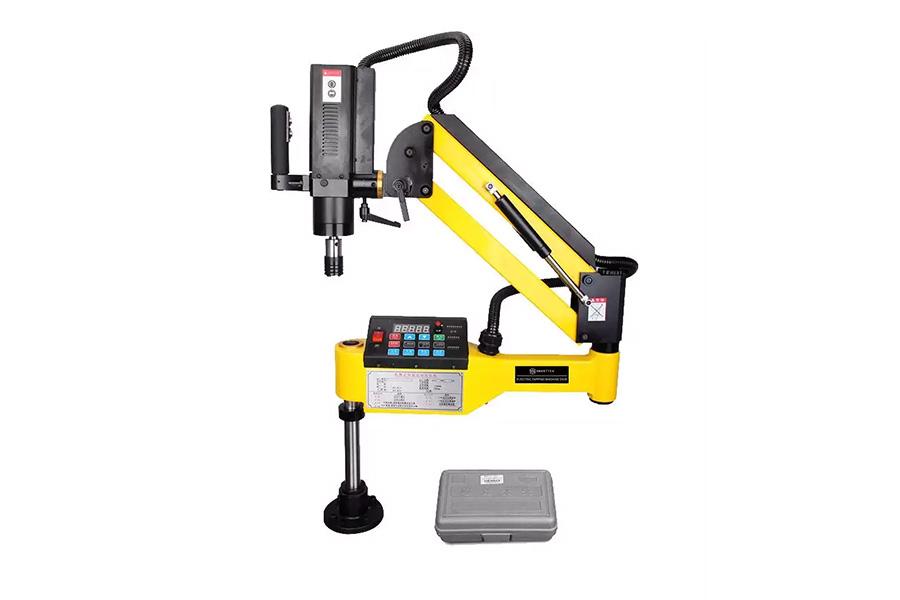
The metalworking industry involves drilling holes in metals and other materials such as concrete, plastic, and wood. Drilling machines help create these holes.
They are categorized into two types: gang and radial drilling machines. Gang drilling machines have several spindles mounted on a fixed table. On the other hand, radial drilling machines have their spindle mounted on a rotating arm.
Although there are manually powered drilling machines, most people prefer electric-powered machines due to their precision and ability to work with delicate work. Nevertheless, manually-powered drilling machines are still valuable, especially when portability is needed or when working with incredibly soft materials.
7. Shearing machine

Please don’t confuse this machine with those used for shearing sheep! This shearing machine is used to cut metal sheets into desired sizes and shapes without forming chips or residue, thus reducing harmful debris in the air and on the floor. This beginner’s buying guide to shearing machines is a good place to start for those who do not know what the machine does.
8. Hobbing machines
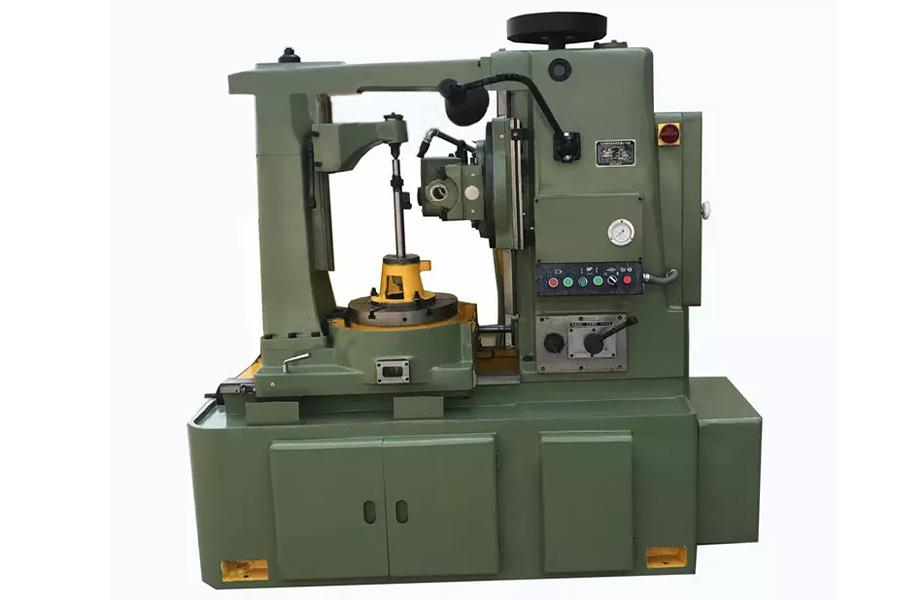
Different industries use metalwork to produce special gears, splines, high-precision shafts, and other cylindrical parts for various applications. Hobbling machines come in handy to help in sorting out these needs. Fortunately, they are budget-friendly and require few people to run, but they still produce large quantities of metal parts daily.
9. Press brake
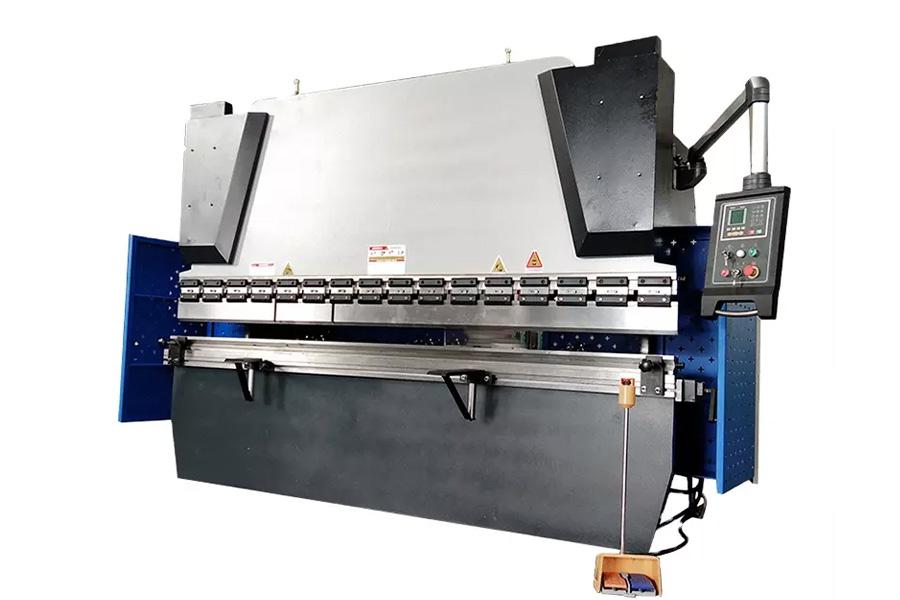
Press brakes have been used for centuries in the metalworking industry for processing metal components. However, with advanced technology, press brakes have become sophisticated tools that use computer technologies and hydraulic systems to bend metal sheets. They can turn or cut metal into unique forms and shapes using a die or punch set at specific angles.
10. Machining center
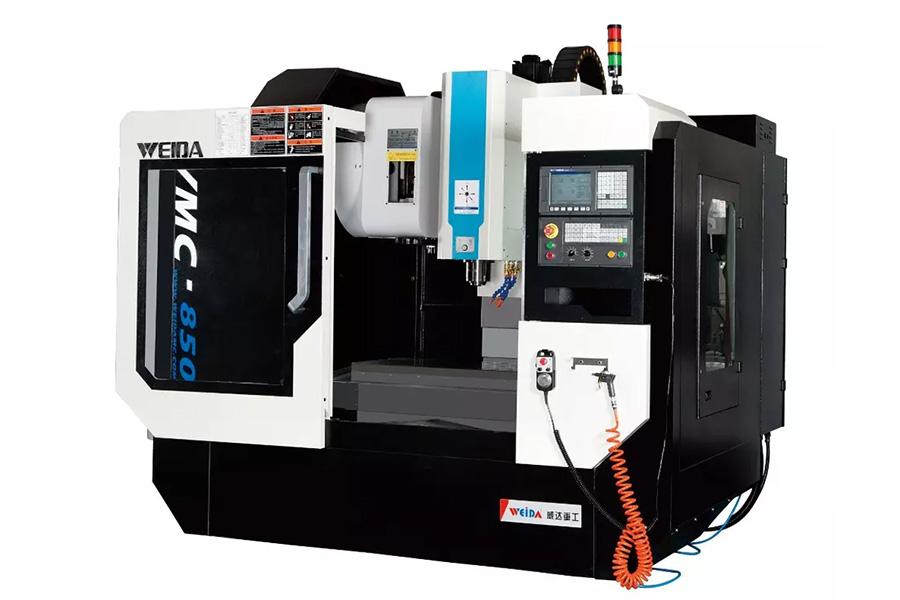
Machining centers are the queen and kings of machines in the metalworking industry. They are multi-functional machines that help conduct several sophisticated mechanical operations, including dull, milling, drilling, and threading because they carry many tools in the changer.
Machine centers vary depending on their functions, dimensions of the working area, and the number of axes; however, they are mainly divided into vertical and horizontal machining centers, depending on the position of the spindle axis.
11. Sandblasters
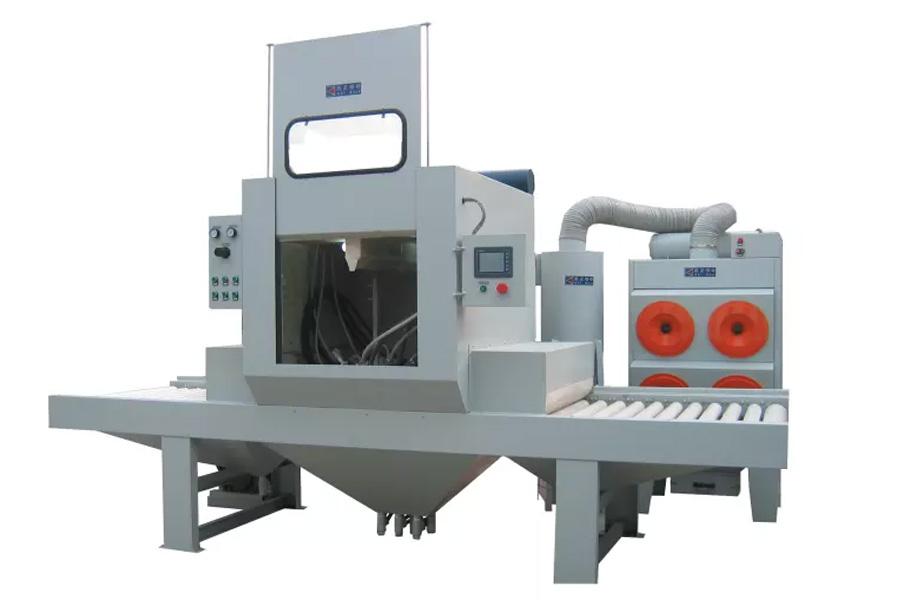
A sandblaster propels fine sand particles or abrasive media at high speed to perform several functions. It is employed in the metalworking industry to clean or remove paint coatings, shot-peening, or improve the surface of different materials.
Facility owners, contractors, rail yards, shipyards, and separate mobile applicability need durable sandblaster machines for corrosion control and cleaning. Although they require specific skills, the machine’s mechanism is easier to understand.
Sandblasters can work with sand, soda, or beads to clean surfaces. One can also use pressured air, fluid, or vapor to produce a suction that pulls abrasive media into the gun’s nozzle before hitting the workpiece surface.
Factor to consider when choosing metalworking machines
Although some metalworking machines are versatile, you can still choose the wrong machine if you don’t exercise caution. With that in mind, these are some of the key factors worth examining before investing in a machine.
The material to be processed
The thickness, type, and consistency of the material being worked on determs the metalworking machine one chooses. For instance, light aluminum or thin gauge metals require an electrically or air-operated shearing machine.
Besides the type of material, it is also vital to consider its structure to determine which machine will best fit it.
The kind of machining to be done
While some metal working machines are versatile, the operator may need robust and sophisticated machines for specific applications. For example, drilling machines can be used for piercing, but they are not suitable for grinding workpieces.
Productivity
Every business wants to operate optimally and enhance its productivity. The metal working machine should be reliable and durable for continual production. It should also produce a maximum number of metal parts daily to improve profitability. For instance, electrically-powered drills are better for mass drilling than manual drilling machines.
Dimensions of workpieces
Larger workpieces require bigger metalworking machines, while smaller materials could require portable and manual-operated machines. The shape and number of axes of the workpiece will also determine the idea type of metalworking machine one should use.
Accuracy levels
The accuracy level in the metalworking field is the machine’s ability to match the specified measurements in the design. The metalworking machine’s accuracy and precision levels are valuable in ensuring proper mechanical functionality of metal parts and customer satisfaction. Furthermore, accuracy and precision help ensure that the produced metal parts are compatible.
Conclusion
The metalworking industry is full of machines, which can confuse many buyers. However, one can maximize their chances of making a good decision through research and consulting experts. One economically viable option is purchasing versatile machines that perform multiple functions. Ensure the device has high productivity and accuracy levels to satisfy customer demands. And for those who want to learn more, also check this guide on selection tips for a metal working factory.