Skid plates have become indispensable in safeguarding vehicles from undercarriage damage caused by rugged terrains and road debris. As off-roading gains momentum and vehicle performance expectations rise, the demand for durable, lightweight, and advanced skid plates continues to grow. Innovations in materials such as aluminum and composites are reshaping the industry, aligning with the needs of electric and fuel-efficient vehicles. For industry professionals and buyers, understanding the latest market trends and product features is crucial to making informed decisions. This guide provides a detailed analysis of the market, explores the diverse options available, and highlights key considerations for selecting the best skid plates.
Table of Contents
Market overview: Skid plates on the rise
A growing industry
Regional leaders
Driving trends and material advancements
Shield options: A detailed look at types and materials
1. Front center skid plates
2. Full belly skid plates
3. Suspension skid plates
4. Material matters
5. Fit and installation options
Choosing wisely: Key factors for the best skid plate
Match terrain needs
Assess material trade-offs
Ensure proper fitment
Installation ease
Conclusion
Market overview: Skid plates on the rise
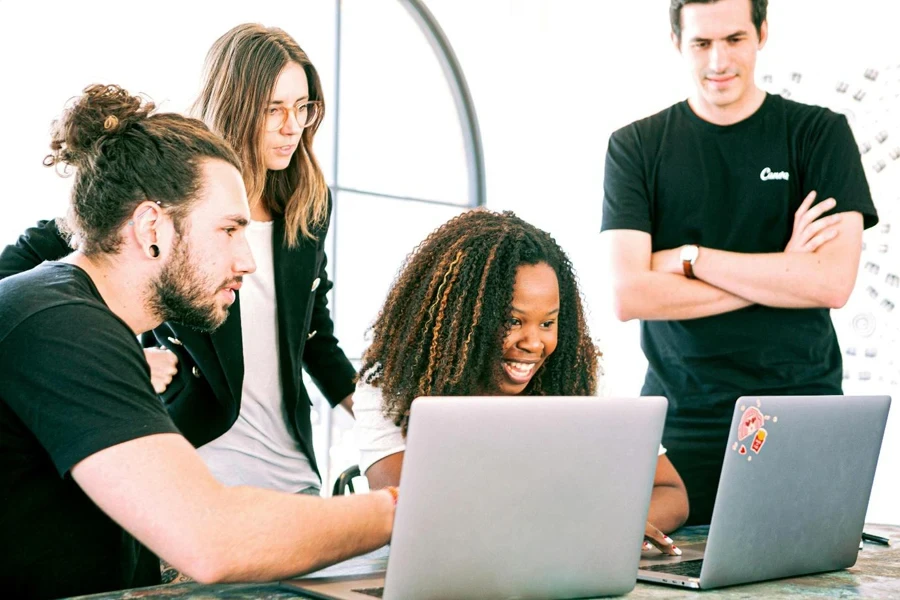
A growing industry
The global skid plate market is experiencing robust growth, with its value projected to increase to USD 6.5 billion by 2032, reflecting a CAGR of 4.22%. This expansion is fueled by the rising popularity of off-road and sport utility vehicles (SUVs), which demand enhanced undercarriage protection to navigate rugged terrains. Manufacturers are also targeting growing segments like electric and hybrid vehicles, where innovations in lightweight materials such as aluminum and composites are critical to maintaining efficiency and sustainability.
Regional leaders
North America and the Asia-Pacific (APAC) regions dominate the market, with North America accounting for a significant share due to its established off-roading culture and high adoption of advanced automotive technologies. Meanwhile, APAC’s expanding automotive production, coupled with a surge in off-road vehicle sales, positions it as a rapidly growing market. For example, North America’s market is expected to grow up to USD 1.85 billion by 2032, driven by demand for durability and enhanced safety features.
Driving trends and material advancements
Off-roading culture and increasing consumer awareness of vehicle protection are key drivers of this market. With advancements in material technology, manufacturers now offer skid plates made from steel for strength, aluminum for lightweight performance, and composites for corrosion resistance. These materials balance protection and weight, making them suitable for diverse applications. Innovations such as high-strength plastics and modular designs further enable customization and sustainable practices, addressing both functional and environmental concerns.
Shield options: A detailed look at types and materials
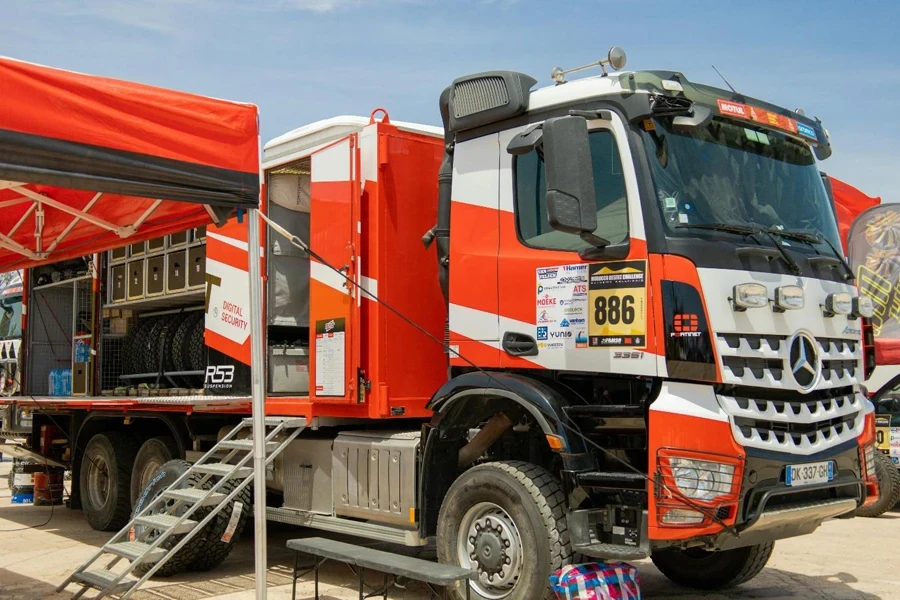
1. Front center skid plates
Front center skid plates are designed to shield critical components like radiators, oil pans, and engines from impacts and debris. These plates are typically crafted from 1/8-inch-thick high-strength steel, which can withstand impacts of up to 20,000 psi without deforming. For lightweight vehicles, 5052-H32 aluminum alloy is a popular alternative, offering high corrosion resistance and a weight reduction of up to 40% compared to steel. Mounting is typically achieved through pre-drilled bolt holes aligned with factory mounting points, ensuring secure and vibration-free installation.
2. Full belly skid plates
Full belly skid plates provide comprehensive protection for the vehicle’s undercarriage, including the transmission, fuel tank, and transfer case. These plates are often constructed from 3/16-inch-thick hot-rolled steel, offering superior tensile strength of 58,000 psi to handle the severe impacts encountered during activities like rock crawling. Some premium designs incorporate reinforced cross-braces to enhance rigidity and reduce stress under high loads. Due to their size, full belly plates may weigh upwards of 100 lbs, necessitating precise customization to ensure they don’t hinder ground clearance or drivetrain performance.
3. Suspension skid plates
Suspension skid plates are engineered to protect components like control arms and shock mounts. Constructed from 6061-T6 aluminum, these plates deliver an optimal balance between lightweight construction and impact resistance. They are designed to dissipate energy from sharp hits, with structural ribbing and stamped contours that increase rigidity while maintaining flexibility to absorb shock forces. Installation typically involves adjustable clamps or brackets, accommodating suspension movement without compromising coverage.
4. Material matters
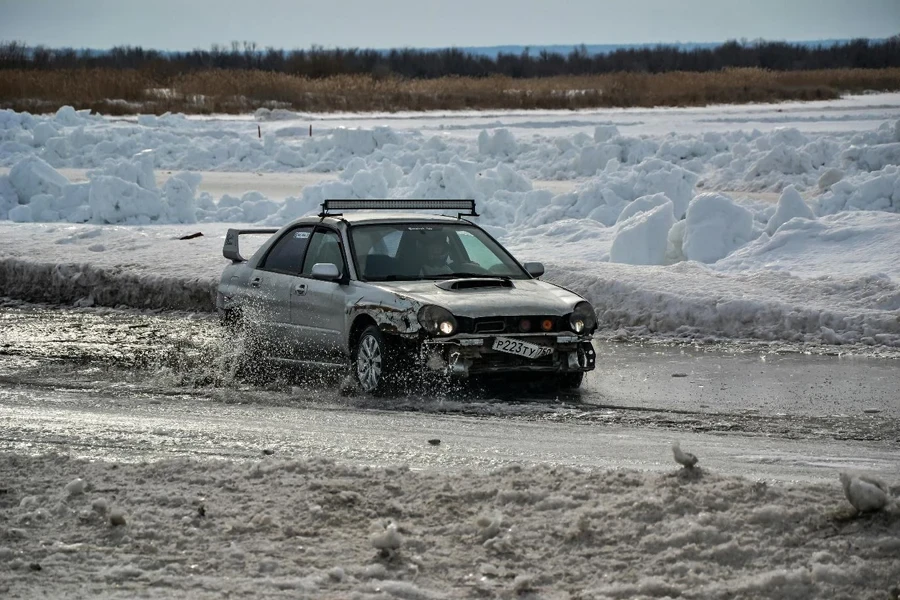
Material selection directly affects the performance of skid plates under different conditions. Steel, particularly grades like A36 or 1045, is favored for its ability to withstand severe impact, with yield strengths reaching 36,000 psi or higher. However, the trade-off is weight, as steel plates can add significant mass, impacting fuel efficiency. Aluminum alloys like 7075-T6 are often used in premium applications, offering a 30% higher strength-to-weight ratio compared to standard aluminum. Composite materials, including Kevlar-reinforced polymers, provide excellent abrasion resistance and thermal stability but are more suited to specialized uses due to higher costs.
5. Fit and installation options
Skid plates come in universal, custom-fit, and integral designs, each with technical benefits. Universal plates are often adjustable, with slotted mounting holes that can accommodate variations in vehicle chassis dimensions. Custom-fit plates use CAD-optimized designs tailored to specific vehicle models, ensuring tolerances within ±1 mm for precise coverage and minimal vibration during operation. Integral designs incorporate skid plates into other components, such as bumpers or side guards, and often include laser-cut reinforcements for enhanced durability under stress. For ease of maintenance, many modern designs feature quick-release panels to access oil pans or transmission drain plugs without full removal.
Choosing wisely: Key factors for the best skid plate
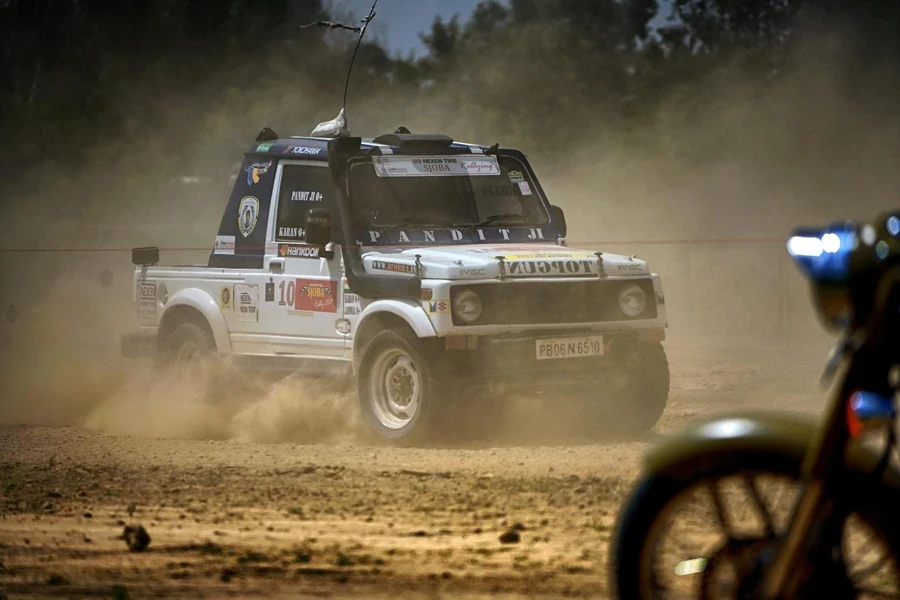
Match terrain needs
The terrain a vehicle is likely to encounter should heavily influence the choice of skid plate. For vehicles primarily operating on sand, mud, or clay surfaces, lightweight skid plates made from 1/8-inch aluminum are ideal due to their reduced weight and minimal impact on vehicle performance. In contrast, off-roaders tackling rocky, gravel-filled, or uneven trails require skid plates made from 3/16-inch steel for enhanced durability and resistance to punctures. Plates designed for harsh terrains often include reinforced edges to withstand lateral impacts, which are common in environments with sharp rocks or tree roots.
Assess material trade-offs
Material selection is critical to achieving the right balance between strength and weight. Steel plates, particularly hot-rolled variants, offer exceptional tensile strength but can add up to 50-100 lbs to a vehicle, potentially affecting fuel economy and handling. Aluminum plates, particularly 5052-H32 alloy, weigh approximately 30% less than their steel counterparts, offering significant advantages for vehicles requiring agility, such as those used in sand dune racing. Composite plates, though lighter, often feature layered construction for added strength but can be less cost-effective for general use.
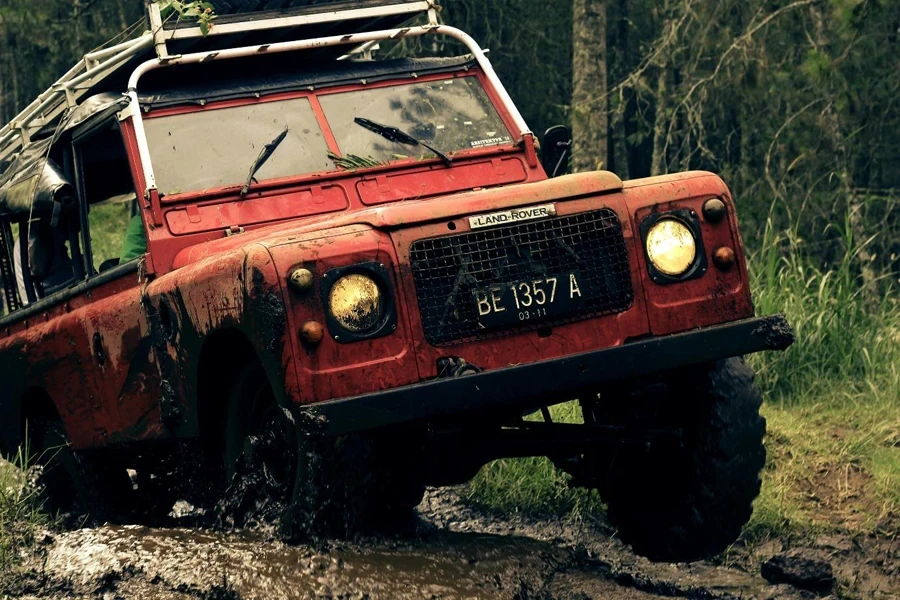
Ensure proper fitment
Skid plates must fit seamlessly with a vehicle’s existing structure to provide maximum protection. Custom-fit plates, often designed using laser scanning and CAD modeling, ensure tight tolerances, typically within 1-2 mm of the vehicle’s undercarriage. Poorly fitted universal plates can leave gaps, exposing critical components to damage. Custom designs also reduce vibration and noise during operation, enhancing the vehicle’s overall ride quality. For vehicles with unique modifications, such as lift kits, skid plates with adjustable mounting points or extended coverage are necessary to ensure compatibility.
Installation ease
The method of installation is another key consideration. Bolt-on skid plates, featuring pre-drilled holes and included mounting hardware, are suited for DIY enthusiasts and typically require basic tools. These plates often come with step-by-step instructions to simplify the process. However, for vehicles requiring heavier or full-body skid plates, professional installation is recommended to ensure proper alignment and secure mounting. Some advanced models include modular designs that allow individual sections to be replaced or upgraded without removing the entire plate, saving time and labor costs.
Conclusion
Skid plates are a critical investment for protecting vehicles in off-road and rugged conditions, shielding vital components from costly damage caused by harsh terrains. With advancements in materials and design, modern skid plates offer tailored solutions that balance strength, weight, and compatibility with specific vehicle models. Selecting high-quality options that align with operational needs ensures enhanced durability and reliability, contributing to long-term cost efficiency and operational peace of mind.