With the introduction of an autonomous transport vehicle at its press plant, BMW Group Plant Regensburg is moving forward with digitalization and automation of its manufacturing processes, thereby taking a further step towards the digital and intelligently connected BMW iFACTORY.
The driverless platform truck, with its electric drive train, will handle the internal transport of press tools and steel blanks for the press lines autonomously, with a payload of up to 55 tonnes. Using sensor technology, the transport system navigates accurately and fully autonomously through the production facilities of the Regensburg press plant at a speed of four kilometers per hour. BMW says that the solution currently exists nowhere else in the world.
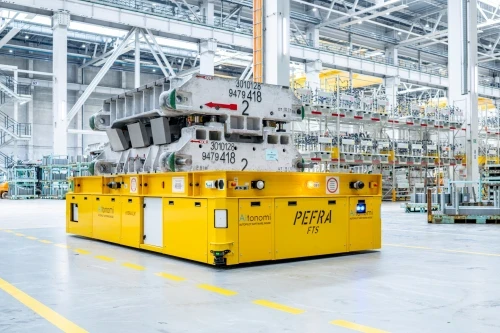
We see tremendous potential in the rollout of autonomous logistics solutions. The emission-free electric vehicle will allow us to make manufacturing processes at our press plant even more efficient and more flexible, as well as reducing transport journeys and lead times. This will not only boost productivity, but also save energy and improve occupational safety for our employees.
—Tobias Müller, press plant maintenance manager at BMW Group Plant Regensburg
The new driverless transport vehicle uses Innovative LiDAR (Light Detection And Ranging) technology from manufacturer Pefra. In conjunction with cameras and radar sensors, they monitor their surroundings, aiding in orientation, obstacle detection and distance measurement, delivering enhanced safety and efficiency in a complex environment – whether on busy roads or in automated industrial settings, such as at the BMW Group’s press plant in Regensburg. The 3D LiDAR process involves scanning the surroundings, using numerous individual optical distance measurements that are then combined to generate a 3D scatter plot of the environment captured by the LiDAR sensor.
The press plant at BMW Group Plant Regensburg processes about 1,100 tonnes of steel every workday, equivalent to a daily output of 131,000 pressed parts. The scope of production includes 113 different body components. In addition to structural and reinforcement parts, the press plant also forms large outer panel sections, such as side frames, door outer skins and bonnets, from sheet steel that can measure up to 4.5 meters in length.
The steel rolls processed can weigh up to 33 tonnes. The most powerful of the four press lines at the Regensburg press shop harnesses high-speed servo technology, making it one of the world’s fastest presses, with a press force of 9,000 tonnes—equivalent to the weight of the Eiffel Tower. The press achieves a rate of up to 23 strokes per minute. The body components manufactured at the press plant are then assembled into vehicle bodies at BMW Group Plant Regensburg’s nearby body shop.
Operations at the Regensburg press shop generate about 80,000 tonnes of offcuts each year, which are then recycled within a closed loop. The first step is for the offcuts to be processed by a recycling press, which forms them into steel cubes measuring 40 x 40 centimeters and weighing 220 kilograms each. These are then sent back to the steel supplier, where they are processed into what is known as secondary steel.
The use of secondary steel at the BMW Group’s Regensburg press plant generates two tonnes less CO2 per tonne of steel, compared to production of primary steel. This reduces the plant’s CO2 footprint by approximately 160,000 tonnes per year. To protect employees, residents and the environment from noise emissions and vibrations, the production and recycling facilities at the Regensburg press plant are equipped with sound insulation. Additionally, all production systems operate with minimal vibrations.
Source from Green Car Congress
Disclaimer: The information set forth above is provided by greencarcongress.com independently of Alibaba.com. Alibaba.com makes no representation and warranties as to the quality and reliability of the seller and products.