Table of Contents
1. Introduction
2. Understanding the main types of injection valves
3. Exploring recent market trends in injection valves
4. Key factors to consider when selecting injection valves
5. Leading models and standout features in 2025
6. Conclusion
Introduction
In industrial settings, injection valves play a key role in controlling the flow of molten substances accurately and efficiently. Their job is to maintain pressure, prevent any backflow, and streamline the injection process, all of which are essential for producing top-notch goods in manufacturing. Thanks to technological progress, today’s injection valves boast increased strength, suitability for various materials, and better performance even in challenging environments. Choosing the right injection valve can affect operational effectiveness by minimizing downtime and improving product quality, making it a pivotal choice for companies in 2025.
Understanding the main types of injection valves
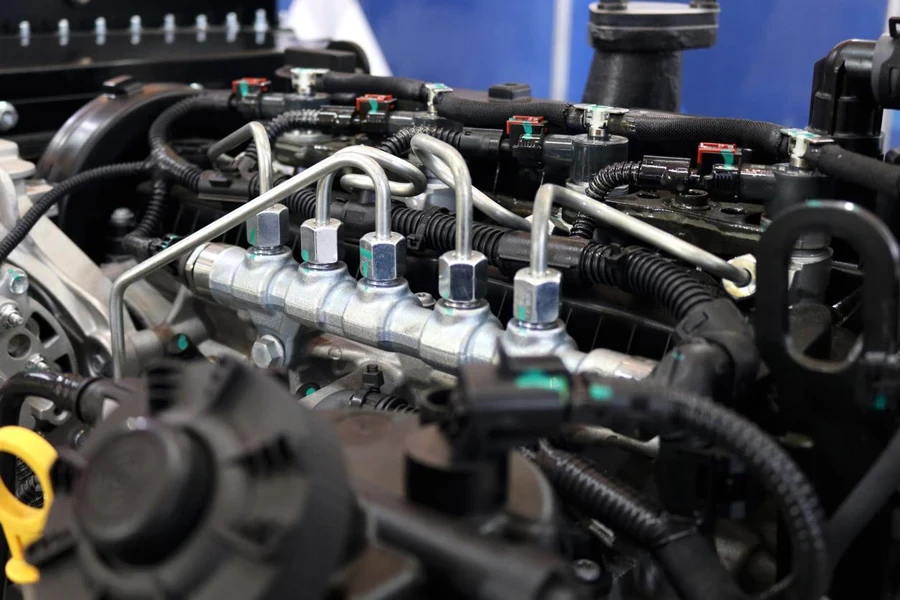
Overview of valve functionality
Injection valves are essential for controlling the flow of molten materials in industrial processes. They ensure unidirectional flow, maintain consistent pressure, and prevent backflow, which is critical for achieving high-quality results. These valves are particularly important in injection molding, where precise control is necessary to produce accurate and defect-free products. By regulating flow and pressure, injection valves support efficiency and improve the reliability of manufacturing operations.
Key types of injection valves
Several types of injection valves are available, each designed to meet specific industrial needs. Check ring valves are widely used because they allow material to flow in one direction and ensure consistent pressure. Their design makes them reliable for producing parts with uniform quality, making them a popular choice in many applications.
Ball check valves use a ball mechanism to control the flow of material, allowing it to move in one direction while preventing backflow. They are effective at sealing but may wear more quickly in heavy-use environments. Poppet valves are designed for precise control, opening to allow flow during the screw’s retraction and closing during injection to prevent backflow, making them ideal for applications requiring accuracy.
MDP valves are built for high-flow applications, especially those involving abrasive materials like glass-filled resins. With durable components such as carbide pins, these valves handle demanding conditions effectively and maintain high performance over time. Free-flow valves, on the other hand, are designed for operations requiring fast and unrestricted flow. They are particularly useful for high-speed processes and are also compatible with glass-filled materials.
Exploring recent market trends in injection valves

Market overview in 2024
In 2024, the global industrial valves market was valued at approximately USD 79.90 billion and is projected to reach USD 108.20 billion by 2029, growing at a CAGR of 6.25% during the forecast period, according to Mordor Intelligence. This growth underscores the escalating need for high-performance valves capable of meeting stringent operational requirements.
Key innovations shaping the market
The injection valve market is evolving due to technological advancements that bring hybrid valves capable of blending toughness with accurate control into play. These valves are crafted to withstand tough environments while ensuring precise flow rates, which are valuable assets for industries with stringent requirements. Moreover, electric actuators stand out as another breakthrough because they offer enhanced efficiency and control compared to their hydraulic counterparts. In addition, the rising trend of smart valves integrated with sensors for real-time monitoring and predictive maintenance reflects a growing preference towards automated processes and interconnectivity within manufacturing operations as part of Industry 4.0.
Regional market analysis
Different regions experience varying growth trends; the Asia Pacific region is at the forefront due to the industrialization in nations such as China and India, which has fueled the demand for various goods like automobiles and electronics. In North America, advancements in technology and automation play a significant role, with a focus on the U.S. ensuring top-notch production quality. Meanwhile, Europe focuses on sustainability, adopting valves that align with environmental regulations and energy-efficient practices. Established industries such as automotive and aerospace further contribute to the region’s demand for advanced injection valves.
Key Factors to Consider When Selecting Injection Valves
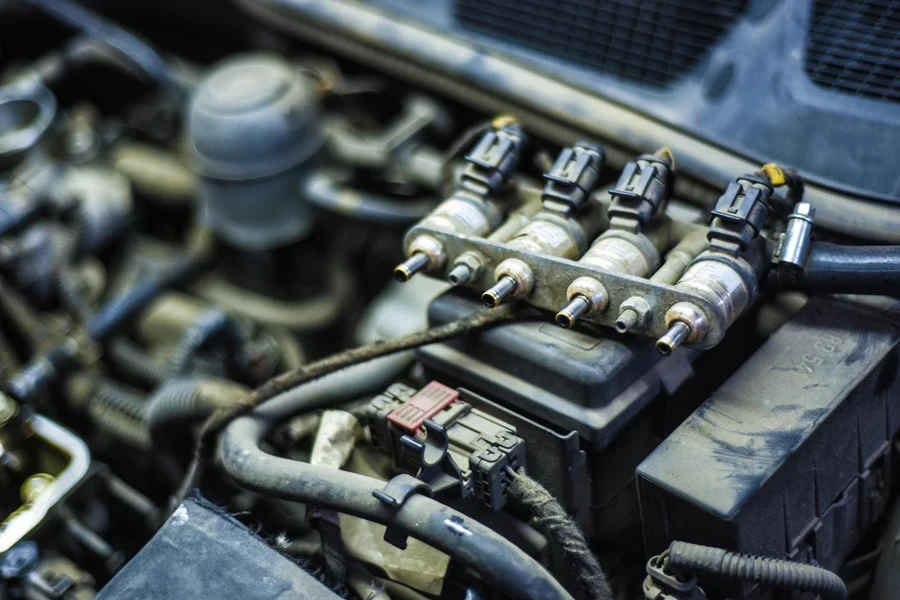
Material Compatibility
Choosing injection valves that are compatible with the materials used is essential to ensure durability and efficiency when dealing with corrosive or abrasive substances. Valves made from materials like carbide are highly effective in resisting the damage caused by substances such as glass-filled resins. Opting for valves crafted from materials that can withstand chemical corrosion and mechanical wear ensures efficient operation and minimizes the need for frequent replacements or repairs.
Pressure and Temperature Requirements
Matching injection valves to their designated pressure and temperature requirements is crucial as it ensures their effectiveness and safety measures are met accordingly. For example, valves employed in high-pressure injection molding tasks should exhibit durability to withstand demands and prevent malfunctions. Similarly, valves subjected to elevated temperatures must be crafted from materials that can endure strains while maintaining operational efficiency.
Maintenance and Durability
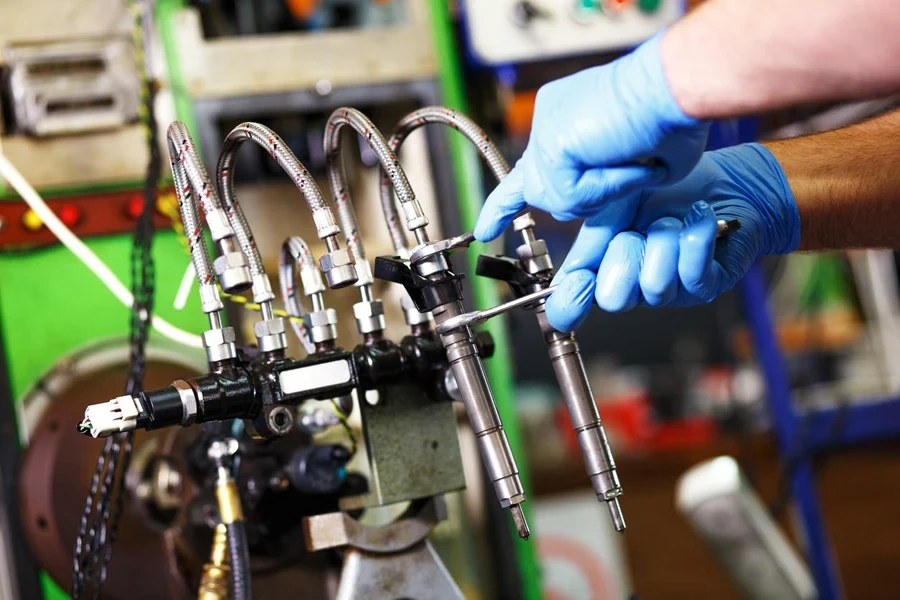
The ease of maintenance and inherent durability of injection valves significantly impact operational efficiency. The smooth maintenance and durability of injection valves play a role in improving efficiency. Valves equipped with quality components and easy-to-maintain designs can reduce downtime and prolong their lifespan. For instance, valves with modular structures enable easy replacement of worn-out parts, cutting down on maintenance time and effort. Choosing valves that combine durability with easy upkeep helps maintain productivity and cost efficiency.
Application-Specific Considerations
Different applications may require specific valve features to achieve desired outcomes. For high-precision molding processes, valves equipped with locking mechanisms can enhance accuracy by preventing unintended movements during operation. In contrast, applications that demand rapid production cycles may benefit from free-flow valves, which allow for faster material flow and reduced cycle times. Assessing the unique requirements of each application ensures that the selected valve type aligns with operational goals and performance expectations.
Leading Models and Standout Features in 2025
Overview of Top-Rated Products
In 2025, injection valves are advancing with designs prioritizing longevity, accuracy, and effectiveness. High-flow valves are gaining popularity for their capacity to manage materials like glass-filled resins while delivering consistent results. These valves are designed to reduce obstructions, making them ideal for fast-paced production operations that need seamless and uninterrupted material movement.
A significant shift in the industry involves incorporating sophisticated control mechanisms like actuators that regulate flow rates and pressure settings. It helps to boost accuracy and operational effectiveness, which is in line with the increasing focus on automation in manufacturing sectors. Injection valves designed with such technologies are particularly valued in industries requiring high levels of precision and reliability.
Key Features Driving Performance
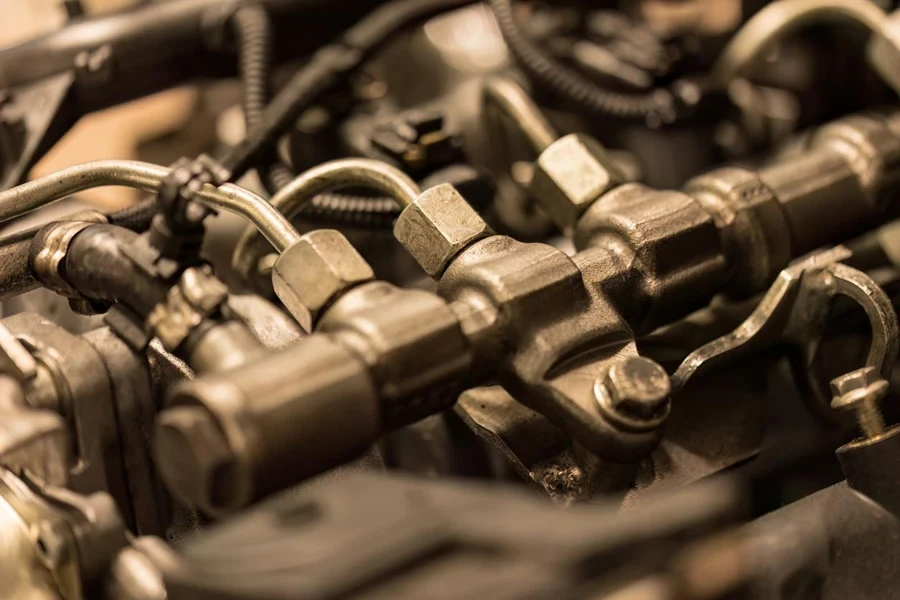
The latest injection valves are defined by features that enhance their functionality and adaptability across applications. Free-flow designs enable efficient material movement, reducing blockages and ensuring smooth operations in fast-paced production environments. These valves are ideal for applications where maintaining consistent flow rates is critical for product quality.
Precision control mechanisms are another essential feature, allowing operators to regulate flow and pressure accurately. Tasks involving intricate design and precision are crucial to maintaining the quality of the product.
Strength is also a consideration in the design process, as the chosen materials are known for their resistance to wear and harsh conditions such as corrosion and high-pressure settings. Such characteristics guarantee extended usability and decreased upkeep needs, resulting in cost-effective choices for challenging operations.
Conclusion
Selecting the right injection valves plays a role in guaranteeing the effectiveness of industrial processes. Companies can improve productivity and uphold uniform product standards by focusing on endurance, accuracy, and suitability. Keeping up to date on industry trends and technological progressions, such as flow configurations and precise control mechanisms, empowers decision-making that corresponds with changing production requirements. When choosing the valve type for processes today, whether it’s about ensuring material compatibility or seeking top-notch performance, making the right choice is crucial for long-lasting reliability and cost efficiency.