Table of Contents
1. Introduction
2. Decoding drive shafts: types and their applications
3. 2024 market insights and trends
4. Essential factors for selecting drive shafts
5. Top drive shaft models and their key features
6. Conclusion
Introduction
Selecting the right drive shafts is crucial for optimizing performance and efficiency in various applications, from automotive to industrial machinery. Drive shafts are integral components that transfer power from the engine to the wheels or other machinery parts, ensuring smooth and reliable operation. High-quality drive shafts can significantly enhance performance, reduce wear and tear, and extend the lifespan of equipment. By understanding the different types and their specific uses, businesses can make informed decisions that lead to better outcomes. This guide aims to provide a comprehensive overview of the key factors to consider when choosing drive shafts in 2024, helping professionals make smart, strategic purchases.
Decoding drive shafts: types and their applications
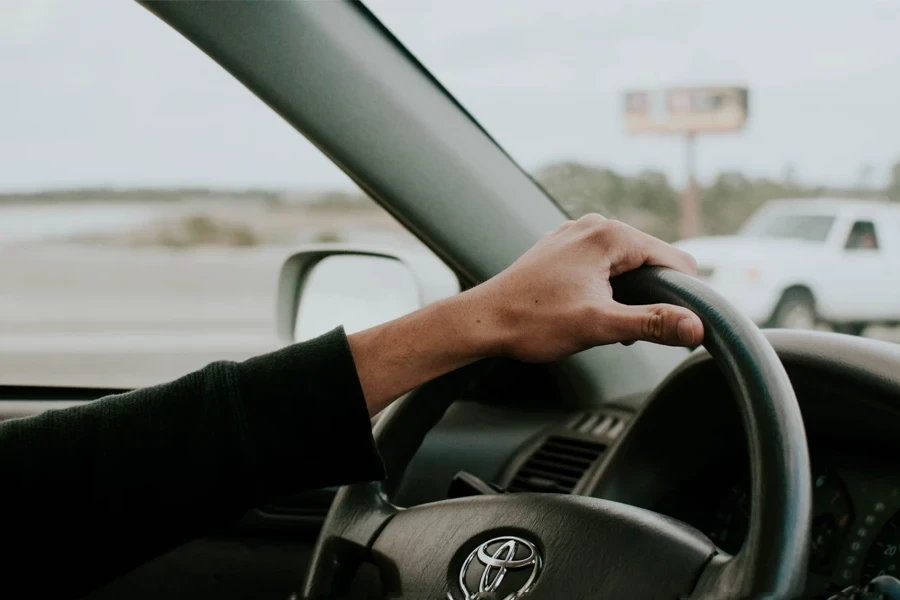
Exploring drive shaft types
Drive shafts are essential components that transfer power from an engine to the wheels or machinery, ensuring smooth and efficient operation. There are several types of drive shafts, each designed to meet specific needs and applications.
Solid drive shafts are known for their strength and durability. Made from a single piece of solid metal, they are ideal for high-torque applications where maximum strength is required. These shafts are commonly used in heavy-duty vehicles and industrial machinery due to their ability to withstand significant stress and torque.
Hollow drive shafts, on the other hand, offer a balance between strength and weight. By reducing the material used, these shafts are lighter, which can improve the efficiency and responsiveness of the machinery. Hollow shafts are often used in applications where weight reduction is crucial, such as in automotive racing and aerospace industries.
Flexible drive shafts are designed to accommodate misalignment between components. These shafts can bend and flex, making them suitable for applications where precise alignment is difficult to maintain. Flexible shafts are commonly used in tools and equipment that require a high degree of maneuverability and flexibility, such as in dental and surgical instruments.
Industry applications
Drive shafts play a pivotal role in various industries, each with unique requirements and benefits.
In the automotive industry, drive shafts are crucial for transferring power from the engine to the wheels. For front-wheel-drive vehicles, shorter drive shafts are used to connect the gearbox to the front wheels. In contrast, rear-wheel-drive vehicles often require longer shafts to transmit power from the engine located at the front to the rear wheels. This setup is particularly common in high-performance and heavy-duty vehicles, where robust and durable shafts are essential to handle the stress and torque generated by powerful engines.
In industrial machinery, drive shafts are integral to the operation of various equipment, from conveyor belts to heavy-duty pumps. Solid and hollow drive shafts are preferred in these applications for their strength and ability to handle high loads and stress. Industries such as manufacturing, mining, and construction rely heavily on the durability and reliability of drive shafts to ensure continuous and efficient operation.
The marine industry also benefits from the use of drive shafts, particularly in power-driven ships where shafts connect the engine to the propeller. Marine drive shafts must be highly resistant to corrosion and capable of withstanding the harsh conditions of saltwater environments. Stainless steel and composite materials are often used in these applications to enhance durability and longevity.
In the aerospace industry, drive shafts are used in various applications, including aircraft engines and landing gear systems. The focus here is on weight reduction without compromising strength and reliability. Hollow shafts and advanced composite materials are commonly used to achieve the desired performance characteristics.
2024 market insights and trends
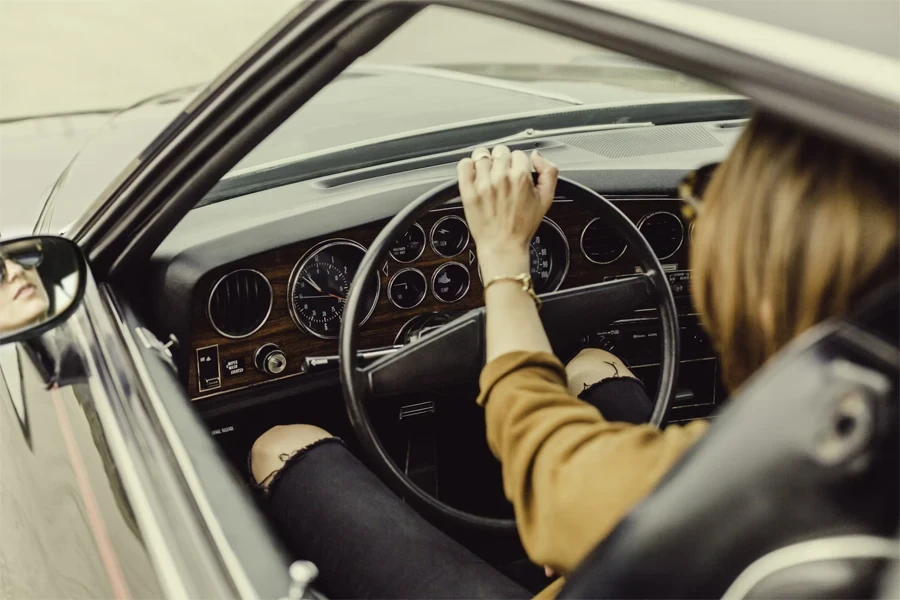
Current market landscape
The drive shaft market is experiencing robust growth, with significant advancements and increasing demand across various industries. In 2024, the global automotive drive shaft market size is expected to reach USD 74.26 billion, and it is projected to grow at a compound annual growth rate (CAGR) of 6.54%, reaching USD 101.94 billion by 2029. This growth is driven by the rising demand for high-performance vehicles and advancements in drive shaft technology, particularly in the automotive sector.
Cutting-edge technological advances
Technological innovations are at the forefront of the drive shaft market, enhancing performance, durability, and efficiency. One notable advancement is the use of advanced materials like carbon fiber composites, which offer superior strength-to-weight ratios compared to traditional steel and aluminum shafts. These materials reduce the overall weight of the drive shaft while maintaining or even increasing its strength, leading to improved fuel efficiency and performance in vehicles.
Manufacturing processes have also seen significant improvements. The filament winding process, for instance, is gaining popularity in the production of composite drive shafts. This method involves winding continuous fibers impregnated with resin around a rotating mandrel, creating a highly precise and strong drive shaft. This technology not only improves the mechanical properties of the drive shaft but also allows for more complex shapes and designs, catering to specific performance requirements.
Furthermore, innovations in design have led to the development of collapsible drive shafts, which enhance safety by absorbing impact energy during collisions. This feature is particularly beneficial in automotive applications, where safety standards are continually evolving. The integration of universal joints and slip joints has also improved the flexibility and adaptability of drive shafts, making them suitable for a wider range of applications.
The adoption of electric vehicles (EVs) is another trend influencing the drive shaft market. EVs require specialized drive shafts that can handle higher rotational speeds and torque levels compared to traditional internal combustion engine vehicles. This has led to the development of new drive shaft designs and materials specifically tailored for electric powertrains, further driving innovation in the industry.
Essential factors for selecting drive shafts
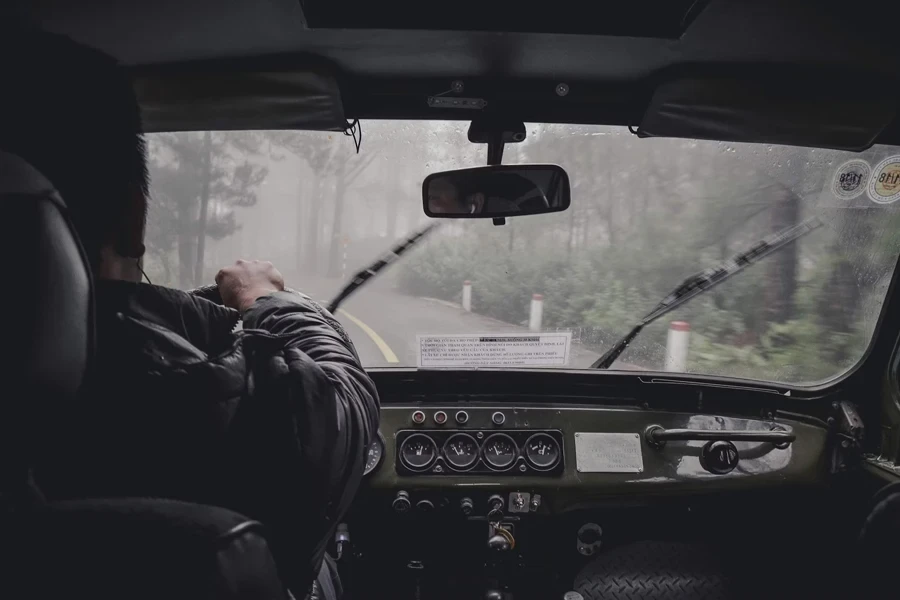
Performance essentials
When selecting drive shafts, three critical factors are weight, flex, and length. These elements significantly impact the overall performance and efficiency of the drive shaft in various applications.
Weight: The weight of a drive shaft influences its stability and rotational speed. Heavier shafts generally provide better stability and help in maintaining lower ball flight with reduced spin, essential for high-performance applications. Conversely, lighter shafts enhance swing speed and elevate ball flight, beneficial for applications where speed is prioritized. In automotive and industrial contexts, the choice between heavier and lighter shafts depends on the specific requirements of torque and speed.
Flex: Flexibility refers to how much the shaft bends during operation. Shafts with higher flex ratings (softer shafts) are suitable for applications requiring greater flexibility and smoother power transmission. These are ideal for lower swing speeds. Stiffer shafts, with lower flex ratings, are better for high-speed operations as they offer more control and reduce the risk of excessive spin. The right flex ensures that the drive shaft can handle the required torque without compromising performance.
Length: The length of the drive shaft affects its control and efficiency. Longer shafts can generate higher speeds but are more challenging to control, leading to less consistent performance. Shorter shafts provide better control and accuracy, making them suitable for precise applications. The length must be chosen based on the specific needs of the application, balancing speed and control for optimal performance.
The power of customization
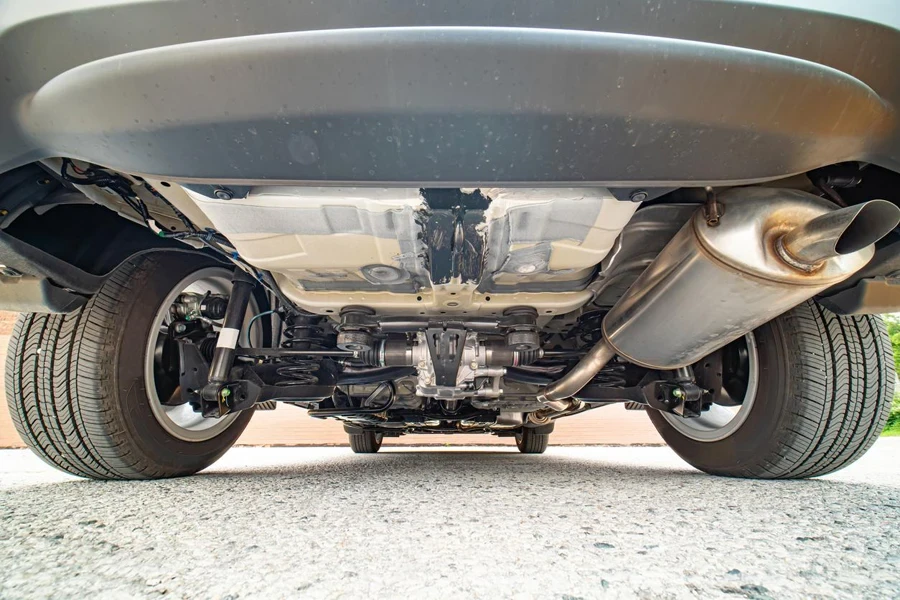
Customization plays a vital role in optimizing drive shaft performance for specific needs. Customized drive shafts can be tailored to meet the exact requirements of different applications, enhancing efficiency and durability.
Benefits of customization: Customizing drive shafts allows for adjustments in weight, flex, and length to suit specific operational conditions. This ensures that the drive shaft can handle the particular demands of the application, whether it involves high torque, precise control, or enhanced speed. Customization also includes selecting the appropriate materials, such as carbon fiber composites for reduced weight and increased strength, improving overall performance.
Professional fitting sessions: For optimal results, professional fitting sessions are highly recommended. These sessions involve detailed analysis and testing to determine the best specifications for the drive shaft. Experts use advanced tools and techniques to assess factors such as torque, speed, and operational environment, ensuring that the customized drive shaft delivers maximum efficiency and reliability. By leveraging professional fitting, businesses can achieve significant improvements in performance and longevity of their drive shafts.
Budgeting for quality
Investing in quality drive shafts is crucial for ensuring long-term performance and durability. Understanding the price ranges and the benefits of different tiers can help in making informed purchasing decisions.
Price ranges: Drive shafts are available at various price points, from standard models to premium options. Standard drive shafts typically cost less and offer basic performance suitable for general applications.
Cost-benefit analysis: When choosing between standard and premium models, it’s essential to conduct a cost-benefit analysis. Premium drive shafts can reduce maintenance costs and downtime, leading to higher overall efficiency and productivity. Businesses should consider their specific needs and budget constraints to determine the most cost-effective option.
Top drive shaft models and their key features
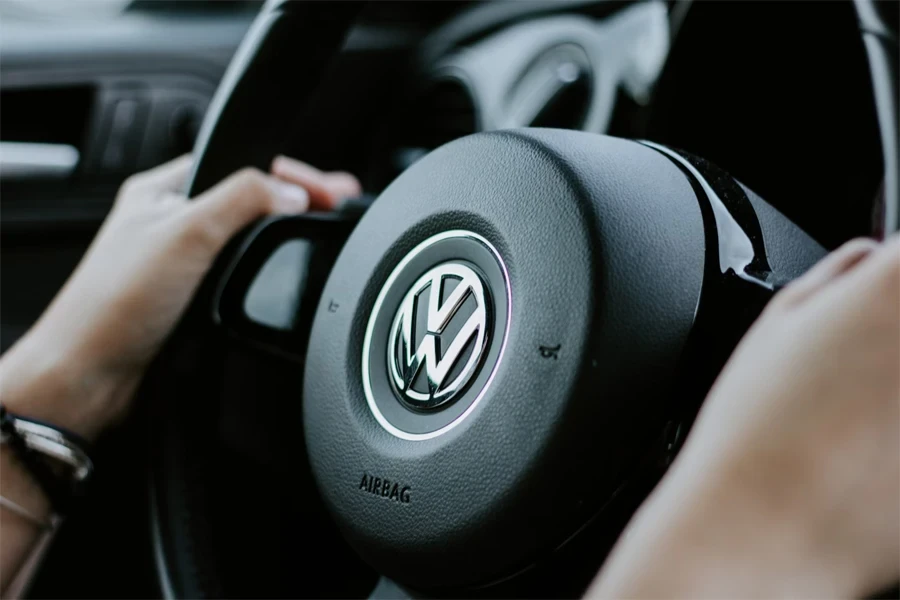
Leading models for 2024
In 2024, several drive shaft models stand out for their innovative design, superior materials, and enhanced performance capabilities. Among the top contenders are the Fujikura Ventus, Graphite Design Tour AD, and Mitsubishi Chemical Diamana, each offering unique features tailored to various needs.
Fujikura Ventus: The Fujikura Ventus series is renowned for its VeloCore technology, which enhances stability and reduces deflection on off-center hits. This technology is incorporated into a multi-material construction, making the Ventus shafts both strong and lightweight. The Ventus Black, in particular, is designed to maximize ball speed and tighten shot dispersion, making it an excellent choice for high-speed players seeking consistency and control. The Ventus lineup includes models with varying flexes and weights, catering to a broad range of swing types and preferences.
Graphite Design Tour AD: The Graphite Design Tour AD series is celebrated for its premium quality and performance. These shafts feature advanced carbon fiber materials that provide a smooth feel and exceptional stability. The Tour AD DI model, for instance, is known for its mid-launch and mid-spin characteristics, making it versatile for different playing conditions. The unique design of these shafts helps in optimizing energy transfer, resulting in greater distance and accuracy. Golfers appreciate the consistent performance and the enhanced control that these shafts offer.
Mitsubishi Chemical Diamana: Mitsubishi’s Diamana series is a staple in the world of high-performance shafts. The Diamana DF model combines two of Mitsubishi’s most successful tour-proven profiles—Blue Board and White Board—into a single shaft that offers lower launch and exceptional stability. The use of MR70, Mitsubishi’s strongest carbon fiber, ensures minimal shaft deformation, enhancing durability and performance. This shaft is ideal for players who demand precision and consistency in their game. The Diamana series is also known for its superior feel, making it a favorite among professional and amateur golfers alike.
Expert insights and customer reviews
Expert opinions and customer feedback play a crucial role in evaluating the performance and suitability of drive shafts. Insights from professional fitters and real-world users provide valuable information that helps in making informed decisions.
Expert insights: According to industry experts, the Fujikura Ventus shafts are highly regarded for their stability and performance enhancements. The VeloCore technology is particularly praised for its ability to maintain the shaft’s integrity during high-speed swings, resulting in improved accuracy and distance. Professionals also highlight the versatility of the Ventus series, which caters to various swing speeds and styles.
The Graphite Design Tour AD shafts are commended for their smooth feel and consistent performance. Experts note that the advanced carbon fiber construction provides excellent energy transfer, which is crucial for maximizing distance. The Tour AD DI model is often recommended for its balanced performance, offering both control and power.
Mitsubishi’s Diamana shafts receive accolades for their innovative use of materials and precise engineering. The Diamana DF model, with its low launch and high stability, is a preferred choice for players seeking to minimize spin and maximize control. The superior strength of the MR70 carbon fiber ensures that these shafts can withstand the rigors of high-level play, making them a reliable option for competitive golfers.
Customer reviews: Real user feedback aligns with expert opinions, with many golfers expressing satisfaction with the performance of these top models. Users of the Fujikura Ventus shafts often mention the noticeable improvement in shot dispersion and overall consistency. The feel and stability provided by the Ventus series are frequently highlighted in customer reviews.
Golfers using the Graphite Design Tour AD shafts appreciate the smooth feel and the enhanced control these shafts offer. Many users report significant gains in distance and accuracy, attributing these improvements to the advanced materials and design of the Tour AD series.
The Mitsubishi Diamana shafts are praised for their exceptional stability and durability. Customers who use the Diamana DF model often comment on the increased confidence they experience due to the shaft’s consistent performance and precise control. The superior feel and reduced spin are also common points of appreciation among users.
Comparative analysis: When comparing these leading models, the Fujikura Ventus stands out for its stability and versatility, making it suitable for a wide range of players. The Graphite Design Tour AD excels in providing a smooth feel and balanced performance, ideal for golfers looking for a combination of control and power. The Mitsubishi Diamana is renowned for its precise engineering and superior materials, offering exceptional stability and low spin, perfect for high-level competitive play.

Conclusion
Selecting the right drive shafts is crucial for optimizing performance and ensuring customer satisfaction. Understanding the key factors such as weight, flex, and length, alongside the benefits of customization and quality investment, can significantly enhance operational efficiency. Leading models like Fujikura Ventus, Graphite Design Tour AD, and Mitsubishi Chemical Diamana offer advanced features tailored for various needs, supported by positive expert insights and user reviews. Making informed choices based on detailed evaluations and professional fitting sessions can lead to superior performance, reliability, and overall satisfaction in any application.