Un regard sur les tendances actuelles et les enjeux de la chaîne d'approvisionnement du secteur automobile
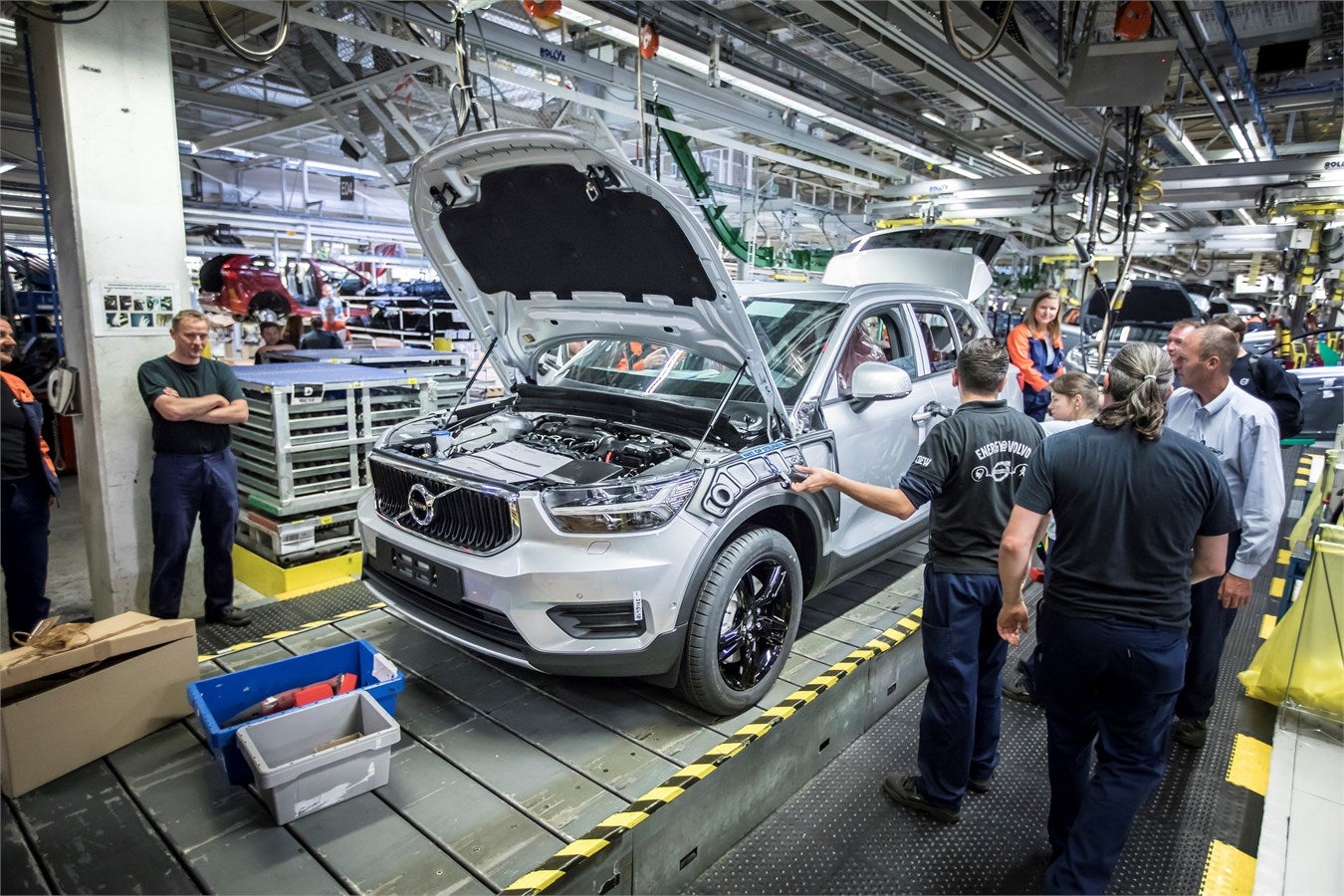
Un véhicule automobile atypique peut contenir entre 15,000 25,000 et XNUMX XNUMX composants, selon la manière dont ils sont mesurés et l'ingénierie de conception de ses principaux systèmes. Cela représente beaucoup de matière à rassembler et à assurer l'intégrité du produit final. En effet, ce n’est pas une mince affaire de rassembler toutes ces pièces dans le bon ordre. Chaque voiture existante est un hommage à la planification des processus, à l'organisation, à l'ingénierie de production et à la logistique de fabrication. Autrefois, les constructeurs automobiles étaient fortement intégrés verticalement, mais cette approche a cédé la place à des fournisseurs de pièces détachées (quelqu'un se souvient d'où vient Visteon et du réseau enchevêtré d'entreprises qui composait le groupe de composants automobiles de General Motors ?) et de fournisseurs de pièces spécialisés qui pouvaient se concentrer sur développement de produits et fonctionner plus efficacement à plus grande échelle pour plusieurs clients.
Les grands intégrateurs de systèmes de niveau 1 approvisionnent directement les constructeurs automobiles, souvent à partir de parcs de fournisseurs idéalement situés à proximité des installations d'assemblage et de fabrication des véhicules, mais il existe plusieurs niveaux de fournisseurs plus petits en dessous du niveau supérieur – chacun jouant un rôle essentiel sur le long chemin depuis le brut. matériaux au produit fini.
L'approvisionnement international en composants est devenu un mode de fonctionnement standard de l'industrie depuis de nombreuses décennies, les équipementiers et les grands fournisseurs cherchant à magasiner sur le marché mondial pour trouver des pièces et des intrants matériels répondant aux seuils de qualité nécessaires au moindre coût. Les distances (et les coûts) de transport et les modalités d'entreposage font également partie du tableau, mais l'efficacité accrue et les progrès technologiques dans le transport international de marchandises ont soutenu une croissance phénoménale des expéditions internationales de pièces détachées.
La croissance de l’industrie automobile chinoise au cours des deux dernières décennies a également été un facteur important dans l’approvisionnement mondial en composants automobiles, en particulier ce qu’on pourrait appeler des pièces universelles ou banalisées qui se vendent principalement au prix de revient. Les fournisseurs chinois ont bénéficié de gros contrats locaux qui stimulent les économies d’échelle, ainsi que de subventions cachées provenant de structures de propriété complexes impliquant des sociétés mères OEM, des entreprises d’État et des actions diversifiées. Au début des années 2000, les constructeurs automobiles américains, en particulier, ont décidé de s’approvisionner davantage en pièces détachées à bas prix en Asie, mettant ainsi à mal certaines entreprises établies de longue date dans la base de fournisseurs américains.
Partout dans le monde, les flux commerciaux internationaux de produits automobiles – tant pour les véhicules finis que pour leurs composants – sont désormais énormes. Estimations compilées par GlobalData montrent que l'Allemagne est de loin le leader mondial en termes d'expéditions sortantes de produits de l'industrie automobile. Ces exportations se reflètent dans les importations et dans un réseau enchevêtré de biens intermédiaires qui sont utilisés comme intrants dans des systèmes de composants raffinés et conçus à différentes étapes du processus de fabrication et qui peuvent être expédiés plusieurs fois au-delà des frontières internationales.
Une autre caractéristique structurelle importante des chaînes d'approvisionnement de l'industrie automobile est l'importance d'une philosophie de gestion de la chaîne d'approvisionnement qui minimise les coûts de stocks et améliore l'efficacité des processus et les boucles de communication de rétroaction pour des normes de qualité améliorées. Connue sous le nom de « fabrication au plus juste », elle a commencé avec Toyota et son essence est résumée par le terme « juste à temps » pour décrire les méthodes et principes d'approvisionnement lean. L’essor des technologies numériques et connectées qui rassemblent toutes les parties du processus de fabrication et de vente au détail a renforcé ces méthodes de travail au cours de la dernière décennie.
Dans le passé, les catastrophes naturelles et leurs impacts localisés ont eu un impact sur les constructeurs automobiles et ont illustré la fragilité des chaînes d’approvisionnement du secteur automobile. Après le tremblement de terre et le tsunami de 2011 au Japon, il y a eu plusieurs exemples notables de perturbations. Un constructeur automobile mondial haut de gamme a rencontré des problèmes d’approvisionnement en pigments de peinture rouge provenant d’une seule source au Japon. Les inondations en Thaïlande plus tard cette année-là ont provoqué une pénurie d'écrans LCD pour l'affichage d'informations sur les véhicules. Les équipementiers et les concessionnaires ont dû s’adapter en conséquence aux pénuries. La guerre en Ukraine illustre à quel point des événements géopolitiques inattendus peuvent également perturber les chaînes d’approvisionnement.
Le défi des semi-conducteurs
Toutes les entreprises ont été touchées directement par la crise de santé publique de 2020 et indirectement par de nombreux autres effets sur les chaînes d’approvisionnement mondiales. Par ailleurs, la reprise des ventes mondiales en 2021 a été fortement perturbée par une conséquence imprévue de la crise du Covid un an plus tôt. Alors que les constructeurs automobiles ont fermé leurs usines sur ordre du gouvernement et réduit considérablement leurs commandes de pièces détachées en 2020, les fabricants de semi-conducteurs ont trouvé des opportunités alternatives dans des domaines tels que l’électronique grand public.
Lorsque les usines automobiles en reprise ont augmenté leurs commandes de puces au premier trimestre 2021, un problème de resserrement de l’approvisionnement est rapidement devenu évident.
Les pénuries de semi-conducteurs n’allaient pas non plus être facilement surmontées en raison des longs délais de mise en œuvre en amont pour ajouter des capacités de fonderie de puces. L'absence d'une pièce critique pour la sécurité ou jugée nécessaire pour le produit fini signifie que certaines gammes de modèles ont été plus gravement touchées que d'autres. Les constructeurs automobiles pouvaient dans certains cas modifier la composition du marché, mais un vieil adage redevenait réalité : les chaînes d’approvisionnement ne sont aussi bonnes/robustes que leur point le plus faible.
Dans l’ensemble du secteur, les méthodes et processus d’approvisionnement sont soumis à un examen minutieux comme jamais auparavant.
Il convient également de noter qu'un élément structurel est à l'œuvre, ce qui signifie que certaines pressions d'approvisionnement en semi-conducteurs resteront probablement un risque à l'avenir : le contenu électronique avancé des véhicules augmente en raison de l'équipement toujours croissant de fonctionnalités technologiques plus sophistiquées. Cela pousse certaines entreprises à conclure des alliances stratégiques avec des fabricants de puces. Non seulement cela peut contribuer à garantir les approvisionnements futurs en microprocesseurs critiques, mais cela peut également faciliter des relations collaboratives bénéfiques en matière de développement de produits futurs dans ce qui devient évident comme un domaine de composants stratégiquement précieux.
D’autres pressions sur les chaînes d’approvisionnement proviennent d’autres sources, telles que des pénuries imprévues de main-d’œuvre et des prix beaucoup plus élevés des expéditions internationales de conteneurs en raison de la flambée des prix de l’énergie.
Le débat entre double et multi-sourcing
La fragilité des chaînes d'approvisionnement automobile s'accompagne de la prévalence de plusieurs niveaux, de flux d'approvisionnement internationaux et d'une tendance à un approvisionnement unique pour maximiser les économies d'échelle dans les programmes automobiles mondiaux. Dans de nombreux cas, cette structure traditionnelle est également ancrée dans une culture de partenaires privilégiés à travers les niveaux d’approvisionnement. Les avantages peuvent également inclure des systèmes partagés et des coûts logistiques, les coûts étant également répartis sur les volumes sur d'autres modèles et systèmes.
La technologie a également joué un rôle en encourageant l’approvisionnement unique, car les entreprises – y compris celles des niveaux 3 et 4 – ont généralement pu centraliser l’expertise et les investissements dans une seule installation dédiée à la fabrication en grand volume. Les problèmes surviennent quand quelque chose ne va pas et fait échouer les plans (l'incendie dans une usine de microprocesseurs Renesas l'année dernière, par exemple).
L'électronique et les capteurs sont des exemples de composants critiques pour les sous-ensembles qui peuvent avoir d'importantes implications en aval dans la fabrication automobile en cas de perturbation en amont. Trouver des fournisseurs alternatifs disposant de capacités inutilisées dans des délais très courts constitue un défi de taille.
Conserver certaines réserves de pièces en stock a un coût et va à l’encontre des principes directeurs du Lean Manufacturing. La décision peut bien entendu être prise d’absorber ou d’amortir les coûts de perturbations aberrants au fur et à mesure qu’ils surviennent – cela dépend en fin de compte de la quantification de l’évaluation des risques.
L’expérience de ces dernières années montre au moins que les entreprises se posent de plus en plus la question de savoir si le mono-sourcing est aussi souhaitable qu’il l’était autrefois. Un monde confronté à des risques et à des incertitudes plus élevés exige peut-être une nouvelle approche. La duplication au sein de la chaîne d’approvisionnement, même si elle implique de se rapprocher du partage avec un concurrent, peut offrir une meilleure solution – du moins pour certains composants – que l’approvisionnement unique. Une plus grande sécurité des produits serait l’avantage d’un double approvisionnement. Comme toujours, c'est une question de coût global.
Électrification et nouveaux modèles de chaîne d’approvisionnement
L’électrification pose de nouveaux défis aux futures chaînes d’approvisionnement du secteur automobile. Les équipementiers sont confrontés à des incertitudes considérables concernant la fourniture de nouveaux composants clés – notamment les batteries du groupe motopropulseur – qu’ils tentent de résoudre. Des questions stratégiques se posent également quant au degré d'intégration verticale souhaitable pour atténuer les risques futurs et exercer un contrôle sur les aspects commerciaux des accords d'approvisionnement. Des joint-ventures avec des spécialistes des batteries ont été créées. D’autres composants clés des véhicules électriques – tels que les moteurs, les pièces du système d’entraînement, les onduleurs haute tension – feront également l’objet d’investissements croissants parallèlement aux considérations de chaîne d’approvisionnement.
Des stratégies d’électrification ambitieuses verront la demande de cellules de batterie lithium-ion monter en flèche. Les producteurs de batteries du monde entier s'engagent dans des stratégies d'expansion de plusieurs milliards de dollars, en ouvrant de nouvelles « gigafactories » pour fournir des cellules aux constructeurs automobiles.
Un exemple notable d’une étroite collaboration OEM-Tier 1 dans ce domaine est fourni par la signature d’un protocole d’accord entre Volkswagen et Bosch. Les deux sociétés prévoient de fournir des systèmes intégrés de production de batteries, une montée en puissance sur site et un support de maintenance pour les fabricants de cellules et de systèmes de batteries. Ils affirment viser le leadership en termes de coûts et de technologie dans la technologie des batteries à l'échelle industrielle et la production en volume de « batteries durables et de pointe ».
Rien qu'en Europe, le groupe Volkswagen prévoit de construire six usines de cellules d'ici 2030 et d'autres fabricants prennent des mesures similaires pour garantir l'approvisionnement futur en cellules et batteries. La région devrait voir une capacité annuelle totale de batteries d’environ 700 gigawattheures d’ici 2030.
En amont, Toyota a formé une JV avec Panasonic (Prime Planet Energy & Solutions – PPES) qui a signé un accord avec le géant minier BHP pour la fourniture future de sulfate de nickel, base du nickel présent dans la cathode de la plupart des batteries lithium-ion. cellules de batterie. Tesla a également signé un accord similaire avec BHP, illustrant que les matières premières sont également très présentes dans la sécurité d'approvisionnement future.
Ces accords soulignent la nécessité pour les acteurs de l'automobile d'examiner plus en amont la chaîne d'approvisionnement des batteries, afin de s'assurer qu'ils ont accès à suffisamment de matières premières pour fournir l'énorme croissance de capacité nécessaire dans le secteur des batteries lithium-ion pour la nouvelle vague de véhicules électriques à batterie lancée dans le années à venir. Le recyclage est également un élément clé dans de nombreuses transactions conclues.
Blockchain pour la visibilité de la chaîne d'approvisionnement
De plus en plus, les constructeurs automobiles utilisent la technologie blockchain pour gagner en transparence sur les problèmes de chaîne d'approvisionnement tels que les émissions de CO2 et la source de cobalt pour les batteries (ce qui peut entraîner des questions éthiques liées à l'extraction de minéraux précieux).
Le concept original de la blockchain, comme son nom l'indique, est une chaîne de blocs ou d'enregistrements horodatés (bloc = informations numériques ; chaîne = base de données publique/communautaire). Les blocs stockent des informations sur les transactions. Lorsqu'un bloc stocke de nouvelles données – une transaction – il est ajouté à la blockchain et, une fois vérifié par un réseau d'ordinateurs peer-to-peer, tout le monde peut le voir (ou il peut être soumis à l'autorisation d'un réseau privé tel que la chaîne d'approvisionnement d'un OEM – le « grand livre distribué »).
Cependant, toutes les parties n’ont accès qu’aux informations qu’elles sont autorisées à consulter. Chaque ordinateur du réseau blockchain possède sa propre copie de la blockchain. En principe cependant, l’idée est de créer un système hautement transparent avec des coûts de transaction nuls entre les deux parties créant un bloc.
Nous pouvons nous attendre à voir davantage de constructeurs automobiles adopter des processus de blockchain – en particulier du type registre distribué (c'est-à-dire réseau privé) – comme moyen d'atténuer le risque de « rupture » de la chaîne d'approvisionnement et de comprendre les forces et les faiblesses tout au long de la chaîne, mais aussi comme moyen moyen de démontrer les exigences croissantes en matière de conformité dans des domaines réglementaires tels que la durabilité.
Les leçons de Toyota
Toyota est généralement considéré comme l'un des acteurs les plus performants de l'industrie automobile en matière de gestion de la chaîne d'approvisionnement. En plus d'être à l'origine des méthodes de production Lean qui sont ensuite devenues les meilleures pratiques largement répandues adoptées par la plupart des équipementiers et des principaux fournisseurs, l'entreprise a également affiné ses systèmes et processus en fonction de l'évolution des circonstances concernant les mesures d'atténuation des risques. De plus, elle a parfois travaillé en très étroite collaboration avec ses fournisseurs et dans l'intérêt d'objectifs sectoriels plus larges face aux urgences.
Après le tremblement de terre et le tsunami de Kyoto en 2011, Toyota a travaillé aux côtés de fournisseurs japonais pour produire une base de données complète d'informations sur la chaîne d'approvisionnement afin de soutenir le secteur manufacturier japonais. Toyota a également introduit une stratégie d'approvisionnement multiple pour les pièces clés, ce qui impliquerait d'organiser l'approvisionnement à partir de trois sources différentes – mais avec le fournisseur principal s'engageant à réaliser près des deux tiers de la commande pour garantir des économies d'échelle. La multiplicité des fournisseurs compromet effectivement les économies d’échelle, mais cela signifie également que des alternatives sont en place si nécessaire.
Toyota dispose également d'un système bien développé pour surveiller son vaste réseau de fournisseurs et d'un système d'alerte précoce en cas de pénurie. En effet, certaines entreprises se tournent vers l’IA pour évaluer l’évolution de leurs chaînes d’approvisionnement – même si cela nécessite en premier lieu de disposer d’une base de données fiable, étendue et détaillée.
Une autre option pour les entreprises consiste à maintenir des stocks d’urgence ou tampons de pièces clés, en particulier celles qui peuvent entraîner l’arrêt d’une chaîne de production. Encore une fois, cela implique des coûts supplémentaires de stockage ou d'entreposage, mais il s'agit de déterminer quel niveau de coût ou de « prime d'assurance » vaut la peine d'être payé. De plus, ce ne sera pas une solution permanente. Toyota a peut-être stocké certains semi-conducteurs, mais la gravité de la pénurie mondiale de puces l’a finalement contraint à réduire sa production. L’apprentissage le plus important de Toyota est peut-être la nécessité d’une révision constante et d’une capacité d’adaptation aux circonstances changeantes et aux incertitudes.
Source à partir de Juste une voiture
Avis de non-responsabilité : les informations présentées ci-dessus sont fournies par just-auto.com indépendamment d'Alibaba.com. Alibaba.com ne fait aucune représentation ni garantie quant à la qualité et à la fiabilité du vendeur et des produits.