Southeast Asia is rapidly making its mark as a prominent manufacturing hub, enticing foreign high-tech companies to diversify their production activities away from China and establish more resilient supply chains to guard against unexpected disruptions.
This shift in the global manufacturing landscape presents a golden opportunity for manufacturing machinery wholesalers to tap into the growing demand for advanced industrial equipment in the region.
By uncovering crucial market drivers and competitive opportunities, as well as delving into the core industries and associated machinery across six countries, this comprehensive, research-driven analysis will equip businesses with the necessary insights to confidently venture into Southeast Asia’s industrial machinery market.
Table of Contents
Industrial machinery in Southeast Asia: a market snapshot
Industrial machinery across six Southeast Asian nations
Competitive landscape of the industrial machinery market in SEA
Unlock Southeast Asia’s industrial revolution
Industrial machinery in Southeast Asia: a market snapshot
The Southeast Asian industrial machinery market is set to flourish between 2023 and 2032, fueled by a vibrant labor workforce of approximately 81 million people and the allure of lower labor wages.
This advantageous business environment has enticed industrial companies to establish their manufacturing processes in the region. As a result, we can expect the manufacturing output in the region to increase significantly, with projections indicating a potential revenue generation of up to US$ 600 billion by 2023.
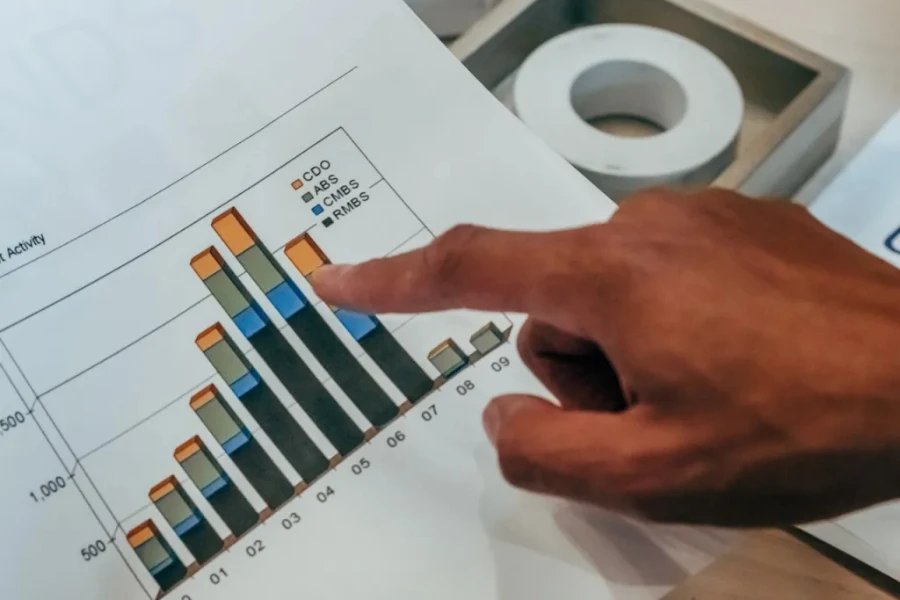
Boosted by the digital transformation of key industries like automobiles, electronics, and food packaging, this remarkably growing manufacturing sector will continue to drive unprecedented demand for automated industrial machinery and equipment.
Southeast Asian governments are lending a hand too, with policies and incentives that draw foreign investments and boost local manufacturing. These initiatives are enticing multinational corporations to set up facilities in the region, driving up the need for advanced machinery to ensure efficient, cost-effective production.
Having established that Southeast Asia possesses a robust industrial base for heavy equipment and machinery, it is time now to delve into the factors propelling this market and the possible obstacles it might face in the future.
Market drivers and restraints
Market drivers | Market restraints |
With ASEAN manufacturing output anticipated to reach a remarkable US$ 600 billion by 2030, the demand for advanced equipment and innovative machinery is on the rise. | Inadequate infrastructure networks in the region constrain the seamless adoption of advanced industrial machinery. The lack of a reliable power supply, for example, hampers the adoption of industry 4.0 technologies. |
Southeast Asian governments actively foster a conducive manufacturing climate via industrialization policies, encouraging technology adoption and infrastructure growth. | Small and mid-sized companies are unwilling to invest in automated industrial machinery due to concerns about the associated costs, the complexity of implementation, and the potential displacement of human labor. |
With an average hourly manufacturing labor cost of just US$ 3.6, the Southeast Asian region presents an attractive alternative hub to companies seeking cost-effective manufacturing solutions. | The scarcity of skilled machinery maintenance workers hampers the efficient operation and upkeep of sophisticated heavy equipment and machine tools. This workforce deficiency leads to decreased productivity and increased downtime. |
In just 2021, the ASEAN region saw an unprecedented US$ 174 billion in foreign direct investments, with multinational companies tapping into local manufacturing capabilities. | Bureaucratic customs procedures pose a significant hindrance to the import of industrial machinery. The clearance process might take approximately 96 hours to complete. |
Market opportunities and threats
Market opportunities | Market threats |
Southeast Asia is shifting focus from low-tech items to high-tech products. This change is evidenced by the fact that the region now accounts for more than 80% of global hard drive production. | As new technologies and automation solutions are developed and implemented, industrial equipment and machinery can quickly become obsolete. This leads to increased costs associated with upgrading or replacing machinery. |
Driven by a strong desire to optimize their production capabilities, factories are increasingly embracing industry 4.0 technologies. This adoption encompasses advanced assembly-line robotics, AI-driven machine tools, and cutting-edge manufacturing solutions. | Insufficient technical education in the region has led to a shortage of skilled laborers, who can operate modernized equipment. This skills gap deters local industries from investing in advanced heavy equipment. |
As additive manufacturing gains traction in Southeast Asia, the need for rapid creation of customized parts and prototypes will grow, driving up the demand for 3D printing machines that transform digital designs into tangible objects. | The manufacturing sector heavily relies on importing intermediate components. Such dependence on external supply chains renders the region vulnerable to disruptions caused by geopolitical tensions, trade restrictions, or global crisis events. |
The enactment of the Regional Comprehensive Economic Partnership (RCEP) will enhance competitiveness in the manufacturing sector by diminishing trade barriers like tariffs and quotas, as well as by fostering transparency and predictability in operational costs. | The region’s industrial framework is heavily influenced by political changes, which can result in abrupt shifts in industrialization policies and trade agreements. The unpredictable policy alterations can discourage companies from expanding their manufacturing operations. |
Industrial machinery across six Southeast Asian nations
Merely catching a quick glimpse at the overall growth of industrial machinery won’t suffice. This comprehensive section offers an immersive journey for businesses, taking them through the vibrant Southeast Asian market and exploring the manufacturing sectors of six standout countries in depth.
Throughout this section, business buyers will acquire a profound understanding of the distinct characteristics of each country’s industrial landscape. The focus will be on the integral industries, offering invaluable perspectives into the specific industrial machinery and heavy equipment experiencing significant demand.
Vietnam
Located at the eastern end of the Indochinese peninsula, Vietnam borders Cambodia, China, and Laos. With a population of 97 million people, it is one of Southeast Asia’s most densely populated countries.
The industrial machinery market in Vietnam is witnessing an extraordinary boom, with the manufacturing sector’s added-value contribution exceeding US$ 114 million. This represents nearly 25% of the national GDP—more than any other single sector did in 2021.
In addition to its proximity to many other countries in the Asia-Pacific region, Vietnam has become a hub for high-tech electronics and textiles manufacturing due to lower labor costs. With wages as low as US$ 133 per month, manufacturing businesses are drawn to Vietnam for cost-effective production.
Electronics
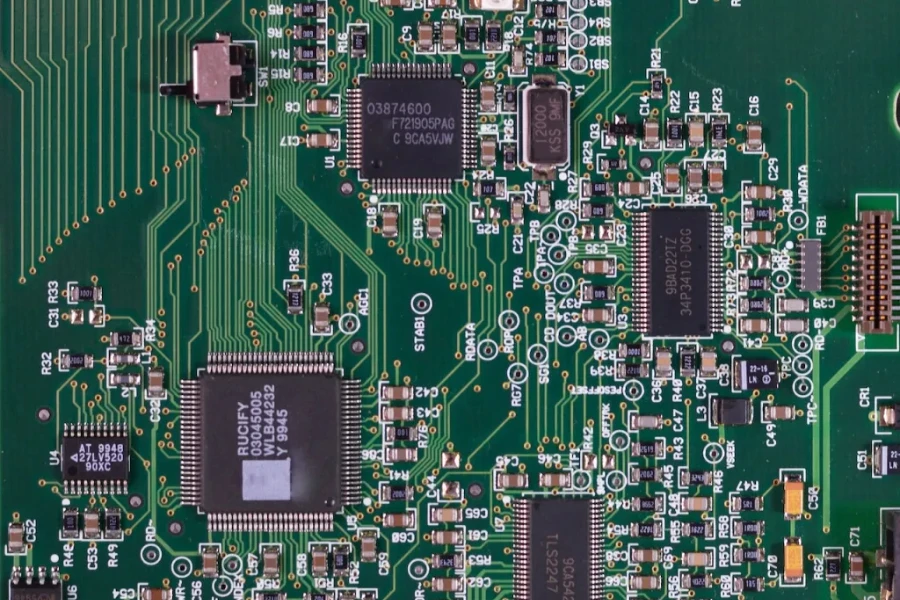
In 2021, consumer electronics accounted for over US$ 8.47 billion of Vietnam’s industrial revenues. Much of this growth was driven by investments from foreign high-tech companies such as Samsung, LG, Canon, and Nokia. As a matter of fact, Samsung alone accounted for roughly 20% of the total Vietnamese exports of electronics.
The country has a massive network of more than 250 industrial zones, particularly in the north where some provinces have expanded into manufacturing hubs for electronics products from television sets and smartphones to printers and household appliances.
As the electronics industry continues to grow, the demand for precision machining tools, such as CNC milling machines, is set to increase. These vital pieces of equipment play a crucial role in crafting intricate and precise components for electronic devices. For example, they can expertly carve out essential features on printed circuit boards and fabricate custom heat sinks.
➕ Read more: What is CNC?
Another indispensable category of equipment in the electronics manufacturing process is soldering gear, especially hot air guns. These valuable industrial tools are essential during the assembly and repair of electronic devices, as they enable the accurate application of heat to solder joints without causing harm to nearby components.
Textiles and apparel
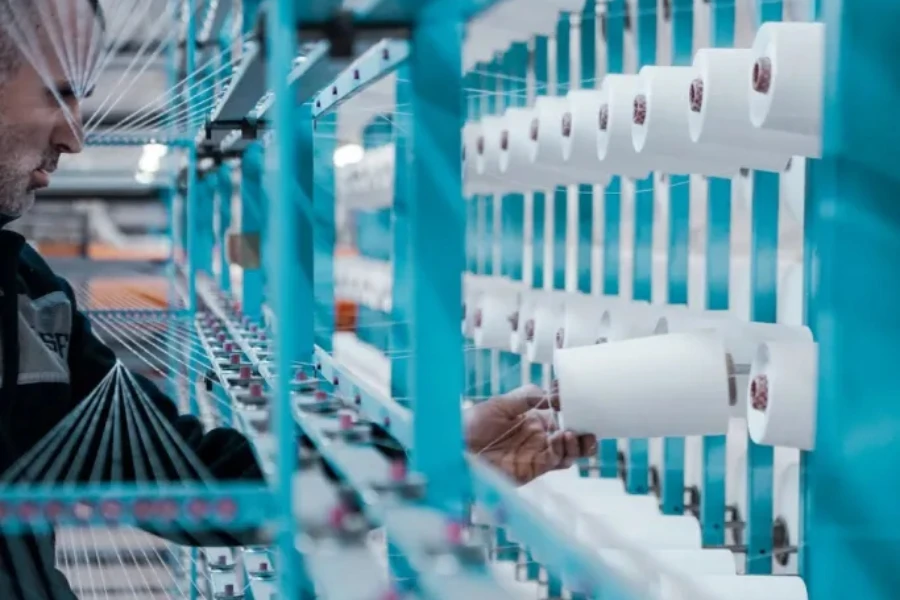
In addition to consumer electronics, the textile industry is a key component of Vietnam’s economy. In fact, the Pearl of the Orient is one of the biggest exporters globally of garment and textile products. Moreover, Vietnamese domestic spending on clothing and footwear has been growing steadily over the past few years thanks to improved living standards.
With this growing demand for fashionable clothing, businesses will be on the lookout for cutting-edge industrial machinery to make their fabric manufacturing and wet processing more efficient and streamlined.
As a result, wrapping machines will continue to be an essential and appreciated solution in the textile industry. They neatly prepare yarn for weaving or knitting by winding it onto beams or cones in a tidy and organized manner. Thanks to these efficient machines, manufacturers can maintain consistent yarn quality while reducing material waste.
➕ Read more: How to select wrapping machines in 2023
Dyeing machines are yet another invaluable tool for clothing manufacturers. As the mainstays of the wet processing stage, these machines infuse fabrics with brilliant colors and eye-catching patterns that truly make them stand out in the fashion world.
With a variety of techniques such as immersion dyeing, spray dyeing, and pad dyeing at their disposal, these machines ensure the perfect color saturation and consistency every time.
➕ Read more: Discover the essential industrial equipment powering Vietnam’s manufacturing sector
Malaysia
Blessed with an abundance of natural resources and a remarkably young population, Malaysia stands as a proud exporter of industrial machinery on the world stage. Yet, the nation still grapples with unlocking its full potential as an industrial titan.
The dawn of 2022 brought a surge in Malaysia’s industrial production, with a staggering 50.1% year-on-year increase. This uptick resulted from the government’s amplified spending on infrastructure projects and a flourishing construction sector.
However, the initial growth proved fleeting, as industrial output only experienced a meager 1.8% year-on-year expansion in January 2023. The downturn primarily stemmed from the reduced production of wood products, furniture, and non-metallic mineral products.
Despite this, Malaysia’s industrial sector remains a vital pillar of its economy, contributing to 37.76% of the GDP. Anchored by the semiconductor and metalworking industries, this vibrant sector is projected to magnetize approximately US$ 23 billion in investments by 2025.
Semiconductors
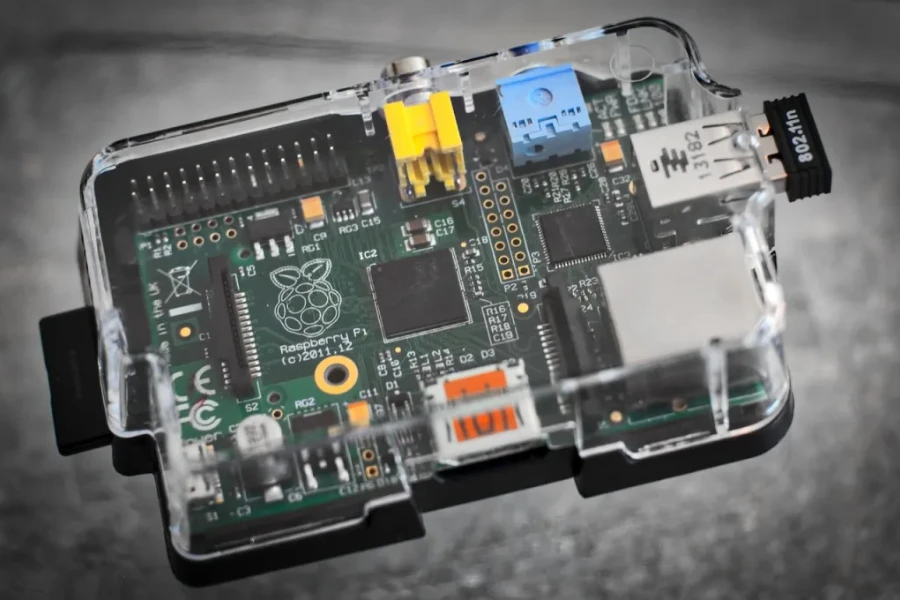
As a driving force behind Malaysia’s economic growth, the semiconductor sector flourishes, with Penang alone accounting for 80% of the nation’s global semiconductor output.
In a bid to transform Malaysia into a global hub for chip testing and packaging, the government has poured significant resources into R&D and human capital development. Consequently, the coming years will likely see a rise in demand for sophisticated industrial pieces of machinery, such as photolithography machines and deposition equipment.
Integral to the semiconductor manufacturing process, photolithography machines deftly transfer circuit designs onto silicon wafers. Utilizing light, these machines project the circuit pattern onto the wafer’s surface, which is coated with a layer of photoresist. Once exposed to light, a chemical reaction ensues, imprinting the circuit pattern onto the wafer.
Equally vital in semiconductor manufacturing, deposition machine tools deposit various materials, including metal films and polysilicon, onto the wafer’s surface to create the distinct layers that form the semiconductor device. Employing a range of techniques—such as chemical vapor, physical vapor, and atomic layer deposition—these machines showcase their versatility and importance in the process.
Metalworking
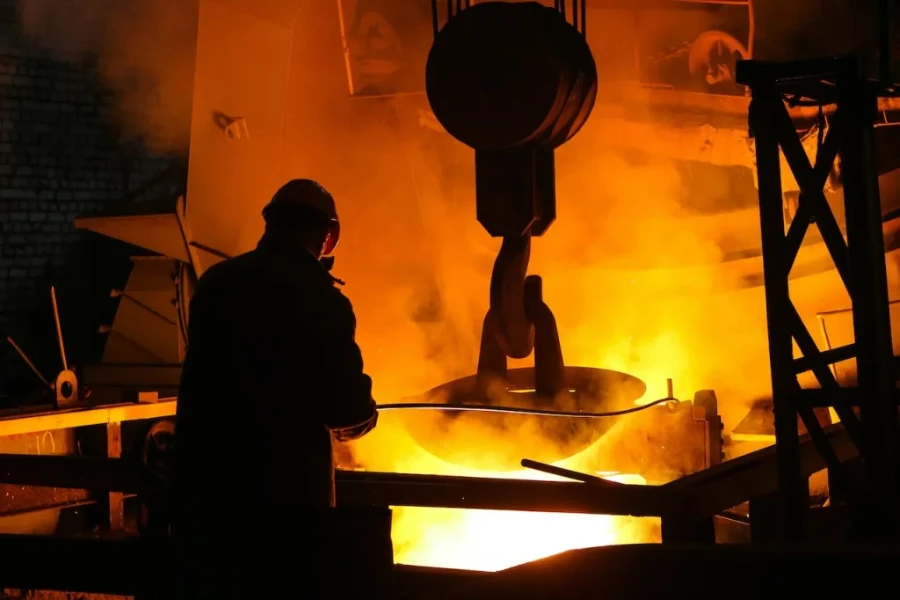
Beyond electronics and semiconductors, Malaysia’s burgeoning metal processing sector stands as another cornerstone of the nation’s economic growth. As reported by Statista, the production index of fabricated metal products in Malaysia climbed to 107.7 points in 2021.
This surge in metal framework demand will spark the need for advanced metalworking machinery, particularly lathes and shearing tools. Lathes, for example, are sought after for their ability to meticulously craft metal components.
➕ Read more: 11 key industrial machines used in the metalworking industry
These versatile machines shape metal parts by removing material from a rotating workpiece through various operations like cutting, sanding, and turning. Consequently, they empower manufacturers to create intricate metal pieces with tight tolerances.
Likewise, shearing machines will experience increased demand due to the growing appetite for lightweight and energy-efficient metal structures across industries like transportation and eco-friendly construction.
➕ Read more: Essential tips to consider before buying a shearing machine
These innovative machine tools equip manufacturers with the ability to produce slender, precisely cut metal sheets and profiles for cutting-edge applications, such as electric vehicle frames and energy-saving building materials.
➕ Read more: 6 important industrial machinery market trends in Malaysia
Singapore
Although not as large as its neighbors, the city-state of Singapore has become one of the most flourishing industrial hubs and ranks as the world’s 5th largest exporter of high-tech goods. This success is attributed to the commitment of the Singaporean government to adopting Industry 4.0 technology and progressive manufacturing methods.
This tiny island nation has set forth an ambitious objective with its “Manufacturing 2030 Vision,” which is aimed at achieving a remarkable 50% growth in the manufacturing sector by the year 2030. Moreover, this small country features a highly-skilled workforce that attracts leading high-tech companies. After all, Singapore ranked second on Global Talent Competitiveness Index (GTCI) for 2022.
Electronics and precision engineering serve as the lifeblood of Singapore’s industrial sector, driving growth and pushing the boundaries of technological evolution. These pivotal industries have played a significant role in the manufacturing sector, which notably contributes approximately 20% to the nation’s GDP.
Electronics
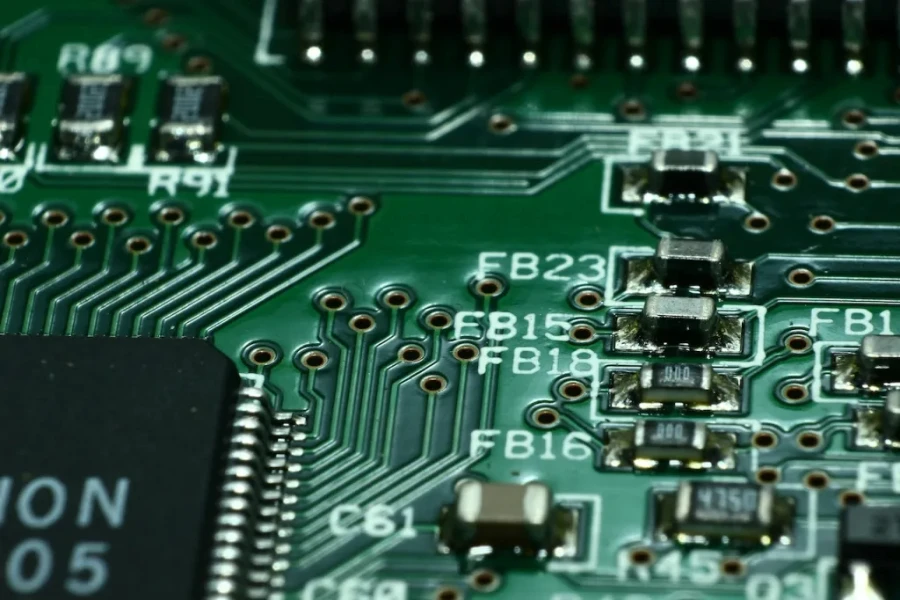
In Singapore’s industrial market, the electronics field will continue to hold the top spot and is expected to achieve a total revenue of US$ 1.76 billion in 2023. Moreover, from 2023 to 2027, the electronics industry is predicted to experience a compound annual growth rate of 7.7%.
With Singapore emerging as a prominent electronics manufacturing center, the need for specialized wire bonding machines is expected to grow significantly. Such machinery produces microscopic connections between electronic components with high accuracy. Moreover, wire bonding machines can perform both ball and wedge bonding using a variety of materials, including gold and copper.
Additionally, demand for electrochemical machines is also expected to increase due to their ability to produce intricate electronic shapes with high precision. Furthermore, these machine tools employ a heat-free, non-contact approach to process thermally sensitive materials like polymers and composites.
Precision engineering
Precision engineering holds a significant place in the Singaporean industrial sector. In 2021, the industrial output from this field generated more than US$ 35 billion. So it comes as no surprise that Singapore has become a leading producer of semiconductor equipment, contributing an impressive 20% to the global output.
As a result of this growth, manufacturers of precision components will continue to demand programmable CNC machines to streamline their engineering processes and eliminate assembling errors. These machines enable users to enter detailed directions via a numeric control system, resulting in complete automation and exceptional accuracy.
On top of CNC equipment, electric discharge machines are also expected to see increased demand, as they possess the capability to process hard metals and conductive materials while maintaining precise tolerances and intricate details. They use electrical discharges to remove material from a workpiece, allowing for the creation of intricate and complex shapes with high precision.
➕ Read more: How does machinery automation change manufacturing?
Thailand
The Kingdom of Thailand, formerly known as Siam, is a country dominated by hilly forested areas and fertile rice fields. This explains why the country heavily relied on agriculture in the past decade, but today, the industrial sector is the backbone of the Thai economy.
The low-cost labor and abundance of raw materials have helped Thailand become an attractive location for manufacturing companies. Furthermore, the country boasts a strong labor participation rate of 67% despite its small population of 57 million people.
Today, the industrial sector serves as the central driving force of the economy, contributing to over 16% of total employment in Thailand. It is also one of the country’s most important export industries, accounting for roughly one-third of its overall GDP.
In addition, the national manufacturing production index (MPI) achieved a high record of 112.28 points in 2022. Consequently, the need for industrial machinery is experiencing a surge, primarily fueled by robust growth in the electronics industry and plastic production.
➕ Read more: A comprehensive overview of the manufacturing sector in Thailand
Electronics
In recent years, Thailand’s electronics industry has experienced substantial growth, contributing to 14% of the nation’s total exports. By 2025, the industry’s value is projected to reach US$ 7 billion.
The country has made concerted efforts to promote a digitally driven economy through the “Thailand Industry 4.0” plan, which seeks to increase the contribution rate of telecommunications and electronic components to 25% of the nation’s GDP by 2027.
As a result of these public initiatives, Thailand has become the second-largest exporter of computer hard drivers and internal components. This explains why high-tech businesses in Singapore will continue to source thin-film deposition machines for the creation of magnetic heads, a crucial element in hard drives.
These deposition machines apply thin coatings of material onto surfaces like silicon wafers or glass substrates, resulting in a remarkably thin layer of magnetic material with consistent thickness.
➕ Read more: What’s the difference between metal coating and metal plating?
Similarly, electroplating machinery will gain more popularity among manufacturers in the coming years. Such heavy equipment allows for coating metal surfaces with a slim layer of a different metal, leading to enhanced strength and increased durability for internal electronic components.
Glue dispensing systems will also gain significant popularity due to their ability to apply adhesive solutions with pinpoint precision on three-dimensional objects. By minimizing human error and enhancing accuracy up to ±0.02mm, these systems prove to be invaluable when dealing with intricate components such as computer hard drives and magnetic disks.
Plastic synthesis

Thailand’s plastics sector contributes a substantial US$ 36.9 billion to the nation’s overall economy, generating 11.8 million tonnes of various plastic goods and byproducts, including resins and bioplastics.
Furthermore, Thailand has emerged as a prominent producer of cellulose and pulp mills, leading to an increased demand for industrial equipment like granulators and hydraulic presses. These machine tools, and particularly granulators, shred and process plastic resin into various forms, including pellets, granules, powder, or flakes.
Additionally, there will be a demand for molding technologies, to transform the raw materials prepared by granulators into a wide range of plastic products. By heating and shaping raw plastic materials, molding machines can create a diverse array of items, such as bottles, containers, automotive parts, and even toys.
➕ Read more: Key factors for sourcing industrial machinery in Thailand
Philippines
The Philippines is a Southeast Asian country situated in the archipelago between the Philippine Sea and the South China Sea. With a working population of over 44 million, this island country has one of the largest labor forces in Southeast Asia and is expected to continue growing as infrastructure development continues to be a priority for the Filipino government.
The Philippine policymakers have been investing heavily in lightning-fast urbanization through the Build Build Build program, which has already made significant progress toward building new transportation networks, energy grids, and industrial center points. In fact, public investments in infrastructure took 6% of the country’s GDP in 2022.
As a result, the Philippines’ industrial sector has grown significantly over the past few years. It now accounts for 25% of the nation’s GDP—the highest percentage since 1980—and is projected to grow further as industrial projects continue to develop throughout the country.
A large part of this economic expansion can be attributed to increases in industrial production volume, which rose 10.6% year-on-year in January 2023. So it’s no surprise that the manufacturing of industrial machinery and equipment propelled a staggering US$ 38.03 billion in gross value from 2020 to 2022. Textile and food processing continue to be two pivotal sectors driving industrial growth in the Philippines.
Textile and apparel
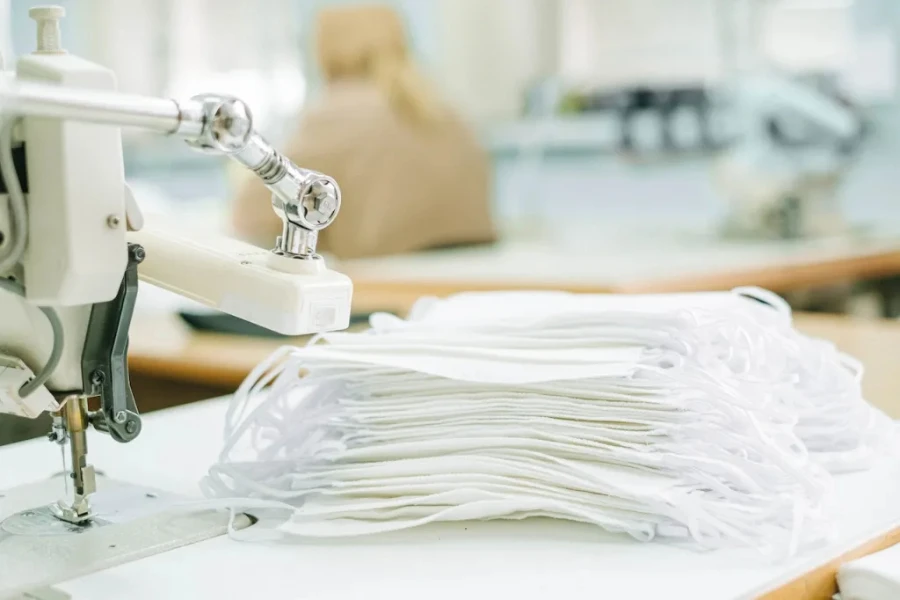
The Philippine textile and apparel industry demonstrates remarkable dynamism, boasting a market valuation of US$ 5.08 billion in 2023. Furthermore, this sector’s growth rate is projected to experience a consistent incline over the subsequent five years, achieving a CAGR of 3.53% from 2023 to 2027.
And with the increasing demand for reasonably priced, non-luxury apparel, there will be a parallel surge in the need for robust dying equipment to execute processing and finishing tasks effectively.
These machines are designed to apply vibrant colors to a diverse range of fabrics, including delicate materials like silk and lace, employing techniques ranging from jet dyeing to beam dyeing.
Highly valued for their ability to impart uniform color distribution, these machines play an integral role in textile production, facilitating operations from weaving preparation through knitting and finishing.
➕ Read more: How to select suitable weaving machines
Moreover, textile manufacturing will require high-speed spinning machines capable of producing yarns with varying thicknesses, textures, and strengths. The spinning process itself yields an array of textile properties, ranging from lightweight and breathable garments to heavy, moisture-wicking items.
Food processing
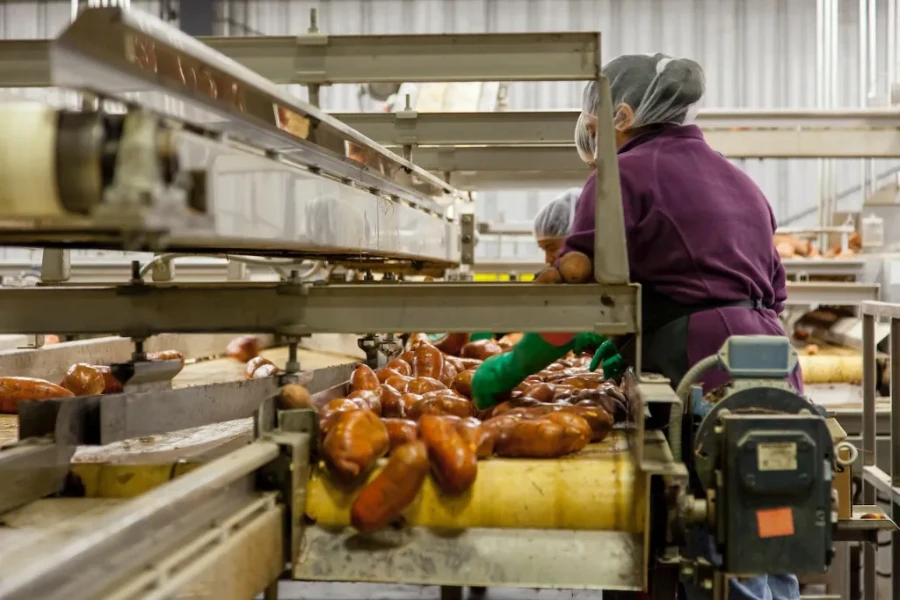
More than 9,000 food processing plants operate across the Philippines, generating an impressive US$ 2 billion worth of goods. Contributing to over 50% of the Philippines’ total manufacturing output, the thriving food processing industry has understandably become one of the country’s leading sectors, boasting a CAGR of 8%.
➕ Read more: Top 8 food manufacturing trends in 2023
In the coming years, the integration of robotics and automation systems in food processing is set to skyrocket. Driven by a desire to boost production speed and minimize contamination risks, food processors are embracing the potential of technology to elevate their operations.
This is especially true for food companies that perform primary processes such as picking, packing, and washing. These processes carry a significant risk of cross-contamination between unprocessed materials and finished products if good hygiene practices are not upheld throughout all stages of production.
The need for sanitation robots in food processing is clear. Not only do they improve product quality by preventing contamination from dirty surfaces or equipment, but they also improve worker safety by reducing contact with harmful chemicals.
Another challenge facing food processors is the need for packaging large quantities at once—which means they need equipment that can handle heavy loads quickly and efficiently.
Automated plastic packaging machines are able to do just that by providing accurate information about how much product has been filled into each package, how full each package is, and whether there are any defects such as damaged packets or missing items.
➕ Read more: 6 key industrial machinery market trends in the Philippines
Indonesia
Indonesia is home to a working force of 135 million people, most of whom are young, making it an attractive labor mine for industrial businesses. The average laborer in Indonesia earns around US$ 82 per month—less than one-fifth of what it would cost businesses to hire someone with similar skill sets in China or India.
The industrial machinery market in this transcontinental country has been growing steadily over the past decade, fueled by low-cost labor coupled with government policies to accelerate economic industrialization. In fact, manufacturing revenues from machinery and equipment stood at US$ 8 billion between 2014 and 2021.
This number is set to grow as Indonesia continues its push toward becoming a global manufacturing center. Indeed, the industrial sector generates more than 19% of the nation’s GDP and accounts for over 70% of its global exports. Auto manufacturing and plastic packaging will continue to fuel demand for industrial machinery and equipment for the foreseeable future.
Automotive
Indonesia is the second largest producer of motor vehicles, selling over 887,000 units in 2021 alone. The country also holds the world’s largest nickel reserve at over 21 million tons. This makes it an ideal industrial hub for producing electric vehicle batteries.
With the manufacturing of vehicles increasing, automotive inspection solutions will be in high demand to inspect vehicle parts such as chassis assemblies and door panels. Vision-guided handling systems with 3D camera scanning capabilities are the most common type of inspection machine tools. These systems allow operators to perform dimensional inspections on auto parts with high accuracy.
➕ Read more: Top 5 machine tool technology trends in the automotive industry
Welding machines are another industrial heavy equipment that will see increasing demand from the automotive industry. They are metalworking tools that use electric current to heat metal parts, so they are malleable enough to be shaped and joined together. These machines are the backbone of automotive manufacturing processes, shaping exhaust systems and building battery packs for electric cars.
Packaging
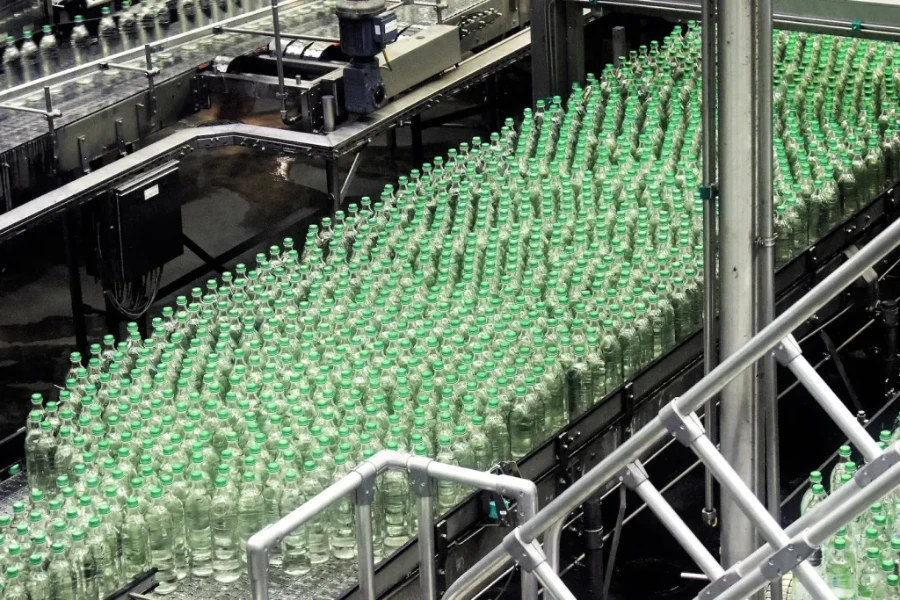
The packaging industry is an impenetrable foundation of almost every Indonesian sector, including food and beverage manufacturing. It is growing at a CAGR of 2.4% with revenues expected to reach US$ 159.2 million in 2024. The flexible packaging segment accounts for more than half of the total market due to its portability, resealability, and cost-effectiveness.
The demand for extrusion tools will rise as the packaging industry continues to grow and become more sophisticated. The applications of these industrial machine tools range from rigid plastics and paper boards to lightweight glass. They use pressure and heat to increase the flow of materials through a die or mold to create shapes from plastic pellets or sheet materials.
➕ Read more: Top packaging machinery trends in 2023
With the growing demand for tightly sealed and protected packaging, the need for machines capable of sealing product packages also escalates. Thus, clamshell closing equipment will remain a vital component for food manufacturing companies.
This industrial equipment ensures that plastic packaging remains sealed and protected, eliminating the possibility of leakage or contamination. They accomplish that by taking two halves of a clam-shaped shell and connecting them with a hinge—all without human interaction.
➕ Read more: An overview of the industrial machinery market in Indonesia
Competitive landscape of the industrial machinery market in SEA
The industrial machinery market in Southeast Asia is characterized by a high level of consolidation, where three key players dominate the market: Mitsubishi Heavy Industries Ltd., Komatsu Ltd., and Caterpillar Inc.
These machinery manufacturers have managed to maintain their stronghold on the Southeast Asian market by leveraging the power of automation and digitalization of their machinery solutions, incorporating advanced technologies such as the Internet of Things (IoT) and Artificial Intelligence (AI).
Incorporating automation capabilities and AI algorithms into their machinery enabled these giant manufacturers to offer heavy equipment that improves the decision-making process, automates repetitive tasks, and enables self-adaptive adjustments in the equipment’s operation.
For instance, Caterpillar Inc. uses IoT and big data to implement predictive maintenance on their industrial machines. They have developed a machine learning algorithm that predicts when an engine will fail based on variables such as temperature, vibration, speed, and RPM.
The algorithm then sends alerts to technicians so they can perform maintenance before the engine fails completely. This allows technicians to schedule preventive maintenance at optimal times rather than waiting for a problem to occur.
Mitsubishi, on the other hand, has advanced digitalization by integrating an automated Directed Energy Deposition (DED) feature into their latest metal 3D printer. This functionality facilitates automatic monitoring and stabilization of the machine’s status.
Furthermore, the DED technology allows the new 3D printing machines to manufacture titanium alloy components with a remarkable precision of 0.05mm, meeting the stringent requirements of the aerospace and aviation industries.
➕ Read more: 8 types of manufacturing equipment you should know
Unlock Southeast Asia’s industrial revolution
Gone are the days when Southeast Asian countries solely relied on primary sectors such as tourism and agriculture for their livelihood. Today, manufacturing is becoming a major driver of economic growth, propelling the region into the global spotlight as a powerhouse of industrial innovation.
With a comprehensive understanding of Southeast Asia’s main industries and the required industrial machinery and equipment, businesses can now confidently source cutting-edge manufacturing machinery and become part of the region’s industrial transformation.