Table of Contents
1. Introduction
2. Types of grease guns and their applications
3. Market trends and insights in 2025
4. Key factors to consider when choosing a grease gun
5. Top grease gun types and features to watch
6. Conclusion
Introduction
Grease guns are essential tools for efficient lubrication, widely used across various industries to maintain machinery and equipment. They deliver precise amounts of grease to specific parts, reducing friction, preventing wear, and prolonging the life of components. Whether for automotive repairs, heavy machinery, or industrial maintenance, grease guns ensure that lubrication is applied accurately and consistently, which helps to minimize downtime and improve overall operational efficiency.
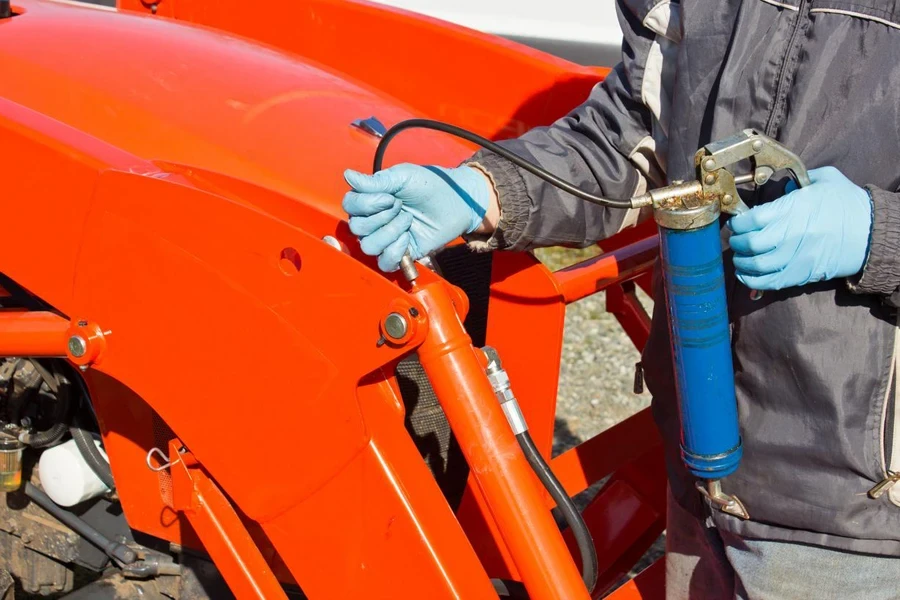
Types of grease guns and their applications
Manual grease guns
Manual grease guns are widely used for basic lubrication tasks that require simplicity and portability. These tools operate without the need for external power sources, making them ideal for smaller-scale jobs where flexibility and control are essential. Lever-style and pistol-grip models are the most common types. Lever grease guns, requiring two hands for operation, can deliver up to 1.28 grams of grease per pump, offering precision for light lubrication tasks. Pistol-grip versions allow one-handed use, making them suitable for tighter spaces and easier operation.
The key advantage of manual grease guns is the ability to control the flow of grease through physical effort, ensuring accuracy. This feature is particularly useful for small workshops and maintenance operations where industrial-scale lubrication isn’t required. These tools are also lightweight and affordable, making them a cost-effective solution for professionals dealing with limited grease volumes or portable maintenance.
Pneumatic (air-powered) grease guns
Pneumatic grease guns are designed to handle high-volume lubrication tasks efficiently and are powered by compressed air rather than manual force. These models excel in environments requiring repetitive greasing, such as automotive or heavy machinery maintenance. Pneumatic models typically deliver higher pressure outputs, making them suitable for industrial settings where continuous greasing is needed. They can reach pressures of up to 6,000 PSI, providing the force necessary to lubricate hard-to-reach areas and heavy-duty equipment.
One of the advantages of using pneumatic grease guns is that they can help decrease operator fatigue and ensure a steady supply of grease is delivered efficiently. However, it’s important to note that these tools rely on access to a compressed air system, which could pose challenges regarding portability and suitability for some settings. Pneumatic grease guns are often preferred in sectors such as construction and manufacturing, where there is a high demand for greasing tasks and heavy workloads.
Battery-operated grease guns
Battery-operated grease guns are becoming increasingly popular due to their portability and ease of use. These models eliminate the need for manual pumping or an air supply, relying on rechargeable batteries to power the greasing mechanism. This makes them highly convenient for large-scale operations or fieldwork, where mobility is key. Modern battery-powered grease guns can deliver up to 10,000 PSI and are capable of dispensing grease up to 75% faster than manual versions.
A key advantage of battery-operated grease guns is their versatility across different settings, from automotive workshops to agricultural machinery. They are ideal for professionals who need to maintain equipment in remote locations or those who deal with frequent lubrication tasks. Despite their convenience, these models can be heavier due to the battery, and the cost is generally higher compared to manual and pneumatic options.
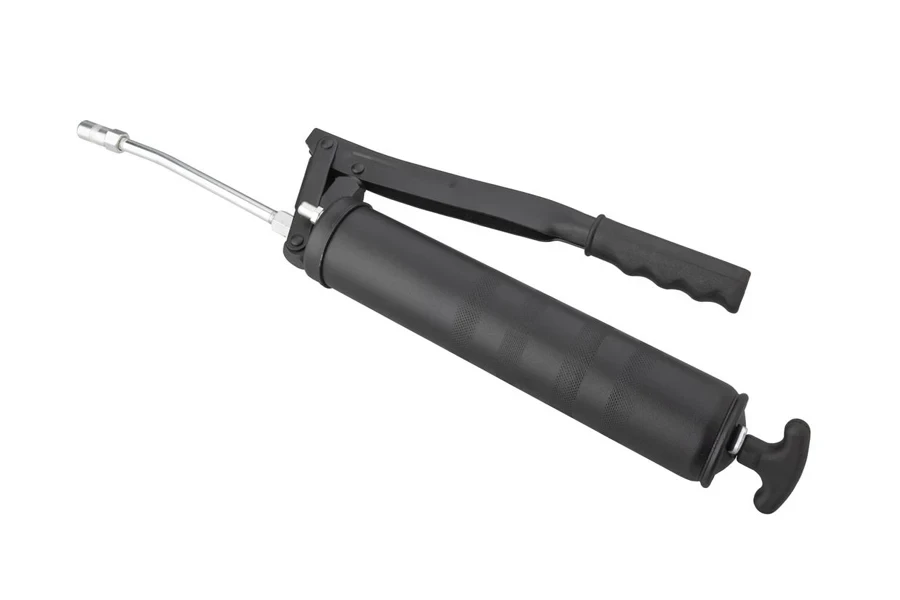
Market trends and insights in 2025
Latest market trends
According to Research Nester, the global grease gun market was approximately USD 1.5 billion in 2023, and they project it to reach USD 3.5 billion by 2036. This growth is anticipated at a compound annual growth rate (CAGR) of 7% from 2024 to 2036, driven by increasing demand across sectors such as automotive, construction, and industrial maintenance.
Emerging technologies in grease gun manufacturing
Technological advancements are reshaping the grease gun market, with new models incorporating features that enhance usability and performance. Key innovations include smart grease guns equipped with digital displays, connectivity options, and data-tracking features. These tools allow for precise control and monitoring of lubrication, enabling predictive maintenance practices across various industries. This integration of smart technology reflects a shift towards more automated and efficient maintenance processes.
Battery-powered versions have become popular because of their ease of use and flexibility. Modern models are crafted to provide increased pressure and quicker distribution speeds, which is ideal for challenging assignments in isolated locations. These improvements cater to workers needing dependable and portable options for industrial purposes.
Moreover, the emphasis on sustainability has resulted in the creation of grease guns that work well with lubricants, meeting the demand for maintenance solutions that are more eco-conscious. Companies are also using durable materials to prolong the longevity of these instruments, guaranteeing their endurance in industrial settings without sacrificing functionality.
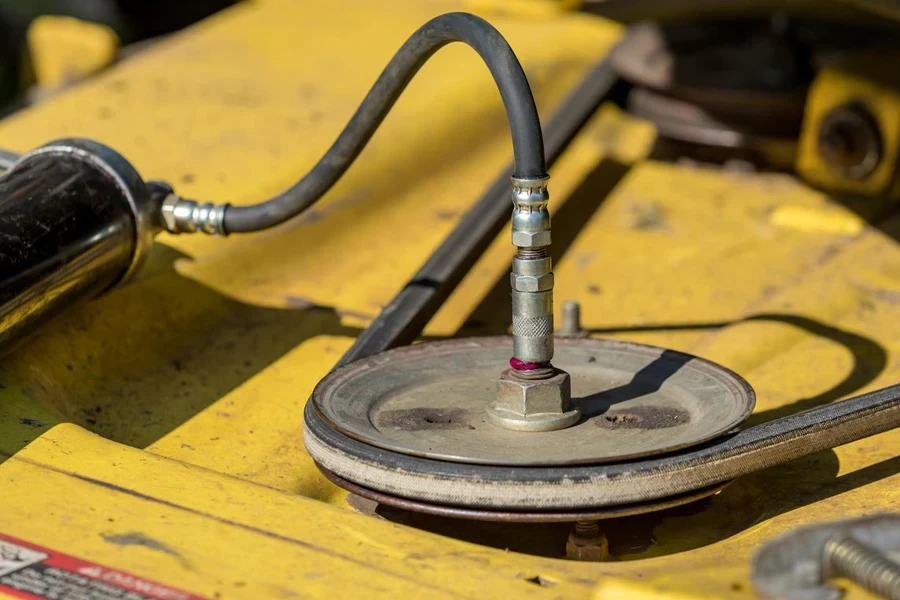
Key factors to consider when choosing a grease gun
Type of lubrication task
Picking the right grease gun largely hinges upon the nature of the lubrication job at hand, as various models shine in different scenarios. Manual grease guns like lever or pistol grip types work best for tasks demanding accuracy and management; lever variants can provide intense pressure, making them perfect for heavy-duty assignments, while pistol grip guns offer convenience and are more suitable for lighter tasks that are done repeatedly. For larger-scale operations, pneumatic and battery-powered versions are more efficient as they provide lubrication effortlessly, which saves time and prevents operator exhaustion.
Pressure output and performance
The pressure rating of a grease gun is a critical consideration, especially for heavy-duty applications. Higher pressure ratings (e.g., up to 10,000 PSI) allow grease to penetrate tight and heavy machinery fittings, which is crucial for industrial and automotive settings. Conversely, tasks requiring less force, such as small equipment maintenance, may not need such high pressure. For instance, lever and pneumatic grease guns typically offer higher pressure outputs than pistol-grip models, making them suitable for challenging environments where robust lubrication is needed.
Portability and power source
Portability is an essential factor when choosing between cordless, air-powered, and manual units. Battery-operated grease guns provide the convenience of portability, making them ideal for field work and situations where flexibility is required. These models combine the power of pneumatic systems with the freedom of cordless operation. In contrast, pneumatic models rely on an air compressor, which may limit their use to environments where a stable air supply is available, although they excel in continuous, high-volume tasks. Manual options, while less automated, are portable and can be used almost anywhere without the need for additional power sources.
Maintenance and ease of use
Ease of maintenance is vital to ensure the grease gun remains reliable and efficient. Factors such as the ease of cartridge replacement, cleaning, and general upkeep can significantly influence the choice. Many modern models feature designs that allow for quick cartridge swaps, reducing downtime during maintenance. Additionally, tools that minimize common issues like air bubbles and clogged fittings ensure smoother operation. For example, priming mechanisms and easy-to-clean components help maintain consistent performance, particularly in industrial settings where downtime can be costly.
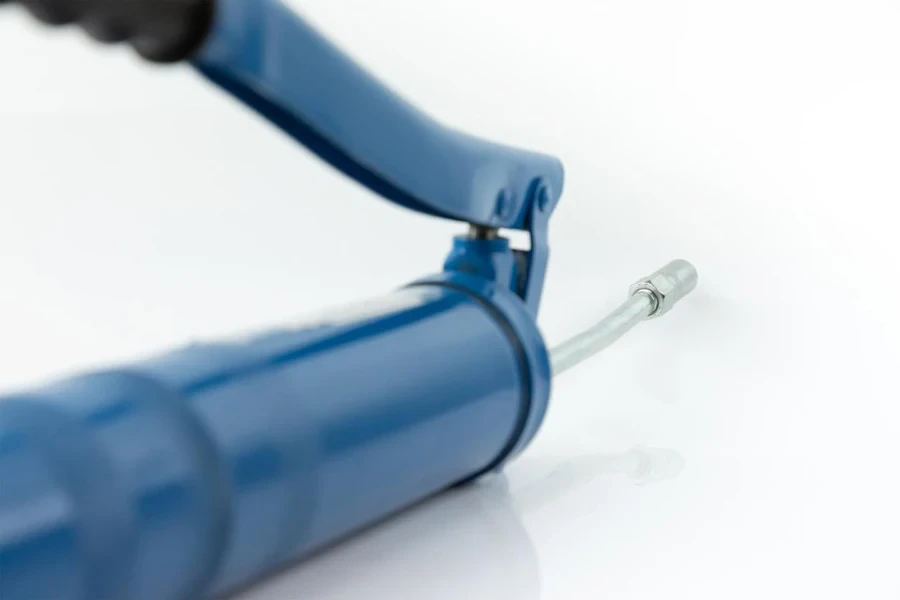
Top grease gun types and features to watch
As industry trends suggest, several types of grease guns have become popular due to their practical features that meet a range of maintenance needs. Below, we focus on the specific features that make certain models best-selling and favored in the market.
Smart technology integration in battery-powered grease guns
Battery-powered grease guns have benefited significantly from emerging smart technology. Modern models now feature variable-speed triggers, LED lights, and digital displays that allow users to monitor pressure, grease flow, and battery levels in real time. These innovations provide better control and precision, particularly in complex maintenance tasks. Additionally, cordless designs ensure mobility, making these tools ideal for fieldwork or environments where flexibility is essential. The integration of longer-lasting lithium-ion batteries further boosts performance, allowing these models to handle multiple lubrication jobs on a single charge.
Enhanced ergonomics and durability in manual and pneumatic models
Manual and pneumatic grease guns are well received because of their robust construction and enhanced ergonomic layouts. Recent versions incorporate lighter materials, like anodized aluminum and high-quality steel, to ensure longevity without unnecessary bulkiness. Comfortable handles and balanced structures help decrease user tiredness from executing repetitive duties. Moreover, certain pneumatic models now offer adjustable speed settings for precision greasing, expanding their adaptability in various industrial environments.
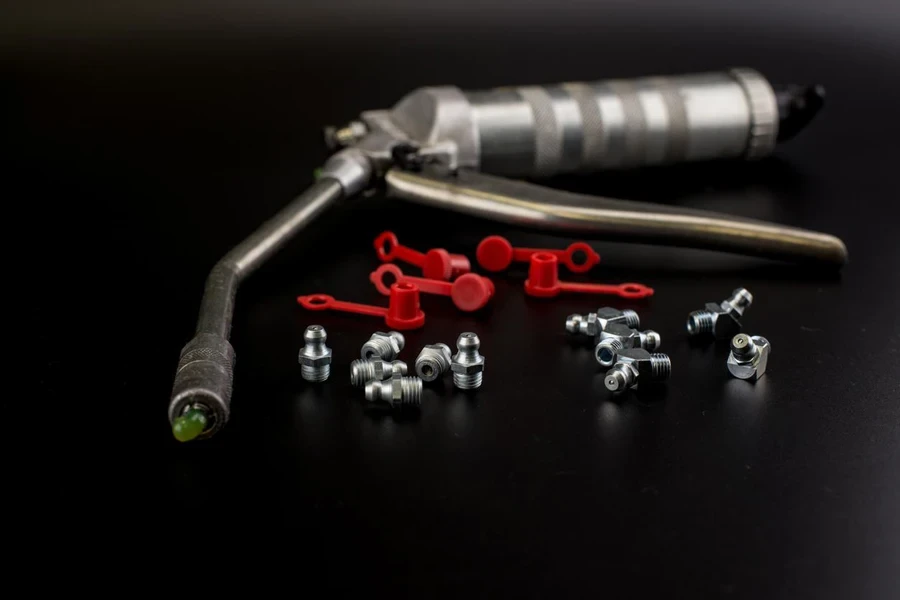
Eco-friendly materials and improved safety features
Sustainability has become a focus in grease gun manufacturing, with companies developing models compatible with biodegradable greases. This ensures safer use in environments where eco-friendly practices are prioritized. Advanced sealing mechanisms and leak-proof designs minimize waste and prevent accidental spills, further promoting environmental responsibility. Additionally, safety features such as anti-leak nozzles, secure couplers, and air bleeder valves have been improved to prevent over-pressurization and ensure consistent, controlled lubrication, reducing maintenance risks.
Compact design for ease of use in mini grease guns
Compact or mini grease guns are designed for light-duty tasks and are favored for their portability and ease of handling. These models are typically equipped with pistol-grip mechanisms that allow for one-handed operation, making them efficient for quick maintenance tasks on smaller equipment. Despite their smaller size, many of these guns maintain durability with robust materials, such as anodized aluminum, and often include flexible hoses for accessing hard-to-reach areas. This combination of portability, durability, and ease of use makes them popular among professionals who need a handy, quick solution for basic lubrication needs.
Conclusion
Selecting the right grease gun is essential for effective and efficient maintenance across multiple industries. In 2025, technological advancements have improved various aspects of these tools, from pressure control and precision to eco-friendly design and smart features. Understanding the benefits of manual, pneumatic, and battery-powered models helps professionals choose tools that align with their specific maintenance needs. With innovations like variable-speed triggers, real-time monitoring, and improved ergonomic designs, modern grease guns offer more convenience, reliability, and safety than ever before. These features minimize downtime, enhance equipment longevity, and promote sustainable practices, making them indispensable in today’s maintenance operations.