Metal polishing is the last step in any metal fabrication process and is used to improve the appearance as well as provide external protection. It improves the sealing and mating capabilities of metal surfaces. There are various metal finishing processes and machines available for different metals. To select the best option for your needs, you must consider several factors involved in polishing.
This guide will offer a brief overview of the market for polishing machines, and then it will highlight the key considerations to bear in mind when choosing a metal polishing machine.
Table of Contents
The global polishing machines market
What is a metal polishing machine?
Types of polishing machines
Factors to consider when buying metal polishing machines
To sum up
The global polishing machines market
The polishing machines market was worth USD 1.5 billion in 2021 and is expected to reach USD 2 billion by 2030. The rising demand for precision machinery due to increased manufacturing activities in the electronics, automotive, and aerospace industries is driving growth.
Automakers increasingly rely on advanced polishing compounds to produce smooth components and parts. Additionally, demand for customized buffing pads and wheels is also expected to drive market growth.
The two most common types are rotary and orbital buffing machines, available in both automatic and manual modes. HTC Group, Kindex, and ASL machines are some of the major players in this market.
What is a metal polishing machine?
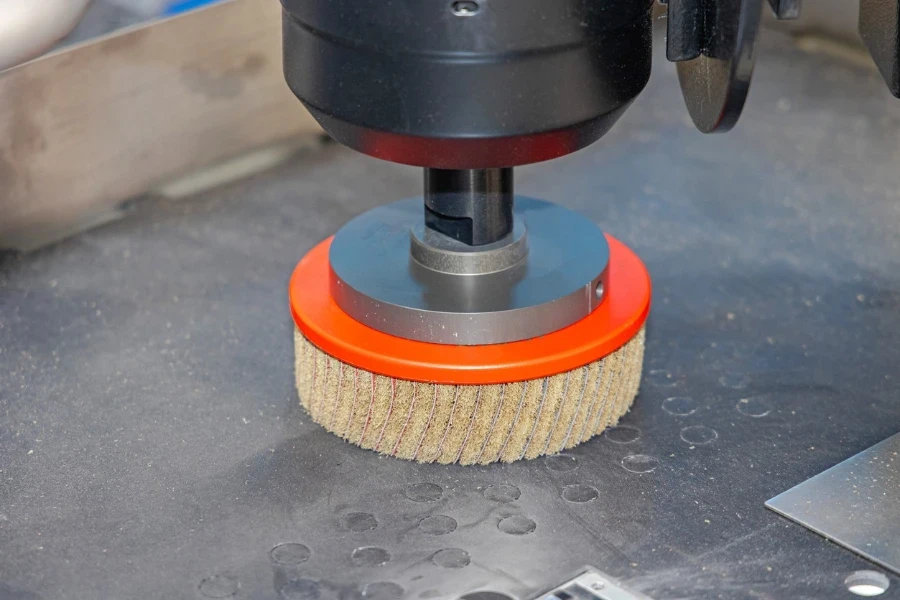
A metal polishing machine is an important finishing tool that smoothens, brightens, and reduces the surface roughness of items made with plated brass, silver, gold, stainless steel, nickel, alloys, or other pure metals. It effectively removes defects from metal surfaces, improves their appearance, and makes them shine.
In addition to improving the aesthetic and cosmetic appeal of the metal surface, a metal polishing tool aids in the removal of oxidation, thereby preventing corrosion and extending the life and functionality of metals.
The metal polishing process
Abrasives are used in the metal polishing process, and the type of abrasive to be used depends on the material being polished. For unfinished materials, several stages must be followed. First, the imperfections on the surface are removed using a rough abrasive, and then finer abrasives are used to provide a shiny and smooth appearance.
Polishing and buffing compounds incorporated into polishing wheels can produce a smooth mirror-like finish. Typically, no additional items are added while polishing; however, lubricants such as was or kerosene can be used in some cases. Furthermore, specialized equipment or die grinders can be used to provide a brighter appearance during buffing.
A fine copper-plated grit can be used to smooth out the surfaces of softer metals like brass. Dry polishing materials are used for the finishing step after the initial grinding process. When additional polishing is required, grease may occasionally be applied. Polishing enhances the surface’s quality and lowers wear and friction.
Abrasives used in polishing
Different abrasives are used for different metals in the polishing and finishing process.
- For instance, gray silicone carbide abrasives are best suited for metals with low tensile strength, such as aluminum, brass, and copper.
- Abrasives such as gray and white aluminum oxide are great for metals with high tensile strength, such as non-ferrous and iron alloys, carbon, and alloy steel. Green chromium oxide abrasives are effective on metals such as steel.
- Materials like leather, canvas, plastic, wool, and rubber are also used for polishing.
Types of polishing machines
- One of the most common types is disc finishers, buffers, and centerless finishers. Disc polishing machines and buffing machines are grinding wheel face grinders that improve the brightness of surface metals. Buffing machines use buffing or non-woven abrasive pads loaded with polishing compounds to finish the parts.
- Centerless finishing machines are used for grinding or finishing, and their applications include processing rods, rollers, rolls, valve systems, and other symmetric shapes. They are commonly used in high-volume applications such as plunge grinding and through-feed. Centreless machines can polish round materials of different lengths and dimensions, providing a glossy finish.
- Cylindrical/outer diameter polishers are used to polish small spaces such as valve systems, cams, rolls, and shafts. These polishing machines can polish surfaces that a centerless finishing machine cannot reach.
- Honing machines are employed to adjust hole alignment and produce the appropriate surface for the application. They work with abrasive stones or sticks mounted within a fixture. When applied to the surface, this fixture rotates and applies pressure.
- Lapping, polishing and buffing machines can be used to create flat and smooth surfaces. Because of the high precision and control of material removal during the polishing process, these machines produce high-quality finishes. They use abrasives in a carrier fluid to process between large lap plates, and lapping removes less material than grinding and polishing.
- Orbital polishers use an orbital motion to produce a smooth finish on a metal surface. They are commonly used to polish automobile parts.
- Polishing lathes are specialized polishers that help achieve a fine or smooth surface finish. They are useful in finishing metallic surfaces or equipment that require high precision.
- Super-finishing polishers are used to reduce the roughness of the surface and improve the surface finish of metallic equipment.
- Oscillatory polishers use a vibrating motion during polishing or finishing.
Factors to consider when buying metal polishing machines
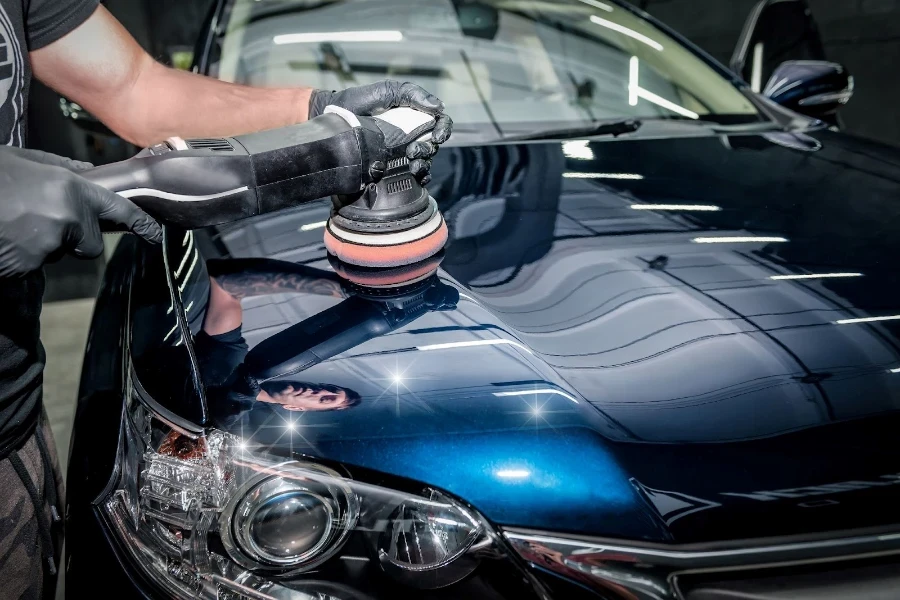
Cost
One aspect that cannot be overlooked is the price. Vibratory polishing, for example, is more expensive than other polishing techniques. However, they make up for it by offering a faster cycle than the cheaper options.
The pricey metal polishing machines have several benefits. For instance, almost all expensive polishers are well-ventilated because they are equipped with blowers that remove dust generated during the metalworking process.
The cheaper polishers are not equipped with blowers, leaving dust in the work area. Furthermore, high-end polishing machines are more compact, have enormous torque, and operate at high cycle rates.
Production speed
Evaluating the production speed and time before deciding on a model is critical. Most polishing machines have speeds ranging from 400 to 1100 RPM, while automatic machines can provide speeds up to 2500 RPM. Knowing the entire metal finishing process, how it works, and what the final product looks like will help users choose the best polishing technique.
Properties of metals
There are many factors involved in polishing, and thus one needs to consider all of them before deciding on a suitable option. One factor that cannot be ignored is the condition of the metal; Hard metals require a more intensive finish or tougher abrasive finishing, whereas softer metals require less intense polishing. Abrasives will be required if metals such as stainless steel and iron are in poor condition.
Surface quality
A good polishing machine should remove contamination, corrosion, oxidation, and blemishes from the surface to enhance its appearance. Thus, ensure that the metal polishing machines are equipped with cutting-edge technologies capable of detecting grain differences in various alloys and making the necessary adjustments to provide a smooth and clean finish.
It is critical to consider surface quality, which is measured in terms of average surface roughness (Ra). Ra denotes the profile’s average deviation from the ideal surface. The standard surface roughness is 3.2 μm (125 μin).
To sum up
As previously stated, metal polishing machines have a wide range of applications in a variety of industries. Some machines are for household use, while others are for heavy-duty work. Before purchasing a metal polishing machine for home or industrial use, one must determine their polishing requirements. Visit Alibaba.com to view the latest metal polishing machines.