Press brakes have traditionally been the go-to bending machines in the sheet metal industry. However, there has been a significant shift towards panel benders as a viable alternative folding machine in recent years. While both have overlapping capabilities, panel benders add various benefits, including enhanced bending efficiency and accuracy.
This guide will give a rundown of both press brakes and panel benders, highlighting their market potential and key applications so that businesses can be ensured to stock the best options for their clients’ needs.
Table of Contents
Press brakes’ market size and potential
Panel benders’ market size and potential
Features to look for when selecting press brakes vs. panel benders
Key differences between press brakes and panel benders
Final takeaway
Press brakes’ market size and potential
The press brake market size was estimated at US$ 569.1 million in 2021 and US$ 594.4 million in 2022. It is projected to increase to US$1.03 billion by 2032, growing at a compound annual growth rate (CAGR) of 6.1%.
Factors driving this market growth include:
- Increased manufacturing activities in various industries, such as automotive, electronics, transportation, and building and construction
- Increased demand for CNC press brakes, which are less labor-intensive and easy to operate
- Improved automation and efficiency resulting in improved tooling, precision controls, and software integration
Panel benders’ market size and potential
The bending machine market value is projected to increase to US$ 1.83 billion, growing at a CAGR of 4.84% from 2021 to 2026. Panel benders contribute to this market growth due to increased demand in various industries, including automotive, heating, ventilation, air conditioning (HAVC), metal fabrication and manufacturing, and architecture.
Factors driving the increased demand for panel benders include:
- Increased automation, productivity, and efficiency
- Great versatility and flexibility, which facilitates efficient and precise bending operations
- Increased demand due to their ability to produce customized panels and components
- Integration of advanced technologies, including intuitive user interfaces, simulation software, and real-time monitoring systems
Features to look for when selecting press brakes vs. panel benders
Both press breakers and panel benders are used for bending and shaping sheet metal. However, they differ in design, capabilities, and applications.
Press brakes
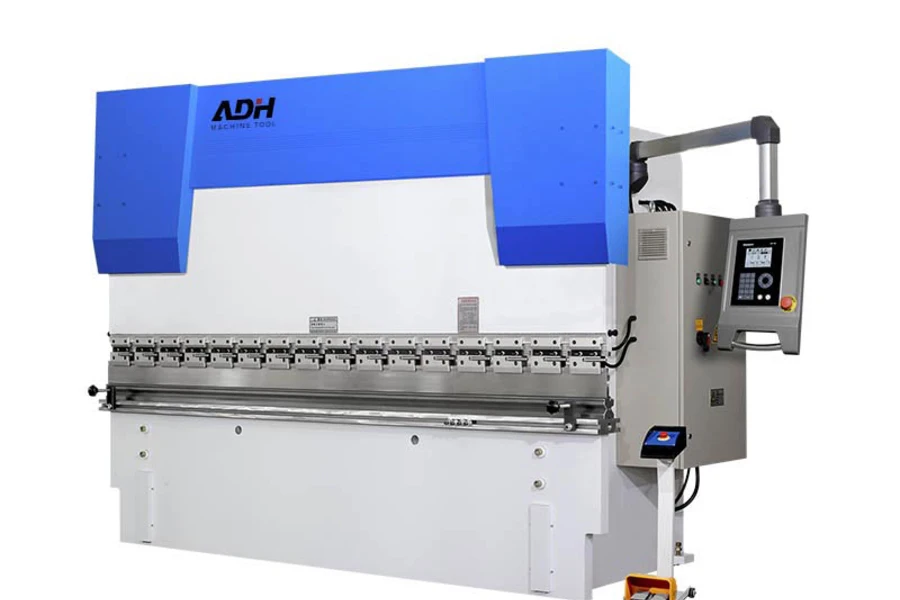
Press brakes are equipment used in metal fabrication, automotive, and construction industries to bend sheet metal. They are designed to handle various materials with precision and accuracy, including steel, aluminum, and stainless steel.
Features
- Press brakes typically consist of a sturdy frame, a bending V-die, a hydraulic or mechanical press system, and a back gauge.
- They are equipped with CNC controls to improve precision and automation
- They are rated in tonnage, primarily within the 40-ton to 350-ton range
Pros
- High precision and repeatability that results in consistent and accurate bending results
- Greater versatility and flexibility
- Consists of tooling and setup configurations that support customization
- They are suitable for heavy materials and complex bending operations
Cons
- Longer setup times
- Lower bending quality compared to panel benders
- Requires more manual handling
Panel benders
A panel bender is a metal fabrication machine used to bend and form metal sheet plates. It is often used with materials of up to ⅛ inch thickness and in projects that require precise radius forming, hemming, or offset bends.
Features
- Panel benders are characterized by features such as CNC controls, a bending beam, clamping and folding tools, and a back gauge
- They have automatic material-feeding systems
- They are rated based on the material thickness they can bend, which is approximately 11 gauge (0.120 inches) in CRS, 10-inch height, and 156-inch length
Pros
- Panel benders have faster setup times and advanced automation capabilities
- Requires less human personnel compared to press brakes
- Can produce a higher number of workpieces per hour than press brakes
- Their higher degree of automation, greater accuracy, and repeatability result in better bending quality
Cons
- Panel benders, especially those with advanced automation and integration features, are expensive to acquire and maintain
Key differences between press brakes and panel benders

While press brakes and panel benders are used for bending sheet metal, they have varying features, designs, and capabilities. As a result, they are used to perform specific bending operations. This section explores their various differences.
1) Machine setup
Each piece of equipment has a different setup, which results in a significant difference in the physical bending of the metal sheet.
Press brakes
Press brakes consist of an upper punch and lower riser (V-die) held using hangers secured by clamps. During a metal bending operation, an operator uses a foot pedal to control the machine, thus bringing down the upper punch on the sheet metal to form the bend into the V-die. The desired angle in the sheet metal depends on the force applied by the punch.
It is crucial to note that different sheet thicknesses and bend radii/angles may require different types of dies, including V-dies and specialty dies. In addition, tooling change over time is essential as the project progresses.
Panel benders
Panel benders are more automated than press brakes. These machines use a counter blade and blank holder to hold the sheet metal during bending. The bending force is generated using the upper and lower universal bending blades, applying pressure to the metal to create the desired bends and folds.
Press brakes are highly versatile since they are designed to accommodate varying material sizes and thicknesses. Unlike press brakes, panel benders do not require tooling change, allowing the operators to work without frequent adjustments and die swaps. Thus, panel benders are more efficient for high-volume sheet metal production and streamlined workflow.
2) Production efficiencies
Panel benders are more efficient in terms of workpieces production per hour since they can quickly complete small batches or complete workpieces. A panel bender can bend a material two to three times faster than a press brake and more consistently. For instance, the Salvagnini P4 Panel Bender is estimated to complete 17 bends per minute due to its high automation.
Unlike press brakes, panel benders require less human personnel to complete the bending process. However, they require manual adjustments after completing each bending cycle, while panel benders are entirely or semi-automated.
3) Bending quality
Press brakes have lower bending quality due to back bending, often resulting in wrinkles and kinks. During bending operations, press brakes use the punch to press the plates into the lower die, often resulting in scratches.
On the contrary, panel benders leverage automation, high levels of precision, and accuracy to eliminate back bending, resulting in high-quality material. Integrating sensors in panel benders helps calculate the bending force, further improving the bending quality.
4) Functionality
Press brakes and panel benders have different functional capabilities:
Press brakes
Press brakes have a wide pressure range, typically from 40 tons to thousands of tons, which allows them to handle materials with varying thicknesses and bending requirements. However, press brakes also have a lower degree of automation than panel benders, which results in a higher need for personnel and longer set-up time.
Moreover, factors such as the type of sheet metal, back gauge, and angle adjustment determine the accuracy of the results. The equipment’s versatility and flexibility allow modifications, resulting in more satisfactory results.
Panel benders
For panel benders, bending operations are based on sheet metal thickness rather than tonnage. They have a bending tolerance of 0.008 inches, which increases precision and efficiency in assembling the workpieces.
Besides, panel benders‘ higher levels of automation reduce the number of personnel required per operation and the setup time. They are also designed to adapt to the shape of the bent sheet metal.
Final takeaway
Press brakes and panel benders are used for bending and folding sheet metals. While they may be used for similar functions, it is crucial to consider their critical functional differences, which can affect their application and results.
Thus, choosing between press brakes and panel benders should depend on the specific production needs, desired automation level, bending quality, and efficiency. Go to Alibaba.com to view a range of listings of quality press brakes and panel benders.