Foundry is a fundamental industry with an irreplaceable position. At present, there are about 26,000 casting companies in China, and the annual production of castings accounts for approximately half of the global total production. Among the many casting methods, sand casting is the most common production method, and the products produced through sand casting account for over 90% of the total casting quantity. However, there are the following problems with traditional sand casting methods:
- The labor intensity is high, the labor environment is harsh, and labor shortages, recruitment difficulties, and retention difficulties are common.
- Mold-making costs are high, and the cycle is long, which makes it hard to meet the production needs of multiple varieties and small batches.
- For manufacturing molds with complex geometric shapes, the density, and accuracy are low, which increases the difficulty of subsequent processing.
Additive manufacturing technology (3D printing) breaks the constraints of traditional preparation processes with computer-aided design to divide the 3D model of a part into multiple 2D sections with the discrete/stacking principle based on digital models and stack the sections into 3D solids through stacking. At present, it is common to apply this technology in the field of sand casting, which precisely meets the needs of the industry:
- Instead of manual operation, all molding processes are carried out in a relatively closed box, and there will be no dust during the printing process, improving the labor environment and reducing heavy physical labor.
- Omitting the process of making molds not only saves production costs but also improves the speed and flexibility of product trial production.
- Improving product size accuracy, enhancing the control ability of sand mold size, reducing the dependence of enterprises on high-tech workers, and enhancing product quality not only reduces the product scrap rate caused by size issues in the future but also improves the efficiency of subsequent casting product processing.
With the continuous development towards high-performance, high reliability, and low cost in fields such as aviation, aerospace, shipbuilding, and new energy vehicles, more and more parts and components are tending towards high strength, lightweight, and complexity, thus promoting the application of additive manufacturing technology in many fields.
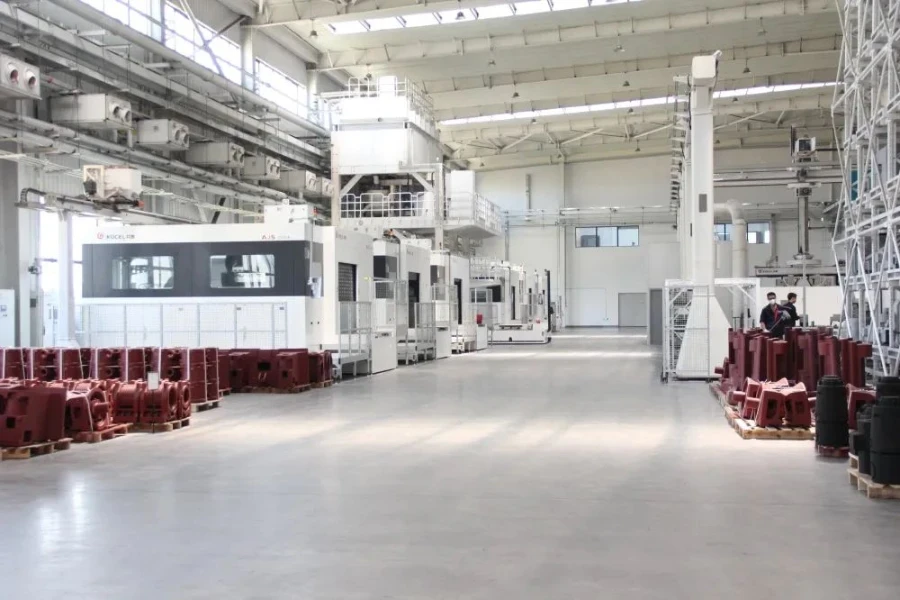
Sharing Intelligent Equipment Co., Ltd., relying on the more than 50 years of casting experience of the Sharing Group, began focusing on the industrial application research of casting 3D printing in 2012. As of now, it has independently developed more than ten casting sand mold 3D printing equipment and established five casting 3D printing intelligent demonstration factories nationwide. Over the past decade of industrial production, our clients have received services in the military industry, aerospace, engines, robots, compressors, and other fields.
Now, let’s review the typical application cases in various industries served by the company.
1. Engine flywheel housing
Product weight: 50-100 kg
Product difficulty: The main structure is a large plane and thin wall (7mm) and is partially thick, prone to defects such as bubbles and cold insulation.
Solution: Adopting inclined pouring process and multi-point exhaust on a large plane to ensure good filling.
3D printing delivery cycle: 15 days
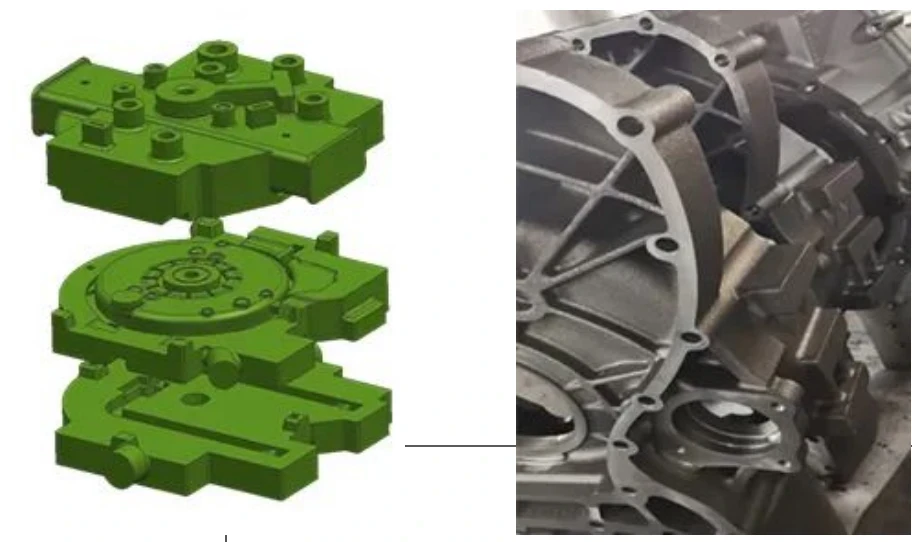
2. Screw compressor housing
Product weight: approximately 1 ton
Product difficulty: The internal cavity structure is complex, local structures are thick and prone to shrinkage and loosening, and there are many drilling parts to be processed.
Solution: Isolate thick parts and use effective chilling measures; adopt specific smelting process (CE4.4 ~ 4.5, △T≤3) to achieve simultaneous solidification.
Mold cost: 700,000 yuan for wooden molds
Mold opening cycle: 50 days
3D printing delivery cycle: 25 days
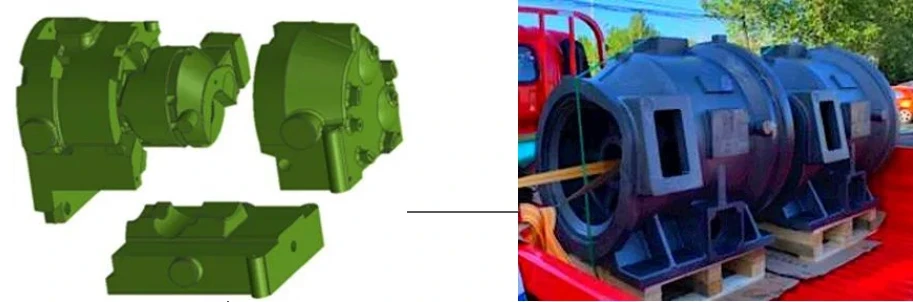
3. Multi-way valve
Product weight: 15-400 kg
Product difficulty: High precision requirements for internal flow channel dimensions and no defects such as drapes; body sampling (near the center) for metallographic testing, with a spheroidization rate of ≥ 90% and a graphite ball count of ≥ 100
Solution: The flow channel core is made into a whole core, ensuring dimensional accuracy and avoiding defects such as core assembly seams, taking long-term inoculants, and specialized spheroidizing agents to achieve metallographic requirements.
Mold cost: 500,000 yuan for metal molds
Mold opening cycle: 90 days
3D printing delivery cycle: 15 days
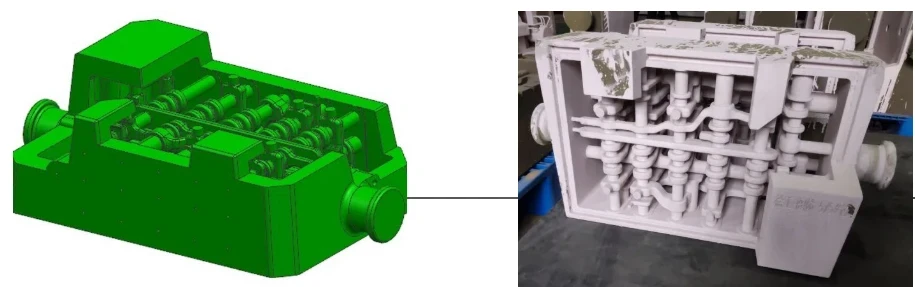
4. Internal combustion engine
Product weight: 30-2000 kg
Product difficulty: The product structure is particularly complex, and any form of welding repair is not allowed. The cost and difficulty of mold opening are high, and the size of the sand core is large.
Solution: Adopting 3D printing form for overall modeling, solving problems such as double-layer tubes, body inner cavity cores, and complex inner cavity structures. The most complex products only need to be divided into five sand cores.
Cost savings: 20% -60% of mold costs
Mold opening cycle: 3-6 months
3D printing delivery cycle: delivery of the first article within 25-30 days
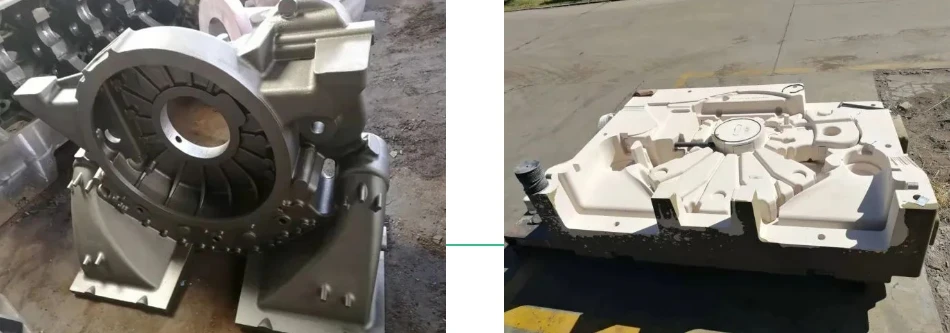
5. Aluminum alloy casting
Product weight: 2-60 kg
Product difficulty: High precision requirements for internal flow channel dimensions and no defects such as drapes; Complex structure, difficult mold forming
Solution: Simplify complexity, connect multiple cores into one, reduce core assembly, ensure dimensional accuracy, and avoid defects such as core assembly seams
Cost savings: 20% -60% of mold costs
Mold opening cycle: 20-90 days
3D printing delivery cycle: 15-25 days delivery
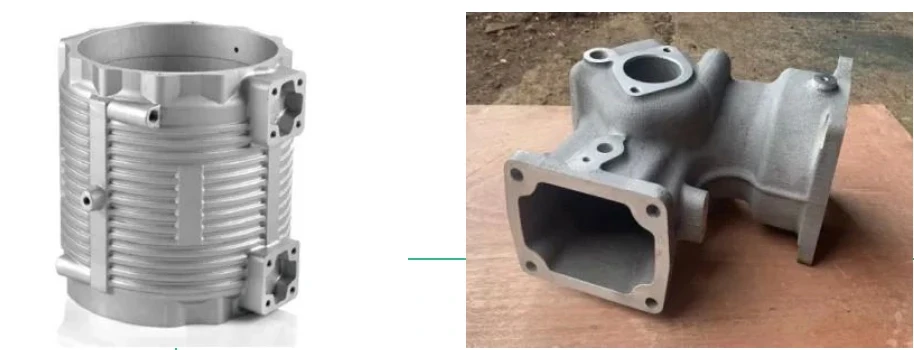
The integration of 3D printing technology and traditional industries has become an inevitable trend. In the field of sand casting, 3D printing technology has also opened up new ways for the development and production of rapid, green, multi-functional, large-scale, complex, and high-demand parts. The sharing meeting will not forget the original intention, continue to focus on promoting the industrial application of foundry 3D printing technology, and improve the transformation and upgrading of the foundry industry.
Source from ofweek.com