Behind every smooth operation and thriving business, there are bound to be some invisible or unsung heroes; safety stock is one of such pillars. Though unseen by the consumers, it serves as the backbone of supply chain resilience, ensuring all favorite products are just an aisle away, no matter the situation or any disruptions.
Continue reading to explore the concept of safety stock, including its definition, significance, and methodologies for calculation, along with a range of practical methods tailored to various functional focuses.
Table of Contents
1. Fundamentals of safety stock
2. Key concepts affecting safety stock levels
3. How to calculate safety stock: key formulas and steps
4. Buffering for stability
Fundamentals of safety stock
Definition in inventory management
Inventory management fundamentally involves balancing inventory carrying costs against risks like stock-outs. In line with this, safety stock serves as a critical reserve that guards against forecasting errors, possible supply delays, and other supply issues. It is crucial for preventing shortages that could disrupt production and maintaining uninterrupted supply.
In essence, safety stock acts as the “extra stock,” in contrast to cycle stock, which refers to the inventory a business regularly uses to fulfill customer orders and replenishes as it depletes. While safety stock levels are calculated for individual SKUs and adjusted periodically, it is vital to customize these levels for different products due to varying consumption rates and lead times.
It’s also important to note that although both buffer stock and safety stock are considered “additional” inventory, they serve distinct purposes. Buffer stock aims to manage unexpected increases in customer demand, making it predominantly demand-induced. Conversely, safety stock is held to guard against potential supply issues, thereby leaning more towards being supply-induced.
The rationale for not simply ordering one extra stock for both purposes often lies in a more detailed supply chain management approach. They are separated to address specific risks more effectively. For instance, maintaining safety stock might involve higher storage costs or capital lock-up, especially if the components are costly or bulky. In contrast, buffer stock might be cycled more quickly, thereby incurring lower carrying costs. However, it may require a larger quantity during peak seasons or for products with unpredictable sales patterns.
The critical role of safety stock in inventory management
Safety stock plays several critical roles in supply chain management, the most crucial being its function as a buffer in inventory management that mitigates risks across various fronts. It guards against potential supply issues that can arise from sudden market shifts or the activities of competitors, ensuring availability even during unexpected supplier failures. Such availability is imperative in preventing stockouts, maintaining continuous operations, and supporting a competitive edge, which in turn, preserves customer trust and loyalty.
Safety stock is fundamentally the key strategy to reduce the operational strain caused by supplier delays and to decrease the administrative burden associated with emergency restocks and logistics. With sufficient safety stock on hand, additional costs associated with rush orders and expedited shipping can be minimized. By maintaining consistent levels of safety stock, businesses can also foster stronger relationships with suppliers and retailers, ensuring smooth operations and steady supply, even when disruptions occur in the supply chain.
Key concepts affecting safety stock levels
Before exploring the various calculations and formulas used to optimize safety stock, it’s crucial to grasp some fundamental concepts that influence safety stock levels. These include variability in supply, lead time, and demand.
Consider a realistic scenario involving a small electronics manufacturer that sells components both online and to local businesses. This manufacturer sources materials from various international suppliers and is particularly vulnerable to delays in receiving one critical component supplied from a region known for occasional political instability and logistical challenges. To guard against potential supply disruptions, the small manufacturer maintains an additional two weeks’ worth of this component as safety stock.
Such a buffer ensures that operations continue smoothly even if shipments are delayed and provides enough inventory to cover both regular sales and any potential increase in demand. In this context, safety stock is vital for managing both supply and demand variabilities—two primary factors incorporated into modern inventory management strategies.
Overall, in this scenario, the electronics manufacturer utilizes safety stock to ensure seamless production amidst supplier issues (supply and lead time variability) and to meet both regular and potentially increased sales demands (demand variability).
This approach highlights that while the classic definitions of buffer and safety stock tend to differentiate demand-induced issues from supply-induced ones, in practice, especially among smaller businesses with limited resources, there may not be a strict separation.
Often, these businesses maintain a higher level of general stock to mitigate all uncertainties, effectively blending the roles of buffer and safety stock to cover both demand and supply variabilities. This integration also acknowledges the interdependence among these factors, especially in today’s highly interconnected market and supply chain environments.
How to calculate safety stock: key formulas and steps
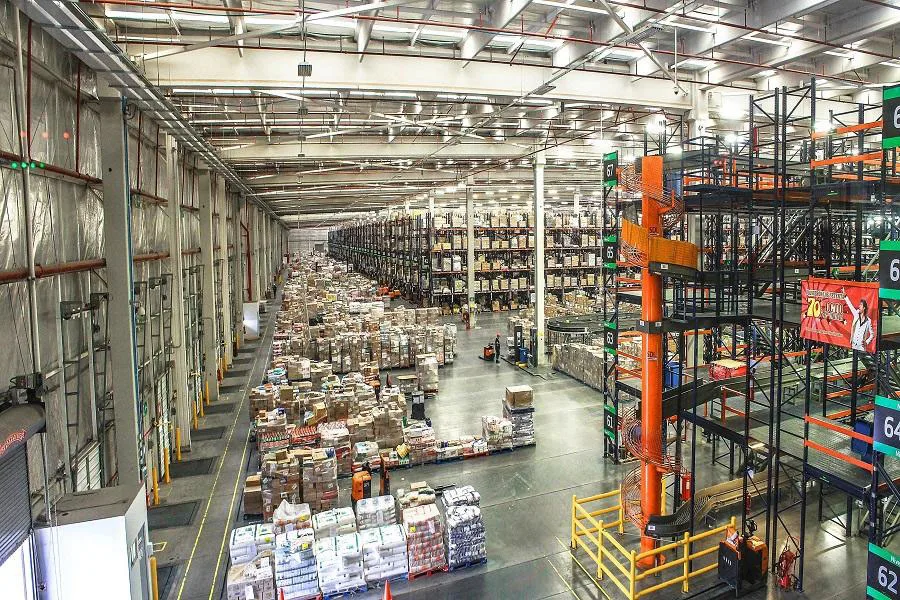
The following safety stock calculation methods are classified according to their primary focus and utility, demonstrating how each contributes to a holistic inventory management strategy. This includes addressing specific challenges and goals such as operational readiness, advanced variability management, and strategic inventory planning.
Operational readiness
The simplest safety stock formula aims to ensure an organization can meet expected requirements efficiently without any disruptions. This basic method enhances operational readiness by simply multiplying daily sales by the targeted number of days for safety stock.
For example, if a business records 100 daily sales for a particular product and wishes to maintain a safety stock for 10 days, it would require a safety stock with 1,000 units (100 units x 10 days). However, this is rather simplified as it does not account for critical safety stock factors such as demand fluctuations and lead times, making it lack any detailed accuracy.
To refine this basic formula, incorporating lead time is essential to make it account for possible delays in replenishment. A common enhancement to this formula is:
Basic safety Stock= AS (Average sales) x LT (Lead Time)
This adjusted formula uses the average daily sales multiplied by the lead time (LT) — the period required to receive replenishment stock. However, for a more sophisticated approach to calculating safety stock, additional variables should be included to provide a more nuanced calculation. The more complete safety stock formula that involves average and maximum amount, which is also named as average – max safety stock formula is as follows:
Average – max safety stock formula= (maximum daily sales x maximum lead time) – (average daily sales x average lead time)
The improved formula above, accounting for the maximum and average daily sales and lead times, can be especially beneficial for businesses experiencing variable demand and supply conditions, offering a more robust calculation of safety stock. Since this formula considers both the maximum potential daily usage and the longest possible lead time, along with average figures, it helps mitigate a broader range of supply and demand risks.
Which formula is better for basic operational readiness largely depends on the specific business context. Ultimately, the most commonly used formula also depends on the industry’s typical risk levels and the specific business’s appetite for risk and complexity in inventory management.
Advanced variability management
When data is sufficient and detailed statistical analysis is feasible, deep analysis of variability beyond the basic formula is recommended for managing the complexities of variability. By considering the actual variability in demand or lead times, the standard deviation safety stock formula uses statistical approaches to calculate safety stock more accurately.
Standard deviation safety stock formula= Z × σLT × D avg
Where:
Z is the desired/ targeted service level, reflecting how often one aims to meet demands.
σLT is the standard deviation of the lead time, calculated based on past lead time data.
D avg is the average daily demand, obtained by dividing total sales by the number of days.
Here are the easy and practical steps to calculate standard deviation safety stock:
1) Z score (Service level determination):
This is to decide the desired service level. Higher service levels result in holding more stock.
Here’s how to find the Z-scores for various service levels:
a) Firstly, determine the service level aimed to be achieved, such as 92%, 99%, etc. For instance, choosing a 95% service level means maintaining enough safety stock to cover 95% of demand scenarios, reducing the risk of a stockout to 5%.
b) Once the service level percentage is confirmed, refer to a standard normal distribution table (Z-table) or use a statistical software or calculator that provides the Z-score corresponding to the cumulative area up to the desired service level. For example:
– 95% Service Level: See Z-score table for cumulative probability of 0.95, that’s about 1.65.
– 85% Service Level: At 0.85 cumulative probability, the Z-score is approximately 1.04.
2) × σLT (standard deviation of the lead time):
To understand fluctuations, track both the expected and actual lead times for several orders. As the standard deviation calculation can be complex, just make use of online calculators such as this free Standard Deviation Calculator, by simply input actual data to get the result.
Steps to make full use of the online standard deviation calculator:
a) Collect Real Data: Gather actual lead times for a series of orders. For instance, if managing 10 orders, note lead time for each: 11, 15, 18, 11, 19, 15, 20, 10, 17, and 10 days.
b) Input Data: Enter the above figures (days) into the online standard deviation calculator.
c) Analysis: The calculator will utilize it to compute the standard deviation.
Important Note: Always use precise operational data for calculations to ensure the standard deviation reflects true variability rather than hypothetical scenarios.
Standard deviation online calculator result samples:
– Real lead times: 11, 15, 18, 11, 19, 15, 20, 10, 17, 10 days. (Standard deviation: 3.66)
– Expected lead times: 10, 14, 14, 10, 14, 14, 18, 10, 18, 10 days. (Standard deviation: 2.99)
3) D avg (Demand average):
Calculate the average number of products sold daily over a set period. Choose a consistent period, such as a month, and compute accordingly:
a) Determine the total monthly sales; for example, if monthly sales= 500 units.
b) D avg = Total Monthly Sales/ Number of Days in the Month = 500/ 30 ≈16.67 units per day
This method involves straightforward averaging based on the company’s sales records and is vital for ensuring the company meets daily sales expectations without overstocking.
Finally, Combine all above results with the formula to find the safety stock = Z × σLT × D avg
As per the examples provided above, the calculation would be:
= 1.65 (@ 95% service level) x 3.66 (standard deviation of actual data) x 16.67 (D avg) = 100.67 units
In short, this sophisticated approach provides a more tailored inventory buffer that reflects the actual variability and the specific risk tolerance of businesses.
Strategic inventory planning
In order to add depth and sophistication to the above safety stock formulas for more strategic inventory planning, one can utilize a few complementary formulas. The Economic Order Quantity (EOQ) formula, for example, helps to determine the optimal order quantity that balances the costs associated with inventory management.
The essence of the EOQ formula is to determine the best order quantity that minimizes the total costs related to inventory management, including both ordering and holding costs.
EOQ (Economic Order Quantity) formula = √(2DS/H)
where:
D represents the annual demand for the product
S is the ordering cost per order, and
H is the holding or storage cost per unit per year
Calculation of the square root of (2DS/H) is crucial as it helps to balance these costs. It allows businesses to find the ideal order size that minimizes inventory costs. It does this by getting the quantity that equates these costs (both costs associated with ordering more often and the costs of storing excess inventory), leading to the lowest possible total cost, allowing businesses to thereby achieve the lowest overall expenses.
For strategic inventory planning, integrating EOQ with safety stock formulas—whether using the average-max formula for basic variability management or the standard deviation formula for more precise variability handling— ensures product availability while minimizing total inventory costs.
In practical terms, using EOQ alongside safety stock involves calculating the optimal order quantity with EOQ and then adding the safety stock quantity, depending on the level of demand and supply variability experienced.
A practical example to illustrate this concept:
Suppose a company has an annual demand (D) of 10,000 units for a product, the cost to place an order (S) is $50, and the holding cost per unit per year (H) is $2. The EOQ would be calculated as follows:
EOQ = square root of (2 * 50 * 10,000 / 2) = square root of 500,000 ≈ 707 units.
Now, if the safety stock calculation based on the standard deviation method suggests keeping an additional 600 units as a buffer due to various demand, supply, and lead time variabilities, the total order quantity would be:
Total Order = EOQ + Safety Stock = 707 units + 600 units = 1307 units.
Together, these formulas represent strategic inventory management approaches that can enhance basic and variability management safety stock formulas by incorporating broader inventory management principles.
Buffering for stability
The integration of safety stock into inventory management systems is paramount for managing the inherent variabilities in supply chains. By understanding and applying safety stock principles, businesses can create a buffer that compensates for the uncertainties of demand, supply, and lead times, all vital elements of safety stock to ensure that there are always spare stocks for stable supply.
Formulas and calculations for safety stock vary, from basic methods that are easy to implement to more advanced models that provide a greater level of precision in highly variable environments. These methodologies are designed to align with specific business needs, addressing everything from daily operational challenges to long-term strategic goals. Through the effective application of these safety stock formulas, businesses can optimize their inventory levels, ensuring an efficient and reliable buffer for long-term stability.
For additional insights and practical tips on inventory management, visit Alibaba.com Reads regularly and stay abreast with the latest industry trends as well as expert advice for more industry insights and business updates.
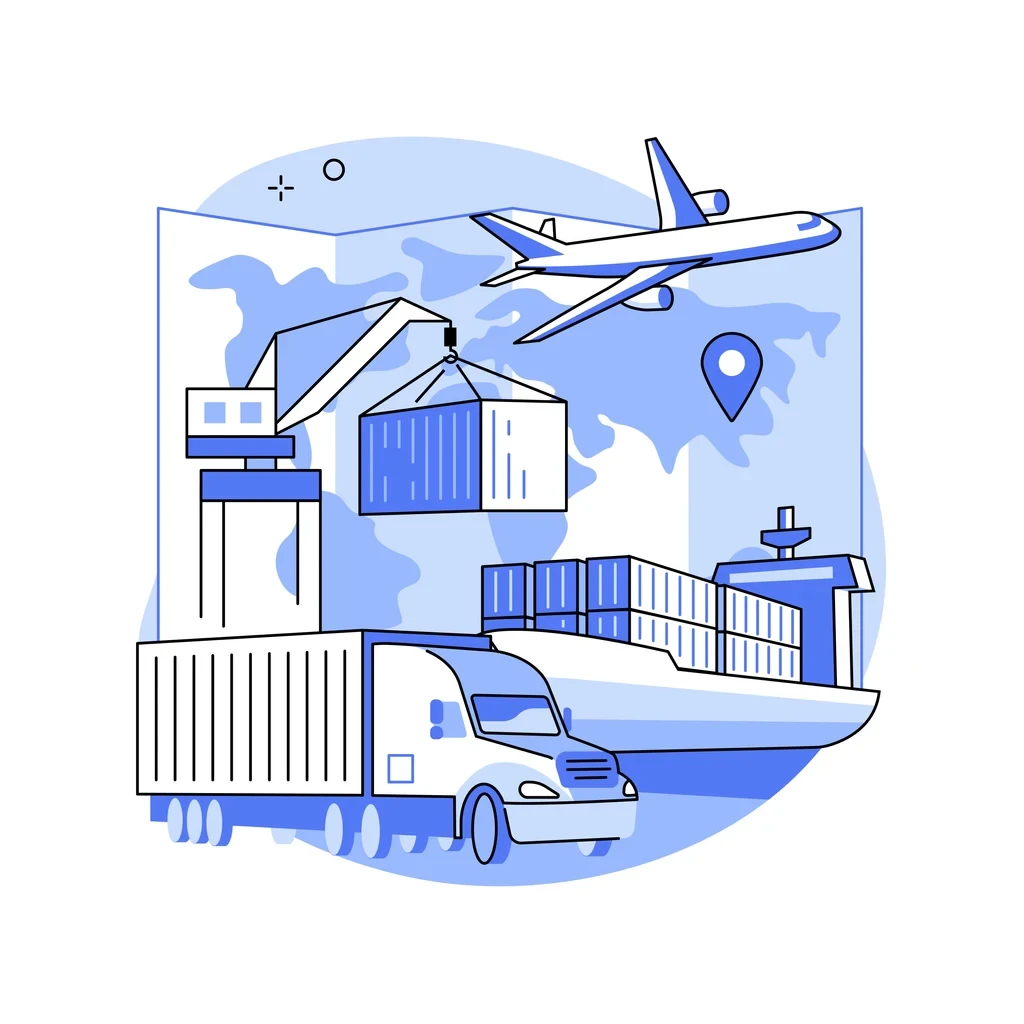
Looking for a logistics solution with competitive pricing, full visibility, and readily accessible customer support? Check out the Alibaba.com Logistics Marketplace today.