The demand for high-quality, freshly-made chips is skyrocketing. However, finding the perfect chip making machine is not necessarily an easy task. With countless options available in the market, navigating the choices and making an informed decision is crucial.
This comprehensive guide equips you with the knowledge and insights to choose the ideal chip making machine. Additionally, you will discover the different types of chip making machines available and the market share of potato chips.
Table of Contents
Potato chips market share
Types of chip making machines
Key factors to consider when selecting a chip making machine
Summary
Potato chips market share
According to a report published by Expert Market Research, by the end of 2022, the global potato chips market size will hit a value of USD 30.7 billion. With a compound annual growth rate of 4.3%, the market is expected to reach a value of USD 39.52 before the end of 2028.
Some of the factors leading to increasing demand for potato chips and chip making machines include technological advancements leading to the development of machines that are more advanced, customization, and innovation leading to increased demand for a variety of chips flavors and textures. Also, the growing snack consumption rate has increased demand for these machines as people seek tasty and convenient snacks.
Regions with high demand for potato chips include North America, Latin America, the Middle East, Europe, and Asia-Pacific.
Types of chip making machines
1. Manual chip making machines
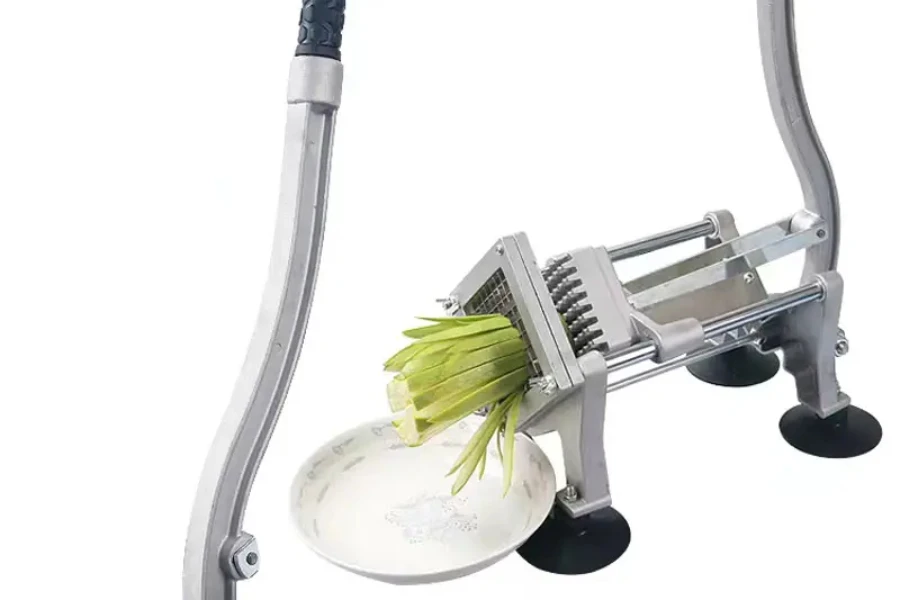
Manual chip making machines are operated by hand, meaning they require more labor throughout the various stages of the chip-making process. These machines are generally compact and well-suited for small-scale or home-based chip production. Typical components of manual chip making machines include a slicer operated by hand, a fryer, and manual controls for operating and regulating the machine.
2. Automatic chip making machines
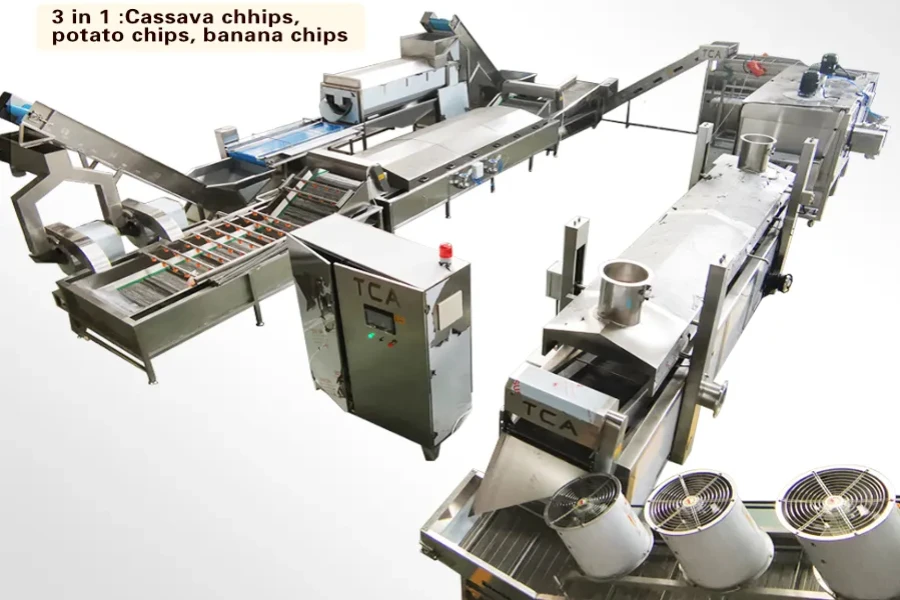
Automatic chip making machines are purposefully engineered to optimize the chip production process, minimizing the need for manual intervention. These machines are outfitted with automated slicing, frying, and seasoning systems. They are well-suited for large-scale chip manufacturing operations with their higher production capacity.
Advanced features like temperature control, conveyor systems, and automated seasoning are often integrated into automatic machines to enhance efficiency and consistency in chip production.
3. Batch fryers
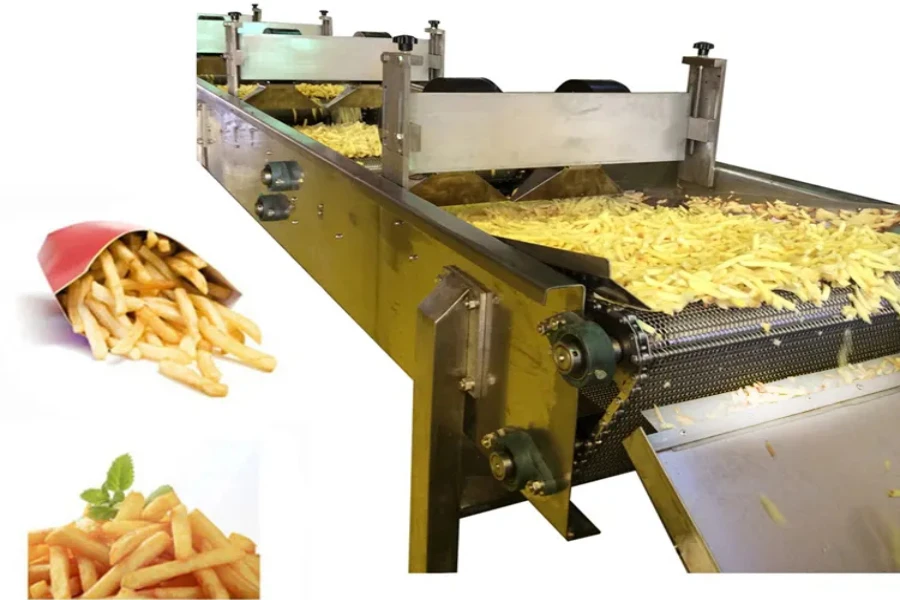
Batch fryers are machines specifically designed for frying chips in batches, ensuring optimal results. These chip making machines typically include essential components such as a frying chamber, heating elements, an oil circulation system, and a control panel.
The key advantage of batch fryers lies in their ability to maintain precise temperature and cooking time control, guaranteeing even frying and consistent quality of the chips. As a versatile tool, batch fryers find their applications in manual and automatic chip production lines, catering to different manufacturing setups and requirements.
4. Potato peeling machines
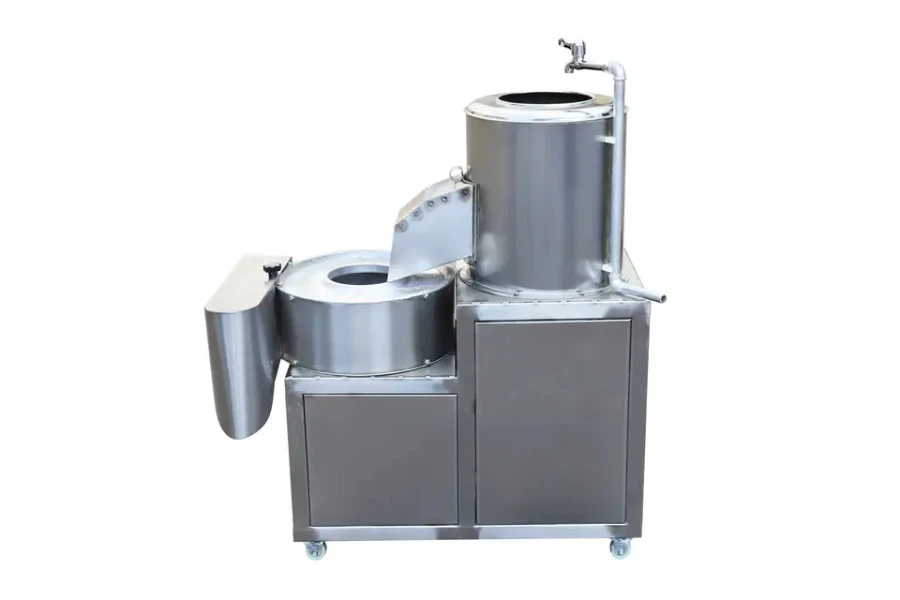
Potato peeling machines are an indispensable asset in large-scale chip production. Their primary purpose is to efficiently and rapidly remove the outer skin of potatoes. These machines employ various techniques, such as abrasive surfaces or water jets to accomplish this task, significantly reducing the need for manual labor and saving valuable time.
Given the substantial quantities of potatoes that must be peeled consistently in large-scale chip production facilities, potato peeling machines are vital in ensuring a streamlined and efficient process.
5. Slicers and dicers
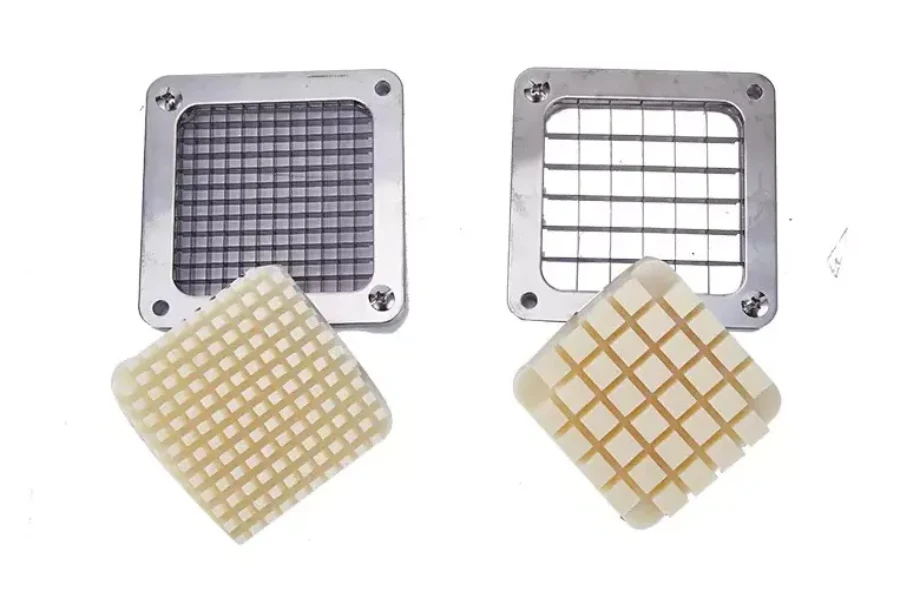
Slicer and dicer machines are purpose-built to achieve precise and uniform cuts of potato or other chip production ingredients. Their main objective is to create consistent slices or strips contributing to the chips’ high quality and appealing appearance. These machines have different configurations, offering manual, semi-automatic, and automatic options to suit diverse production needs.
By ensuring a consistent thickness and shape of the potato slices or strips, slicer and dicer machines play a crucial role in maintaining the desired standards of chip production.
Key factors to consider when selecting a chip making machine
1. Speed
The speed indicates how many chips the machine can produce within a specific timeframe. Evaluating your production requirements and selecting a machine that can meet your desired output is essential. On average, chip making machines have a production speed that ranges from 500 to 1,500 chips per hour. However, it’s important to note that the actual speed can vary depending on the specific machine model, size, and operational conditions.
To determine the speed of a machine, you can assess the number of chips it produces per hour or the processing time required for each batch. This information lets you decide and select a machine that aligns with your production goals.
2. Price
While price is an important factor, it’s essential to avoid solely focusing on the cheapest option. Instead, weigh the features and capabilities of each machine against their cost. Manual chip making machines typically range in price from USD 200 to USD 800, automatic chip making machines range from USD 1,000 to USD 5,000, and industrial-grade chip making machines prices start from USD 5,000 and go up to USD 10,000, depending on the size, capacity, and advanced features.
Additionally, consider the long-term cost-effectiveness by evaluating maintenance and operational expenses. By balancing price, quality, and long-term cost-effectiveness, you can make a well-informed decision that meets your budget and needs.
3. Capacity
Capacity refers to the number of chips the machine can produce within a specific time frame. It is typically measured in pounds or kilograms of chips per hour. The average capacity ranges from around 100 to 500 kilograms (220 to 1100 pounds) of chips per hour. Ranges of chip-making machines can vary depending on the machine’s size, model, and specifications.
To determine the suitable capacity, evaluate production goals and estimate the demand for chips in your target market. By understanding the volume of chips aimed to produce, you can choose a machine with a capacity that aligns with the requirements. This ensures a smooth and efficient production process without overburdening or underutilizing the machine’s capabilities.
4. Compatibility
Before purchasing any chip making machine, it’s essential to consider its compatibility with specific ingredients used for chip production. While many machines are designed for potatoes, specific models can also handle other ingredients, such as sweet potatoes or root vegetables.
To ensure that desired chip varieties meet the desired taste, texture, and quality, choosing machines suitable for processing those specific ingredients is crucial. Verify that the selected machine can effectively handle and process the intended ingredients.
5. Durability
Look for machines constructed from robust materials like stainless steel or food-grade materials that can withstand the demands of continuous use. Choosing a durable machine is crucial as it will be more resistant to wear and tear, resulting in fewer repairs and replacements. This ensures uninterrupted production and extends the lifespan of the machine.
The lifespan of chip making machines can vary depending on several factors, including the quality of the machine, its maintenance and care, frequency of use, and operational conditions. A well-maintained chip-making machine can last 5 to 15 years or more.
6. Energy efficiency
It’s crucial to prioritize energy efficiency to minimize operational costs and reduce environmental impact. Look for machines designed to be energy-efficient, incorporating features such as efficient heating systems or power-saving mechanisms.
Choosing an energy-efficient machine not only helps to lower electricity bills but also aligns with sustainability efforts. These machines contribute to environmental preservation and resource conservation by reducing energy consumption.
7. Noise level
This factor is particularly significant if the machines will be used in residential areas or shared workspaces. Opt for machines with built-in noise reduction features or operate quietly to create a more comfortable working environment for operators and those nearby.
A machine with low noise emissions is crucial for maintaining a pleasant atmosphere and minimizing disturbances during production. It helps to create a more harmonious working environment and prevents noise-related inconveniences, particularly in settings where noise regulations or considerations are essential.
8. Key components
When buying these machines, components like the processor, control unit, conveyor system, stainless material, and slicing mechanism must be considered. The processor and control unit is vital for the machine’s performance and accuracy, ensuring efficient operation and precise control over the manufacturing process.
A robust conveyor system is necessary to handle the required capacity, offering reliability and smooth material flow. Additionally, a high-quality slicing mechanism delivers consistent chip thickness and shape.
Summary
This guide has aimed to help retailers discover the perfect chip making machines. By considering a range of factors, from price to capacity and durability, one can be ensured to confidently source the right models for a range of client needs. Visit Alibaba.com to explore a wide range of options and confidently purchase the ones that meet your needs.