A research consortium including Farasis Energy, Kautex Textron GmbH & Co. KG (supplier of energy storage systems) and the Fraunhofer Institute for High-Speed Dynamics, Ernst-Mach-Institut, EMI is working to make plastic-based battery housings safer by means of virtual design and thus increase the safety of electric vehicles.
Farasis, a developer and producer of high-performance lithium-ion battery technology and pouch cells for electromobility is leading the method development of the simulation model for mapping the thermal runaway of individual cells and propagation in the module. The company is also providing support on all battery-related topics within the project.
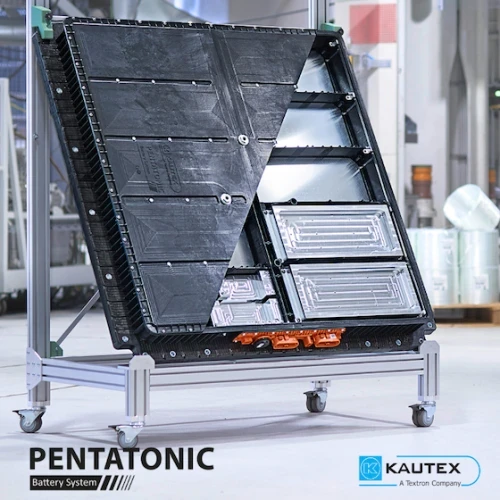
The three-year project—SiKuBa—“safe and sustainable plastic-based battery housings”—received €2.6 million from the German Federal Minsitry for Economic Affairs and Climate Action and started in July 2023.
Plastic enclosures have many advantages over metal enclosures. They are lighter, more sustainable, and cheaper to produce, and have better electrical insulation. In the event of a damaged cell, the battery housing can be exposed to enormous thermal loads if thermal runaway of individual cells occurs due to the damage and, in the worst case, this reaction spreads to adjoining cells (thermal propagation).
The battery housing has a high safety-relevant function in this case, as it contains the spread of the resulting hot gases and particles. One challenge, however, is proving its safety, which is complex and expensive.
This is where the SiKuBa project comes in. The formation and propagation of hot gas and particle flows and their interaction with structural elements are to be analyzed experimentally and transferred to simulation models, which will lead to increased cost- and time-efficiency in the development phase. It will also be possible to assess battery safety regarding load case scenarios, materials, and component design.
Fundamental effects are investigated at laboratory level, including thermomechanical material behavior and cell degassing. The knowledge gained is integrated into simulation models and finally validated by physical tests on a demonstrator housing that closely resembles the planned product. The simulation methods developed not only enable significant time and cost savings during the development phase, but also a comprehensive assessment of battery safety under a variety of different load case scenarios, materials, and component design.
Farasis Energy, together with its partners, will develop a detailed model for simulating thermal runaway or enhance the existing models within the company. In future development processes for module and pack projects, the insights gained from the developed simulation model will be utilized to expedite development and save on costly testing. Additionally, these simulation models enable the company to achieve a quicker and safer integration of plastic-based module and pack enclosures.
Source from Green Car Congress
Disclaimer: The information set forth above is provided by greencarcongress.com independently of Alibaba.com. Alibaba.com makes no representation and warranties as to the quality and reliability of the seller and products.