A GlobalData guide to competing EV powertrain technologies
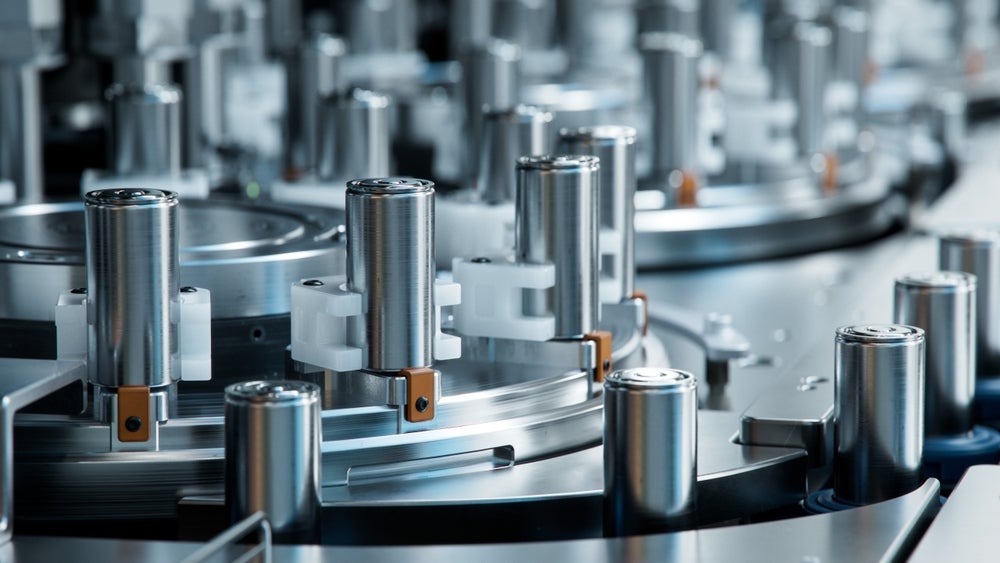
Batteries are the twenty-first century’s oil barrels
Over the past decade, the battery industry has progressed sufficiently to enable portable consumer electronics, the mobile internet, the first electric cars, and the initial adoption of intermittent renewable power storage and generation. Given stored energy’s accelerating and expanding role in tackling climate change, it will become one of the world’s most significant industries over the next ten years.
Will there be enough batteries?
As governments worldwide get serious about decarbonizing their economies, demand for cheap, safe, high-performance, long-lasting, and low-carbon-footprint batteries will soar, most notably from the automotive industry.
Consequently, supply chain bottlenecks will materialize over the next decade. The lack of low-cost, easy-to-purify raw materials to feed the world’s existing and planned battery gigafactories is the biggest threat to supply security. Moreover, the decline in investment in crucial mineral mines – coupled with the growing importance of environmental, social, and governance (ESG) factors – will restrict the development of new capacity.
There will likely be a severe but temporary global battery shortage by 2025 due to a sharp increase in demand for electric vehicles (EVs) and a shortage of mined and refined battery metals. However, the industry is investing heavily to prevent this from becoming a sustained threat by reducing its use of scarce materials, developing new materials and battery technologies, and, most importantly, creating a global battery recycling industry.
Meanwhile, China’s control of the entire global supply chain, from mines and refiners to component markers and cell producers, is a mounting geopolitical issue. The US and Europe are taking significant steps to reduce the dependence on China within their battery supply chains by 2030. Battery recycling is as much about geopolitics as it is about environmental sustainability. The circular battery economy will be critical to the energy transition, and nations (and companies) must develop domestic recycling as EV volumes and end-of-life volumes rise sharply.
The chemistries – some basic principles
Battery technologies span many chemistries, different cell types, and alternative technologies.
A battery is a container consisting of one or more electrochemical cells in which chemical energy is converted into electricity. They are used as a source of power. Batteries are critical facilitators of many other technologies. They are integral to modern mobile lifestyles and the mass production of electric vehicles (EVs). Battery and energy storage technologies will be foundational in the transition to renewable energy.
There are two types of battery cells: primary cells and secondary cells.
- Primary cells produce an electric current by an irreversible chemical reaction and are referred to as disposable batteries.
- Secondary cells create this electric current through a reversible chemical reaction. These are often referred to as rechargeable batteries or storage cells.
A fuel cell is another energy source, but it is not a battery. Batteries create energy using the chemicals already inside them. In contrast, a fuel cell uses a continuous, external supply of fuel flowing through it as the source of chemicals for electricity generation. Fuel cells have been used in unmanned space probes, cars, and for backup emergency power. However, the fuels used – typically hydrogen – have been considered too dangerous for everyday use.
Batteries convert chemical energy into electrical energy
Batteries store chemical energy and convert it into electrical energy through an electrochemical reaction. They consist of three main components: a positive electrode (cathode), a negative electrode (anode), and an electrolyte. The two electrodes are made of different materials. The electrodes are separated from one another by a separator, which is semipermeable to certain chemical species, and the battery is housed in a casing.
When a battery is connected to an electric circuit, an electrochemical reaction happens. Electrons flow from the anode, through the wire to power a connected device, and to the cathode.
Every battery cell contains a limited amount of reactive material. Eventually, the electrochemical processes within the battery will stop supplying electrons to the negative electrode, and electricity will stop flowing. For this reason, the power available in a battery is limited.
Recharging
Secondary batteries can be recharged using an external source, such as solar panels, wind turbines, car brakes, or mains electricity. During recharge, the electrochemical reactions happen in reverse, restoring the cell and its components to near their original state. However, phenomena such as battery hardening and dendrite formation prevent batteries from recharging an infinite number of times. Dendrites can lead to dangerous short-circuiting, though ceramic separators are being developed to help alleviate the issue.
Lithium-ion (Li-ion) is the dominant battery technology for connected devices (e.g., laptops and smartphones), electric vehicles (EVs), and renewable energy storage in the home. In all these use cases, safety is of paramount importance. Li-ion wins in these fields because of its safety. As the demand for smaller, more powerful batteries with longer lifecycles grows, researchers are actively trying to solve the problems of short-circuiting and overheating, which can lead to dangerous fires and explosions.
Li-ion cells store more energy for a given weight (energy density)
Li-ion cells can store more energy for a given weight and volume than lead-acid or NiMH-based batteries and allow for faster recharging and discharging. These properties make them ideal for energy storage for electric vehicles, where great energy density in a lightweight package is essential.
Lithium iron phosphate (LFP) batteries are another battery type used in today’s portable electronics. LFPs have a lower energy density than Li-ion batteries, so the latter is the typical go-to for power-hungry electronics that drain batteries at high rates. However, LFPs can withstand high temperatures with minimal degradation and are suited for objects that need to run for extended periods before being charged. In addition, LFP batteries typically have more lifecycles than Li-ion batteries. That is, they can be charged and discharged more times. Arguably, one of the biggest advantages of LFPs over Li-ion batteries is safety. Improved thermal and chemical stability mean that LFPs stay cool in hot temperatures and are incombustible (do not catch fire) if mishandled during rapid charging or discharging, or during short-circuiting.
Advanced battery chemistries are also being developed that may offer advantages over commercially available batteries.
Performance advantages include a lighter weight, higher energy density, broader temperature tolerance, extended lifecycle, and improved safety. For example, the liquid electrolyte in Li-ion batteries can become incredibly volatile if exposed to outside air, such as during a crash or a failure of the cell’s structure. Lithium battery fires are especially violent and difficult to extinguish, often needing to be completely immersed in water for multiple days to become fully inert. There is no evidence to suggest EV fires happen with any greater frequency than combustion-vehicle fires – indeed, they may even be statistically less likely.
However, EV makers must still reassure the public that their vehicles are safe. Samsung’s disastrous launch of the Galaxy Note 7, a smartphone plagued by Li-ion battery fires, thrust the potential dangers of this battery chemistry into the public eye – a mistake that EV makers will not want to repeat.
Solid-state batteries are the next most viable option
Solid-state cells generally use the same lithium-ion-based chemical reaction to store and discharge energy as conventional cells. The difference lies in the electrolyte used to separate the anode and cathode. Conventional cells use a liquid-based electrolyte – commonly a lithium salt suspended in an organic solvent – while solid-state cells swap that out for a wafer-thin solid electrolyte, usually made from either ceramic, polymer, or glass.
Removing the liquid electrolyte brings many potential benefits. Solid-state cells are lighter and more compact than their liquid-based counterparts, meaning pack weight can be reduced, or energy capacity increased. They should be more resistant to lithium dendrite formation, which will improve power discharge performance and raise potential charging speeds, along with extending the service life of the battery pack. In addition, once mass manufacturing is achieved, they should be easier and quicker to make than conventional Li-ion cells thanks to the removal of industrial solvents.
There are even more pronounced benefits offered by solid-state cells in the field of battery safety. Fires caused by defective or damaged lithium-ion cells have been widely publicized (eg Chevrolet Bolt and its LG-sourced batteries). In many cases, these fires occur because internal failure or external damage has caused the volatile lithium electrolyte to become exposed to the outside air, causing it to ignite and setting off a chain reaction that can destroy the whole battery pack. Solid electrolytes sidestep these problems entirely and are highly resistant to fire and explosion – even in the event they are punctured or impacted.
While they offer many theoretical benefits, no company has yet demonstrated the ability to mass manufacture solid-state cells for light vehicles, with most still at the bench-test stage. There are still some issues left to solve including designing the solid electrolyte and electrodes in such a way that they interface evenly across their entire surface, because any warping can create gaps that limit cell efficiency. In addition, material stability has been shown to be a problem, with the electrolyte’s brittleness leading to microscopic fractures that limit cell performance.
Blue Solutions, a subsidiary of France’s Bolloré, has won a contract to supply its solid-state cells for Daimler’s eCitaro G articulated urban bus – the first recorded commercial supply agreement for the technology. However, the optional solid-state pack needs to be deliberately heated to a relatively high operating temperature of between 50C and 80C – sapping some range in the process and making it inappropriate for use in light vehicles with their unpredictable usage patterns.
Fuel cells (hydrogen) – a long-term bet
Fuel cell electric vehicles (FCEVs) generate power on board by oxidizing fuel – usually hydrogen – through a fuel cell membrane, with the only emission being water. This power can be sent directly to the electric motor or stored in a separate battery for later use. FCEVs can be quickly ‘refuelled’ similarly to combustion vehicles by refilling the tank with hydrogen, eliminating the lengthy recharge period required by BEVs. The push toward hydrogen is also partially driven by its potential role as part of a circular energy economy. Here, renewable wind or hydroelectric energy is used to crack hydrogen from seawater. The hydrogen then acts as a store for the off-peak energy generated by those sources.
While FCEVs have many potential benefits, the technology needs refinement before it can compete with BEVs. The cost of generating hydrogen is currently higher than the cost of producing gasoline, making refills expensive. Plus, the infrastructure to support FCEVs has yet to be built, while EV recharging networks are already growing rapidly.
FCEVs may be of the greatest value to heavy-duty and commercial vehicles. Batteries are heavy so are not well suited to long-range trucks because the sheer weight of batteries needed would use up too much potential carrying capacity. The predictable routes long-range trucks take also require fewer hydrogen refuelling stations to serve effectively.
In essence, FCEVs are seen in the industry as a likely direction of travel for transportation in the long-term – with their applications most likely initially in heavy-duty commercial vehicles alongside closed-loop charging station networks.
Source from Just Auto
Disclaimer: The information set forth above is provided by just-auto.com independently of Alibaba.com. Alibaba.com makes no representation and warranties as to the quality and reliability of the seller and products.