Charcoal making machines have brought about a remarkable transformation in charcoal production. These ingenious devices transform diverse biomass materials into charcoal, presenting a greener alternative to conventional manufacturing techniques. By integrating cutting-edge technology, these machines have simplified the production process and notably accelerated it, ushering in a transformative era for the industry.
This guide takes an in-depth look into the key factors to consider when acquiring a charcoal making machine.
Table of Contents
Market share for charcoal making machines
Charcoal making machine structure
Types of charcoal making machines
A guide to buying charcoal making machines
Summary
Market share for charcoal making machines
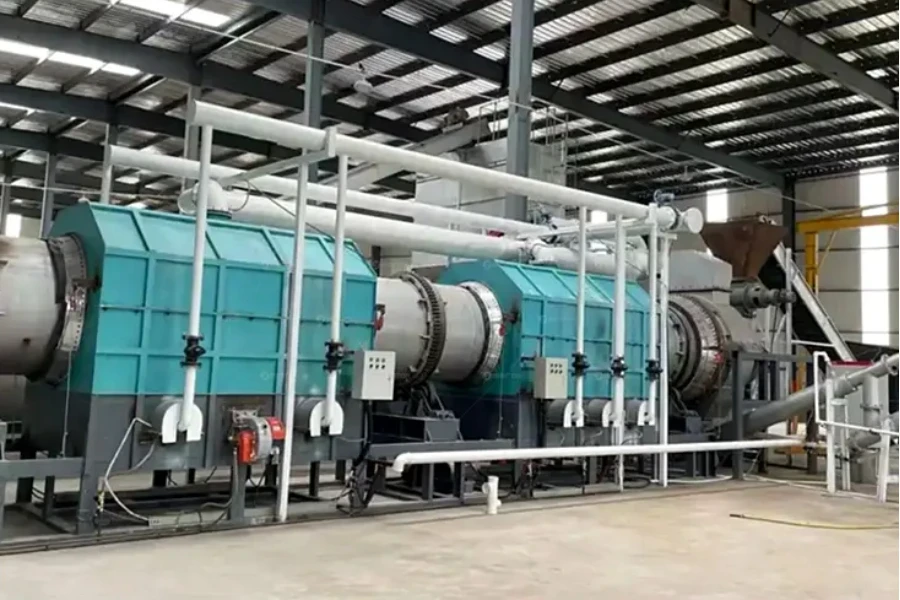
A report published by Data Intelo shows that the global market size for charcoal-making machines will grow at a CAGR of 6.1% from 2022 to 2028. The market share for these machines has soared due to a confluence of factors. With a heightened global focus on sustainability, these machines offer an eco-friendly solution by converting biomass into charcoal. Their efficiency, emissions reduction, and streamlined production have made them crucial for businesses aiming at both economic and environmental gains.
The demand is pronounced in regions like Southeast Asia (including Indonesia, Thailand, and Vietnam) and parts of Africa, where agriculture and forestry thrive. Similarly, areas in Europe and North America with strict environmental regulations also seek charcoal making machines for greener practices.
Charcoal making machine structure
A charcoal making system contains essential additives for efficiently transforming biomass into charcoal. The process starts with the feeding gadget, which introduces raw materials like timber chips or sawdust. These substances are then put into the carbonization chamber, the machine’s center, where they undergo controlled heating to provide charcoal.
Whether electric, gas, or biomass, the heating source is answerable for initiating and maintaining the carbonization technique. Once carbonization is complete, the collection and discharge machine comes into play, facilitating the elimination of the finished charcoal from the system.
Managing structures and safety features are incorporated to ensure particular and safe operation. These systems display and adjust the temperature, incorporate safety mechanisms like pressure alleviation valves and emergency close-offs, and oversee the overall technique. The aggregate of those components allows the green manufacturing of charcoal.
Types of charcoal making machines
1. Traditional charcoal kilns
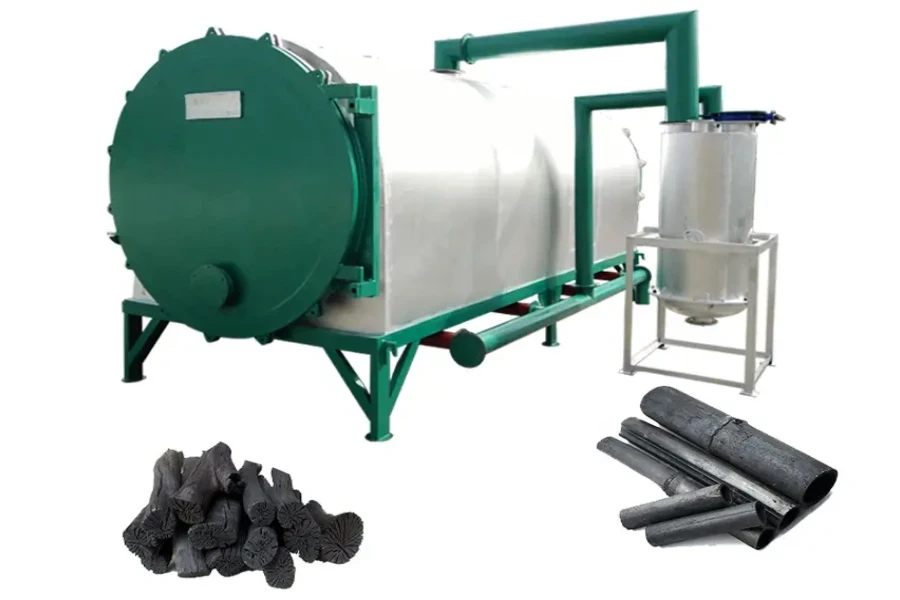
Traditional charcoal kilns have been used for centuries and involve the slow pyrolysis of biomass materials in a low-oxygen environment. While culturally significant and straightforward, they tend to have drawbacks regarding efficiency and emissions. These kilns are commonly used in small-scale, traditional operations where modern technology may not be readily available or affordable.
Traditional charcoal kilns, often with a capacity ranging from 100 to 500 kilograms per batch, uphold their time-honored legacy. However, they work leisurely, taking 6 to 8 hours for a single batch to complete. In terms of cost, these kilns exhibit variability, with smaller models coming in at approximately USD 1,000 to USD 5,000, while larger and more sophisticated variants can reach prices exceeding USD 10,000.
Pros
– Traditional kilns hold cultural significance, preserving traditional methods
– They are simple to operate without the need for advanced technology
– Initial setup costs are lower compared to modern machines
Cons
– Traditional kilns are less efficient due to their long carbonization process
– Limited temperature control can result in uneven charcoal quality and higher VOC emissions
– The produced charcoal may lack uniform quality
2. Retort charcoal kilns
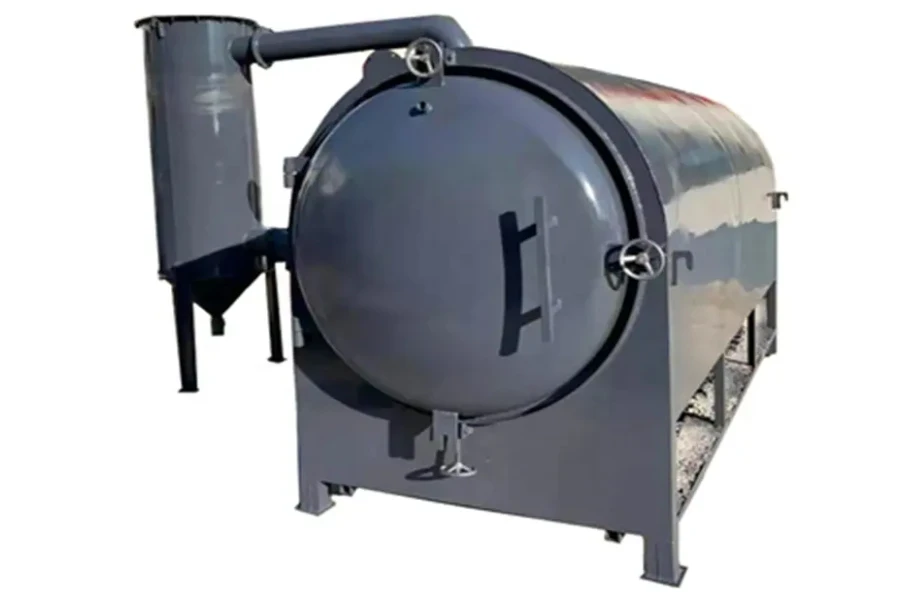
Retort charcoal kilns are designed to capture and recycle the gases and heat produced during carbonization, improving energy utilization and reducing emissions. The closed-loop system ensures that gases generated during the process are re-burned to provide heat, thus enhancing overall efficiency.
Retort charcoal kilns offer a step up in capacity, producing 1 to 5 tons of charcoal per batch. Thanks to their closed-loop design, they accelerate the carbonization process, completing it in 4 to 6 hours. The initial investment ranges from about USD 5,000 for smaller models to USD 20,000 or higher for larger, more efficient units.
This type of kiln is particularly favored for its ability to produce higher-quality charcoal while minimizing environmental impact. Retort kilns are commonly employed by medium to large-scale producers, prioritizing output quality and sustainability.
Pros
– Enhanced energy efficiency through gas and heat recycling
– Production of high-quality charcoal with precise temperature control
– Reduction of emissions through closed-loop gas re-burning
Cons
– Requires a higher initial investment in complex equipment
– Operating retort kilns may demand more training and expertise compared to traditional methods
– Best suited for medium to large-scale production, not ideal for small-scale operations
3. Continuous carbonization furnaces
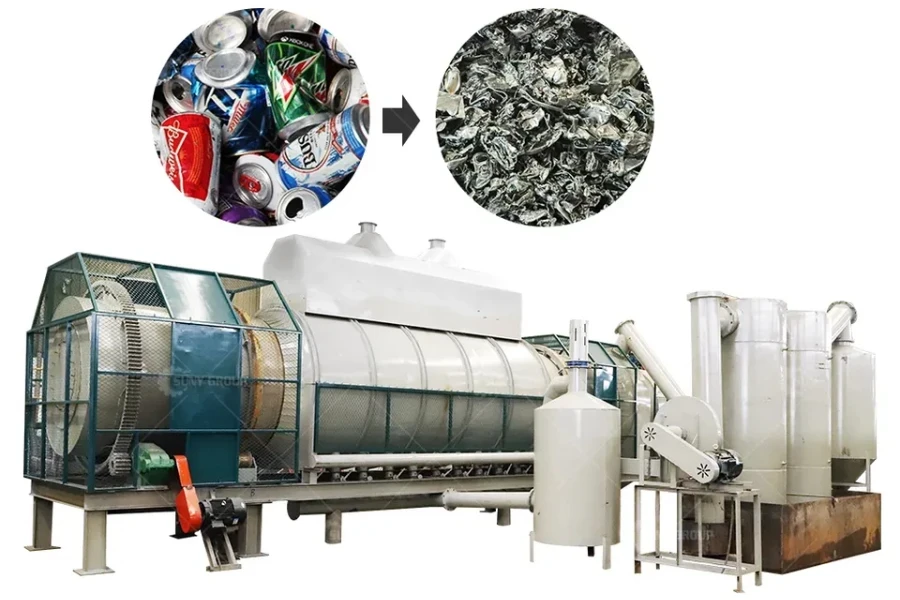
Geared towards industrial-scale production, continuous carbonization furnaces offer a streamlined charcoal-making approach. These furnaces operate continuously, allowing for a consistent output of charcoal. They have advanced temperature and airflow controls, producing efficient carbonization and uniform charcoal quality.
However, these furnaces require substantial investment and are better suited for operations with significant biomass resources and high production demands. Their automated nature and large-scale capabilities make them ideal for enterprises aiming to produce charcoal on a commercial level.
These furnaces are industrial workhorses, with capacities ranging from 5 to 20 tons of charcoal per day or even more. They operate continuously, ensuring a consistent output, and typically take 1 to 2 hours per batch. However, their price tag reflects their industrial prowess, starting at USD 50,000 and scaling up to USD 100,000 or more for the largest models, depending on their size and features.
Pros
– The continuous operation ensures a consistent charcoal output
– Advanced controls result in efficient carbonization and uniform charcoal quality
– Well-suited for commercial enterprises due to automation and large-scale capabilities
Cons
– Substantial upfront investment is needed for equipment and infrastructure
– Best suited for operations with abundant biomass resources and high production needs
– May entail higher maintenance complexity and oversight
4. Charcoal briquette machines
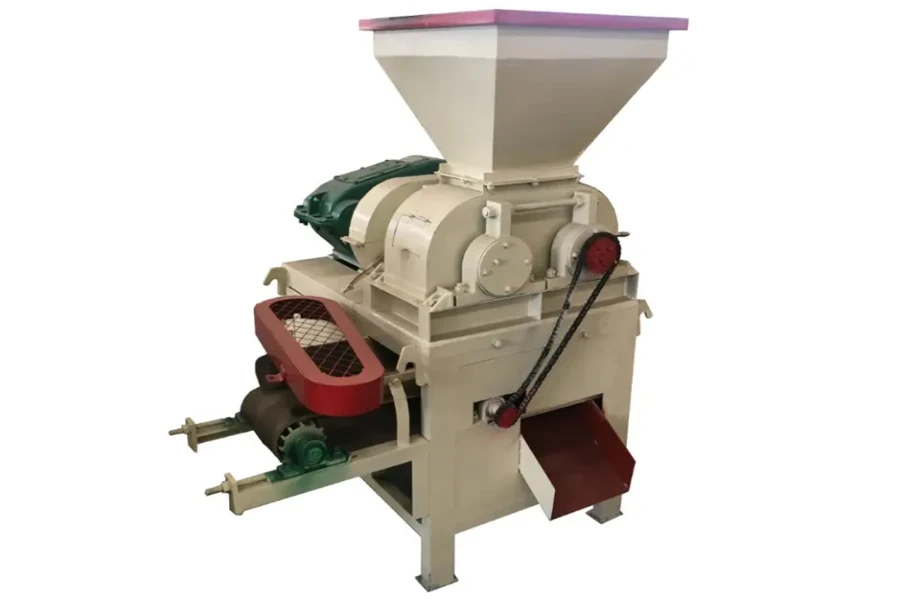
Charcoal briquette machines focus on transforming loose charcoal dust or biomass into compact briquettes. These machines often employ binders and additives to facilitate compression and improve the briquettes’ ignition characteristics. The resulting briquettes are uniform in shape and density, making them easy to handle, transport, and store.
These machines are famous for domestic and commercial use due to their convenience and extended burn time. Charcoal briquette machines cater to those who prioritize ease of use and efficient packaging of charcoal.
Charcoal briquette machines offer varying capacities, ranging from small, manual units producing approximately 50 kilograms per hour to larger, automated systems capable of generating up to 5,000 kilograms (or 5 tons) of briquettes per hour.
Entry-level manual machines typically start at approximately USD 500. On the other hand, larger, high-capacity, and feature-rich automated units can range from USD 10,000 to over USD 100,000, depending on their production capacity and advanced capabilities.
Pros
– Briquettes offer convenient packaging with uniform shape and density
– They provide a longer burn time than loose charcoal
– Ideal for domestic and commercial users who value ease of use and efficient packaging
Cons
– Dependence on binders and additives may impact charcoal purity
– These machines specialize in briquette production and are not versatile for other charcoal products
– There is an initial cost involved in purchasing and maintaining the machinery
A guide to buying charcoal making machines
1. Capacity
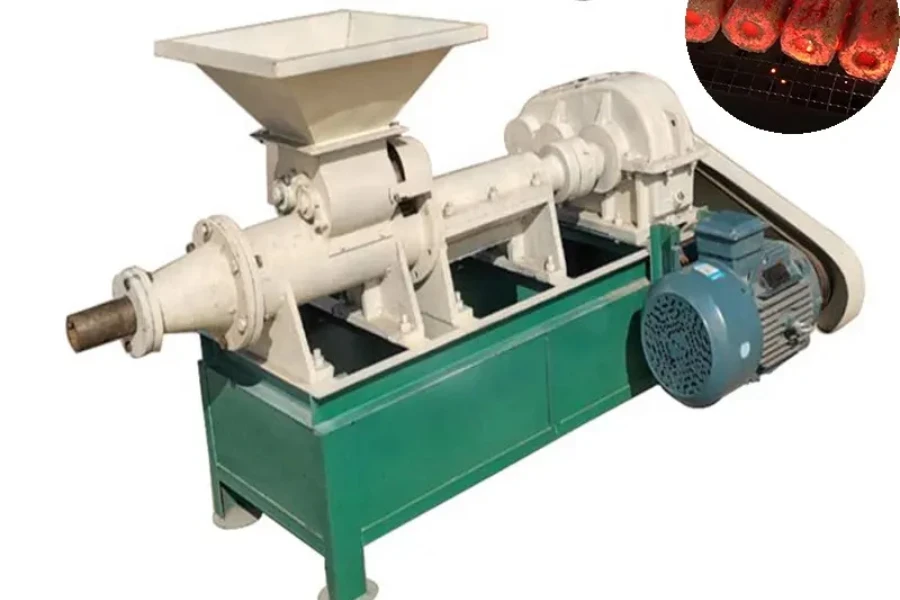
To ensure seamless operations, aligning the machine’s output with production demands is essential. Going too small risks underutilization, potentially hampering efficiency, while selecting a charcoal making machine that exceeds the needs might result in suboptimal outcomes. You establish a harmonious and effective production workflow by gauging the production requirements against the machine’s capabilities.
Traditional charcoal kilns can often produce around 1 to 5 tons of charcoal per batch, retort charcoal kilns typically range from 1 to 10 tons per batch, continuous carbonization furnaces can handle 500 kg to 10 tons per hour depending on size and design, and charcoal briquette machines vary widely but can usually produce 100 to 1000 of briquettes per hour.
2. Price
While considering affordability is prudent, evaluating the potential return on investment throughout the machine’s lifespan is equally imperative. Remember that investing more initially in a charcoal making machine that offers enhanced efficiency and durability can often lead to significant cost savings over time.
The price range for traditional charcoal kilns is between USD 300 and USD 3,000. Retort charcoal kilns begin at approximately USD 5,000, potentially escalating to USD 20,000 or more depending on size and features. Continuous carbonization furnaces fall from about USD 10,000 to USD 30,000, contingent upon capacity and technological intricacies. Charcoal briquette machines exhibit a broader price spectrum, with costs varying widely from USD 3,000 to USD 50,000 or higher,
3. Efficiency
Charcoal-making machines incorporating advanced technologies often showcase heightened efficiency, improving charcoal quality and minimizing waste generation. Despite a potential upfront cost premium, these technologically advanced options merit consideration for their ability to provide more excellent overall value.
Traditional charcoal kilns may have lower efficiency due to longer processing times and less control. Retort charcoal kilns are designed to optimize energy usage and improve output quality. Continuous carbonization furnaces are equipped with sophisticated controls for precise temperature regulation and efficient processing, and charcoal briquette machines, depending on their design, can offer higher efficiency in compressing biomass and charcoal particles into uniform briquettes.
4. Type of raw materials
Considering the diversity of biomass materials, matching the charcoal making machine with the resources available is important. Ensure the machine is adept at processing raw materials like wood chips, sawdust, agricultural waste, or other sources.
For example, traditional charcoal kilns often handle wood logs or branches. Retort charcoal kilns are versatile and can work with various biomass types, including sawdust and agricultural residues. Continuous carbonization furnaces are engineered to accommodate a wide range of biomass materials. Charcoal briquette machines are designed to effectively compress a mixture of charcoal dust, sawdust, and other binders into briquettes of consistent shape and size.
5. Speed
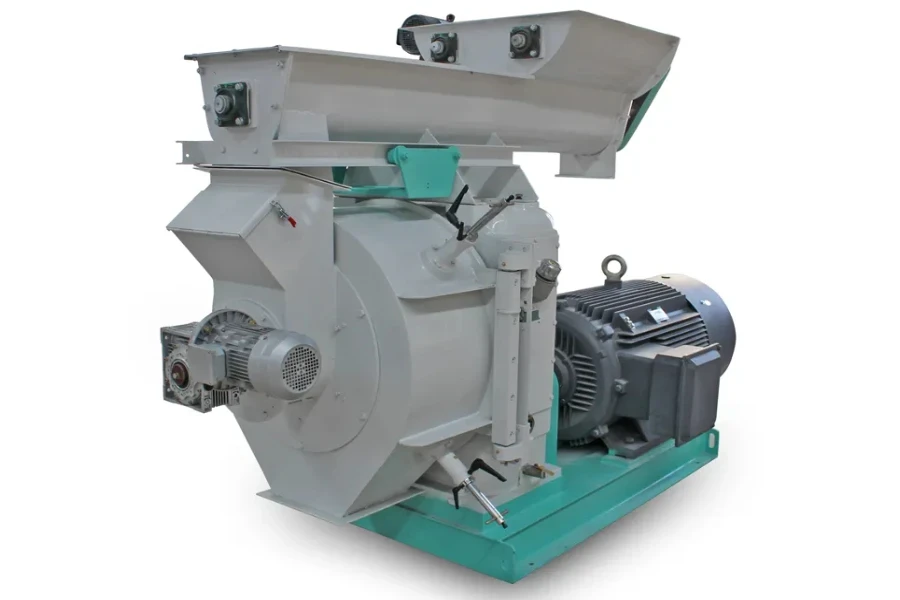
The rate at which a charcoal making machine functions carries significant weight, particularly for commercial ventures. However, striking a balance between speed and the quality of the charcoal is of paramount importance. While prioritizing faster machines aligns with productivity objectives, it is critical not to compromise the integrity of the end product.
To offer a practical sense of speed, traditional charcoal kilns might necessitate days for a batch to finalize, retort charcoal kilns can accelerate the process to a few hours, continuous carbonization furnaces enable ongoing processing ranging from several hours to a full day, and charcoal briquette machines can produce numerous briquettes within a matter of minutes to an hour, contingent upon the specific machine’s design and capacity.
6. Durability
Opting for a robustly built charcoal making machine fashioned from durable materials is akin to an investment in a machine’s extended working life. This longevity is a buffer against unexpected disruptions that stem from potential breakdowns. This emphasis on durability guarantees smoother operations and underscores the long-term viability of a charcoal production enterprise. On average, charcoal making machines can last between 10 to 30 years, depending on maintenance and usage intensity.
Summary
To sum up, delving into charcoal making machines requires thoughtful consideration of multiple essential factors. From capacity and pricing to efficiency, raw materials, speed, quality, and durability, each facet significantly shapes the outcome of any charcoal production venture. Explore a diverse range of options and delve deeper at Alibaba.com.