鋳造業はかけがえのない基盤産業です。 現在、中国には約26,000社の鋳物会社があり、鋳物の年間生産量は世界の総生産量の約半分を占めています。 数ある鋳造法の中でも砂型鋳造は最も一般的な製造方法であり、砂型鋳造で生産された製品は鋳物全体の90%以上を占めています。 しかし、従来の砂型鋳造法には次のような問題がありました。
- 労働集約度は高く、労働環境は厳しく、人手不足、採用困難、定着困難が一般的です。
- 金型の製作コストが高く、サイクルが長いため、多品種・小ロットの生産ニーズに応えることが困難です。
- 複雑な幾何学的形状の金型を製造する場合、密度と精度が低いため、後続の加工の難易度が高くなります。
積層造形技術 (3D プリンティング) は、コンピュータ支援設計により従来の準備プロセスの制約を打ち破り、デジタル モデルに基づく離散/スタッキング原理で部品の 3D モデルを複数の 2D セクションに分割し、スタッキングを通じてセクションを 3D ソリッドに積み重ねます。 。 現在、この技術は砂型鋳造の分野に適用されるのが一般的であり、業界のニーズを正確に満たしています。
- 手作業ではなく、すべての成形工程が比較的密閉された箱の中で行われるため、印刷工程中に粉塵が発生せず、労働環境の改善と重労働の軽減が図られます。
- 金型作成工程を省略することで製造コストを削減できるだけでなく、製品試作のスピードや柔軟性も向上します。
- 製品サイズの精度を向上させ、砂型サイズの制御能力を強化し、企業のハイテク労働者への依存を減らし、製品の品質を向上させることにより、将来的にサイズの問題によって引き起こされる製品の廃棄率が低下するだけでなく、その後の生産効率も向上します。鋳物製品の加工。
航空、宇宙、造船、新エネルギー自動車などの分野では、高性能、高信頼性、低コスト化が進み、部品の高強度化、軽量化、複雑化が進んでいます。積層造形技術は多くの分野に応用されています。
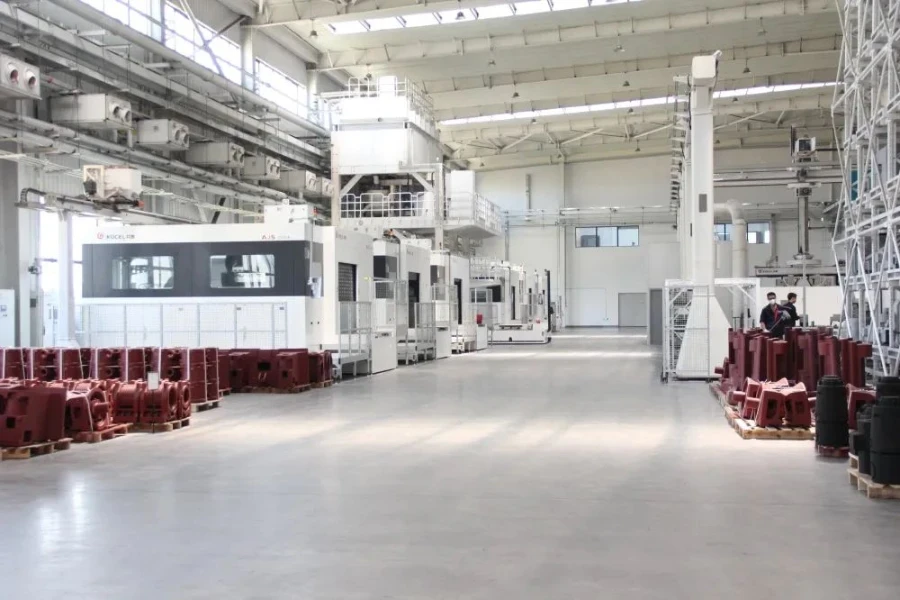
シェアリングインテリジェントイクイップメント株式会社は、シェアリンググループの50年以上の鋳造経験をもとに、3年より鋳造2012Dプリンティングの産業応用研究に注力し始めました。現在までに3種類以上の鋳造品を独自に開発しています。砂型3Dプリンティング設備を導入し、全国XNUMXか所の鋳造XNUMXDプリンティングインテリジェント実証工場を設立しました。 過去 XNUMX 年間の工業生産において、当社のお客様は軍事産業、航空宇宙、エンジン、ロボット、コンプレッサー、その他の分野でサービスを受けてきました。
ここで、同社がサービスを提供するさまざまな業界における典型的なアプリケーション ケースを確認してみましょう。
1. エンジンフライホイールハウジング
製品重量: 50-100kg
製品の難点:本体構造は平面が大きく薄肉(7mm)で部分的に厚みがあり、気泡や保冷不良などの欠陥が生じやすい。
解決策:傾斜注入プロセスと広い平面上の多点排気を採用し、良好な充填を保証します。
3D プリントの納期サイクル: 15 日
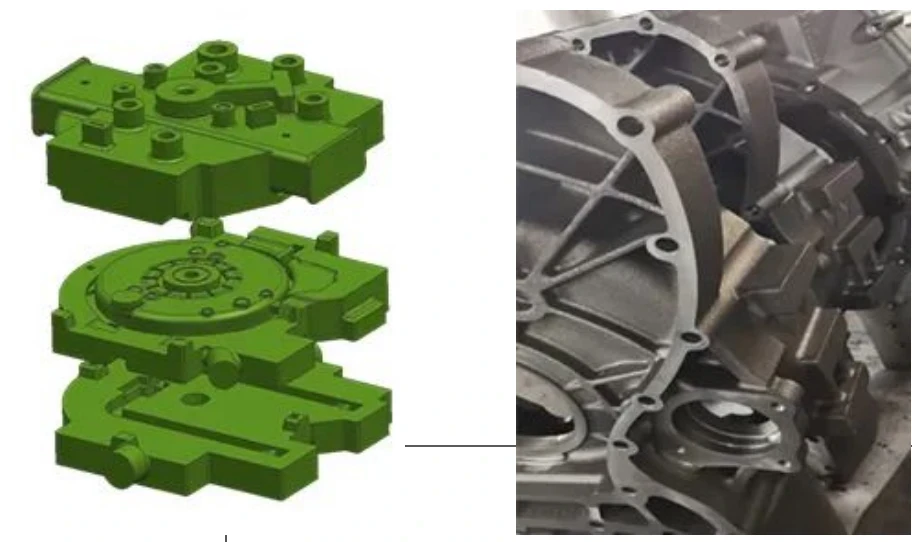
2. スクリューコンプレッサーハウジング
製品重量:約1トン
製品の難点:内部の空洞構造が複雑で、局部構造が厚く縮みや緩みが発生しやすく、穴あけ加工箇所が多い。
解決策: 厚い部品を隔離し、効果的な冷却対策を講じます。 特殊な製錬プロセス(CE4.4~4.5、△T≤3)を採用し、同時凝固を実現します。
金型費用:木型700,000万元
型開きサイクル:50日
3D プリントの納期サイクル: 25 日
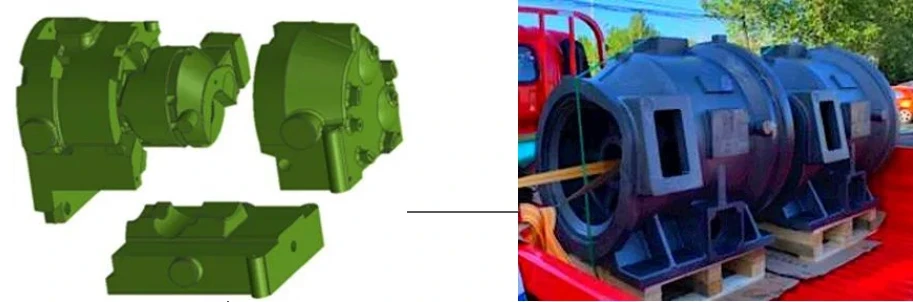
3.多方弁
製品重量: 15-400kg
製品の難易度: 内部流路寸法の高精度要件とドレープなどの欠陥がないこと。 金属組織検査用のボディサンプリング (中心付近)、球状化率 ≥ 90%、グラファイトボール数 ≥ 100
解決策: フロー チャネル コアはコア全体として作成され、寸法精度を確保し、コア アセンブリの継ぎ目などの欠陥を回避し、長期の接種剤と特殊な球状化剤を使用して金属組織学的要件を達成します。
金型費用:金型500,000万元
型開きサイクル:90日
3D プリントの納期サイクル: 15 日
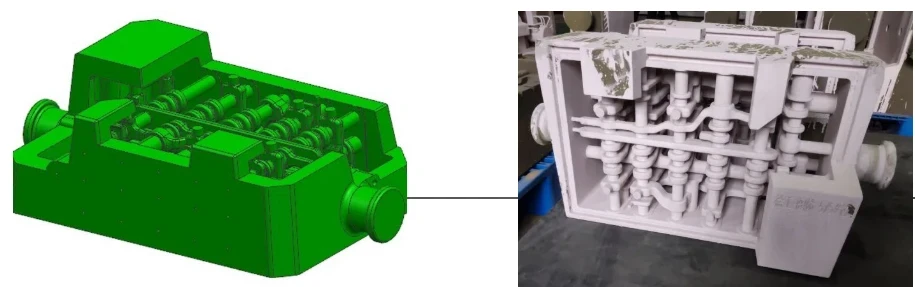
4. 内燃機関
製品重量: 30-2000kg
製品の難易度:製品の構造が特に複雑なため、いかなる溶接修理も認められていません。 コストと型開きの難易度が高く、砂中子のサイズが大きい。
ソリューション: 全体のモデリングに 3D プリンティング フォームを採用し、二重層チューブ、ボディ内腔コア、複雑な内腔構造などの問題を解決します。 最も複雑な製品は、XNUMX つの砂コアに分割するだけで済みます。
コスト削減: 金型コストの 20% ~ 60%
型開きサイクル:3~6ヶ月
3D プリントの納品サイクル: 最初の製品の納品は 25 ~ 30 日以内
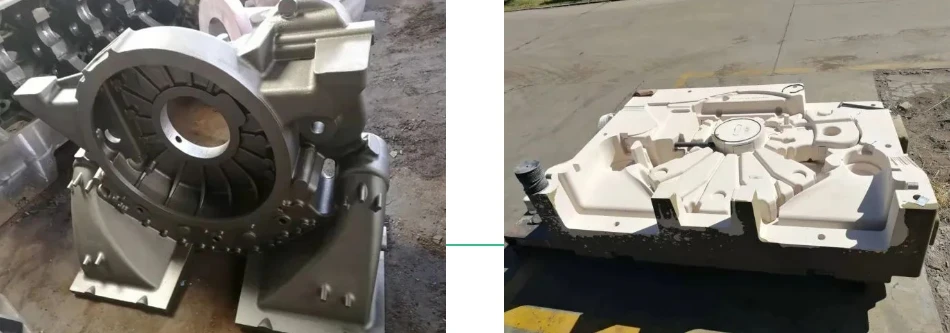
5. アルミニウム合金鋳物
製品重量: 2-60kg
製品の難易度: 内部流路寸法の高精度要件とドレープなどの欠陥がないこと。 複雑な構造、金型成形が難しい
解決策: 複雑さを簡素化し、複数のコアを XNUMX つに接続し、コアのアセンブリを削減し、寸法精度を確保し、コア アセンブリの継ぎ目などの欠陥を回避します。
コスト削減: 金型コストの 20% ~ 60%
型開きサイクル: 20-90 日
3D プリントの納期: 15 ~ 25 日
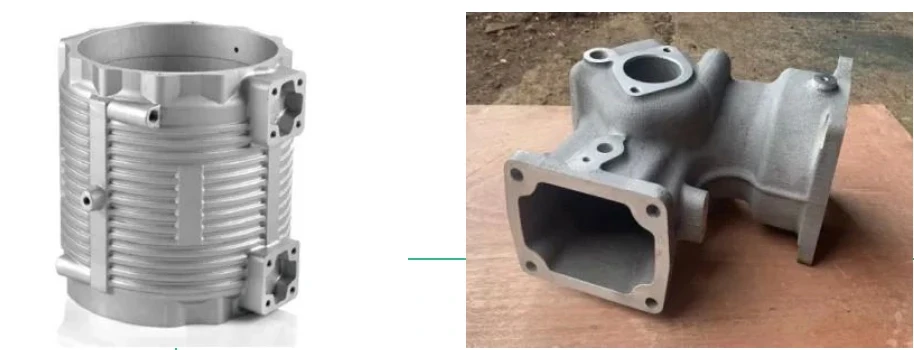
3D プリンティング技術と伝統産業の統合は避けられない傾向となっています。 砂型鋳造の分野でも、3D プリンティング技術は、迅速、環境に優しい、多機能、大規模、複雑、需要の高い部品の開発と生産のための新しい方法を切り開きました。 共有会議は初心を忘れず、鋳造3Dプリンティング技術の産業応用の促進に引き続き注力し、鋳造業界の変革とアップグレードを改善します。
ソースから ofweek.com