Otomotiv sektörü için mevcut trendlere ve tedarik zinciri sorunlarına bir bakış
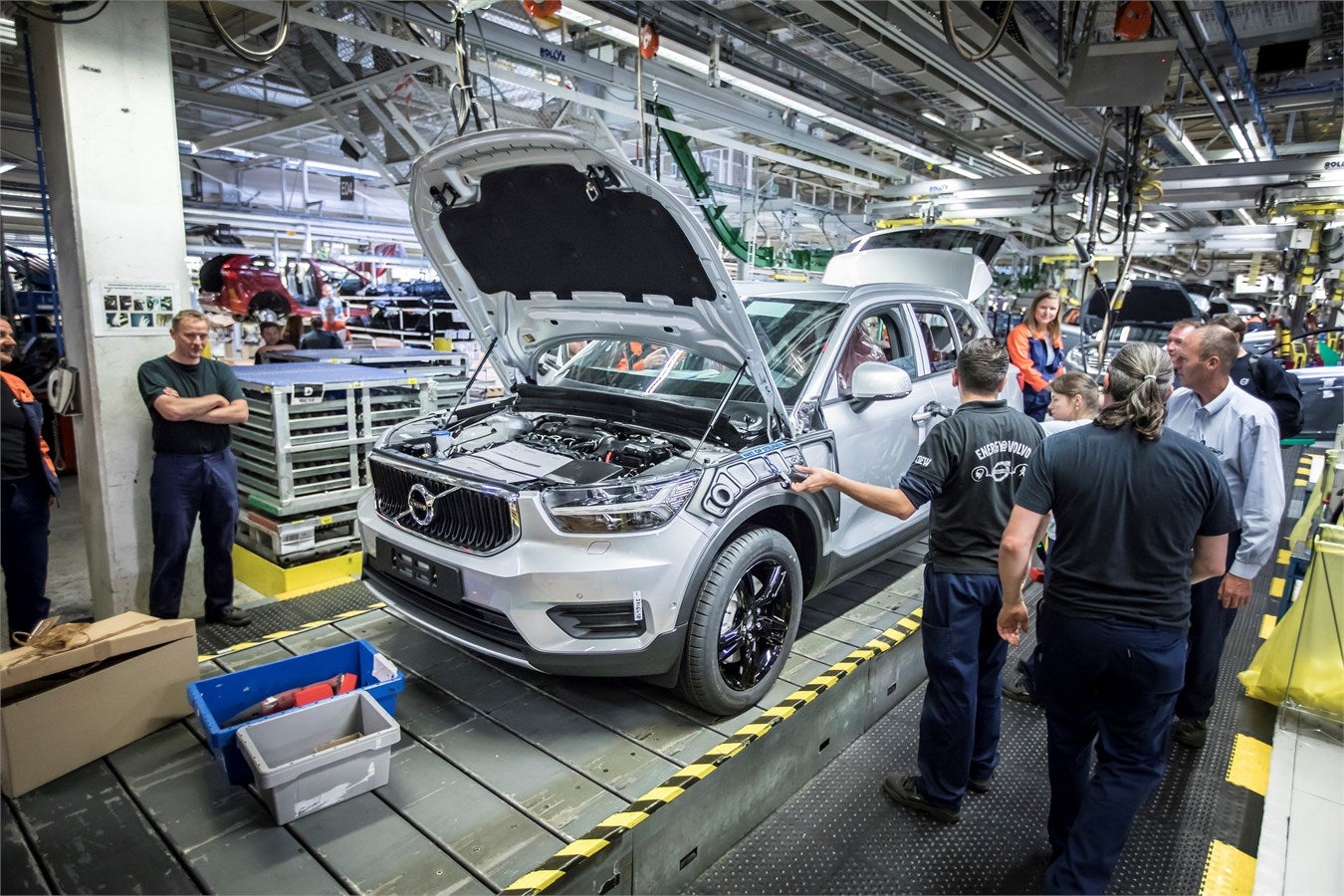
Tipik olmayan bir motorlu araç, nasıl ölçüldüklerine ve ana sistemlerinin tasarım mühendisliğine bağlı olarak 15,000 ile 25,000 arasında bileşen parçası içerebilir. Bu, nihai ürün için bir araya getirilecek ve bütünlük sağlayacak çok fazla malzemedir. Aslında tüm bu parçaları doğru sırayla bir araya getirmek hiç de kolay bir iş değil. Var olan her araba süreç planlamasına, organizasyonuna, üretim mühendisliğine ve üretim lojistiğine bir övgüdür. Bir zamanlar araç üreticileri dikey olarak son derece bütünleşmişti, ancak bu yaklaşım yerini tasfiyelere (Visteon'un nereden geldiğini ve General Motors'un Otomotiv Bileşenleri Grubunu oluşturan karmaşık şirketler ağını hatırlayan var mı?) ve uzman parça tedarikçilerine odaklanabilecek hale getirdi. ürün geliştirme ve birden fazla müşteriye daha yüksek ölçekte daha verimli çalışma.
Büyük 1. Kademe sistem entegratörleri, genellikle araç montaj ve üretim tesislerine yakın elverişli bir konumda bulunan tedarikçi parklarından doğrudan araç üreticilerine tedarik sağlar, ancak en üst kademenin altında, her biri ham maddeden üretime uzanan uzun yolda hayati roller üstlenen çok sayıda küçük tedarikçi kademesi vardır. Bitmiş ürüne malzemeler.
OEM'ler ve daha büyük tedarikçiler, gerekli kalite eşiklerini en düşük maliyetle karşılayan parça ve malzeme girdileri için küresel pazarda alışveriş yapmaya çalıştıklarından, bileşen parçalarının uluslararası tedariki, onlarca yıldır endüstri standardı bir çalışma şekli haline geldi. Nakliye mesafeleri (ve maliyetleri) ve depolama düzenlemeleri de resmin bir parçasıdır, ancak uluslararası yük taşımacılığındaki daha yüksek verimlilik ve teknolojik ilerlemeler, uluslararası parça gönderilerindeki olağanüstü büyümenin temelini oluşturmuştur.
Çin otomobil endüstrisinin son yirmi yıldaki büyümesi, otomotiv bileşenlerinin, özellikle de esas olarak maliyet fiyatına göre satılan evrensel veya ticarileştirilmiş parçalar olarak adlandırılabilecek parçaların küresel olarak tedarik edilmesinde de büyük bir faktör oldu. Çinli tedarikçiler, ölçek ekonomilerini artıran büyük yerel sözleşmelerin yanı sıra OEM ana şirketlerini, devlet kuruluşlarını ve çeşitlendirilmiş hisse senetlerini içeren karmaşık sahiplik yapılarından kaynaklanan gizli sübvansiyonlardan da yararlandı. 2000'li yılların başlarında, özellikle ABD'li araç üreticileri, Asya'dan daha düşük maliyetli parçalar tedarik etmeye yöneldi ve bu süreçte, ABD tedarikçi tabanındaki bazı köklü şirketlerin altını oymaya başladı.
Dünya genelinde, otomotiv ürünlerinde (hem bitmiş araçlar hem de bileşen parçaları) uluslararası ticaret akışı artık çok büyük. Tarafından derlenen tahminler GlobalData'nın Almanya'yı otomotiv endüstrisi ürünlerinin yurtdışına sevkiyatında açık ara dünyanın uluslararası lideri olarak gösteriyor. Bu ihracatlar, ithalat ve üretim sürecinin farklı aşamalarında rafine edilen ve tasarlanan bileşen sistemlerine girdi olarak kullanılan ve uluslararası sınırların ötesine birçok kez gönderilebilen karmaşık bir ara mallar ağıyla yansıtılmaktadır.
Otomotiv endüstrisindeki tedarik zincirlerinin bir diğer önemli yapısal özelliği, gelişmiş kalite standartları için envanter maliyetlerini en aza indiren ve süreç verimliliğini ve geri bildirim iletişim döngülerini geliştiren bir tedarik zinciri yönetimi felsefesinin önemidir. 'Yalın üretim' olarak bilinen bu üretim Toyota ile başlamıştır ve özü, yalın tedarik yöntem ve ilkelerini tanımlayan 'tam zamanında' terimiyle özetlenmiştir. Üretim ve perakende sürecinin tüm parçalarını bir araya getiren dijital ve bağlantılı teknolojilerin yükselişi, son on yılda bu çalışma şekillerini daha da güçlendirdi.
Geçmişte, doğal afetler ve bunların lokasyonlar üzerindeki yoğun etkileri otomotiv şirketlerini etkilemiş ve otomotiv tedarik zincirlerinin kırılganlığını ortaya çıkarmıştı. Japonya'da 2011 depremi ve tsunamisinden sonra birkaç dikkate değer aksaklık örneği yaşandı. Küresel bir birinci sınıf otomobil üreticisi, tedarik veya kırmızı boya pigmentinin tek kaynak olarak Japonya'dan temin edilmesi konusunda sorunlar yaşadı. Aynı yılın sonlarında Tayland'da meydana gelen sel felaketleri, araç bilgi ekranları için LCD ekran tedarikinde sıkıntıya neden oldu. OEM'ler ve bayiler buna göre eksikliklere uyum sağlamak zorunda kaldı. Ukrayna'daki savaş, beklenmedik jeopolitik olayların tedarik zincirlerini de nasıl bozabileceğini gösteriyor.
Yarı iletkenlerin mücadelesi
Tüm şirketler, 2020'deki halk sağlığı krizinden doğrudan ve küresel tedarik zincirleri üzerindeki daha birçok etkiden dolaylı olarak olumsuz etkilendi. Üstelik 2021'deki küresel satışlardaki toparlanma, bir yıl önceki Kovid krizinin öngörülemeyen sonucu nedeniyle ciddi şekilde sekteye uğradı. Araç üreticileri, 2020'de hükümet emriyle fabrikaları kapatıp parça siparişlerini büyük ölçüde azalttıkça, yarı iletken üreticileri tüketici elektroniği gibi alanlarda alternatif iş imkanları buldu.
İyileşen otomotiv fabrikaları 2021'in ilk çeyreğinde çip siparişlerini artırırken, tedarik sıkıntısı sorunu hızla ortaya çıktı.
Talaş dökümhanesi kapasitesinin yukarı yönde eklenmesinde uzun teslim süreleri nedeniyle yarı iletken kıtlığının üstesinden kolaylıkla gelinemeyecekti. Güvenlik açısından kritik olan veya bitmiş ürün için başka bir şekilde gerekli görülen bir parçanın bulunmaması, bazı model hatlarının diğerlerinden daha ciddi şekilde etkilendiği anlamına geliyordu. Araç üreticileri bazı durumlarda pazar karışımını karıştırabiliyordu ancak eski bir atasözü yeniden doğrulanıyordu: Tedarik zincirleri yalnızca en zayıf noktaları kadar iyi/sağlamdır.
Sektör genelinde satın alma yöntemleri ve süreçleri daha önce hiç olmadığı kadar inceleniyor.
Ayrıca, bazı yarı iletken tedarik baskılarının gelecekte de bir risk olmaya devam edeceği anlamına gelen yapısal bir unsurun iş başında olduğunu belirtmekte fayda var: Araçların gelişmiş elektronik içeriği, daha karmaşık teknolojik özelliklerin giderek artan donanımı nedeniyle artıyor. Bu, bazı şirketlerin çip üreticileriyle stratejik ittifaklara yönelmesine neden oluyor. Bu, yalnızca kritik mikroişlemcilerin gelecekteki tedariklerinin güvence altına alınmasına yardımcı olmakla kalmaz, aynı zamanda stratejik açıdan değerli bir bileşen alanı olduğu açıkça ortaya çıkan gelecekte yararlı işbirliğine dayalı ürün geliştirme ilişkilerini de kolaylaştırabilir.
Tedarik zincirleri üzerindeki diğer baskılar, öngörülemeyen işgücü kıtlığı ve enerji fiyatlarının artmasıyla birlikte çok daha yüksek uluslararası konteyner nakliye fiyatları gibi diğer kaynaklardan geldi.
Çoklu kaynak kullanımına karşı ikili kaynak tartışması
Otomotiv tedarik zincirlerindeki kırılganlık, çoklu katmanların yaygınlığı, uluslararası kaynak bulma akışları ve küresel araç programlarında ölçek ekonomilerini en üst düzeye çıkarmak için tek kaynak kullanımı eğilimi ile birlikte geliyor. Çoğu durumda, bu geleneksel yapı aynı zamanda tedarik katmanlarında tercih edilen ortaklar kültürüne de yerleşmiş ve kökleşmiştir. Avantajlar arasında, maliyetlerin diğer model ve sistemlerdeki hacimlere yayılmasıyla birlikte paylaşılan sistemler ve lojistik maliyetleri de yer alabilir.
Şirketler - 3. ve 4. kademedekiler de dahil olmak üzere - genellikle uzmanlığı ve yatırımı yüksek hacimli üretime ayrılmış tek bir tesiste merkezileştirebildikleri için teknoloji, tek kaynak kullanımının teşvik edilmesinde de rol oynadı. Sorunlar, Schuppers'ın planladığı bir şeyler ters gittiğinde ortaya çıkar (örneğin geçen yıl Renesas mikroişlemci fabrikasında çıkan yangın).
Elektronik parçalar ve sensörler, yukarı yönde herhangi bir kesinti olması durumunda araç imalatında aşağı yönde büyük etkileri olabilecek alt montajlar için kritik bileşenlerin örnekleridir. Çok kısa sürede yedek kapasiteye sahip alternatif tedarikçiler bulmak büyük bir zorluktur.
Bazı yedek parçaları stoklarda tutmak bir maliyet getirir ve yalın üretimin yol gösterici ilkelerine aykırıdır. Elbette, herhangi bir aykırı aksaklık maliyetini ortaya çıktıkça absorbe etme veya silme kararı alınabilir; bu, sonuçta risk değerlendirmesinin niceliğine bağlıdır.
Son yıllardaki deneyimler, en azından şirketlerin tek kaynak kullanımının eskisi kadar arzu edilir olup olmadığı sorusunu giderek daha fazla sorduğuna işaret ediyor. Daha yüksek riskler ve belirsizliklerle kuşatılmış bir dünya belki de yaklaşımda bir sıfırlamayı gerektirebilir. Tedarik zinciri içinde çoğaltma, bir rakiple paylaşmaya yaklaşmak anlamına gelse bile, tek kaynak kullanımından en azından bazı bileşenler için daha iyi bir çözüm sunabilir. Daha fazla ürün güvenliği, ikili kaynak kullanımının avantajı olacaktır. Her zamanki gibi bu bir genel maliyet meselesi.
Elektrifikasyon ve yeni tedarik zinciri modelleri
Elektrifikasyon, otomotiv sektörünün gelecekteki tedarik zincirlerine yeni zorluklar getiriyor. OEM'ler, çözmeye çalıştıkları yeni ve temel bileşenlerin (en önemlisi güç aktarım sistemi aküleri) tedariki konusunda önemli belirsizliklerle karşı karşıya kaldı. Gelecekteki riskleri azaltmak ve tedarik düzenlemelerinin ticari yönleri üzerinde kontrol uygulamak için arzu edilen dikey entegrasyonun derecesi konusunda da stratejik sorular vardır. Akü uzmanlarıyla ortak girişimler kuruldu. Elektrikli araçlara yönelik motorlar, tahrik sistemi parçaları, yüksek gerilim invertörleri gibi diğer temel bileşenler de tedarik zinciri hususlarının yanı sıra artan yatırımlara tabi olacaktır.
İddialı elektrifikasyon stratejileri, lityum iyon pil hücrelerine olan talebin hızla artmasını sağlayacak. Dünyanın dört bir yanındaki pil üreticileri, otomobil üreticilerine hücre tedarik etmek için yeni 'gigafabrikalar' açarak milyarlarca dolarlık genişleme stratejilerine bağlı kalıyor.
Bu alanda derin OEM-Kademe 1 işbirliğinin dikkate değer bir örneği, Volkswagen ile Bosch arasında bir Mutabakat Zaptı imzalanmasıyla sağlanmıştır. İki şirket, pil hücresi ve pil sistemi üreticilerine entegre pil üretim sistemleri, yerinde geliştirme ve bakım desteği sağlamayı planlıyor. Endüstriyel ölçekli pil teknolojisinde maliyet ve teknoloji liderliğini ve 'sürdürülebilir, son teknoloji pillerin' hacimli üretimini hedeflediklerini söylüyorlar.
Yalnızca Avrupa'da, Volkswagen Grubu 2030 yılına kadar altı hücre fabrikası kurmayı planlıyor ve diğer üreticiler gelecekteki hücre ve pil paketi tedarikini güvence altına almak için benzer adımlar atıyor. Bölgenin 700 yılına kadar yıllık toplam pil paketi kapasitesinin yaklaşık 2030 gigawatt saat olması bekleniyor.
İleriye bakıldığında Toyota, Panasonic (Prime Planet Energy & Solutions - PPES) ile bir ortak girişim kurdu ve bu şirket, çoğu lityum iyonun katotunda bulunan nikelin temeli olan nikel sülfatın gelecekteki tedariği için madencilik devi BHP ile bir anlaşma imzaladı. pil hücreleri. Tesla ayrıca BHP ile de benzer bir anlaşma imzaladı; bu, gelecekteki tedarik güvenliği açısından hammaddelerin de önemli bir rol oynadığını gösteriyor.
Bu anlaşmalar, otomotiv oyuncularının, 2019'da piyasaya sürülecek yeni akülü EV dalgası için lityum iyon akü sektöründe ihtiyaç duyulan muazzam kapasite artışını sağlamak için yeterli hammaddeye erişime sahip olmalarını sağlamak amacıyla akü tedarik zincirini daha yukarılara bakma ihtiyacını vurguluyor. gelecek yıllar. Geri dönüşüm, yapılan birçok anlaşmada da önemli bir husustur.
Tedarik zinciri görünürlüğü için Blockchain
Otomotiv şirketleri, CO2 emisyonları ve piller için kobalt kaynağı (değerli minerallerin madenciliğini çevreleyen etik soruları da beraberinde getirebilen) gibi tedarik zinciri konularında şeffaflık kazanmak için blockchain teknolojisini giderek daha fazla kullanıyor.
Orijinal blockchain konsepti, adından da anlaşılacağı gibi, zaman damgalı bloklar veya kayıtlardan oluşan bir zincirdir (blok = dijital bilgi; zincir = genel/topluluk veritabanı). İşlemlerle ilgili bilgilerin saklanmasını engeller. Bir blok yeni veri (bir işlem) depoladığında, blok zincirine eklenir ve eşler arası bilgisayar ağı tarafından doğrulandıktan sonra bunu herkes görebilir (veya özel bir ağın iznine tabi olabilir). bir OEM'in tedarik zinciri – 'dağıtılmış defter').
Ancak tüm taraflar yalnızca görme iznine sahip oldukları bilgilere erişebilir. Blockchain ağındaki her bilgisayarın kendi blockchain kopyası vardır. Ancak prensipte fikir, iki taraf arasında sıfır işlem maliyetiyle bir blok oluşturarak oldukça şeffaf bir sistem oluşturmaktır.
Daha fazla otomotiv şirketinin, tedarik zinciri 'kırılmaları' riskini azaltmak ve zincir boyunca güçlü ve zayıf yönleri anlamak için bir araç olarak, özellikle de dağıtılmış defter (yani özel ağ) tipinde blockchain süreçlerini benimsediğini görmeyi bekleyebiliriz. Sürdürülebilirlik gibi düzenleyici alanlarda artan uyumluluk taleplerini göstermenin bir yolu.
Toyota'dan dersler
Toyota, tedarik zinciri yönetimi söz konusu olduğunda genellikle otomotiv endüstrisinin en iyi performans gösterenlerinden biri olarak görülüyor. Daha sonra çoğu OEM ve büyük tedarikçi tarafından benimsenen yaygın en iyi uygulama haline gelen yalın üretim yöntemlerinin yaratıcısı olmasının yanı sıra, risk azaltma önlemleriyle ilgili olarak değişen koşullara göre sistemlerini ve süreçlerini de geliştirmiştir. Ayrıca acil durumlar karşısında zaman zaman tedarikçileriyle çok yakın ve daha geniş sektör amaçları doğrultusunda çalışmıştır.
2011'deki Kyoto depremi ve tsunamisinden sonra Toyota, Japonya'nın imalat sektörünü desteklemek amacıyla kapsamlı bir tedarik zinciri bilgileri veri tabanı oluşturmak için Japonya'daki tedarikçilerle birlikte çalıştı. Toyota ayrıca, üç farklı kaynaktan tedarikin organize edilmesi anlamına gelen, anahtar parçaların birden fazla kaynaktan temini için bir strateji başlattı; ancak ana tedarikçi, ölçek ekonomilerini sağlamak için siparişin neredeyse üçte ikisini yapmaya yönelikti. Birden fazla tedarikçi ölçek ekonomilerinden ödün verir, ancak bu aynı zamanda gerektiğinde alternatiflerin mevcut olduğu anlamına da gelir.
Toyota ayrıca geniş tedarikçi ağını izlemek için iyi geliştirilmiş bir sisteme ve eksiklikler için erken uyarı sistemine sahiptir. Aslında bazı şirketler tedarik zincirlerindeki gelişmeleri değerlendirmek için yapay zekaya yöneliyor; ancak bunun için öncelikle güvenilir, kapsamlı ve ayrıntılı bir veri tabanına sahip olunması gerekiyor.
Şirketler için diğer bir seçenek de, özellikle üretim hattının durmasına neden olabilecek önemli parçalar için acil durum stokları veya tampon stokları tutmaya başlamaktır. Yine, depolama veya depolamada ekstra maliyet gerektirir, ancak bu, hangi düzeyde maliyetin veya 'sigorta priminin' ödemeye değer olduğuna karar verme meselesidir. Ayrıca kalıcı bir çözüm olmayacaktır. Toyota bazı yarı iletkenleri stoklamış olabilir, ancak küresel çip kıtlığının ciddiyeti, sonunda onun da üretimi azaltmak zorunda kalması anlamına geliyordu. Belki de Toyota'dan öğrenilen en önemli şey, sürekli gözden geçirme ve değişen koşullara ve belirsizliklere uyum sağlama ihtiyacıdır.
Kaynaktan Sadece Otomatik
Yasal Uyarı: Yukarıda belirtilen bilgiler Alibaba.com'dan bağımsız olarak just-auto.com tarafından sağlanmaktadır. Alibaba.com, satıcının ve ürünlerin kalitesi ve güvenilirliği konusunda hiçbir beyan ve garanti vermez.