Warehousing is a critical part of a company’s supply chain process, primarily for storing products for different lengths of time, and for transferring products between the manufacturer and consumer. This article explains the different types of warehousing, and what is involved in warehouse management and operations.
Table of Contents
The basics of warehousing
Warehouse management
Warehouse operations
Warehouse management systems
All about warehousing: key considerations
The basics of warehousing
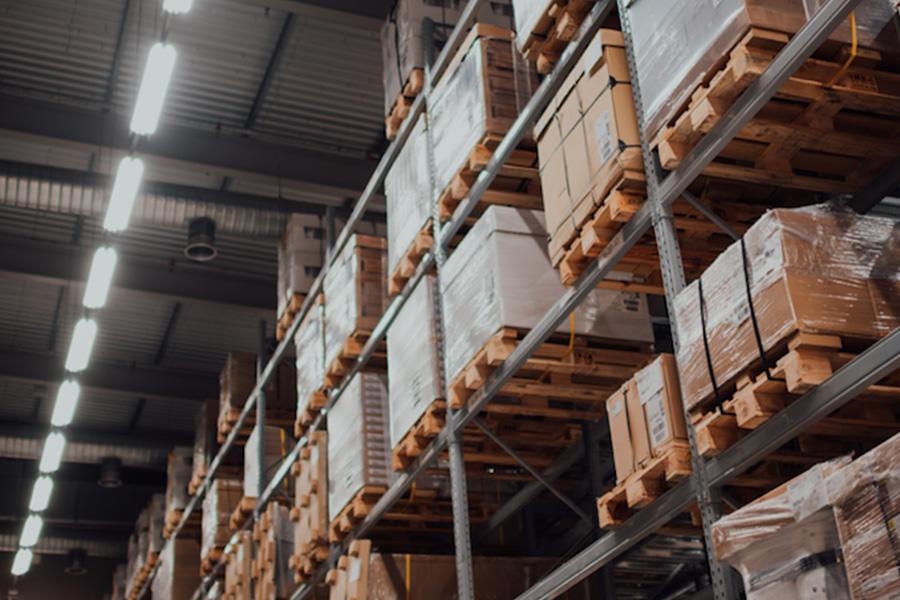
Warehouses store physical inventory that is part of any buyer or seller’s supply chain. As such, they are usually located where there is easy trucking access, and proximity to airports, ports, rail or road networks.
They have facilities and equipment to load and unload trucks easily, and to move those goods to or from storage racks. Fork lift trucks move the goods on standard size pallets. In addition, Warehouse Management Systems (WMS) are used to manage inventory, plan capacity, and to record stock in and stock out.
Warehouses are used by:
- manufacturers to store products
- importers and exporters as part of the shipping process
- customs authorities as part of the clearance process
- logistics companies as part of a service offering
- wholesalers and distributors
- e-commerce providers as fulfillment centers
Warehousing for manufacturers
Manufacturers need warehousing to store their products for a short time, but their objective is to sell and move the products quickly. There may be production and stock surpluses, or unsold items, that require long term storage.
Warehousing as part of the shipment cycle
Shipping companies have dedicated or shared warehouses to hold shipments temporarily at origin or destination. Once a shipment has been picked up from the manufacturers warehouse, it may be held in the warehouse while waiting for a carrier, or to be consolidated with other shipments. On arrival at the destination port, goods may be held temporarily by the receiving cargo agent in their own warehouse, while awaiting delivery instructions or duty payment from the shipper.
Warehousing as part of the customs clearance process
Once a shipment arrives at the destination port, if the goods have not cleared customs, they may be held at a bonded warehouse until cleared. Approved companies are allowed to store imported dutiable goods for a period of time in a designated area, licensed by customs, with duty and taxes suspended. This designated area is termed as a bonded, or licensed warehouse.
Warehousing as part of a logistics service offering
When warehousing is offered as a logistics service, a logistics provider such as an air express company provides an integrated service of warehousing and transportation that can be scaled to the customer’s needs. Logistics providers can then offer value-added services within a production supply chain to ship raw materials or replacement parts.
Warehousing for wholesalers and distributors
A distribution center is a warehouse that is usually within a manufacturer’s or retailer’s supply chain that holds inventory for regional distribution and onward sales. In this way, a manufacturer can hold customer-specific inventory items closer to their end customer for prompt delivery and retail restocking. Distribution centers can be managed by the manufacturer or outsourced to a third party.
E-commerce warehousing and fulfillment centers
A fulfillment center is a warehouse used by any retailer or seller that has an e-commerce storefront. The fulfillment center is usually outsourced to a third-party logistics provider (3PL warehousing). The retailer or seller will purchase products wholesale and store them in the fulfillment center until e-commerce customer orders come in for individual products. The fulfillment center manages the seller’s inventory, picks and packs the items, and ships the orders directly to the end customer.
Warehouse management
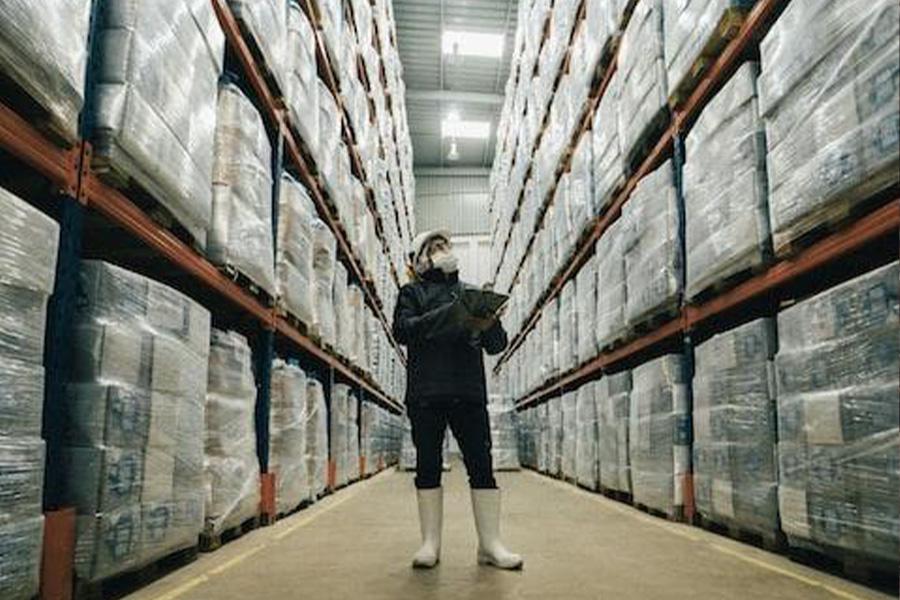
Warehouse management includes organizing warehouse space, scheduling labor, managing inventory and fulfilling orders. Effective warehouse management involves integrating and optimizing all aspects of warehouse operations to increase productivity and keep costs low.
Managing shipment volume
Warehouse space is limited; therefore, it is important to manage inventory levels and shipment volumes. At the heart of managing volume is good planning, and a warehouse management system can be of help. Some inventory may be stored temporarily and others for long durations, so picking strategy is important in rotating inventory, for example, in using FIFO or LIFO (first-in-first-out, last-in-first-out).
Labor management
Labor management in the warehouse includes scheduling and planning of shifts and teams. Staff need training to operate systems, and to be a motivated part of the overall fulfillment process to reduce picking, packing and shipping errors.
Regulatory compliance
Warehouse regulatory compliance includes both warehouse safety procedures, and industrial compliance regulations. These might include safe handling of hazardous materials, foodstuffs, and high value inventory. Compliance can also include safe lifting training, forklift operation, and fire and safety procedures.
Security processes
It is important to operate a secure warehouse environment, internally and externally, to minimize loss of inventory. External warehouse security systems deter theft, while internal warehouse security systems would help to prevent theft in the event of any external breaches. Security systems include security cameras, staff IDs, inventory tracking systems, alarm systems, and door and window access controls.
Warehouse operations
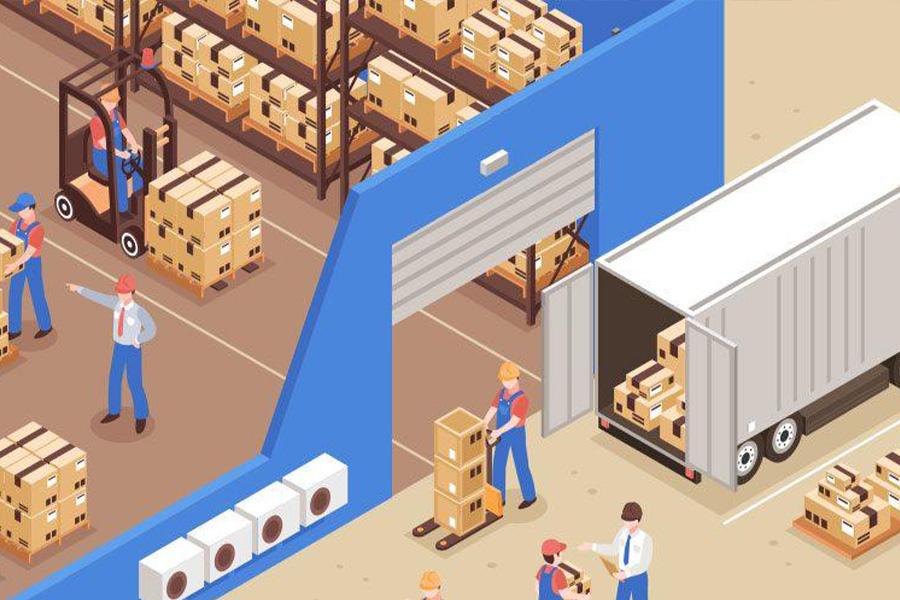
Warehouse operations cover a number of key activities in the planning and operation of warehouse functions. These include space utilization and capacity planning, storage systems and inventory optimization, equipment operation and maintenance, labor usage, and customer management.
Warehouse capacity planning
This planning factors in both storage capacity and working capacity. Storage capacity is the amount of available space for holding inventory, whereas working capacity is the amount of available space for packing, shipment preparation, and moving.
Storage and inventory optimization
Optimizing warehouse storage and inventory involves integrating infrastructure, equipment, and labeling, into inventory management. An efficient racking system is advisable that makes optimal use of floor and vertical space. Access equipment will include pallets and forklifts or automation systems. Labeling and tracking systems typically use barcodes or RIFD tags.
Warehouse automation
With the increasing use of robotics and technology in warehousing, there are many options available to automate stock movement, racking, picking, and restocking.
Warehouse equipment maintenance
Regular maintenance of warehouse equipment is essential to keep operations running. Forklifts need to be maintained, trolleys and elevators kept working smoothly, and any automation systems checked and serviced.
Customer management
With the rise of e-commerce and the link to fulfillment centers, consumers are accustomed to rapid product picking and shorter shipping times. A warehouse’s internal processes and efficiencies have become quite important to customer satisfaction, so customer experience and feedback becomes part of the optimization process.
Warehouse management systems

A warehouse management system (WMS) is software used to manage all aspects of warehouse operations, such as inventory management including replenishment, picking and packing, shipping, and warehouse management including capacity planning, workflow efficiencies and statistical analysis.
Why use WMS software?
One of the most important reasons for using a WMS is for warehouse inventory management. It is important to know what stock is currently in the warehouse, what stock is low or has run out, and where in the warehouse to find that stock. A good system also connects to the retail or e-commerce shopfront to show available stock for the customer to see.
A good WMS also will provide real-time analysis into every aspect of warehouse operations, including receiving and shipping, inventory and order fulfillment, capacity planning and labor usage, and operating costs.
The benefits of WMS automation
A WMS is essential for a warehouse to run efficiently and to track goods from truck to shelf, and from shelf to truck. Most importantly, a WMS brings together all aspects of the product supply chain, and can be used to manage KPIs and to streamline the warehouse processes under one platform.
All about warehousing: key considerations
Warehousing goods is an important part of the overall supply chain process. There are several points along the supply chain where goods need to be held and stored for different lengths of time, and each type of warehousing has different requirements in fulfilling customer satisfaction and requirements. E-commerce has created a need for fulfillment center operations to be more efficient in order to cater to customer shipping demands.
To have successful supply chain operations, it is essential to learn all about warehousing best practices. This way you can guarantee efficient inventory management and timely order fulfillment.
Whatever the type of warehouse, efficient planning and management of inventory is essential, as is optimized storage and capacity planning. Business and capacity growth are also important to ensure that the warehouse capacity is not overwhelmed. Warehouse management systems are key to overall management, and strategy planning.
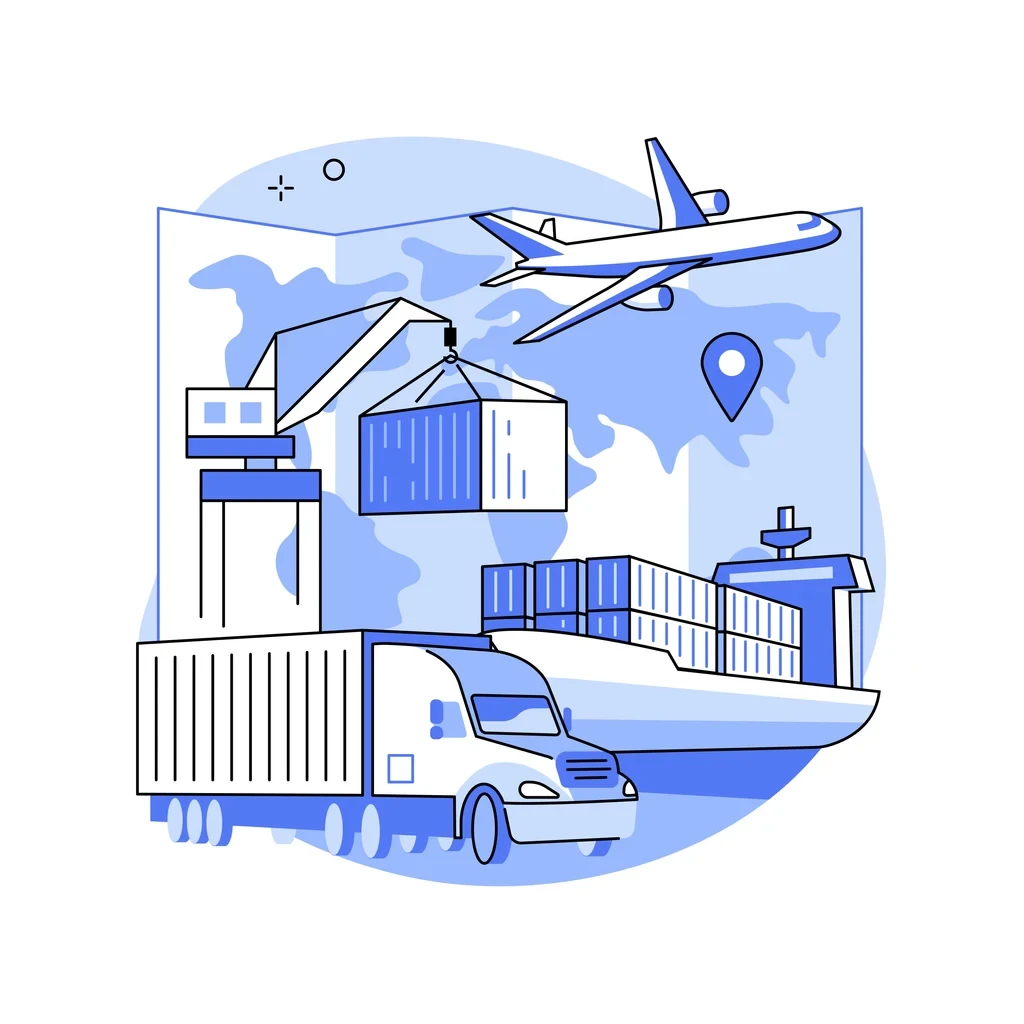
Looking for a logistics solution with competitive pricing, full visibility, and readily accessible customer support? Check out the Alibaba.com Logistics Marketplace today.