Napoleon Hill famously defined a goal as “a dream with a deadline.” This maxim highlights the importance of deadlines in achieving goals, particularly in terms of ecommerce, where customer satisfaction highly relies on timely delivery and the unboxing experience. Meeting delivery deadlines is vital for ensuring customer delight and gaining brand loyalty from them.
To learn more about how order slotting and scheduling contribute to meeting delivery deadlines, continue reading to understand the definitions of order slotting and scheduling, their roles in the delivery processes, and the technology that enhances their efficiency. Also, explore further the common challenges in order slotting and scheduling and the suggested solutions to overcome them.
Table of Contents
Order slotting and scheduling essentials
Optimizing processes for punctual deliveries
Leveraging technology for efficiency
Overcoming common challenges
Timelines optimized
Order slotting and scheduling essentials
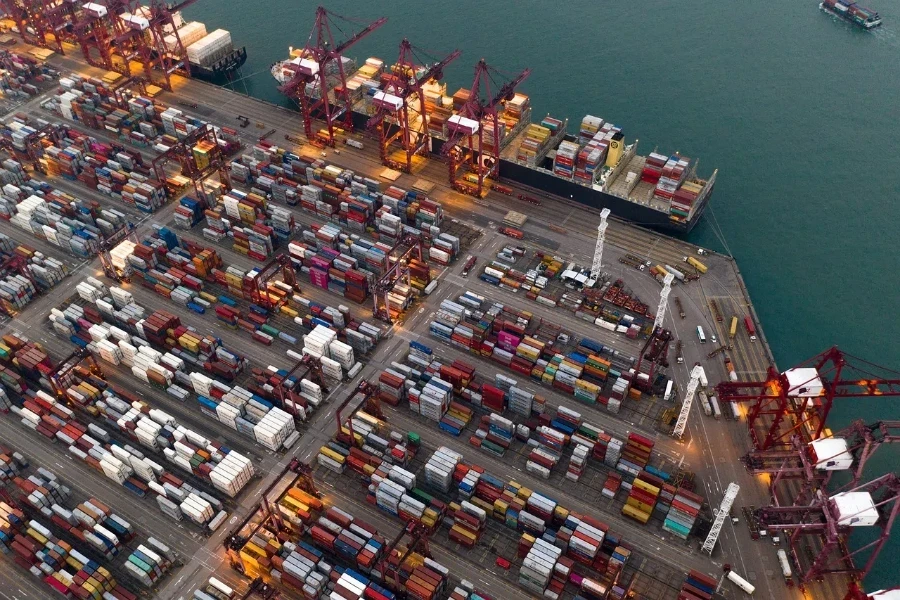
Adding to the ever-growing list of “smart” items, order slotting and scheduling nowadays represent another smart process, assigning orders based on multiple thorough considerations. These include delivery deadlines, and resource and transportation availability, all carefully planned and optimized via advanced tech features such as real-time data integration, predictive analytics, automated systems, and software.
Such efficient strategic organization and precise timing of order fulfillment in logistics and supply chain management aim to ensure timely deliveries by optimizing warehouse operations and improving fulfillment speed.
More importantly, it’s worth noting that since order slotting and scheduling is essentially a systemized process, it can be encapsulated in various forms under different terms, including “delivery slot management,” “warehouse time slotting,” or even “load planning tools,” all named depending on the specific focus and application.
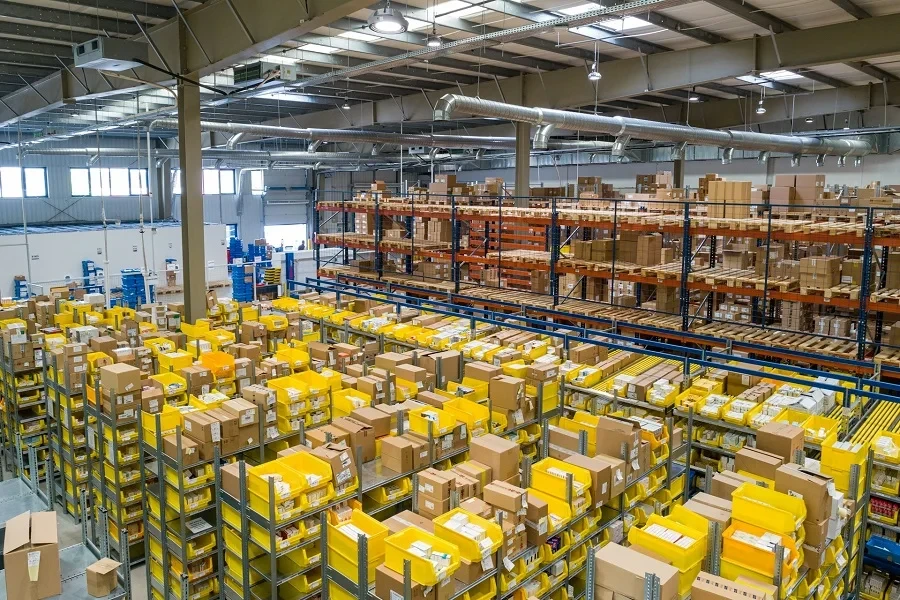
More often than not, these common forms and alternative names of order slotting and scheduling are standalone software solutions specifically designed for such purposes. They are especially useful to companies that require specialized tools tailored to their unique operational needs or smaller businesses that are not considering a full suite of supply chain management features but prefer more focused, cost-effective solutions.
And of course, the order slotting and scheduling functions can also be integrated into larger, more comprehensive solutions such as Transportation Management Systems (TMS) or Warehouse Management Systems (WMS), which will be discussed further in the next section of this article.
In the meantime, while there are numerous benefits of order slotting and scheduling, the most obvious benefit related to meeting delivery deadlines is the enhanced reliability in timely delivery and the reduced likelihood of failed deliveries, which hence increases the rate of successful deliveries on the first attempt. The most direct impact of these benefits on consumers is improved customer satisfaction due to reliable, on-time deliveries and well-coordinated order handling.
Optimizing processes for punctual deliveries
Order slotting optimization methods
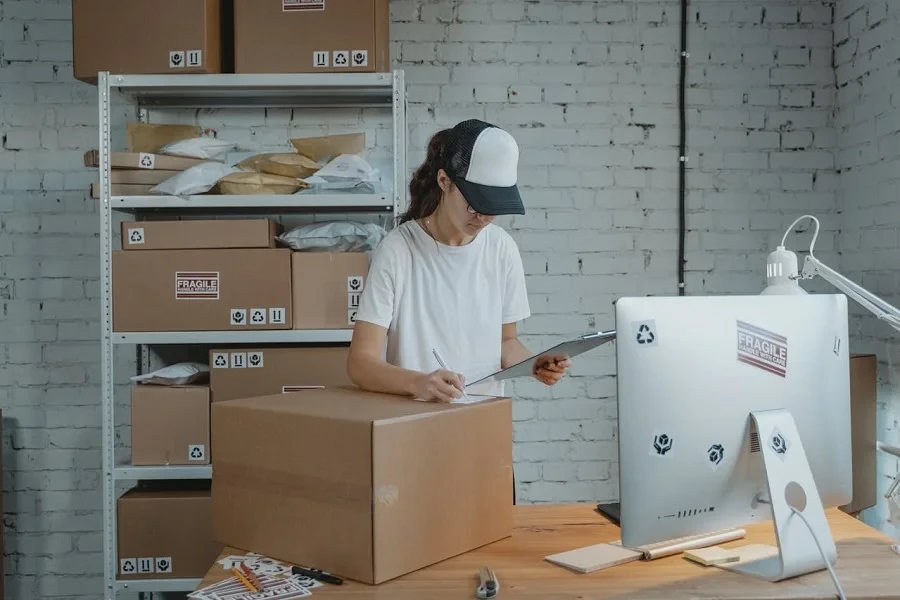
When it comes to the optimization of order slotting, accurate, real-time data is the most powerful asset in managing and refining scheduling practices. Basically, instant reliable data is able to provide insights into current operations, which also allows for immediate adjustments and any future needs forecasts. Furthermore, by utilizing and analyzing data from operations and delivery slot management, predictive planning on resources can be implemented. Such a data-driven management and adjustment approach is the key to initiating and continually enhancing order operations, solidifying the foundation of order slotting to meet delivery deadlines.
Aside from a data-driven strategy, continually adjusting the slotting through regular updates and assessments of the supply chain to identify bottlenecks or areas for improvement is another effective method to better meet operational demands. Various critical criteria in order slotting, including delivery deadlines and resource availability, should also be continuously updated to ensure efficiency.
In any case, while regular updates and adjustments backed by a data-driven approach are helpful in improving order slotting to meet delivery deadlines, adopting a proactive order slotting strategy is what truly drives the continuous advancement in meeting the growing demands of customers.
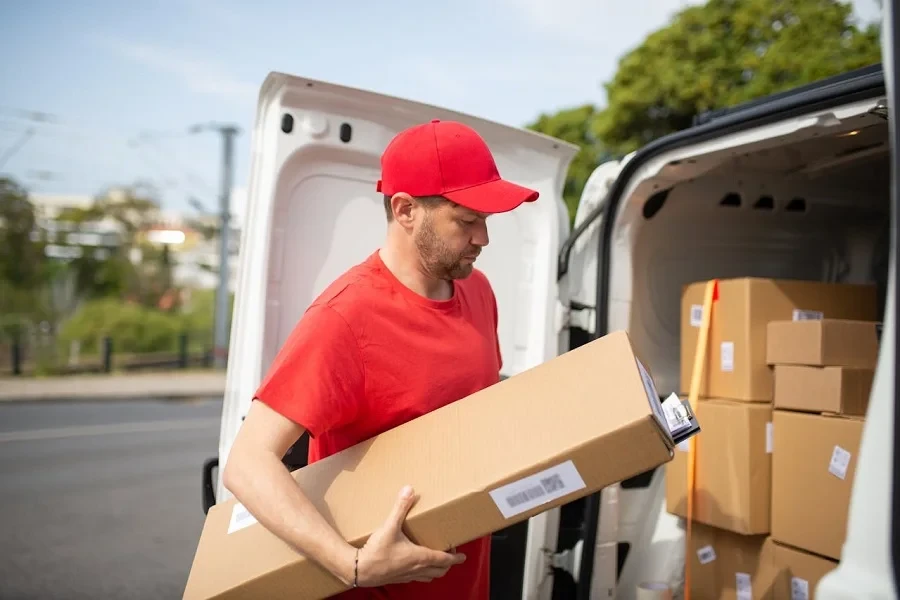
Planning beforehand for advance booking of available delivery slots, for example, is a clear illustration of a proactive slotting method, which helps secure necessary resources well in advance, cutting back on any potential last-minute issues and disruptions. Advance booking is also expected to gain significant cost savings, as it provides better optimization and arrangement of transportation and storage resources.
Another example of proactive slotting is the implementation of predefined order slots, which are determined by businesses based on operational efficiency. This method provides a balanced workload that optimizes production schedules while reducing lead times at the same time. Customers can then choose among these predefined slots based on their convenience. In other words, these predefined order slots can be integrated with preferred delivery slots for customers. For instance, an ecommerce company might have predefined order slots for delivery while also allowing customers to select preferred delivery slots among these timings.
Effective scheduling techniques

Among all the effective scheduling techniques, the prioritization approach is probably the most common and easiest method to be identified, since this approach essentially aligns with the business focus of the company. For example, if a company prioritizes customer preferences or takes a customer-centric approach, it can prioritize deliveries according to the time slots chosen by customers. Alternatively, for companies that place emphasis on resource allocation and control, they can schedule and allocate resources to where these resources are needed most to balance availability and demands.
However, the most relevant prioritization approach in terms of meeting delivery deadlines is actually the dispatch planning prioritization, which prioritizes the most critical orders according to their importance and helps guarantee that high-priority deliveries are dispatched on time. In the same vein, prioritization based on required delivery dates is another effective strategy. Businesses can address the urgency of delivery timelines to make sure orders with the most immediate deadlines are processed first.
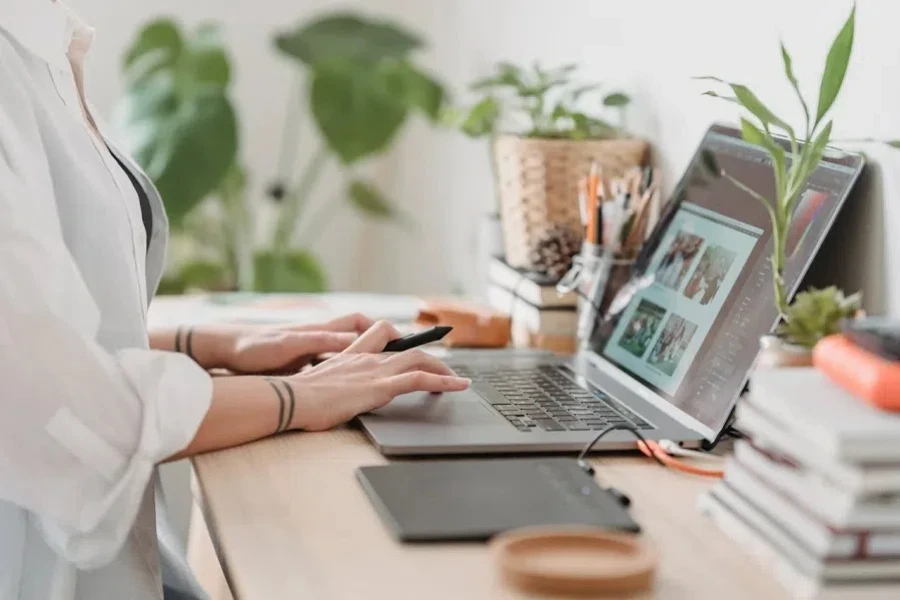
In the meantime, business operations can encounter unexpected situations from time to time. This is especially true for logistics and supply chain processes and such unpredictable conditions highlight the importance of flexible scheduling in response to various changes. The main goal of flexible scheduling technique is to provide rescheduling mechanisms for deliveries, particularly in case of unexpected events such as weather emergencies or logistical disruptions.
Furthermore, proactive scheduling serves as another feature available in most standard time slot management systems that make predictions and scheduling based on real-time data. Finally, businesses can establish another truly instrumental and effective order scheduling technique by integrating proper planning and execution together.
Leveraging technology for efficiency
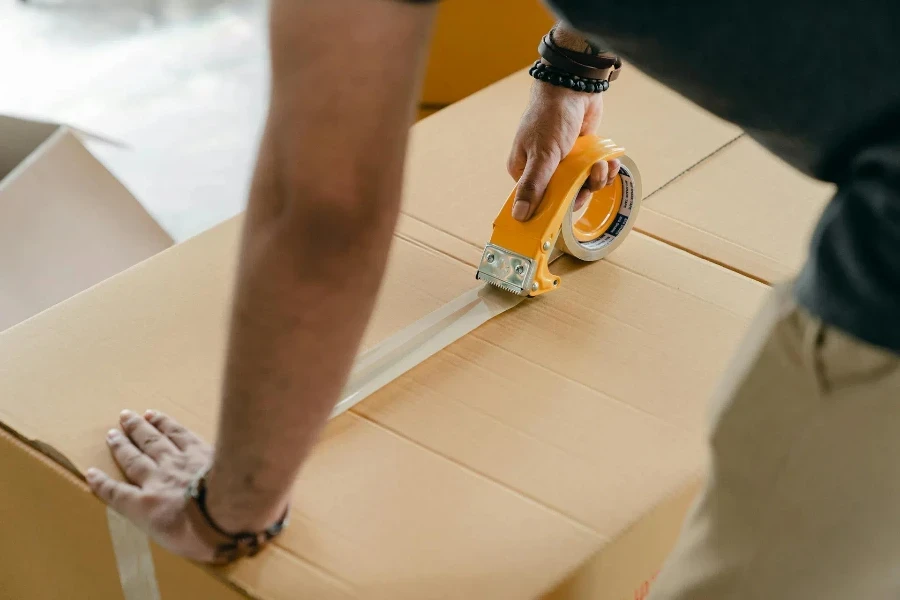
The integration of order slotting and scheduling with larger systems like TMS or WMS is one of the most direct and straightforward ways to understand how technology is leveraged for such functionalities.
In many cases, these features are pre-integrated components of these comprehensive systems for more seamless coordination with different logistics aspects, including inventory management and order fulfillment.
To better understand how technologies are directly contributing to the effectiveness of order slotting and scheduling in meeting delivery deadlines now, let’s focus on three main areas: real-time updates, automated slot allocation, and advanced routing and optimization.
Although real-time feeds and updates are a relatively common and essential feature in order slotting and scheduling today, the advancement of Artificial Intelligence (AI) and machine learning, however, continues to fuel the development of real-time data to new heights. For example, with AI-enhanced customer service chatbots, real-time delivery status updates are now much faster, systematic, and reliable.
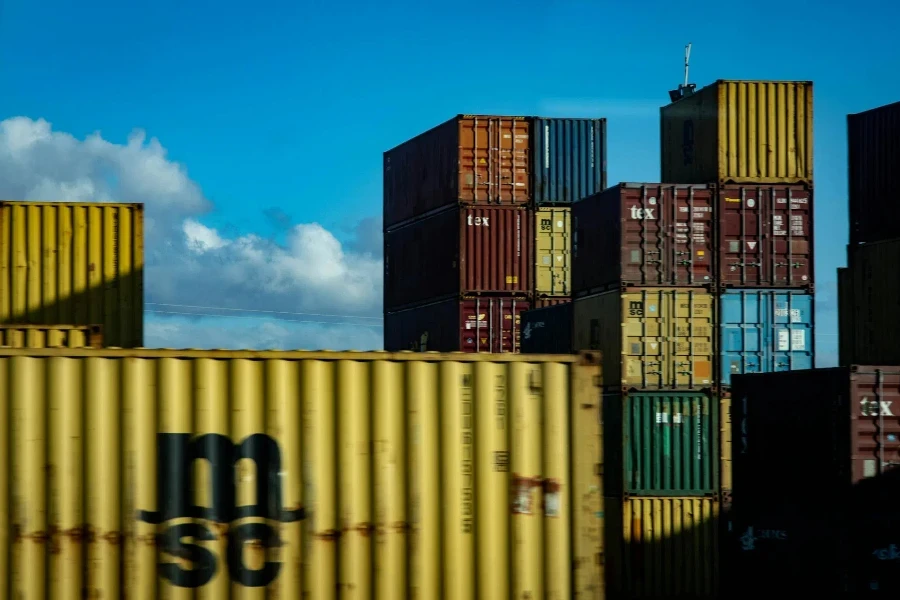
In terms of strategic storage and warehouse optimization, the fact that AI-powered systems can analyze and adjust to real-time data consistently to maximize order fulfillment and storage utilization is another clear indication of how AI brings significant advantages to real-time updates. Overall, AI allows constant adjustments in slotting according to real-time data to improve inventory precision and accuracy.
Another function clearly demonstrated by the advancement of technology in order slotting and scheduling is the increasingly advanced and highly automated slot allocation and management. This is achievable through automated delivery slot management software solutions that operate with minimal or no manual intervention, utilizing advanced algorithms and data analysis to achieve full automation.
Simultaneously, AI is transforming warehouse automation by powering robotics to automate both physical and repetitive tasks, thereby increasing productivity, addressing manpower shortages, and improving overall operational efficiency. This, in turn, enhances the precision and timeliness of order slotting and scheduling to meet delivery deadlines.
Aside from applying advanced algorithms for automation, it is also becoming increasingly common to utilize sophisticated algorithms to create highly efficient and feasible delivery schedules. Utilizing advanced route optimization software with customer preferences for time slots integrated into the routing process is another effective form of routing optimization.
In the meantime, when optimizing routes, AI and machine learning can also be integrated to enable a delivery service to take note of the preferred delivery time and specific instructions of a customer. Considering that machine learning models are constantly processing more data and encountering new scenarios, they can also continue to adapt and refine strategies to improve route optimization systems over time.
Overcoming common challenges
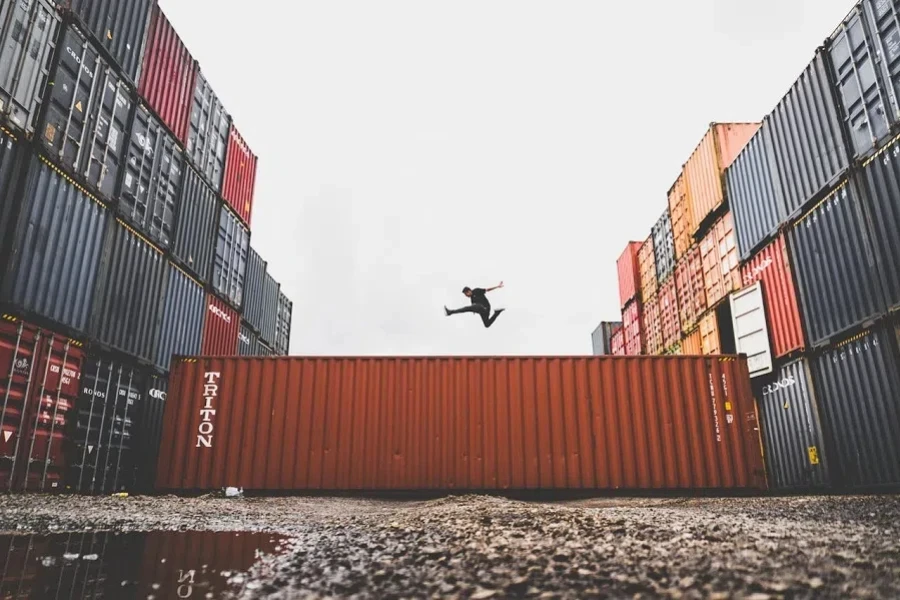
Resource constraints
Just as with any other business operations, logistics, and supply chain management face resource constraints since all resources are available based on limited capacity and demand fluctuations. Resource allocation and management are therefore vital in ensuring that all critical elements in deliveries are fully optimized. This is also where an effective time slot management system can come into play to appropriately utilize all resources without overloading any part of the supply chain.
Handling idle times and bottlenecks
Idle times scenarios and supply chain bottlenecks are two other common issues in order slotting and scheduling that are related to resource constraints. These issues often emerge due to poor coordination and unforeseen disruptions, such as insufficient manpower and warehouse space during specific peak seasons or other temporary disruptions. Idle times, such as extensive waiting times due to scheduling conflicts, often occur when resources like labor, machinery, or transportation are used ineffectively.
These problems can be further compounded by complex slotting methodologies, which risk consuming more resources or misestimating the available resources. Simplifying these methodologies while retaining their effectiveness is the key to regaining control for smooth operations and supporting rescheduling decisions even when facing sudden bottleneck disruptions.
Diverse product attributes
In many instances, diverse product attributes offered by a business may complicate the order slotting and scheduling process. The system must be adaptable enough to handle these varied features without causing delays or other issues such as overcrowded schedules and scheduling conflicts. An order slot management system needs to effectively manage the varied product sizes, weights, and handling requirements to ensure that these diverse product attributes do not cause any operational delays.
Aligning human factors and customer expectations
While the end goal of all order slotting and scheduling efforts is to meet or exceed customer expectations, the customers, however, often demand quicker deliveries at their convenient time and place, even when they may not be available to collect the deliveries. To address such issues, it’s essential to manage human factors like scheduling conflicts due to human-related aspects and the need for training those who are resistant to adopting new technologies. In a nutshell, process automation and adequate staff training are the most direct approaches to overcoming these challenges related to human factors.
Timelines optimized
In conclusion, businesses can improve logistics operations by gaining a thorough, effective order slotting and scheduling processes, whether by using order slotting and scheduling methods as a standalone system or through integration within larger platforms like TMS or WMS. At the same time, order slotting optimization for on-time deliveries involves regular updates, data-driven management, and advance booking, whereas effective scheduling techniques include prioritization, flexible and proactive scheduling.
To enhance the entire logistics operation and to stay highly adaptable to changes, it’s vital to leverage technology such as real-time updates, automated slot allocation, and routing optimization. It is equally important to address challenges such as resource constraints, handling idle times and bottlenecks and diverse product attributes.
To gain more in-depth knowledge and the latest trends in logistics and supply chain management, visit Alibaba.com Reads regularly.
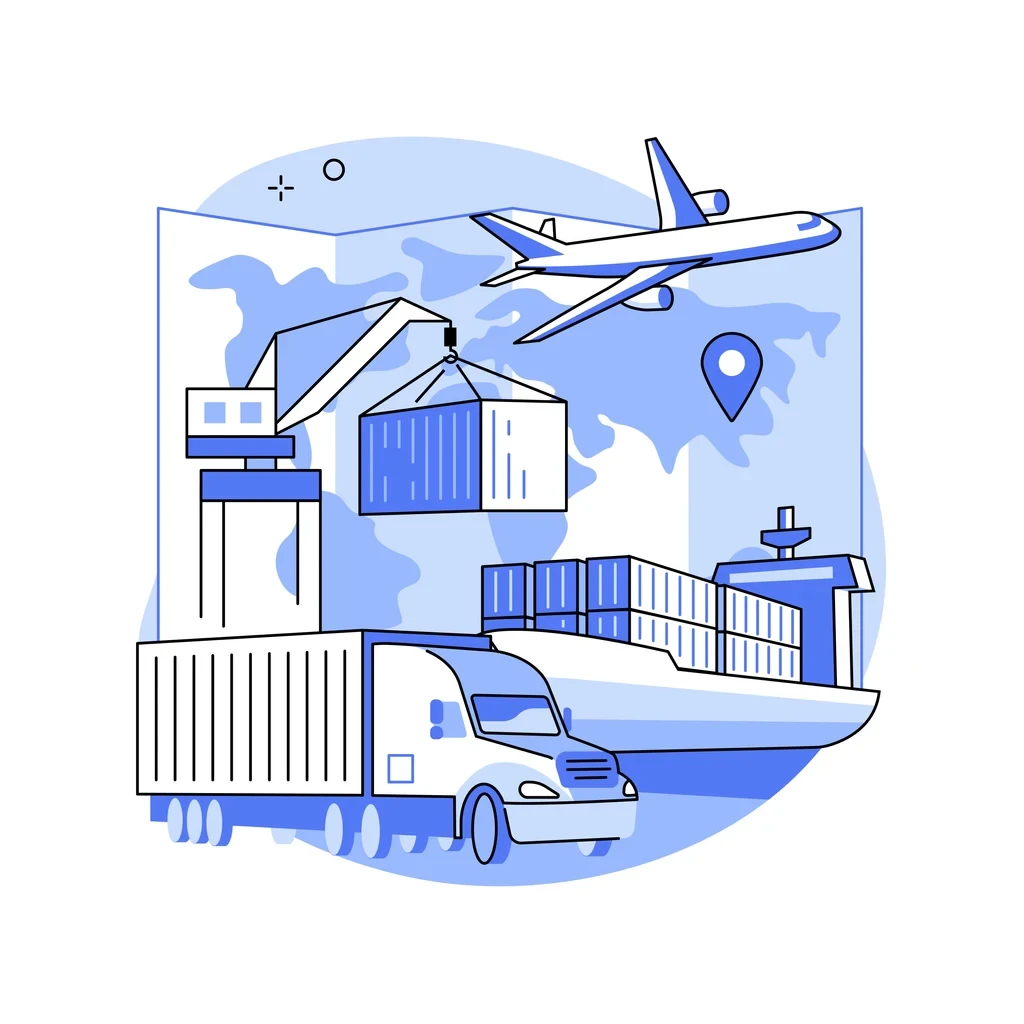
Looking for a logistics solution with competitive pricing, full visibility, and readily accessible customer support? Check out the Alibaba.com Logistics Marketplace today.