近年、プラスチックや金属の世界的な需要を満たすために製造活動が増加しています。 その結果、射出成形および押出プロセスの使用も大幅に増加しました。 これらのプロセスは、競争力のある速度でプラスチックを大量生産するために使用されます。
ただし、XNUMX つの方法には大きな違いがあります。 たとえば、射出成形は XNUMX 次元形状に適しており、押出成形は XNUMX 次元形状に適しています。 このブログでは、これらのプロセスをさらに比較し、プラスチック製造におけるそれらの使用法、長所と短所、および主な違いを探ります。
目次
射出成形プロセス
押し出しプロセス
射出成形と押出成形の違い
まとめ
射出成形プロセス
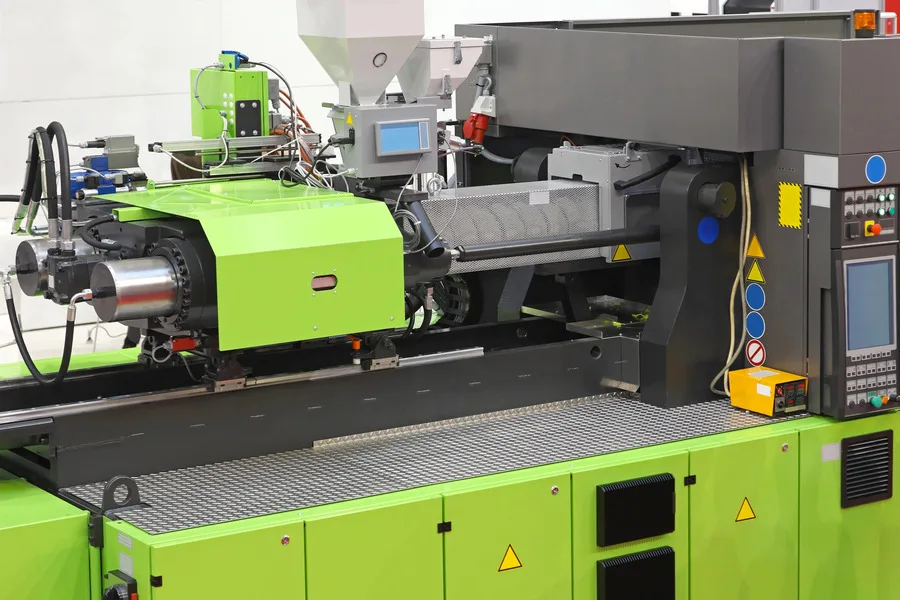
世界中の製造業者は、低コストの大量生産を促進するプロセスとイノベーションを採用しています。 その結果、射出成形は低コストの技術を使用して大量生産と幅広い用途を可能にするため、ほとんどのメーカーにとって頼りになるプロセスになりました。 これは、急速に成長している世界の注射市場規模によって証明されています。 261.8年に2021億XNUMX万米ドル 4.8 年から 2022 年の間に 2030% の CAGR で成長すると予測されています。
射出成形プロセスでは、熱、圧力、射出装置、金型を使用して、プラスチック樹脂を複雑なプラスチック製品に変換します。 この場合、固体プラスチックは特定の融点で溶解され、所定の速度で金型構造に射出されます。 の 射出成形機 必要な圧力を提供する一方、水路は冷却を促進して目的の製品を得ることができます。
射出成形の利点
- 高精度と精度
- ほとんどのプラスチックとの互換性
- 大量生産に向けたコスト効率の高い製品
- 高効率と生産性
- 一貫したパフォーマンス
デメリット
- 初期リードタイムが長い
- 少量生産には不向き
- セットアップコストが高い
押し出しプロセス
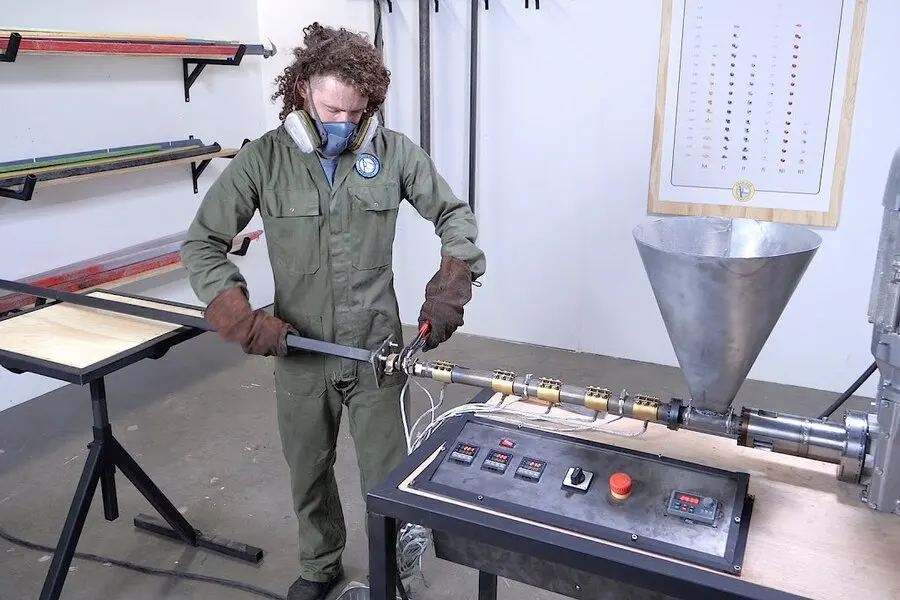
世界の製造業の成長により、 押出機。 この需要は世界の押出機械市場に反映されており、その価値は 8.33年に2022億XNUMX万米ドル 4.3 年から 2023 年の間に 2030% の CAGR で成長すると予測されています。
押出製品は、自動車、消費財、包装など、世界中のさまざまな業界で使用されているため、大きな需要があります。 押出成形プロセスは金属やセラミックにも使用できますが、主にプラスチック材料に使用されます。 視聴者の38%が 2022 年の世界収益シェアの
押出プロセスには、熱可塑性プラスチック材料をイントルーダーに供給することが含まれます。そこで加熱、溶融され、ダイに押し込まれて連続的な特定の形状が作成されます。 押出機は通常、溶融材料を前方に押し出す回転スクリューで構成され、押出に必要な圧力を提供します。 材料が金型から出ると、材料は固化し、望ましい形状を維持します。 このプロセスは、次のような製品を作成するのに適しています。 吹き飛ばされたフィルム、プレート、チューブ、ロッド、および成形材料。
Advantages
- 大量生産に最適
- 汎用性の高いです
- 低価格
- 素晴らしい表面仕上げ
デメリット
- 断面やサイズのばらつきに対応できない
- 潜在的な環境問題
射出成形と押出成形の違い
射出成形と押出成形プロセスは類似していると認識されていますが、プロセスの基本、精度のレベル、互換性など、さまざまな点で異なります。
プロセス
射出成形と押出成形では、最終製品を製造するために異なるプロセスが使用されます。
1) 射出成形プロセス
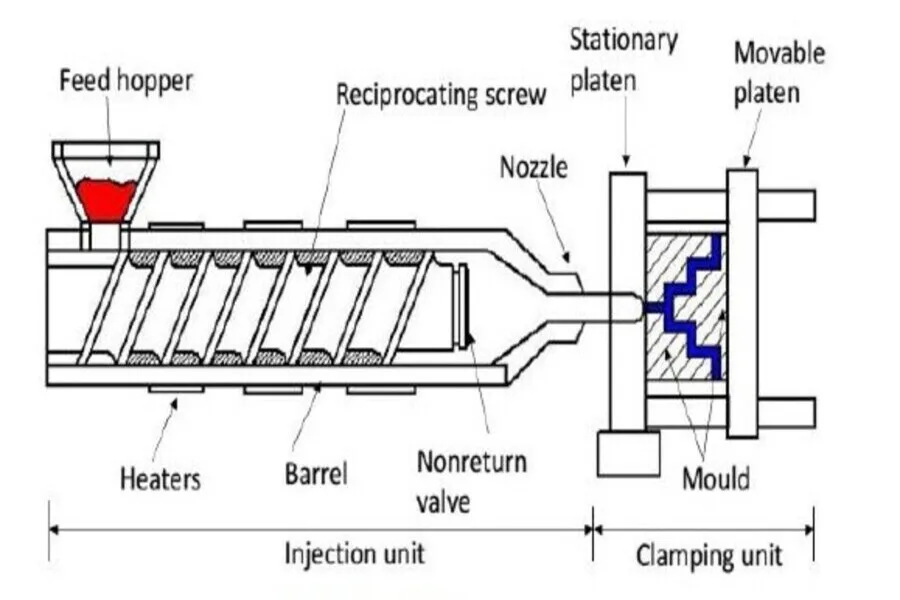
射出成形プロセスは、材料を溶解し、必要な形状のキャビティを備えた金型構造に材料を射出することから始まり、そこで材料が冷却されて固化します。 このプロセスは、以下に説明する XNUMX つの主要な段階で構成される特定のサイクルで発生します。
- 成形前の準備
高品質な製品づくりを目指し、スムーズな製品づくりを目指すメーカー プラスチック射出成形 プロセスではさまざまな準備作業が行われます。 これらには次のものが含まれます。
- 原料の前処理
- バレルの掃除
- インサートの予熱
- 離型剤の選択
- 素材の追加
射出成形プロセスの最初のステップは、材料を追加することです。 操作の安定性と可塑化の均一性を確保し、高品質の製品を得るには、材料を一定量に保って定量的に添加する必要があります。
- 可塑化
中のバレルは、 射出成形機 成形材料を加熱、加圧、混合するために使用され、これにより材料が粒状の固体またはルースパウダーから連続的に均質化された溶融物に変わります。
- 注入する
プランジャーまたはスクリューは、射出シリンダーとピストンを通して大きな圧力を加え、可塑化されたプラスチック溶融物をバレルの前部ノズルと金型ノズルの両方を通して推進します。
- 冷却
プラスチック溶融物が閉じた金型キャビティに射出されると、水、空気、油などの冷却材が導入されて金型をさらに冷却します。
- 脱型
この時点で、冷却されたプラスチックは、エジェクターピンやプレートなどの突き出し技術を使用して金型から押し出されます。 この段階では、形状に損傷や歪みを生じさせずに金型の完成品を確実に分離することで、射出成形プロセスの終了を示します。
- 製品の後処理
この後処理段階には、厚さのばらつき、亀裂、形状の歪みに反映される成形部品の残留応力を除去するなど、さまざまな作業が含まれます。 また、成形品の色、性能、サイズを安定させるために加湿が必要になる場合もあります。
2) 押出成形プロセス
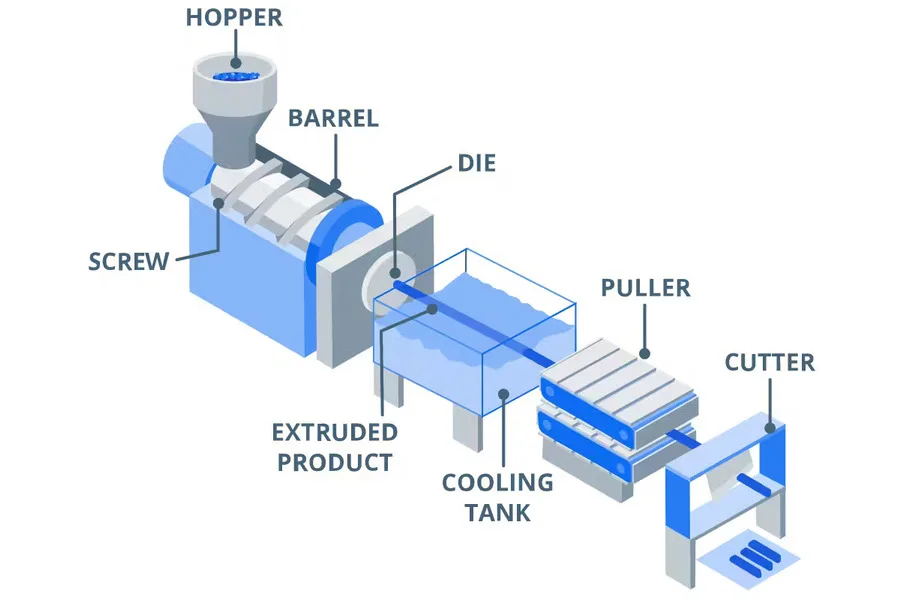
押出中、ポリマー材料は圧力下でスクリューまたはプランジャーを使用してダイに押し込まれます。 押出プロセスは XNUMX つの段階に分かれています。
- 材料の可塑化と加圧
この段階では、原料をペレットまたは顆粒の形で装置に供給する必要があります。 押出機 ホッパーを通して。 次に、スクリューを使用して材料をバレル内に押し込み、熱と機械的作用にさらして可塑化を開始します。 これにより、材料が溶融状態または可塑化状態に変化します。 同時に、回転スクリューが熱を発生させ、混合を促進し、圧力を加えて材料の一貫した可塑化を保証します。
- 整形
この段階では、押し出された材料が、特別に設計された開口部またはチャネルを含むダイの成形要素を通過します。 これらは、押し出された材料が望ましい形状、形状、寸法をとるのに役立ちます。
- 冷却
押出された材料はダイから出ると冷却ゾーンに入り、周囲の空気、水スプレー、冷却槽などの冷却機構にさらされます。 これにより、材料の温度が低下して凝固し、溶融状態から固体の形状に変化します。
プラスチックとの適合性
射出成形と押出成形で使用されるプラスチックの種類によっては重複する場合もありますが、特性や適合性の違いにより、特定の材料がどちらかのプロセスにより適している場合があります。 たとえば、射出成形は、熱可塑性プラスチックやほとんどの熱硬化性プラスチックを含むあらゆる種類のプラスチックと互換性があります。 この適合性は、複雑な化学組成を持つ材料を処理するプロセスの能力に基づいています。
逆に、ほとんどの 押出機 優れたメルトフロー特性と安定性を備え、主に熱可塑性プラスチックと互換性があります。 これは、このプロセスがスムーズな押し出しを実現するために材料の連続的な流れに主に依存しているためです。
精度
射出成形は、押出成形よりも高い精度と厳しい公差を実現します。 優れた寸法精度で高精度で複雑な部品を製造できることで知られています。 これは、このプロセスでは、閉じた金型キャビティ内に溶融材料を高圧で射出することが含まれるため、最終製品の形状、サイズ、表面仕上げの正確な制御が容易になるためです。
押出には、ダイを通る溶融材料の連続的な流れが含まれます。 押出ダイは精密に設計できますが、精度のレベルは射出成形の精度よりも低くなります。 ただし、特により単純な形状やそれほど厳密な公差を必要としないプロジェクトの場合、押し出し加工では許容可能な精度レベルを達成できます。
材料の流動性
材料の流動性は両方のプロセスにとって重要な要素です。 しかし、 射出成形 特に複雑で薄肉の製品の場合、適切な金型充填を確保するには、より高い材料流動性が必要です。 このプロセスで使用される溶融材料は、金型キャビティの複雑な輪郭、コーナー、薄い部分に容易に広がる優れた流動性を備えている必要があります。
逆に、押出成形は連続的でオープンエンドな性質があるため、材料の流れの要件はそれほど厳しくありません。 このプロセスでは、複雑な金型キャビティを充填する必要はありません。つまり、材料がダイをスムーズに流れ、押出製品の長さに沿って一貫した形状と寸法を維持するのに十分な流動性のみが必要であることを意味します。
溶融強度
どちらのプロセスでも、異なる程度の溶融強度が必要です。 たとえば、射出成形ではプラスチックが金型内で成形されるため、高い溶融強度は必要なく、幾何学的制限を受けることになります。 さらに、材料は制御された冷却下で注入されるため、迅速な固化が可能になります。
押出成形では、材料は自由にダイから出てくるため、熱成形や中空ブロー成形などの後続プロセスが必要になる場合があります。 これらの工程により、たるみや伸びなどの歪みが生じ、完成品の品質を低下させる可能性があります。 したがって、必要な金属強度は射出成形よりも押出成形の方が高くなります。
まとめ
製造部門の成長により、射出成形と押出成形の採用が大幅に増加しました。 どちらのプロセスもプラスチックの製造に使用されますが、機能的にはかなりの違いと特性があります。 たとえば、射出成形は 3D 製品に適しており、押出成形は 2D 製品に適しています。 さらに、射出成形は押出成形に比べて幅広いプラスチックに適合します。 したがって、どちらを選択するかは、プロセス、材料、効率を慎重に検討し、計画する必要があります。
射出成形や押出成形に関連する何千もの製品や機械を見つけるには、次のサイトをご覧ください。 Alibaba.com.