There is no effective supply chain management without internal audits. We can think of audits as health check-ups for supply chains to ensure they operate as smoothly and cost-effectively as possible, from sourcing raw materials to delivering products to the final customer.
By systematically reviewing supply chains, organizations can identify potential risks and inefficiencies in procuring raw materials, production processes, supplier relationships, inventory management, and customer satisfaction.
So, how can companies conduct internal audits? Which supply chain aspects should they consider? And how should they document the findings and corrective actions? Continue reading to learn how to conduct supply chain audits the smart way!
Table of Contents
1. Prepare for the audit
2. Collect the data
3. Conduct the audit
4. Report the audit findings
5. Supply chain audit is an ongoing cycle
Prepare for the audit
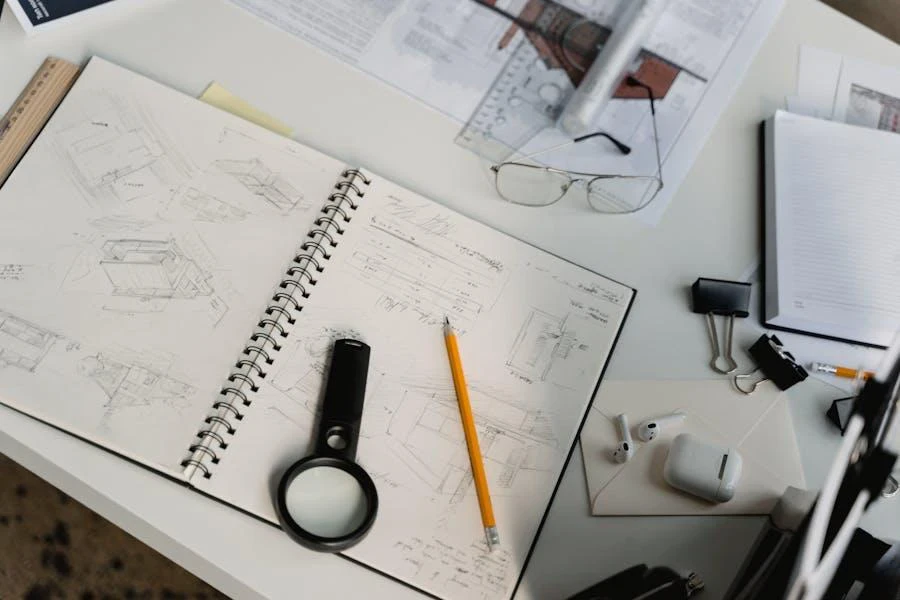
Just as we can’t lay the first brick of a house without an architectural blueprint, we can’t conduct an audit without a plan. Before acting like detectives to search for supply chain risks and vulnerabilities, we need to clearly understand the “why” (objectives), “where” (scope), and “how” (actual plan).
Determine the scope of the audit
Without a clearly defined scope, supply chain audits will take forever to conduct (imagine how much time and resources will be wasted). There are many aspects to consider when auditing supply chains, but companies should concentrate their efforts where it matters.
For instance, if there has been a historical pattern of product quality issues, the audit should prioritize manufacturing processes and quality control systems. Businesses may even limit the audit scope to include particular product lines with a history of increasing quality issues.
Define the objectives of the audit
Once the audit scope is determined, it’s important to establish SMART objectives. Just as it wouldn’t make sense to start painting a portrait without knowing who or what you’re painting, conducting internal audits without clear objectives is illogical.
SMART objectives should be Specific, Measurable, Achievable, Relevant, and Time-bound. For example, the objective of an audit could be to assess whether current quality control systems maintain a defect rate below 5% within a year.
Develop an audit plan
After clarifying the audit objectives and determining which parts of the supply chain should be reviewed, companies should finalize this step by developing a detailed audit plan (the how).
Think of an audit plan as an outline that specifies the team members (auditors), methodologies (how they will conduct the assessments), and the resources they will need (such as checklists, surveys, data analysis software, etc.).
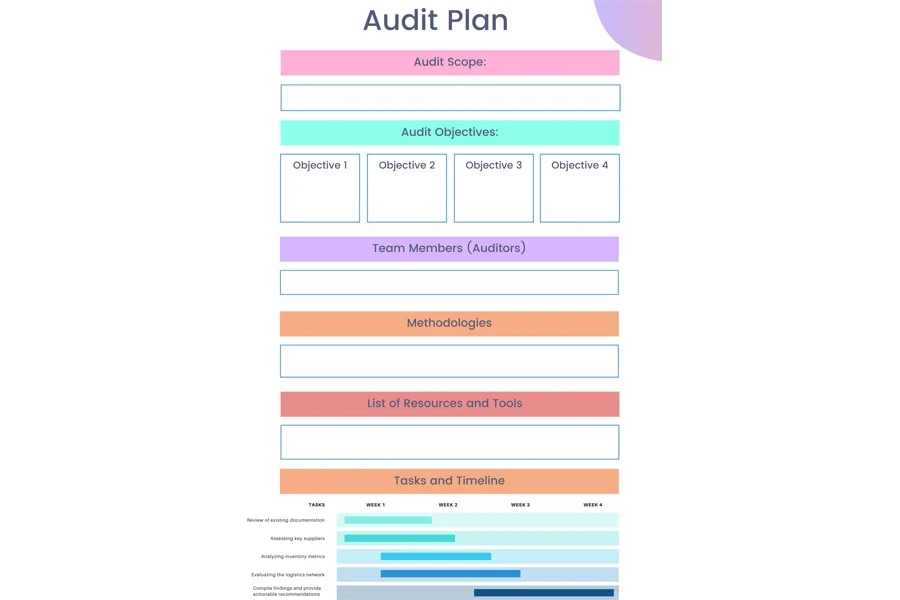
Collect the data
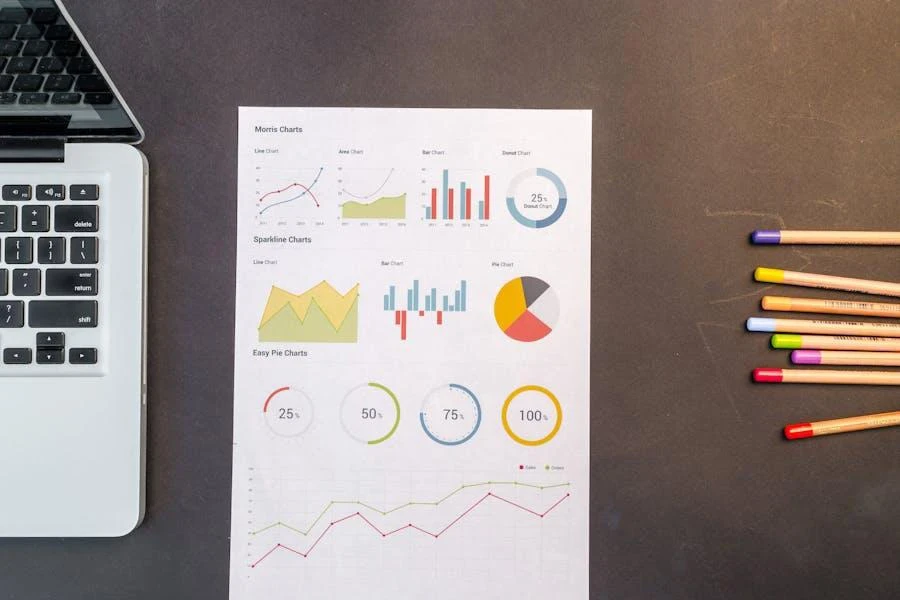
Without data, auditing supply chains is like searching with a blindfold for a needle in a haystack. Auditors need to collect data to get a clear picture of the current state of supply chain processes. Data also provides a baseline for benchmarking supply chains against industry best practices. Below are some examples of data sources:

1. Internal documents and records:
Internal documentation is the primary source of data for any organization. These documents include purchase orders, supplier contracts, inventory records, and past performance reports. For instance, auditors can use logistics KPIs to assess cycle time, on-time delivery rate, and supplier lead time.
2. Interviews with personnel:
Another primary data source is speaking with key staff, such as warehouse managers, production officers, and logistics coordinators. For example, warehouse managers can pinpoint discrepancies between physical stock counts and inventory records or highlight bottlenecks that slow down order fulfillment.
3. Surveys and questionnaires:
Another way to collect data is to distribute surveys and question forms to operational employees, suppliers, and customers. For instance, auditors can get an idea of current customer satisfaction by collecting feedback on product availability, delivery times, and the rate of handling returned orders.
4. On-site visits:
Nothing is better than having a first-hand view of operations to spot discrepancies that paper audits might miss. Physical inspections allow auditors to assess the working and storage conditions, the maintenance of facilities and equipment, and the execution of quality assurance protocols.
5. Industry benchmarks and standards:
While auditors can evaluate collected internal data against pre-established KPIs, it’s also important to have some kind of external baseline. Without industry benchmarks, businesses can’t be sure that their supply chain is performing well.
For instance, if an internal audit reveals that the customer return rate is 5%, the company might think it’s positive according to its internal KPI. However, if competitors have a return rate of only 2%, it clearly indicates that something is wrong.
6. Third-party audit reports:
Businesses can also use the audit reports conducted by external bodies to get an impartial look at the current state of their supply chains. For example, if a company has obtained a quality management system (QMS) certification, such as ISO 9001, it could use the audit report as a starting point to assess current inefficiencies within its supply chain, from production to delivery.
Conduct the audit

After businesses have determined what parts of their supply chains they want to audit (the defined scope) and gathered all information about what they hope to achieve (established objectives) and what things actually look like (data of current state), it’s time to wear the detective hat and start auditing.
We can summarize the audit process in the following decision tree questions:
- Is everything running according to what we’ve planned?
- If yes, are there any opportunities to improve the performance of the supply chain?
- If not, what actions should we take to fix the identified problems?
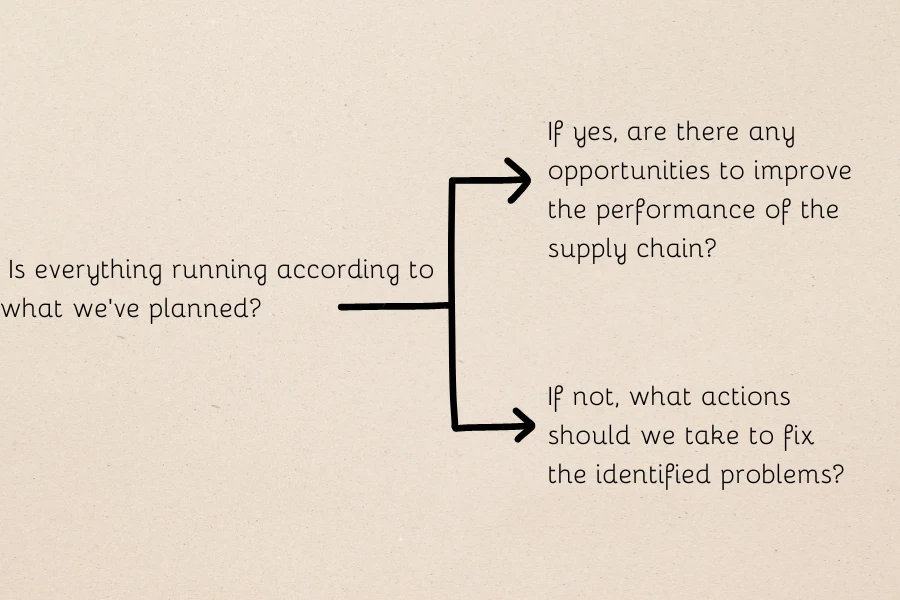
Let’s go over some examples of audits that a company can conduct across the different stages of its supply chain:
1. Sourcing and procurement:
A great starting point for auditing supply chains is by analyzing the full lifecycle of the procurement process. After developing a flowchart that details each step of the procurement cycle, auditors can evaluate the following aspects to detect inefficiencies:
- Supplier performance: Supplier audits help detect if vendors and subcontractors are the source of waste, quality issues, and slow delivery times. Auditors can assess suppliers using a risk matrix that segregates vendors according to KPIs like on-time delivery rate, credit score rating, and rate of returns.
- Receiving and inspecting goods: Businesses must verify that goods (especially raw materials) are accepted only if they match the required quality and quantity standards. Auditors can analyze the inspection process, including criteria for acceptance and rejection, sampling procedures, and testing methodologies.
- Invoicing and payment: It’s important to confirm that payments are made only for accepted goods. For example, auditors can verify that delivery receipts and invoices are logged and matched against purchase orders. It’s also a good idea to ensure that payments are made on time (to benefit from early payment discounts and avoid late payment penalties).
2. Production and manufacturing
The production and manufacturing stages should be on the checklist of every supply chain audit. After all, we don’t want faulty or inferior products to reach the hands of customers. Here are some ways to audit these supply chain stages:
- Sample testing: The most intuitive way to audit production and manufacturing is through random sample testing. Generally, auditors collect samples randomly from the production lines at scheduled intervals, and then they perform various tests to check if samples meet pre-set standards. These tests might include quality and safety checks such as appearance, weight, and toxicity.
- Standard operating procedures (SOPs): When conducting on-site visits, auditors can observe and check if the various stages of production and manufacturing are followed exactly as described in SOPs. For example, an unannounced visit might reveal that employees are not operating a machine according to the steps prescribed in the SOP. Maybe they are not performing pre-operation safety checks before running the machine.
3. Warehousing and inventory management
If there are any discrepancies between the physical inventory and recorded inventory in a company’s database, this might lead to stockouts or excess stock. Inventory affects the cost of goods sold, so we must perform regular internal audits to identify potential inefficiencies in the warehousing operations. Here are some ways how businesses can audit inventory management:
- Inventory count: A straightforward way to audit inventory is by regularly scheduling physical counts and then comparing the counts with what’s recorded in the warehouse management system. Physical counting can be done manually, where operators count every item in the warehouse. However, manual counting is labor-intensive, so businesses can use barcode scanning or RFID tags to track every item moving into, within, and out of the warehouse.
- Performance metrics and KPI tracking: Businesses can also audit the efficiency of their warehousing by monitoring KPIs against pre-established levels and benchmarks (it’s time to use that collected data!). For example, we can audit the order accuracy rate by measuring the percentage of orders shipped without errors (correct product, quantity, and to the correct customer). We can also check the carrying cost of inventory, which includes storage, insurance, and obsolescence.
- Inventory process walkthrough: Eyes on the ground are always the best auditing tool. Auditors can physically follow the flow of inventory items from receiving to shipping. For instance, they can watch a pick-and-pack cycle to assess if the path and time taken are optimized and if the packing materials are adequate. It’s also a great opportunity to check if goods are inspected upon arrival and how they are logged into the warehouse management system.
4. Logistics and distribution
A supply chain audit won’t be comprehensive without assessing transportation routes and logistics operations. This is the time to evaluate the efficiency of distribution routes and look for any non-value-added freight costs. Here are some practical ways to audit these parts of the supply chain:
- Data analytics and performance metrics: Auditors can analyze GPS and telematics data from vehicles, along with delivery schedules and logs, to look for deviations in delivery times and costs. For example, businesses can evaluate whether cargo space utilization (the ratio of cargo space used to total available space in transport vehicles) is close to 100%.
- Mystery shipments: Another way to audit distribution networks is to send packages as a “mystery shopper” without telling the logistics department. Auditors mimic a typical customer order and record the exact dispatch and arrival times. This will allow businesses to assess whether their transit times are within the expected range.
5. Customer satisfaction
When evaluating the performance of global supply chains, we should remember that the ultimate success indicator is the level of customer satisfaction. As we have seen in the phase of “collecting data,” customer feedback can be a mine of insights. Let’s explore some ways of auditing customer satisfaction in supply chains:
- Net promoter score (NPS): When auditing customer satisfaction, auditors generally use the NPS to measure customer loyalty. Businesses use surveys, questionnaires, and focus groups to ask customers how likely they are to recommend the company to others. The NPS score (on a scale of 0 to 10) categorizes customers into promoters, passives, and detractors.
- Customer complaint analysis: Another direct way to audit customer satisfaction is to analyze the nature and frequency of customer complaints and look for deviations from the benchmarks or baseline metrics. For instance, businesses can look at the number of complaints received about the same issue to identify any recurring patterns. Auditors can also measure the average time taken to resolve a complaint to determine whether it falls within an acceptable predefined range.
6. Compliance, risks, and sustainability
Businesses that want to perform a comprehensive audit of their supply chains can also examine whether their operations and processes are in compliance with regulatory and sustainability regulations. This is also an opportunity to audit businesses’ resilience against potential supply chain risks, such as natural disasters, political instability, and cybersecurity threats. Here are two ways to audit the compliance and resilience of supply chains:
- Environmental resource management: Businesses should audit their environmental impacts, especially if they want to obtain or maintain an environmental management certification, such as ISO 14001. Auditors can evaluate whether the company is using and sourcing raw materials obtained from sustainable sources. Another way to audit the environmental impact is by calculating the total carbon footprint, including direct and indirect emissions, from all supply chain activities.
- Stress testing and scenario analysis: Stress testing is an extreme way to evaluate the supply chain’s ability to continue functioning under different risk conditions. Businesses can simulate different risks (e.g., political unrest, economic shocks, cyber-attacks) and observe how quickly and effectively the supply chain can respond. For example, a company might simulate a scenario where a typhoon disrupts the production of key suppliers for a month. Then, they would review whether they could maintain product deliveries to customers.
Report the audit findings
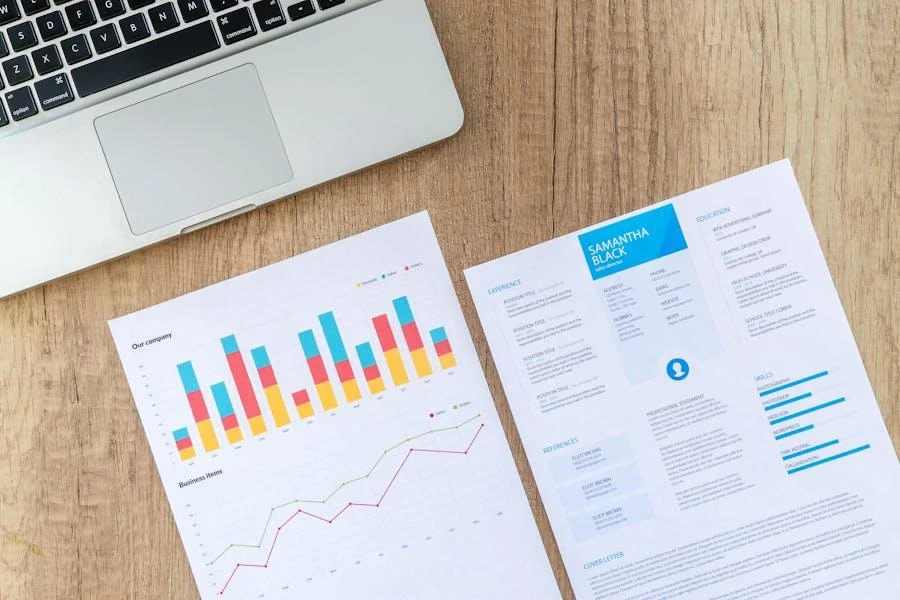
The post-audit step is obviously the reporting of findings to key stakeholders. But spotting where problems are found is not enough. We also need an action plan to fix problems. Here’s what should typically be included in the audit report:
- Executive summary: A brief summary of the audit scope and objectives, the audit timeline, the methodologies used, and the most critical issues found.
- Methodologies: The report should describe how the data was collected and list any tools or methods used in the audit process. This section is where auditors should explain how they have determined whether a supply chain operation or process is performing well.
- Detailed findings: This section should list all the issues and deviations spotted during the audit process. To facilitate the report’s interpretation, the problems identified should be categorized according to their priority and/or risk levels in terms of impact and likelihood of recurrence.
- Recommendations: It’s the solutions, not the problems, that lead to improvement. An audit report without a corrective action plan is like pointing out what’s broken without a fix. The report should suggest corrective actions for each identified issue. Even if there are no problems, the report should recommend improvements (e.g., upgrading software for better inventory management).
- Implementation plan: To make sure the key stakeholders will implement the recommended measures, the report should prioritize the list of corrective actions based on their impact and feasibility. It’s equally important to include a timeline for implementing the recommendations and define who is responsible for each part of the action plan.
Supply chain audit is an ongoing cycle
Reporting the findings is not the end of the audit process. We can’t just measure supply chain performance, recommend an action plan, and move on. Businesses need to conduct regular follow-up audits to verify that the corrective actions are implemented, confirm whether they have indeed fixed the problems, and determine whether they improved the supply chain’s efficiency.
It’s difficult to say how often businesses should conduct internal audits, as this depends on the supply chain’s complexity, past audit findings, and regulatory requirements. For example, if previous internal audits revealed many critical issues, it might be necessary to increase the frequency of audits. However, as a rule of thumb, small—and medium-sized businesses should conduct supply chain audits at least once a year.
When auditing global supply chains, it’s important to understand what makes them vulnerable. Check out the top five supply chain issues in 2024 and make sure they are included in your next internal audit!
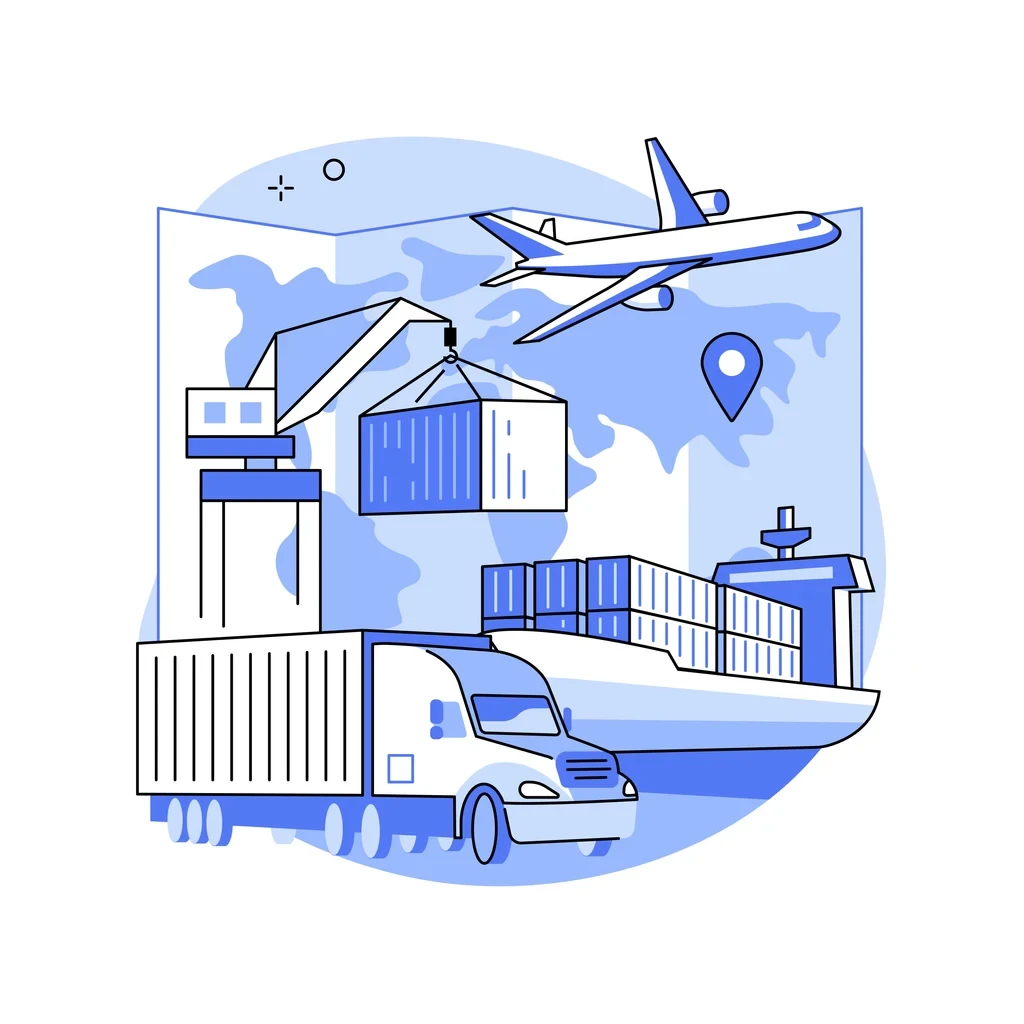
Looking for a logistics solution with competitive pricing, full visibility, and readily accessible customer support? Check out the Alibaba.com Logistics Marketplace today.