Milling machines—also known as multi-tasking machines—are indispensable in metalworking and woodworking shops. A milling machine is a device that rotates a circular tool with several cutting edges symmetrically arranged about its axis, which is used for removing material from a workpiece.
It is no secret that a good quality milling machine can last years and help manufacturers meet high tolerance standards. However, choosing a perfect milling machine is a task in itself if you are not well versed with the specifications.
This guide offers a quick overview of the milling machines and tips you can follow to get the best milling machines to meet the requirements of your end customers.
Table of Contents
The milling machine market potential
Tips for selecting the right milling machines
A key piece of machinery for metalworking and woodworking
The milling machine market potential
Fabricated metal products are used widely across the world from household to industrial purposes, giving a steadfast growth for milling machines. The milling machine market is estimated to reach USD 102.3 billion by the end of 2026, growing at a CAGR of 7.2%.
Today’s advanced technology is also giving a good scope for automatic CNC milling machines. This market size is set to expand to USD 128.41 billion by 2028. While these are global projections, the Asia Pacific market is expected to witness the highest growth. In addition, the European market is also expected to witness significant growth compared to North America, the Middle East and Africa, and Latin America.
The key growth driver for CNC milling machines can be attributed to the increasing investments in the Internet of Things (IoT) within the manufacturing sector. Moreover, adopting additive and subtractive manufacturing techniques to build complex, high-precision products will increase demand for these machines.
Tips for selecting the right milling machines
1: Number of axes

Milling machines are of three types based on the number of axes: vertical, horizontal, and universal. The differences between these milling machines lie in the axes the spindle can move. Most milling machines have three axes: a vertical axis called the Z-axis, a longitudinal axis called the X-axis, and a transverse axis called the Y-axis.
Vertical milling machine
The vertical milling machine is the most widely used. It has a vertical spindle that is perpendicular to the workpiece. In a vertical milling machine, the workpiece remains fixed while the table moves along it. These milling machines are easily movable, allowing the operator to remove material from the workpiece more flexibility.
The head of the vertical machine can also be moved in different directions. This machine is typically used for working on vertical surfaces for angular milling, slot milling, T- slot milling, and flat milling. Normally, vertical milling machines can process parts of up to 6000mm in width, 2500mm in height, and 700mm in depth.
Horizontal milling machine
Horizontal milling machines are primarily used for jobs where vertical milling machines are unsuitable. Horizontal milling machines have a horizontal spindle, and tools are attached parallel to the table. These machines are ideal in cases where a milling job involves removing excess material with less accuracy.
In this milling machine, several milling cutters can be placed next to each other. The machine can also carry heavy load cutting and can cut with an end mill. Horizontal milling machines are generally suited for making simultaneous grooves, bevels, and planes and work better for chip evacuation. These machines are also helpful for making heavier and deeper cuts compared to a vertical milling machine.
Similar to vertical milling machines, horizontal mills are available in varying table sizes to process parts of up to 6000mm in width, 2500mm in height, and 700mm in depth.
Universal milling machine
A universal milling machine has a universal spindle attached to a hinge, and unlike other milling machines, it can operate on multiple axes. Multiple saw blades can be clamped at once in a universal milling machine, making it very efficient. The machine’s milling head can swivel at 45 degrees to the left and right and has sufficient rigidity and stability. Universal milling machines are primarily used to process different surfaces of small, low-weight parts and serial production.
It is also possible to use additional attachments like slotting attachment, rotary attachment, vertical milling attachment, and index head or dividing head to enhance the machine’s capacity.
2. Feed type
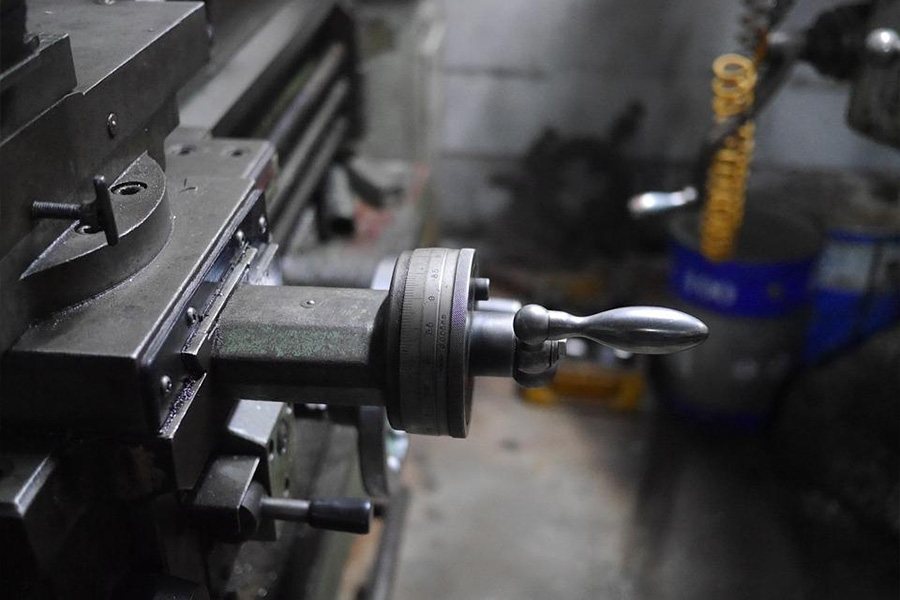
Milling machines have come a long way in terms of ingenuity. Traditional milling machines use handwheels that the operator turns to move the workpiece to and from the drill. However, machines available today require minimal or no physical labor. Therefore, if you’re eying to capture a market in the industry, you can offer more options to your customers, and the feed type for table travel is one of the critical selling points. The most popular feeds you’ll find in milling machines today are:
- Traditional feed
- Power-fed motor
- CNC milling machine
Traditional feed
Traditional feed is still one of the most popular choices, thanks to conventional milling practices. This feed mechanism operates on 3-axes using handwheels. A handwheel is used to move the table, which is marked with measurements like millimeters to give more control to the operator when moving the table and attain precision while making cuts.
Power feed motor
In this type of milling machine, power feeds are attached to the ball screws of drilling, milling, and other machines for an accurate, repeatable feed rate. They are designed to provide automated feed replacement for handwheels on manually-controlled machine tools, allowing the table to move consistently. The power feed mechanism uses DC geared motor with 12V, bevel gears, and a timing belt.
CNC milling machine
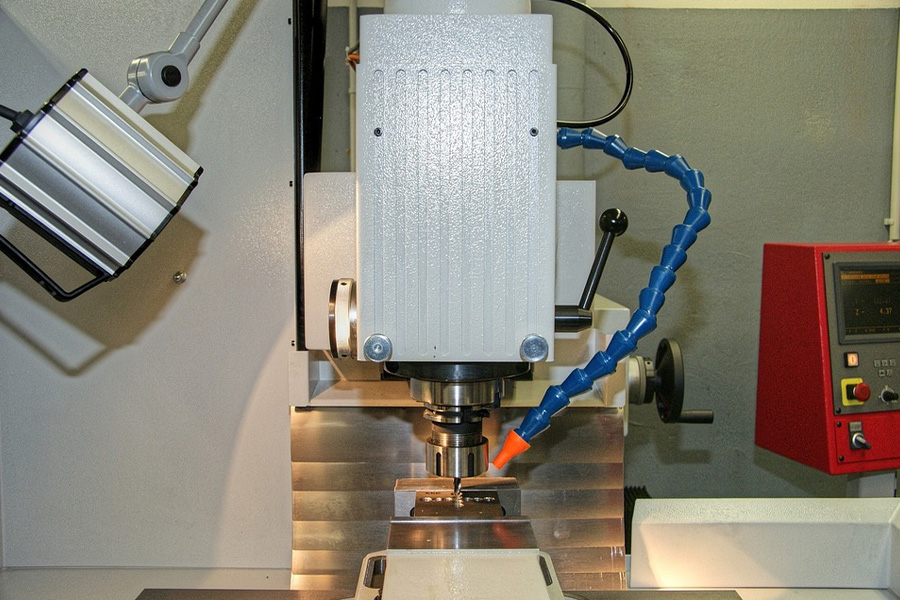
Computer Numerical Control or CNC milling machines are technologically enhanced machines that use a computer-controlled system.
The spindle provided in these milling machines can move in three directions, which means it can rotate 360 degrees. The user simply requires uploading the workpiece design, and the machine will automatically take care of the milling operations. This type of milling machine is similar to the bed type or an upgraded version of the bed type milling machine.
CNC milling machines are flexible and have a high production efficiency. They can also cut complex shapes and materials accurately. Besides, these machines come with a memory function that allows operators to replicate an operation many times. CNC milling machines are becoming more popular thanks to their ease of use and reduced operator labor intensity. With the autonomy, accuracy, and precision offered by this new age of milling machines, traditional machines are rapidly becoming obsolete.
3. Speed
Speed is one of the crucial factors you should consider when selecting a milling machine, as it will directly influence the quality and overall finish of the final processed part. The most popular choice is to go for higher RPM (rotation per minute) machines with small coated tooling, cutting at a shallower depth. The higher RPM results in cleaner finishing and requires less horsepower.
4. Cooling options
Cutting oil works as a great coolant while milling. It also acts as a lubricant and decreases the stress on the machine and workpiece. The oil dissipates heat generated from the cutting tool and the workpiece, extends the machine’s life, and prevents wrapping and seizing. Cutting oil also helps clear the surface of the workpiece from the chips and shavings and reduces the risk of unwanted chippings and errors.
5. Accuracy
Accuracy is one of the critical parameters when selecting milling machines. It is a specification that will help you understand how accurate the milling machine is in performing the desired operation. For instance, if the requirement is to cut the workpiece at 50mm, the machine must closely position the tool to match this value whenever the operation is triggered. The tool positioning accuracy should usually be under 0.05mm. For jobs requiring greater accuracy, milling machines with an accuracy of 0.01mm must be selected.
6. Table size
When selecting a vertical milling machine, one of the key factors to consider is its size. The size of these milling machines is determined based on the table’s maximum longitudinal, cross, and vertical travel and the machine’s working surface. These dimensions will also give you an idea about the size of parts that can be processed using the machine. Typically, the table dimensions start from 600X300mm and go all the way up to 6000X2500mm, depending on the type of milling machine you choose.
A key piece of machinery for metalworking and woodworking
Milling machines make metalworking and woodworking a breeze. With the right type of machines in your catalog, customers will have an easy time making purchase decisions. Consider all these aspects before buying a milling machine and invest your money in machines that precisely meet the needs and expectations of your consumers.